In order to receive a delivery, it is necessary to select a confirmed WM- document (marked with a down arrow) on the list and click the button [Take Receipt].
- Have the status Confirmed
- Have no associated WM+ document
- Originate from the POS workstation or the ERP system
- Have the target warehouse specified as a warehouse available for WM-/WM+ documents within a center to which the POS workstation is assigned
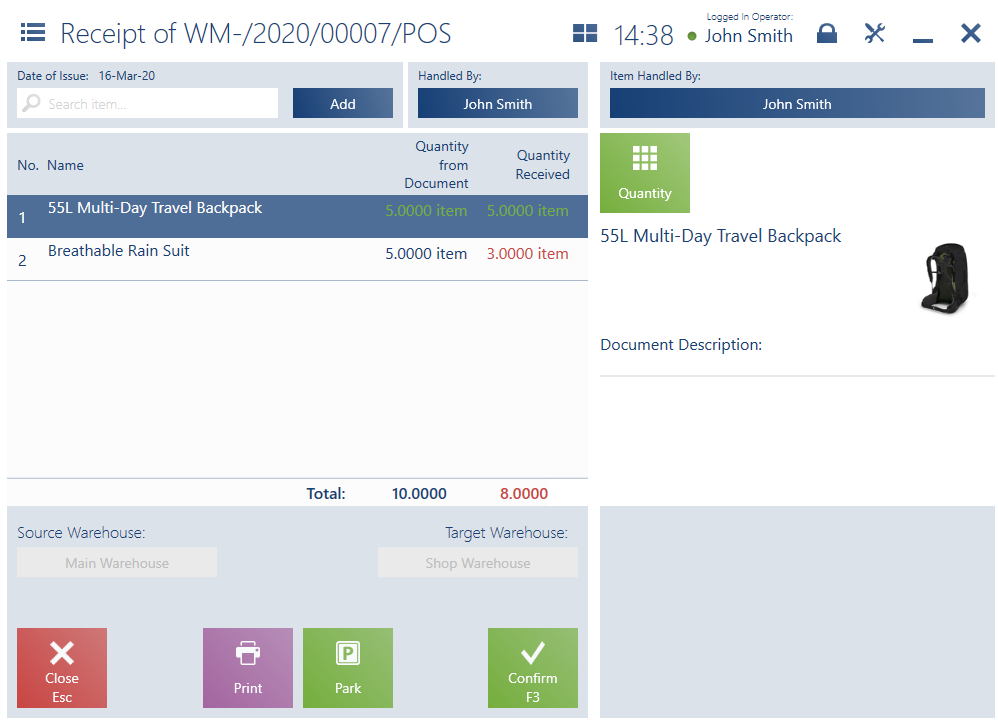
On the receipt form of a WM- document, it is necessary to enter delivery items using one of the following options:
- Selecting them on the item list
- Scanning them
- Manually changing quantities of a given item
In contrast to the form of a new WM- document, the delivery receipt form contains the following columns on the document item list:
- No.
- Name
- Quantity from Document
- Quantity Received
- Item Code (hidden by default)
If an entered item has been received with a quantity consistent with a value displayed in the column Quantity from Document, such an item is marked in green. In the case of a shortage or surplus, the item is marked in red (in the Quantity Received column).
Below the list of document items, the application presents information on:
- Sum of item quantities from a document
- Sum of received item quantities
The lower part of the document window contains the following buttons:
- [Confirm] – it confirms the document, generating a receiving and delivery report (RDR) and a confirmed WM+ document
- [Park] – it saves the document as unconfirmed for further processing
- [Print]
The preview of a receiving and delivery report (for consistencies and inconsistencies in a delivery receipt) is analogous to the receipt form of a WM- document.
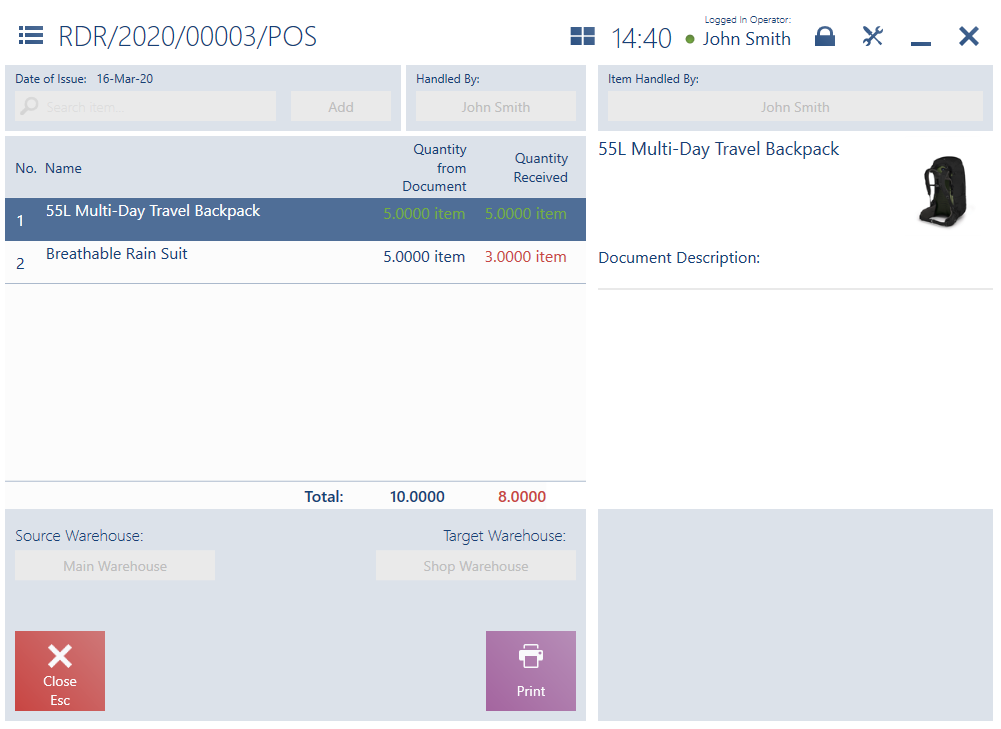
On the list of warehouse documents, it is possible to cancel a RDR document.
If the parameter Automatically generate WM- for remaining items is active, before a WM- created in the ERP system is confirmed on the POS workstation, the system verifies whether a released quantity is equal to the quantity from the retrieved document. If these quantities are different, the user may:
- Create a new WM- document for differences between the WM- retrieved from the headquarters and the actual quantity in the WM- document
- Abandon the creation of another WM- document