Spis treści
Opis zagadnienia
W dokumencie opisano możliwości systemu za pomocą których można odwzorować procesy produkcyjne na różne możliwe sposoby.
Ponadto niniejszy dokument zawiera podstawowe informacje o tworzeniu zleceń produkcyjnych, ich przetwarzaniu, metodach rezerwacji artykułów, weryfikacji wydajności zasobów. Dodatkowo w dokumencie zostały opisane możliwości systemu w kontekście przyjęć i rozchodów magazynowych z wykorzystaniem odpowiednich aplikacji.
Definicje pojęć
- Zlecenie produkcyjne – podstawowym elementem procesu produkcji lub sterowania produkcją jest zlecenie produkcyjne. Zawiera ono polecenie wyprodukowania materiałów lub wykonania usług w określonym terminie i określonej ilości. Zlecenie produkcyjne określa, przy pomocy jakich operacji lub zasobów i z jakich materiałów do produkcji należy wyprodukować podaną ilość artykułu w konkretnym terminie.
- Metoda produkcji – zawiera wytyczne dotyczące produkcji artykułu i składa się z zestawienia materiałowego, zestawienia materiałowego i marszruty, technologii. Za pomocą metody produkcji można zdefiniować alternatywne procesy produkcji. Artykuł może być produkowany w każdej metodzie produkcji z różnymi zestawieniami materiałowymi, marszrutami, technologiami lub wszystkie metody mogą zawierać te same zestawienia materiałowe i te same marszruty.
- Technologia – jest wspólnym elementem zestawienia materiałowego i marszruty. W technologii powiązane są ze sobą poszczególne artykuły z zestawienia materiałowego i marszruty. Technologia przedstawia czas przebiegu procesu produkcyjnego.
- Zestawienie materiałowe– to zestawienia wszystkich elementów potrzebnych do produkcji artykułów. Elementami takiego zestawienia mogą być surowce, materiały, półfabrykaty lub inne zestawienia materiałowe. Do artykułów produkcyjnych można przyporządkować jedno lub wiele zestawień materiałowych (w metodzie produkcji). Zestawienia materiałowe mogą być wykorzystywane do produkcji najróżniejszych artykułów.
- Marszruty – zawierają operacje konieczne do wyprodukowania artykułu. Kolejność operacji w marszrucie i ewentualne wzajemne zależności operacji uwzględniane są podczas uruchamiania zlecenia produkcyjnego.
- Zasoby – to środki produkcji i osoby biorące udział w procesie produkcji, które posiadają określoną wydajność. Zasoby tego samego rodzaju można pogrupować w grupy. Zasoby można przyporządkować do centrów kosztowych.
- Zmiany – określają model czasu pracy, np. pierwsza zmiana od godz. 06:00 do 14:00. Zmiany i modele czasu pracy ustalane są na dzień tygodnia. Dni tygodnia grupowane są w model tygodniowy, który przedstawia profil wydajności dla zasobów produkcyjnych.
- Uruchomienie – z chwilą uruchomienia zlecenia produkcyjnego zwalniane są struktury produkcyjne, tworzony jest harmonogram i pozycje zlecenia w oparciu o podany artykuł produkcyjny. Ponadto rezerwowane są potrzebne materiały, wraz z produktami ubocznymi i zasobami produkcyjnymi. Wyróżnia się uruchomienie jedno i wielostopniowe.
Procesy i dokumenty
W tym rozdziale opisano informacje na temat relacji z różnymi jednostkami biznesowymi oraz instrukcje dotyczące kontroli produkcji w środowisku wielofirmowym. Kontrola produkcji może być stosowana zarówno do produkcji indywidualnej, jak i seryjnej lub masowej. Możliwa jest również produkcja różnorodna (warianty) i produkcja podzielona.
Produkcja podzielona
Proces produkcyjny zawsze odbywa się w odniesieniu do zakładu produkcyjnego. (lokalizacji organizacji logistyki magazynowej). W przypadku produkcji podzielonej, dla poszczególnych lokalizacji, muszą być rejestrowane oddzielnie dane dotyczące produkcji:
- Dane konfiguracyjne (podstawowe dane artykułu, technologia produkcyjna, zestawienie materiałowe (BOM))
- Zasoby produkcyjne
- Magazyny
Lokalizacje nie mogą być określone za pomocą formuł i warunków.
W środowisku jednofirmowym istnieje tylko jeden zakład produkcyjny z jedną lokalizacją, dlatego też produkcja podzielona może być odwzorowana w kontekście produkcji obcej.
Natomiast w środowisku wielofirmowym może istnieć dowolna liczba zakładów produkcyjnych. W obu środowiskach część procesu produkcyjnego może zostać przeniesiona do dostawców zewnętrznych (podwykonawców). W tym celu wykorzystywany jest proces produkcji obcej.
Produkcja podzielona z wykorzystaniem produkcji obcej
Aby rozpocząć proces produkcji obcej, na zleceniu produkcyjnym powinna zostać dodana jedna lub więcej operacji produkcji obcej. Po uruchomieniu zlecenia (ZP) automatycznie generowane są dokumenty zakupu (ZZ). Zamówienie zakupu zawiera materiał, który ma być dostarczony wraz z wyprodukowanym artykułem w produkcji obcej u podwykonawcy. Jednakże, zamówienie zakupu nie jest inicjatorem zlecenia dostawy do podwykonawcy. Cały proces produkcji obcej oraz dostawy do podwykonawcy są kontrolowane za pomocą aplikacji Księgowanie operacji produkcji obcej.
Produkcja podzielona w środowisku wielofirmowym
Jeżeli procesy produkcyjne są rozmieszczone w różnych lokalizacjach organizacji, wówczas etapy produkcji są określone dla każdej lokalizacji z uwzględnieniem zdolności produkcyjnych wykorzystywanych zasobów. Ma to konsekwencje dla danych produkcyjnych, co pokazuje następujący przykład dotyczący konfiguracji operacji:
Lokalizacje należące do kilu firm wymagają:
- Różnych centrów kosztowych dla zasobów
- Różnych jednostek kosztowych
- Utworzenia oddzielnych tras dla lokalizacji
W przypadku zestawień materiałowych:
- Muszą być one utworzone co najmniej raz dla danej lokalizacji
- Posiadać tylko jedną organizację logistyki magazynowej, która jest upoważniona do ich przetwarzania
Są one specyficzne dla danej organizacji tylko wtedy, gdy zostały określone magazyny wydawania materiałów lub magazyny przyjęcia.
W odróżnieniu od technologii, marszrut i zasobów, zestawienia materiałowe mogą być również wykorzystywane oraz powielane w innych lokalizacjach. W celu powielenia zestawienia materiałowego należy upewnić się, że materiał posiada dane dotyczące logistyki magazynowej w lokalizacji docelowej, w której ma zostać powielony.
Zlecenia dystrybucji lub transakcji magazynowych umożliwiają przesunięcia materiału i półfabrykatów między lokalizacjami produkcji. Podczas planowania zapotrzebowania materiałowego, system może automatycznie obliczać propozycje dystrybucji materiału. Podstawą do tego jest ustawienie zakresu wymagań w danych dyspozycji dla artykułu.
Przegląd etapów procesu produkcyjnego
Podstawą całego procesu produkcyjnego są zlecenia produkcyjne. Zlecenia produkcyjne mogą być generowane:
- Z planowania zapotrzebowania materiałowego
- Z zamówień sprzedaży
- Ręcznie lub przekazywane za pośrednictwem interfejsu
Proces z planowania zapotrzebowania materiałowego
Planowanie zapotrzebowania materiałowego uwzględnia wymagania z procesu sprzedaży, produkcji, zakupu wewnętrznego dla wszystkich lokalizacji oraz prognoz zapotrzebowania. Zlecenia produkcyjne mogą być generowane i także uruchomione z wykorzystaniem propozycji produkcyjnych.
Generowanie zlecenia produkcyjnego z zamówienia sprzedaży
Zlecenia produkcyjne mogą być generowane automatycznie (tylko dla skonfigurowanych artykułów) lub ręcznie dla wszystkich artykułów produkcyjnych przy pomocy zamówienia sprzedaży.
Uruchomienie
Przy uruchomieniu zleceń produkcyjnych, generowane i planowane są niezbędne pozycje dla materiałów, operacji i zasobów. W ten sposób obliczane są ilości i czasy. Materiał jest dynamicznie rezerwowany pod względem dostępności. Nie jest on trwale rezerwowany dla tego zlecenia, ale też nie jest widoczny jako dostępny w kalkulacji dostępności. Wykorzystywane zasoby są zarezerwowane na wymagany w procesie produkcyjnym okres. Uruchomienie odbywa się w odniesieniu do podstawowych zestawień materiałowych, marszrut i technologii. Alternatywnie, poszczególne pozycje zleceń produkcyjnych mogą być również tworzone lub zmieniane ręcznie. Na podstawie tych informacji mogą być generowane różne dokumenty produkcyjne. Po wydaniu materiału z magazynu, opcjonalnie z integracją akwizycji danych maszynowych (MDA) lub akwizycji danych produkcyjnych (PDA), odbywa się właściwa produkcja.
Po indywidualnych zgłoszeniach produkcji, artykuł produkcyjny jest księgowany jako przyjęcie towaru.
Poniższy schemat pokazuje wybrane współzależności produkcji:
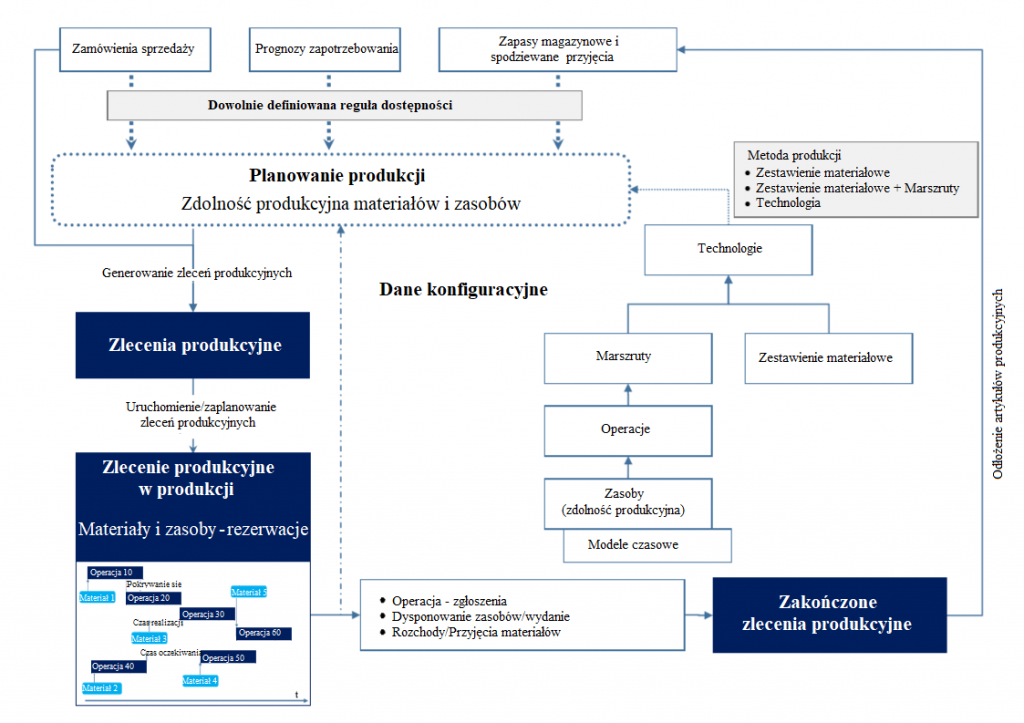
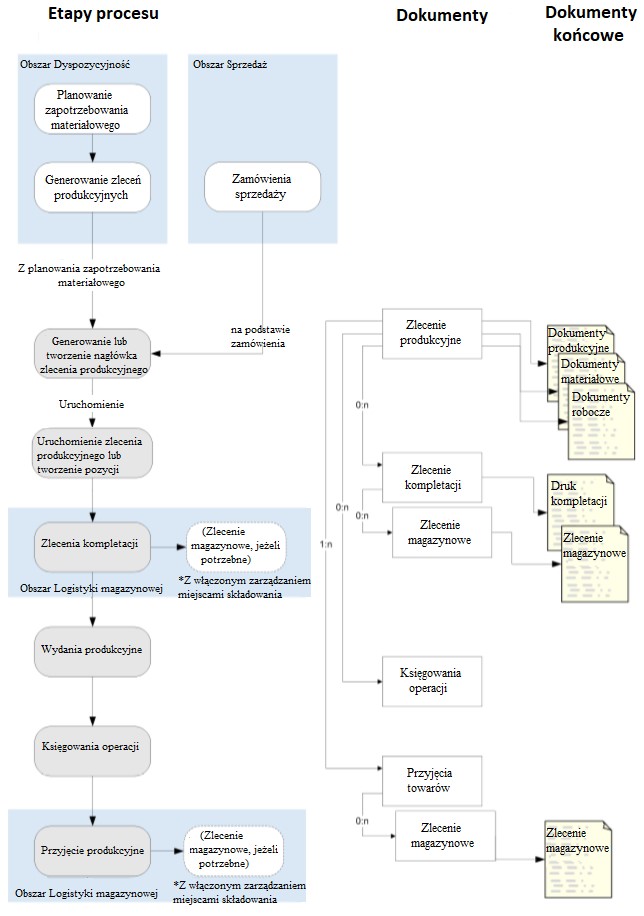
Etapy procesu, dokumenty i dokumenty końcowe w produkcji
Procesy w kontroli produkcji rozpoczynają się od utworzenia zlecenia produkcyjnego, obejmują uruchomienie i harmonogramowanie zlecenia, przydziały zdolności produkcyjnych, kontrolę i planowanie danych operacyjnych. Dostępne zdolności produkcyjne są określane w sposób zmienny poprzez przydzielanie profili zdolności produkcyjnych w modelach tygodniowych (przydzielanie modelu czasowego, model zmianowy). Jeśli nie można przypisać stałego modelu tygodniowego dla określonych zasobów, które są dostępne lub wymagane, wówczas można elastycznie zdefiniować dostępne zdolności produkcyjne do zmiany lub do modelu czasowego za pomocą aplikacji Wydajność zasobów.
Dokumenty robocze wymagane dla danego procesu produkcyjnego są tworzone na podstawie zlecenia produkcyjnego. Wydruk dokumentów roboczych musi być wydany możliwie najpóźniej, aby wszelkie niezbędne zmiany były na nich uwzględniane i ujęte w procesie produkcji.
Zgłoszenie zmian jest przeprowadzane za pomocą funkcji: Księgowania operacji, Rozchody na produkcję i Przyjęcia towaru. Zgłoszenia mogą się odbywać również za pośrednictwem urządzeń do wprowadzania danych biznesowych np. przy użyciu odpowiednich interfejsów importowych. Zgłoszenie to służy jako podstawa do uruchomienia zarezerwowanych materiałów i zasobów, księgowania powstałych transakcji magazynowych i usługowych oraz dostarczania tych danych do kontroli.
Proces produkcji obcej
Operacje produkcji obcej mogą być tworzone w zleceniu produkcyjnym wraz z artykułami produkcji obcej i materiałami dostarczanymi do sprzedawców.
Zasób o odpowiedniej wydajności zasobów dla operacji produkcji obcej jest oferowany przez podwykonawcę. Do obserwacji zdolności produkcyjnych podwykonawcy wymagają konkretnych informacji, które są przechowywane w aplikacji Konfiguracja w pozycji Dane dostawcy lub w danych konfiguracyjnych dostawcy w pozycji Dane produkcyjne w polach Początek pracy, Dzienna wydajność i Kalendarz zakładowy. Jeżeli w danych konfiguracyjnych dostawcy nie wprowadzono żadnych zmian, to obowiązują te, które zostały zdefiniowane w aplikacji Konfiguracja.
Jeżeli zlecenie produkcyjne zawiera operacje produkcji obcej, wówczas podczas uruchomienia generowane są dodatkowe zamówienia zakupu.
Etapy procesu produkcji obcej:
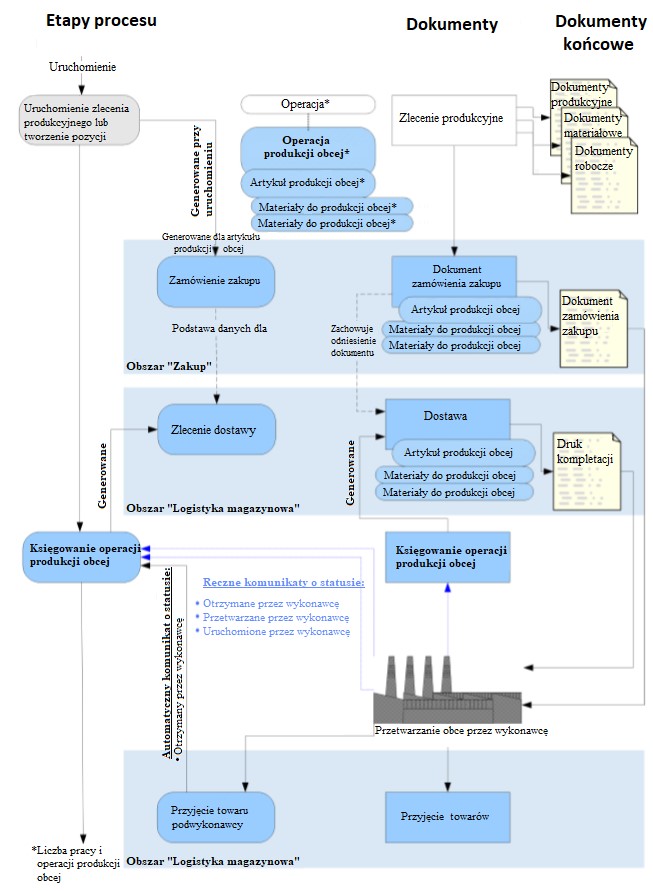
Łańcuch dokumentów powiązanych
W łańcuchu dokumentów powiązanych zlecenia produkcyjnego, widoczne są dokumenty:
- Zamówienia sprzedaży – jeżeli zlecenie produkcyjne zostało wygenerowane z zamówienia sprzedaży. Powiązanie może być utworzone automatycznie lub ręcznie dla skonfigurowanych artykułów i tylko ręcznie dla wszystkich innych artykułów produkcyjnych.
- Kalkulacje kosztów produktu (kalkulacja zlecenia) – jeżeli skonfigurowany artykuł został obliczony automatycznie lub kalkulacja zlecenia została ręcznie powiązana ze zleceniem produkcyjnym.
- Zamówienia zakupu – dla uruchomionego zlecenia produkcyjnego zawierającego operacje produkcji obcej.
- Przyjęcia towarów z produkcji – na podstawie zgłoszenia zakończenia (i zaksięgowania przyjęć) artykułu produkcyjnego i powiązanych produktów ubocznych.
- Kompletacje produkcji – na podstawie przeniesienia składników materiałów z magazynu głównego do magazynu produkcyjnego.
Wyświetlanie i przetwarzanie za pomocą aplikacji Lista: Zlecenia produkcyjne
Zlecenia produkcyjne, księgowania operacji i błędy uruchomienia (z uwagi na późniejsze zmiany w wydajności zarezerwowanych zasobów) mogą być wyświetlane w aplikacji Lista: Zlecenia produkcyjne.
W tym miejscu użytkownik może w szybki sposób przejrzeć zlecenia produkcyjne, wraz z ich pozycjami i statusem oraz rozpocząć ich masową realizację za pomocą aplikacji Listy: Zlecenia produkcyjne.
W aplikacji można wykonywać następujące czynności:
- Wyszukiwanie i wybór zleceń produkcyjnych
- Wyświetlanie łańcucha dokumentów powiązanych dla wybranego zlecenia produkcyjnego
- Dokonywanie zmian w aplikacji Zlecenia produkcyjne w celu
- Wydanie zleceń produkcyjnych
- Zablokowanie zleceń produkcyjnych
- Uruchomienie zleceń produkcyjnych
- Zmiana ilości i terminów zleceń produkcyjnych
- Wydanie dokumentów roboczych dla zleceń produkcyjnych
- Generowanie zleceń kompletacji
- Ustawianie ilości dyspozycyjnych
- Obliczanie dostępności
Dane domyślne i konfiguracyjne w procesie produkcji
Podstawowe ustawienia dla generowanych zleceń produkcyjnych dokonywane są w aplikacji Rodzaje zleceń produkcyjnych, która umożliwia ich identyfikacje, a także wprowadzenie ustawień domyślnych i dodatkowych, dla określonego rodzaju zleceń.
Jeśli aktywowane jest ręczne odniesienie do zlecenia, każde zlecenie produkcyjne musi być przyporządkowane do pozycji zamówienia sprzedaży.
W przypadku zleceń produkcyjnych, które zostały połączone z zamówieniami sprzedaży, nie ma potwierdzenia ilości i terminów w zamówieniu sprzedaży. Są one dostępne tylko wtedy, gdy zlecenia produkcyjne zostały wygenerowane na podstawie pozycji zamówień sprzedaży.
Jeżeli zlecenia produkcyjne są generowane z pozycji zamówienia sprzedaży, to zlecenia produkcyjne są otwierane automatycznie z ich podstawowymi informacjami na podstawie domyślnych wartości rodzaju zlecenia produkcyjnego i ilości wprowadzonej w zamówieniu sprzedaży.
Ważne ustawienia w aplikacji Rodzaje zleceń produkcyjnych:
- Zakres numerów wykorzystywany jest do automatycznego przydzielania numerów do zleceń produkcyjnych
- Magazyn produkcyjny, magazyn wydań i magazyn przyjęć. Magazyn produkcyjny odbiera materiały, które są wymagane podczas produkcji
- Wymagane są klucze księgowania do wydań materiałów z magazynu produkcyjnego.
- Wymagania dotyczące rezerwacji pozycji materiałowych
- Rodzaj kompletacji jest konieczny, jeżeli magazyn produkcyjny jest zaopatrywany przez magazyn główny (ustrukturyzowany lub nieustrukturyzowany). Przeniesienie z magazynu głównego do magazynu produkcyjnego jest kontrolowane przez zlecenie kompletacji
- Rodzaj zamówienia zakupu i rodzaj zlecenia dostawy. Aplikacje służą do generowania zamówień zakupu i dostawy materiałów, jeżeli w zleceniu produkcyjnym uwzględniono operacje produkcji obcej
Dane konfiguracyjne produkcji opisują strukturę produkcji i jej przebieg. Należą do nich:
- Operacje, do których przypisane są zasoby niezbędne do wykonania operacji, przykładowo osoby uczestniczące w produkcji i maszyny
- Marszruty, do których przypisane są operacje. Przypisanie uwzględnia kolejność i zależności, w których mają zostać wykonane
- Zestawienia materiałowe, w których materiał jest wymieniony w ilości wymaganej do produkcji. W razie potrzeby wymienione są również produkty uboczne powstające podczas produkcji
- Technologie, w których ustanowiono interakcję pomiędzy operacjami i materiałami wykorzystywanymi podczas operacji
Aby przeprowadzić proces produkcyjny, musi zostać zdefiniowane przynajmniej jedno zestawienie materiałowe z jedną pozycją materiałową. Możliwe jest wtedy utworzenie artykułu produkcyjnego.
Więcej informacji znajduje się w dokumencie Dane konfiguracyjne produkcji.
Typy harmonogramów
Typ harmonogramu ustala zasady według których odbywa się harmonogramowanie zlecenia produkcyjnego. Dostępne są następujące typy harmonogramów:
- Do przodu o jeden poziom
- Wstecz o jeden poziom
- Do przodu o wiele poziomów
- Wstecz o wiele poziomów
- Do przodu o wiele poziomów w kolejności
- Wstecz o wiele poziomów w kolejności
Datę rozpoczęcia i zakończenia zlecenia produkcyjnego można obliczyć według następujących typów harmonogramów:
- Wprzód bez limitu zdolności produkcyjnych
- Wprzód z limitem zdolności produkcyjnych
- Wstecz bez limitu zdolności produkcyjnych
- Wstecz z limitem zdolności produkcyjnych.
Podczas uruchomienia zlecenia produkcyjnego, struktury produkcyjne są podzielone, jak poniżej:
- Dla wszystkich ważnych pozycji materiałowych w zestawieniach materiałowych generowane są rezerwacje materiałowe, które mają wpływ na obliczenie dostępności
- Dla wszystkich ważnych pozycji produktów ubocznych w zestawieniu materiałowym generowane są pozycje produktów ubocznych
- Dla wszystkich ważnych operacji marszruty generowane są pozycje operacji
- Dla wszystkich ważnych zasobów operacji generowane są pozycje zasobów i alokacje
- Dla operacji produkcji obcej generowane są zamówienia zakupu
Procedura przekazywania zgłoszeń w procesie produkcyjnym
Można wybrać etap procesu, dla którego mają być generowane zgłoszenia istotne dla procesu produkcyjnego (np. zakończenie inwentaryzacji). Można określić następujące informacje:
- Zgłoszenie przy przyjęciu towaru z produkcji – pozycje oznaczone do automatycznego zgłoszenia są księgowane podczas zgłaszania wyprodukowanego artykułu na przyjęciu towaru
- Zgłoszenie dla raportów operacyjnych – pozycje oznaczone do automatycznego zgłoszenia są księgowane podczas księgowania operacji
Istnieje również opcja ręcznej procedury przekazywania zgłoszenia.
Wydanie materiału może być również księgowane indywidualnie za pomocą aplikacji Rozchody na produkcję. Pozycje materiałowe, księgowania operacji i operacje produkcji obcej, które posiadają automatyczne oznaczenie nie mogą być zgłaszane ręcznie. Mogą one zostać zaksięgowane ręcznie tylko wtedy, gdy pozycje nie mają automatycznego oznaczenia.
Identyfikacja artykułów
Artykułami można zarządzać za pomocą identyfikatorów. Identyfikatory są używane do jednoznacznego rozpoznania artykułu lub jego ilości. Można zastosować następujące identyfikatory istotne dla produkcji:
- Partia
- Szarża produkcyjna/seria
- Numer seryjny z ewidencją zapasów
W niektórych branżach przemysłowych niezbędne są informacje o specyfikacjach materiałów używanych w produkcji (śledzenie serii). Jeżeli artykuł produkcyjny jest zarządzany przez specyfikacje, wówczas tworzona jest analiza specyfikacji źródłowej i jej zastosowanie. Analiza identyfikacji źródłowej i jej zastosowanie dostarcza informacje o pochodzeniu i wykorzystaniu specyfikacji. W procesie produkcji, są one śledzone na wszystkich etapach produkcji, w których wyprodukowane artykuły są zarządzane przez identyfikacje. W ten sposób może być monitorowana cała historia artykułu: od przyjęcia surowca do dostarczenia klientowi produktu końcowego wyprodukowanego z surowca. Taką samą metodą możliwe jest prześledzenie historii identyfikacji, która została uwzględniona w reklamacji klienta, powracając do poszczególnych surowców.
Dla skonfigurowanych artykułów z tym samym numerem, ale mają różne właściwości, można przypisać dodatkową identyfikację poprzez specyfikację.
Metoda produkcji
W aplikacji Konfiguracja określa się dla każdego mandanta, czy ma pracować z procesami produkcyjnymi czy bez. Produkcja bez określonej metody produkcji oznacza, że w procesach nie są dostępne żadne technologie.
Przypisanie materiału do operacji nie jest możliwe w danych konfiguracyjnych, co z kolei wpływa zarówno na automatyczne uruchomienie, jak i produkcję obcą. Materiał przekazany do operacji produkcji obcej nie może być przypisany z wyprzedzeniem. Takie przyporządkowanie może być wykonane ręcznie w zamówieniu.
Zaletą pracy bez technologii jest to, że dla każdego artykułu produkcyjnego można indywidualnie określić, z jakimi marszrutami i zestawieniami materiałowymi ma być produkowany i obliczany.
Dokumenty zlecenia produkcyjnego
Do zlecenia produkcyjnego można wystawić następujące dokumenty:
- Dokument produkcyjny
- Karta obiegowa
- Lista materiałów
- Specyfikacja materiału
- Lista prac
- Karta pracy
- Druk dostawczy produkcji obcej
Dokumenty, które mają zostać udostępnione, są określone w aplikacji Konfiguracja w funkcji Produkcja, podfunkcji Dokumenty.
Wyjątkiem jest zlecenie kompletacji. Jest ono niezbędne dla formy organizacji magazyn główny – magazyn produkcyjny. Szablon dokumentu końcowego jest tworzony w funkcji Logistyka magazynowa, podfunkcja Dokumenty.
Więcej informacji na temat tworzenia dokumentów zlecenia produkcyjnego można znaleźć w dokumencie Dokumenty produkcyjne.
Ilości i czasy w procesie produkcyjnym
Czasy w procesie produkcyjnym: okres przetwarzania (te) i czasy przezbrojenia (tr) można określić dla operacji. W tym celu w danych konfiguracyjnych należy wprowadzić wartości domyślne. Te wartości domyślne mogą być zmienione ręcznie w zleceniu produkcyjnym.
Formuły do obliczania okresów przetwarzania i czasów przezbrojenia mogą być stosowane na postawie zasobów lub parametrów operacji. Można odwołać się do cech konfiguracyjnych z konfiguratora produktu, metody produkcji, cech artykułów lub innych pól artykułów produkcyjnych lub ilości zleceń produkcyjnych.
Można również zdefiniować dodatkowe czasy tolerancji pomiędzy operacjami i wykorzystać formuły do obliczeń.
Istnieje także możliwość zdefiniowania czasów transportu, które podlegają jedynie ręcznej edycji.
Podobne udogodnienia są dostępne dla stałych i zmiennych ilości zużycia materiałów. Ilości stałe i zmienne mogą być obliczane za pomocą formuł.
Alternatywne artykuły mogą być zdefiniowane w zestawieniach materiałowych i wybrane w zleceniu produkcyjnym.
Odpad
Odpad to ilość, która nie może być wykorzystana w produkcji lub ma wadę produkcyjną.
W przypadku pozycji materiałowych, dodatkowe zużycie materiału można obliczyć automatycznie za pomocą współczynników odpadu.
Ilość/(ilość – (ilość * współczynnik odpadu/100)) = dodatkowe zapotrzebowanie
Przy współczynniku odpadu 15%, ilość 20 sztuk skutkuje dodatkowym zapotrzebowaniem na 4 sztuki:
20/(20 – (20 * 0,15)) = x
20/17 = x
1,176 = x
Dodatkowe zapotrzebowanie oblicza się z 20 szt. * 1,176 = 40.
Dodatkowe zużycie materiału może być automatycznie odjęte poprzez wprowadzenie ilości odpadu z artykułu produkcyjnego w przyjęciu towaru. Również ilość odpadu można księgować za pomocą oddzielnej aplikacji.
Produkty uboczne
Produkt uboczny powstaje na różnych etapach produkcji produktu głównego. Produkty uboczne to artykuły magazynowe, które są księgowane w magazynie przyjęcia, gdy artykuł produkcyjny jest przyjmowany. Mogą one również podlegać częściowym kosztom produkcji w obliczeniach całościowych procesu produkcyjnego.
Są one odejmowane ze stanu magazynowego jako materiał, a następnie ponownie księgowane na stan magazynowy jako produkt uboczny po przyjęciu zgłoszenia o zakończeniu produkcji.
W przypadku produktów ubocznych termin realizacji dla artykułu można określić w zleceniu produkcyjnym. Termin ten jest uwzględniany w dostępności materiału jako planowane przyjęcie.
Opisy dla danych konfiguracyjnych
Można wprowadzać dodatkowe teksty dla prawie wszystkich danych konfiguracyjnych w produkcji. Teksty te służą do wprowadzenia dodatkowego opisu lub uwag dla danych konfiguracyjnych. Zazwyczaj są one używane do sporządzania dokumentów w celu uzupełnienia tekstów w dokumentach końcowych.
Teksty z danych konfiguracyjnych są przyjmowane zgodnie z określoną kolejnością podczas uruchomienia zleceń produkcyjnych.
Zależności między operacjami i zasobami
Operacje w marszrucie i zasoby wykorzystywane w operacji mają różne rodzaje zależności.
Zależności mogą być:
- Rozpoczęte nie wcześniej niż
- Rozpoczęte po
- Rozpoczęte równolegle do
- Zakończone równolegle do
- Zakończone nie później niż
- Zacząć się nakładać na siebie z
Rezerwacje w produkcji
Zasoby (osoby uczestniczące w produkcji, maszyny, narzędzia) i materiały (półfabrykaty, surowce, zakupione części) mogą być zarezerwowane do produkcji.
Rezerwacje zasobów
Zasoby mają zdolności produkcyjne, które są definiowane w modelu tygodniowym. Wolne zdolności produkcyjne zasobów, które nie są jeszcze udokumentowane przez operacje w istniejących zleceniach produkcyjnych, są automatycznie rezerwowane w momencie uruchomienia operacji.
Rezerwacja zasobów może być edytowana (w widoku graficznym) lub wyświetlana w aplikacji Wykorzystanie zasobów. Możliwe jest także wyświetlenie planowanych, tymczasowych rezerwacji zasobów, które zostały określone w planowaniu zapotrzebowania materiałowego. Rezerwacje zasobów są zwalniane automatycznie po całkowitym zgłoszeniu operacji lub skompletowaniu zlecenia produkcyjnego. Rezerwacje, które nie zgadzają się z faktycznym zleceniem produkcyjnym, które zostały uruchomione mogą być wyświetlane za pomocą Lista: Zlecenia produkcyjne/błędy rozdzielenia obciążenia. Może się to zdarzyć w przypadku późniejszej zmiany (zmniejszenia) zarezerwowanych zdolności produkcyjnych zasobów.
W takich przypadkach należy ponownie uruchomić zlecenie produkcyjne.
Jeżeli zdolności produkcyjne zasobów nie odpowiadają już ich zdolnościom produkcyjnym lub jeżeli zdolności produkcyjne nie odpowiadają istniejącemu modelowi tygodniowemu, można je ponownie zdefiniować za pomocą aplikacji Wykorzystanie zasobów.
Rezerwacje materiału
Zarówno zapotrzebowania (materiał, wymagane półfabrykaty), jak i źródła pokrycia zapotrzebowania (artykuły produkcyjne, produkty uboczne, składniki do produkcji) mogą być zarezerwowane. Warunkiem wstępnym jest zarezerwowanie artykułów danej lokalizacji i magazynów wykorzystywanych w zleceniach produkcyjnych. Ponadto, dla każdego artykułu, który może być wykorzystany w produkcji, można określić, czy jest on dozwolony do rezerwacji, czy nie.
Źródło pokrycia zapotrzebowania na pozycje materiałowe może nastąpić albo poprzez istniejący stan magazynowy albo poprzez planowane przyjęcia (np. zamówienia zakupu lub, jeśli chodzi o półfabrykaty, nawet inne zlecenia produkcyjne).
Rezerwacje mogą być generowane ręcznie, automatycznie bez terminu rezerwacji lub automatycznie z terminem rezerwacji:
- Automatycznie bez terminu rezerwacji oznacza, że istniejące zapasy lub planowane przyjęcia zostaną zarezerwowane w momencie uruchomienia lub wydania. Ten moment automatycznej rezerwacji może być kontrolowany poprzez rodzaj zlecenia
- Rezerwacji można dokonać natychmiast po uruchomieniu zlecenia lub tylko podczas jego wydania
- Alternatywnie można generować rezerwacje za pomocą przycisku akcji Pozycje rezerwowe lub Ustaw ilości zadysponowane (jeśli są aktywne w rodzaju zlecenia produkcyjnego)
Ponadto, aplikacja Alokacja zapasów może być wykorzystana do rezerwacji istniejących zapasów.
Jeżeli rezerwacje są wykorzystywane w produkcji, to wszystkie pozycje materiałowe muszą mieć zarezerwowane zapasy zanim zostaną zaksięgowane wydania produkcyjne lub zostaną wygenerowane zlecenia kompletacji.
Jeśli stosuje się przydział do dostawy (alokację zapasów) lub trzeba ustalić ilości dyspozycyjne, to reguła ta ma zastosowanie również do ilości dyspozycyjnych.
Jeżeli rezerwacje nie są już konieczne lub ilości zarezerwowanych pozycji materiałowych są pilnie wymagane przez inne zlecenia, wówczas rezerwacje można ręcznie usunąć w aplikacji Rezerwacje.
Jeżeli zapasy zostały zarezerwowane, wpływa to również na planowanie zapotrzebowania materiałowego. Więcej informacji na ten temat można znaleźć w dokumencie Wprowadzenie: Dyspozycja.
Należy zwrócić uwagę na następujące cechy szczególne:
Planowany przychód produkcyjny z wygenerowanego zlecenia produkcyjnego może być automatycznie zarezerwowany na zapotrzebowanie pozycji zamówienia sprzedaży w przypadku produkcji opartej na zamówieniach (zlecenie produkcyjne generowane jest z zamówienia sprzedaży)
W przypadku wielostopniowego uruchomienia zaplanowane przychody półfabrykatów mogą być automatycznie zarezerwowane na potrzeby pozycji (materiał) zlecenia produkcyjnego wyższego rzędu. Warunkiem wstępnym jest, aby przychody znajdowały się zawsze w tym samym magazynie co rozchody.
Produkty uboczne nie są rezerwowane automatycznie poprzez zamówienia wyższego rzędu.
Status
Informacja o statusie zlecenia produkcyjnego i jego formularz pozycji stanowi dodatkowy element informacyjny. Dzięki tej informacji, użytkownik może szybko zorientować się w bieżącym statusie przetwarzania zlecenia produkcyjnego i poszczególnych pozycji zlecenia. Informacja o statusie jest przechowywana w systemie.
Statusy są wprowadzane na poziomie całego zlecenia produkcyjnego i poszczególnych pozycji zamówienia. W związku z tym status nagłówka zlecenia zestawia status poszczególnych pozycji.
Więcej informacji o statusach można znaleźć w dokumencie Zlecenia produkcyjne.
Warianty w produkcji
Dostępnych jest kilka opcji wspierających produkcję z wariantami artykułu produkcyjnego. W przypadku prostych wariantów artykułów, które różnią się od innych artykułów tylko jedną cechą, rekomendowane jest utworzenie artykułu jako odniesienia i wariantu artykułu. Wszystkie warianty można produkować tylko z jednym zestawieniem materiałowym i jedną marszrutą za pomocą warunków i formuł, które odnoszą się do wariantów artykułu. Należy przeanalizować możliwy spadek przejrzystości i prześledzenia na podstawie określonego poziomu produkcji oraz liczby formuł i zastosowanych warunków. Z czego wynika, że lepiej jest pracować z kilkoma zestawieniami materiałowymi i marszrutami lub metodami produkcji.
W przypadku bardziej złożonych wariantów artykułów, należy odpowiednio skonfigurować system aby każdy wariant został wprowadzony jako niezależny artykuł. Jeżeli są stosowane cechy konfiguracyjne (cechy artykułu lub konfiguracji produktu), wówczas należy je ocechować/opisać za pomocą formuł i warunków.
Ze względu na fakt, że wariant jest zapisywany jako konfiguracja, a nie jako artykuł, to ten sam wariant musi być ponownie dostępny dla nowej produkcji albo w istniejącym zleceniu produkcyjnym albo w pozycji zamówienia sprzedaży.
Jeżeli nagłówek zlecenia produkcyjnego lub istniejąca skonfigurowana pozycja zamówienia sprzedaży zostaną powielone, wówczas konfiguracja zostanie również powielona. W celu późniejszej identyfikacji skonfigurowanych artykułów, system udostępnia specyfikacje.
Więcej informacji można znaleźć w dokumencie Konfiguracja produktu.
Produkcja na zamówienie i produkcja na magazyn
Niektóre produkty są produkowane tylko na życzenie zleceniodawcy. Może to być artykuł indywidualnie skonfigurowany dla zleceniodawcy lub nawet standardowy artykuł produkcyjny. Inne produkty są produkowane w oparciu o prognozy i długotrwałe planowanie magazynowe. Oba rodzaje produkcji mogą być kontrolowane za pomocą systemu ERP.
Produkcja na zamówienie
W przypadku produkcji na zamówienie, decyzja dotycząca tego, co zostanie dostarczone, kiedy i do kogo leży po stronie sprzedawcy. Takie decyzje podejmowane są przed decyzjami związanymi z produkcją, czyli kiedy i co produkować. W przypadku produkcji na zamówienie, produkcja danego produktu rozpoczyna się dopiero po otrzymaniu zamówienia na ten wyrób. Taka sytuacja dominuje w produkcji jednostkowej lub małoseryjnej, w szczególności w odniesieniu do produktów o wielu wariantach oraz tych, które są indywidualnie skonfigurowane przez klienta.
Produkcja na zamówienie jest wspierana w procesie sprzedaży. Istnieją artykuły skonfigurowane i nieskonfigurowane.
Jeżeli tworzone jest odniesienie do zlecenia pomiędzy zleceniem produkcyjnym a zamówieniem sprzedaży, to dostępne są poniższe możliwości.
W rodzaju zlecenia sprzedaży można wybrać jedną z dwóch opcji:
- Zlecenie produkcyjne ma być wygenerowane ręcznie dla wszystkich rodzajów artykułów produkcyjnych
- Zlecenie produkcyjne ma być wygenerowane automatycznie dla artykułów skonfigurowanych.
Zlecenie produkcyjne można również ręcznie połączyć z pozycją zamówienia sprzedaży. We wszystkich przypadkach tworzona jest relacja dokumentów pomiędzy tymi zleceniami i zamówieniami. Terminy i ilości są przyjmowane z zamówienia sprzedaży. Zmiany w ilościach są możliwe do momentu uruchomienia zlecenia produkcyjnego. Zmiany terminów w zamówieniu sprzedaży są również uwzględniane w przypadku uruchomionych zleceń produkcyjnych. Nie następuje automatyczne uruchomienie zleceń produkcyjnych.
- Ilość planowana w zleceniu produkcyjnym nie może być mniejsza niż ilość w zamówieniu sprzedaży. Zwiększenie ilości w zleceniu produkcyjnym jest dozwolone po potwierdzeniu komunikatów ostrzeżeń w systemie
- Data wysyłki jest przyjmowana z zamówienia sprzedaży i wprowadzana w polu Koniec najpóźniej i jest używana jako wartość domyślna dla pól Aktualny koniec i Aktualny początek
UwagaW przypadku wielopoziomowego uruchomienia zlecenia produkcyjnego, tylko najwyższe zlecenie zawiera produkt końcowy z zamówienia sprzedaży, a zatem zawiera również odniesienie do pozycji zamówienia sprzedaży. Półfabrykaty są traktowane jak artykuły magazynowe.
Produkcja na magazyn
Decyzje dotyczące produkcji są podejmowane wcześniej niż decyzje dotyczące sprzedaży w produkcji na magazyn. Wyprodukowane artykuły są przechowywane w magazynie wyrobów gotowych i pozostają tam, dopóki nie zostaną zamówione przez klienta. W przypadku produkcji wielkoseryjnej, wariantowej, masowej i produktów ubocznych dominuje produkcja na magazyn.
Zlecenia produkcyjne koncentrują się w dużej mierze na planowaniu zapotrzebowania materiałowego z generowanymi przez niego propozycjami produkcji. Propozycje produkcji mogą być również uruchamiane przez zamówienie sprzedaży jako określone źródło zapotrzebowania. Ponadto uwzględniane są również minimalne i bezpieczne poziomy stanu magazynowego, tzw. kryteria logistyki magazynowej i planowanie ilości z prognoz zapotrzebowania.
Podczas, gdy w planowaniu dostępne jest odniesienie wymaganej ilości do jej pochodzenia, w zleceniu produkcyjnym nie ma już odniesienia do jego pochodzenia.