W niniejszym biuletynie opisane zostały przykłady wykorzystania Planu produkcji z zastosowaniem różnych wariantów parametryzacji dokumentu PP.
Jak za pomocą Planu produkcji uzyskać informację o ilości produktu potrzebnej do wytworzenia w danym okresie planistycznym?
Plan produkcji umożliwia m. in. uzyskanie informacji na temat ilości produktu potrzebnej do wytworzenia w danym okresie planistycznym. Potrzeba wytworzenia produktu może wynikać, np. z zarejestrowanych w systemie zamówień sprzedaży.
Parametryzacja definicji dokumentu PP
W pierwszej kolejności należy odpowiednio przygotować dokument Planu produkcji, aby był przeliczany wg interesującego nas zakresu parametrów. Jeśli chcemy, by Plan produkcji zwracał informacje o zapotrzebowaniu na produkty w określonych okresach planistycznych, to na definicji dokumentu PP w odpowiednim centrum struktury firmy należy takie okresy planistyczne zdefiniować:
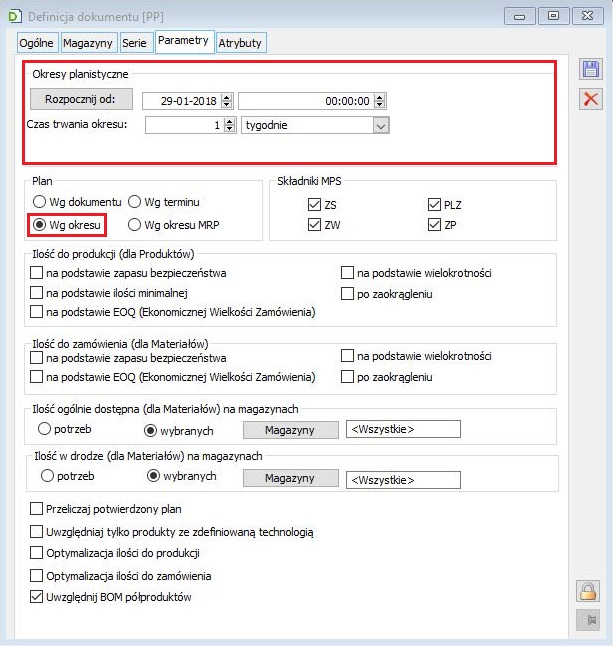
Dodatkowo, jeśli wśród analizowanych produktów są takie, dla których nie określono technologii podstawowej (na karcie towaru), to aby były one widoczne na Planie produkcji, należy na definicji dokumentu PP pozostawić niezaznaczony parametr: Uwzględniaj tylko produkty ze zdefiniowaną technologią:
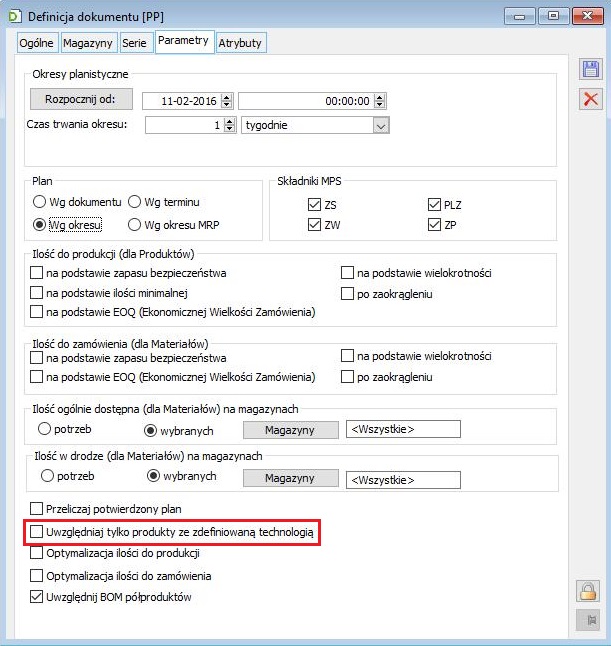
Nowy dokument Planu produkcji będzie domyślnie przyjmował parametryzację, jaką zastosowano na jego definicji w danym centrum struktury firmy, jednak w zależności od potrzeby, niektóre ustawienia można będzie dodatkowo zmienić z poziomu dokumentu.
Przykład obliczania ilości produktu, koniecznej do uzupełnienia w kolejnych okresach planistycznych, na potrzeby realizacji zamówień sprzedaży
W systemie zarejestrowano następujące potwierdzone zamówienia sprzedaży:
ZS-1 na 10 szt. P1, z datą realizacji 01-02-2019, na magazyn MAG
ZS-2 na 20 szt. P1, z datą realizacji 02-02-2019, na magazyn MAG
ZS-3 na 30 szt. P1, z datą realizacji 03-02-2019, na magazyn MAG
ZS-4 na 10 szt. P1, z datą realizacji 06-02-2019, na magazyn MAG
ZS-5 na 20 szt. P1, z datą realizacji 08-02-2019, na magazyn MAG
ZS-6 na 30 szt. P1, z datą realizacji 01-03-2019, na magazyn MAG
Na magazynie MAG znajdują się 4 szt. produktu P1.
Dodano nowy Plan produkcji, którego definicję sparametryzowano jak w punkcie 1.1.
Na dokumencie wskazana została grupa produktów, która zawiera produkt P1 oraz magazyn, na który wystawione zostały zamówienia.
Dodatkowo zaznaczono, że Plan produkcji ma uwzględnić dokumenty ZS jako składniki MPS.
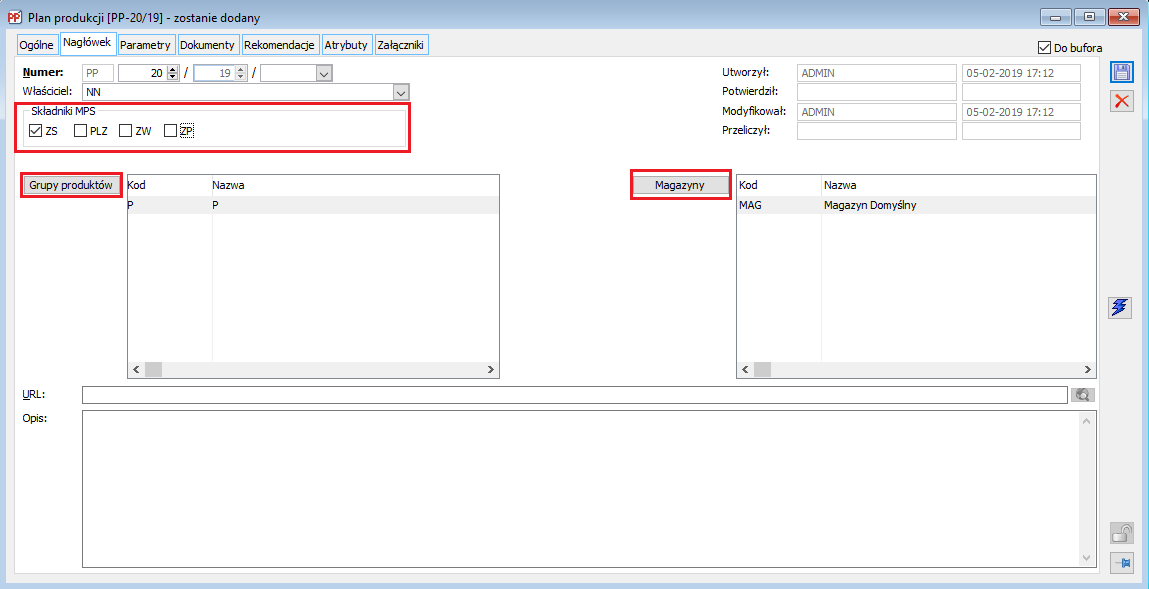
Na dokumencie wskazano także zakres dat, w jakich analizowane ma być zapotrzebowanie na produkty:
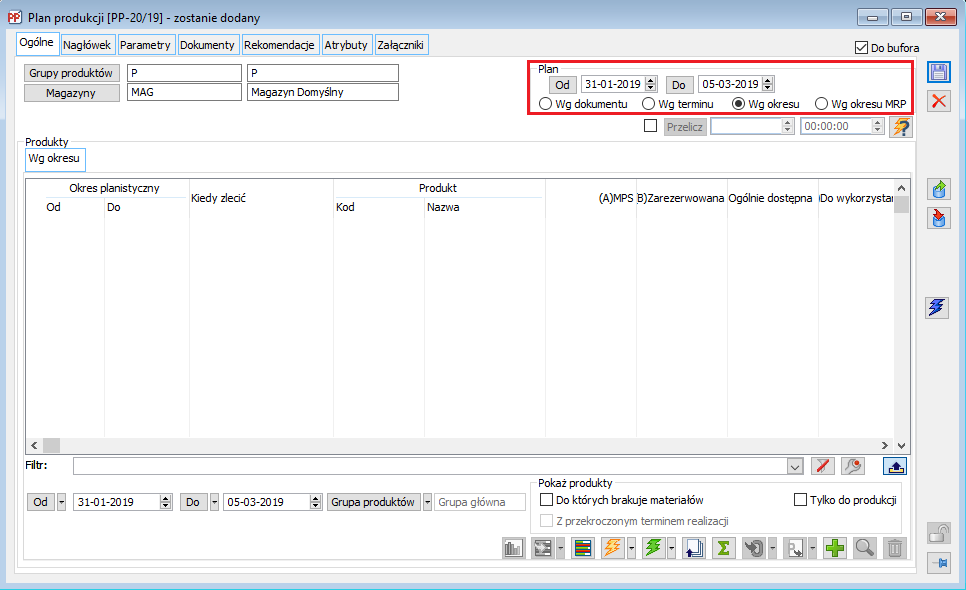
Następnie, za pomocą opcji: [Przeliczenie Planu produkcji] przeliczono Plan „Wg okresu”:
W wyniku przeliczenia, na Planie produkcji wyświetlone zostały odpowiednie elementy wynikające z zastosowanej parametryzacji i zarejestrowanych w systemie danych:
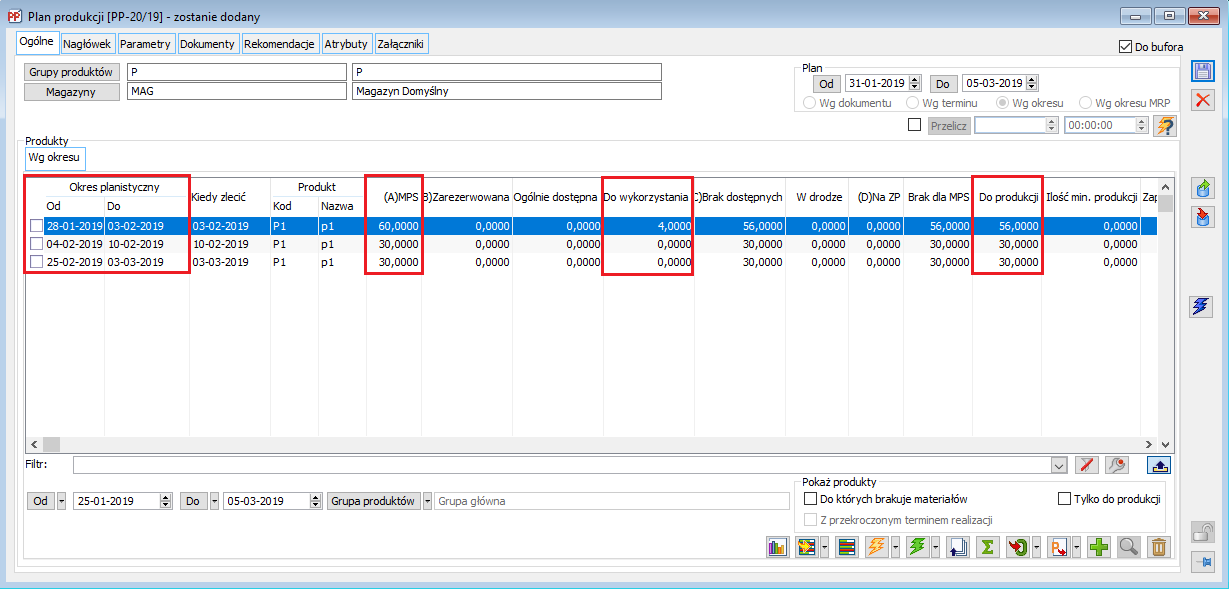
Potrzeby produkcyjne, wynikające z ww. zamówień sprzedaży, zostały pogrupowane w ramach kolejnych okresów planistycznych w zależności od dat realizacji elementów tych zamówień i przedstawione w kolumnie: MPS.
Informacja o ilości produktu, jaką należy wytworzyć w danym okresie planistycznym, została wyświetlona na Planie produkcji w kolumnie: Do produkcji i wynika ona z następujących danych:
W pierwszym okresie planistycznym, trwającym od 2019-01-28 do 2019-02-03, uwzględnione zostały potrzeby wynikające z zamówień sprzedaży, które należy zrealizować w tym okresie. Należy w tym okresie wytworzyć taką ilość produktu, by wystarczyła na realizację: ZS-1, ZS-2 i ZS-3. Łączna ilość produktu P1 wynikająca z tych zamówień, to 60 szt. (widoczne w kolumnie: MPS). Ponieważ dodatkowo na magazynie MAG, znajdują się 4 szt. produktu P1 (widoczne w kolumnie: Do wykorzystania), które również można wykorzystać na poczet realizacji ww. zamówień, to ostateczna ilość produktu P1, jaką należy wytworzyć w pierwszym okresie planistycznym, by uzupełnić zapotrzebowanie wynikające z zamówień, to 56 szt. Ilość ta prezentowana jest w kolumnie: Do produkcji, dla pierwszego okresu planistycznego.
W drugim okresie planistycznym, trwającym od 2019-02-04 do 2019-02-10, uwzględnione zostały potrzeby wynikające z zamówień ZS-4 i ZS-5. Ponieważ po realizacji zamówień z pierwszego okresu planistycznego, nie będzie już na magazynie dostępnej ilości produktu, to w kolumnie: Do produkcji w drugim okresie planistycznym prezentowana jest potrzeba wynikająca w całości z zamówień ZS-4 i ZS-5, czyli 30 szt. produktu P1.
W trzecim okresie planistycznym, trwającym od 2019-02-25 do 2019-03-03 uwzględniona została potrzeba wynikająca z zamówienia ZS-6. Ilość prezentowana w kolumnie: Do produkcji w tym okresie planistycznym to 30 szt.
Na obliczoną w kolumnie: Do produkcji ilość produktu można z poziomu Planu produkcji wygenerować dokumenty ZP, ZZ, ZW, za pomocą opcji dostępnych w rozwijanym menu obok opcji: [Generowanie dokumentu]:
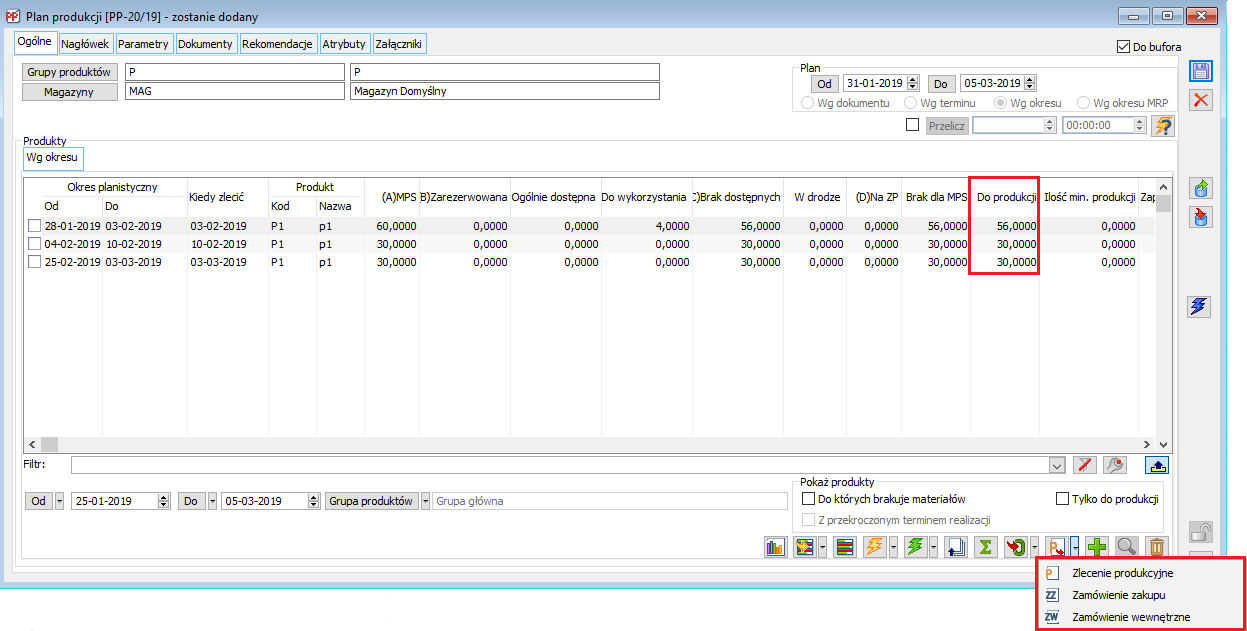
Jak na Planie produkcji uzyskać informację o potrzebach produkcyjnych na konkretny termin?
Jednym ze sposobów przeliczania Planu produkcji jest przeliczanie „Wg terminu”. Opcja ta pozwala na zebranie informacji o potrzebach produkcyjnych z podziałem na konkretne terminy.
Parametryzacja definicji dokumentu PP
Jeśli chcemy by dokument Planu produkcji był domyślnie przeliczany „Wg terminu”, należy zaznaczyć odpowiednią opcję na definicji dokumentu w danym centrum struktury firmy:
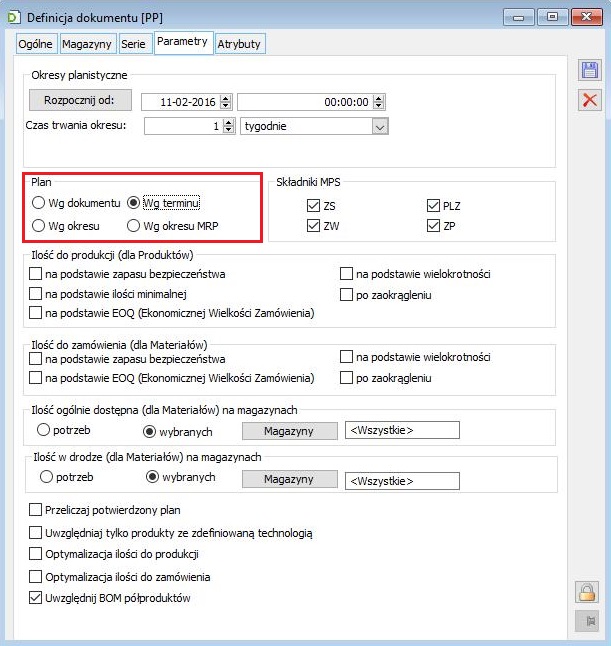
Ww. ustawienie można zmienić z poziomu dokumentu Planu produkcji przed jego przeliczeniem. (Po przeliczeniu Planu, opcja będzie nieaktywna).:
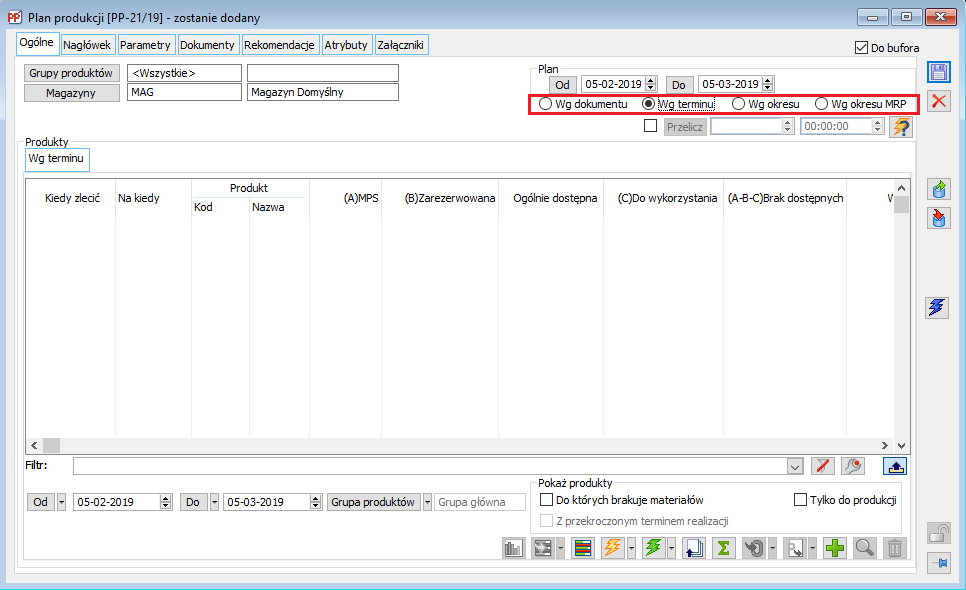
Przykład obliczania potrzeb produkcyjnych na termin, na Planie produkcji
W systemie zarejestrowano następujące potwierdzone dokumenty:
ZS-1 na 10 szt. produktu P1 z datą realizacji 13-02-2019
ZS-2 na 10 szt. produktu P1 z datą realizacji 14-02-2019
ZW-1 na 10 szt. produktu P1 z datą realizacji 13-02-2019
PLZ -1 na 100 szt. produktu P1 za okres: od 11-02-2019 do 14-02-2019
ZS-3 na 10 szt. produktu P2 z datą realizacji 13-02-2019
ZS-4 na 10 szt. produktu P2 z datą realizacji 14-02-2019
ZW-2 na 10 szt. produktu P2 z datą realizacji 13-02-2019
PLZ-2 na 100 szt. produktu P2 za okres: od 11-02-2019 do 14-02-2019
Dodano Plan produkcji, na którym ustawiono parametry odpowiadające za uwzględnienie ww. dokumentów jako składników MPS, wskazano odpowiednią grupę produktów zawierającą produkty P1 i P2. Ustawiono także odpowiedni zakres dat w jakim przeliczany ma być Plan oraz zaznaczono opcję: Wg terminu, jako sposób przeliczania Planu:
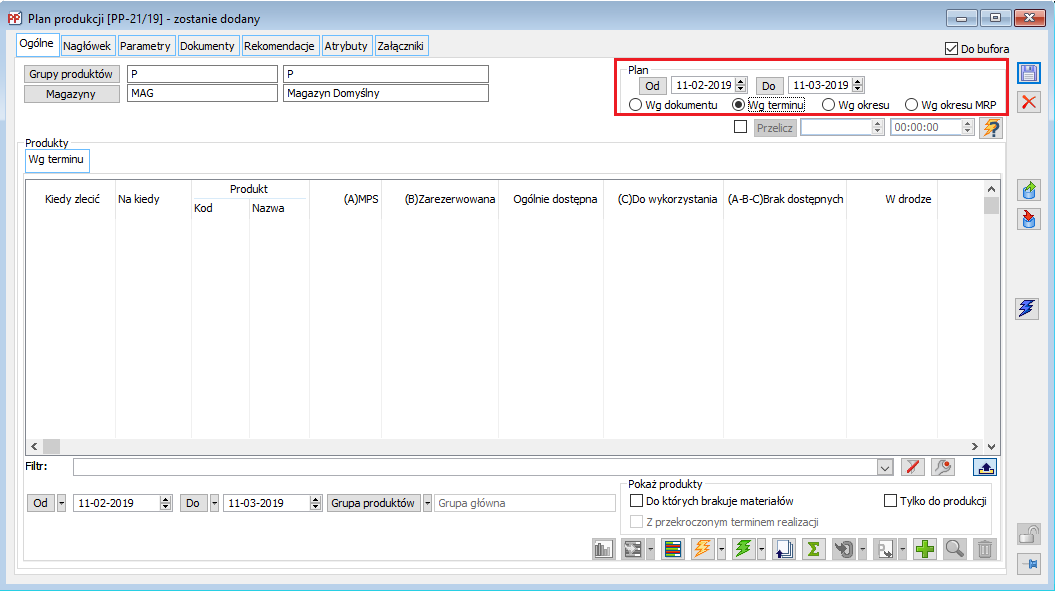
Przeliczenia planu produkcji zwróciło następujący wynik:
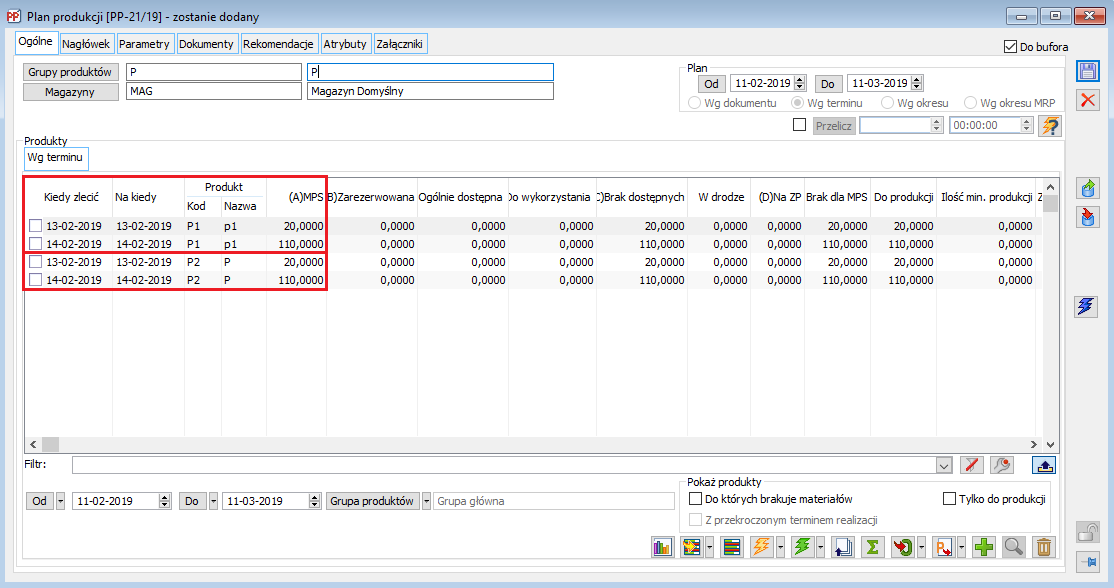
Potrzeby produkcyjne dla produktów P1 i P2, wynikające z ww. dokumentów, zostały odpowiednio pogrupowane wg konkretnych terminów i zawarte w kolumnie: MPS.
Na termin 13-02-2019 łączna potrzeba produkcyjna dla P1 wynosi 20 szt. Wynika ona z dokumentów ZS-1 i ZW‑1, których daty realizacji są zgodne z ww. terminem.
Na termin 14-02-2019 łączna potrzeba produkcyjna dla P1 wynosi 110 szt. Wynika ona z dokumentów ZS-2, którego data realizacji jest zgodna z ww. terminem oraz PLZ-1, którego koniec okresu przypada na ww. termin.
Przeliczenia Planu produkcji zwróciło również analogiczny wynik dla produktu P2.
Dokumenty uzupełniające braki produkcyjne będą generowane z poziomu Planu produkcji na podstawie ilości zawartej w kolumnie: Do produkcji.
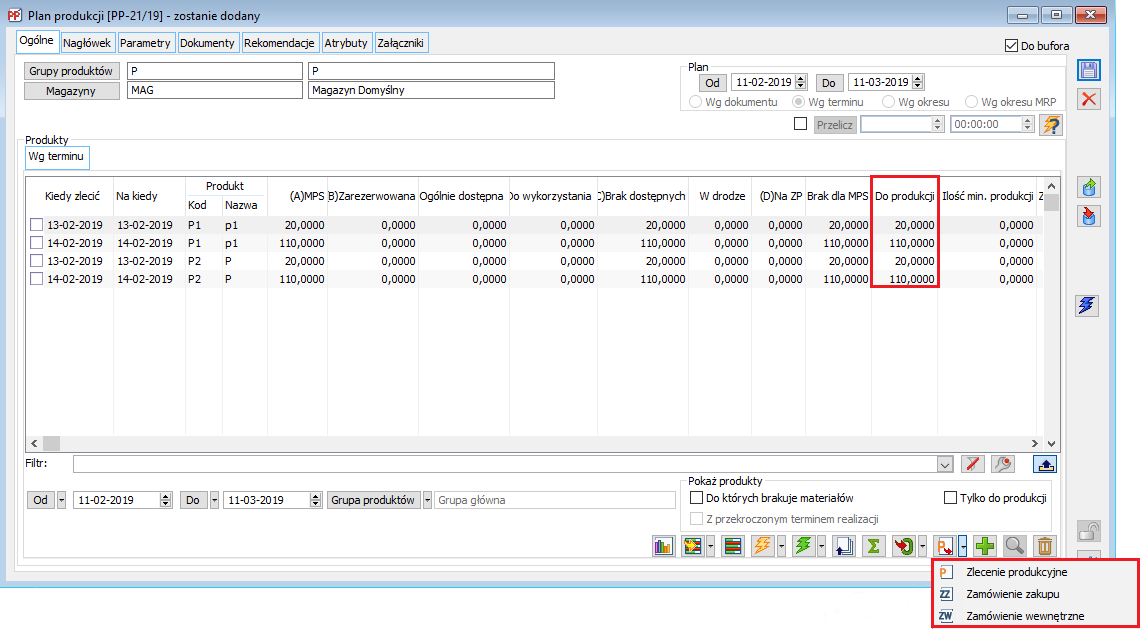
Jak na Planie produkcji uzyskać informację o potrzebach produkcyjnych z wyszczególnieniem dokumentów, które generują te potrzeby?
Najbardziej szczegółowym ze sposobów raportowania potrzeb produkcyjnych na Planie produkcji jest raportowanie ich z wyszczególnieniem dokumentów, które są źródłem MPS. Aby uzyskać ww. raport, należy przeliczyć Plan produkcji „Wg dokumentu”.
Parametryzacja definicji dokumentu PP
Tak, jak w przypadku innych sposobów przeliczania Planu produkcji, przeliczanie go „Wg dokumentu” można domyślnie ustawić na definicji PP:
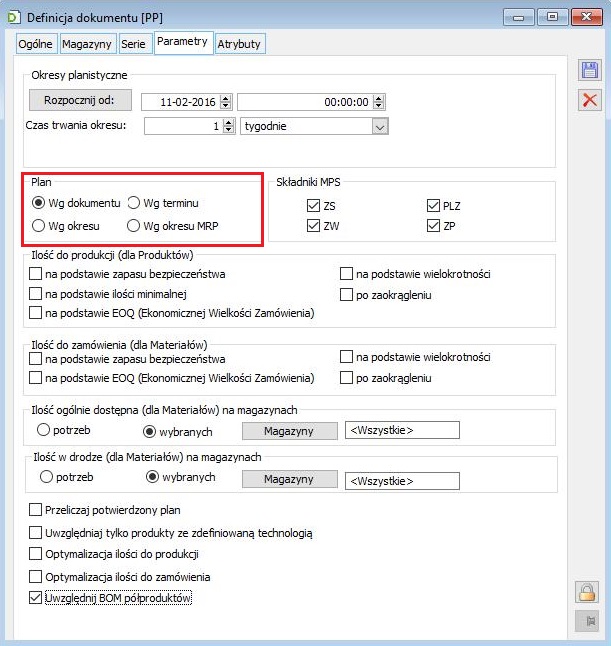
Opcja „Wg dokumentu” jest przenoszona z definicji na dokument PP wystawiany w danym centrum struktury firmy i możliwa do zmiany na dokumencie przed wykonaniem przeliczenia Planu.
Przykład przeliczania Planu produkcji „Wg dokumentu”
W systemie zarejestrowano następujące potwierdzone dokumenty:
ZS-1 na 10 szt. produktu P1 z datą realizacji 13-02-2019
ZS-2 na 10 szt. produktu P2 z datą realizacji 13-02-2019
ZW-1 na 10 szt. produktu P1 z datą realizacji 13-02-2019
ZW-2 na 10 szt. produktu P2 z datą realizacji 13-02-2019
PLZ -1 na 100 szt. produktu P1 za okres: od 11-02-2019 do 14-02-2019
PLZ-2 na 100 szt. produktu P2 za okres: od 11-02-2019 do 14-02-2019
Zaplanowano także zlecenia:
ZP-1 na 100 szt. P1 z datą realizacji (rezerwacji zakupowej) na 15-02-2019
ZP-2 na 20 szt. P1 z datą realizacji (rezerwacji zakupowej) na 15-02-2019
Dodano Plan produkcji, na którym ustawiono parametry odpowiadające za uwzględnienie ww. dokumentów jako składników MPS, wskazano odpowiednią grupę produktów, zawierającą produkty P1 i P2. Ustawiono także odpowiedni zakres dat w jakim przeliczany ma być Plan oraz zaznaczono opcję: Wg dokumentu, jako sposób przeliczania Planu.
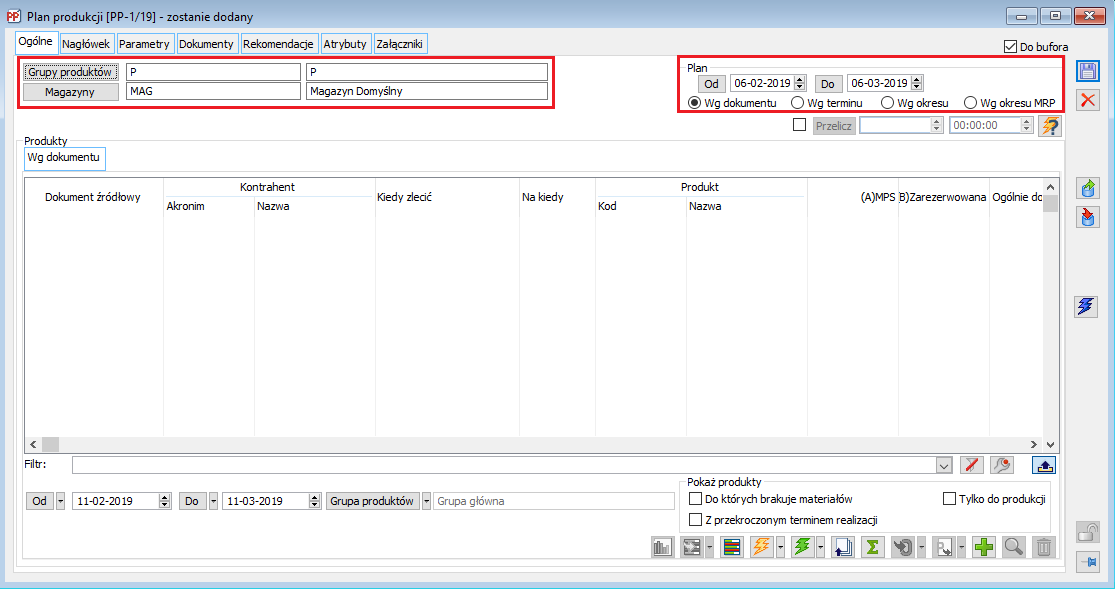
W wyniku przeliczenia, na Planie produkcji przedstawione zostały informacje o potrzebach produkcyjnych, wynikających z każdego (elementu) dokumentu, stanowiącego składnik MPS.
W kolumnie: Dokument źródłowy, prezentowane są dokumenty, które generują poszczególne potrzeby MPS, w kolumnie: Do produkcji – ilości, na jakie należy wygenerować zlecenia lub zamówienia, których realizacja uzupełni braki poszczególnych produktów na magazynach i pozwoli na pokrycie potrzeby MPS. W kolumnie: Zaplanowana prezentowana jest ilość poszczególnych produktów zaplanowana już na zleceniach produkcyjnych:
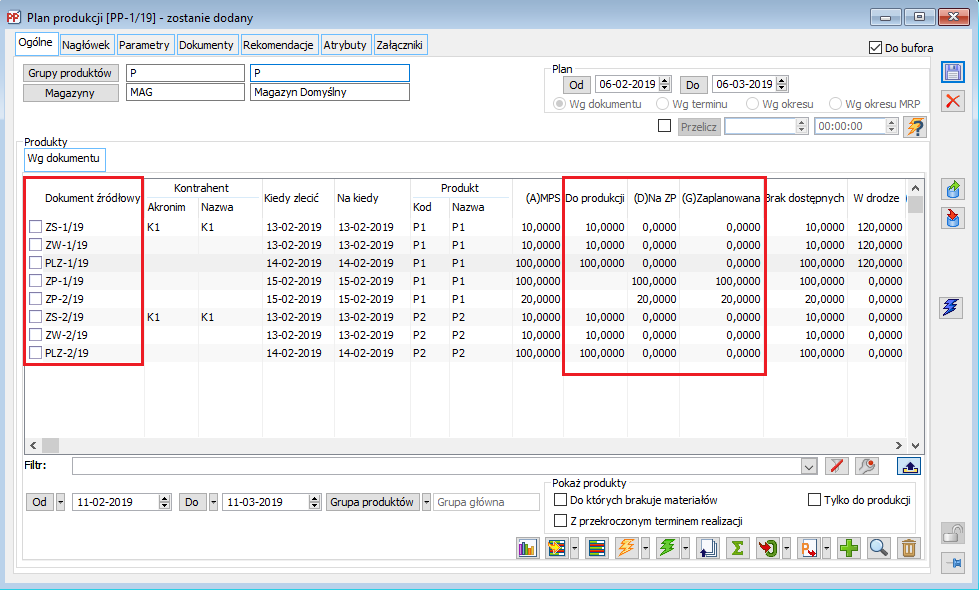
Dokumenty uzupełniające braki produkcyjne będą generowane z poziomu Planu produkcji na podstawie ilości zawartej w kolumnie: Do produkcji:
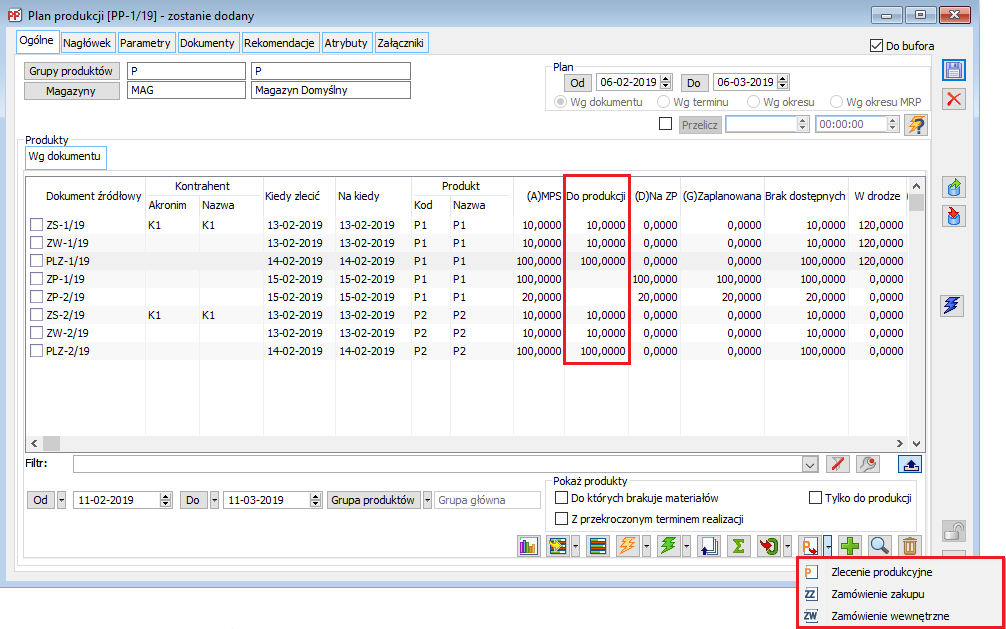
Jak uzyskać informacje o materiałach potrzebnych do wytworzenia produktów raportowanych na Planie produkcji?
Zapotrzebowanie na materiały dla produktów raportowanych na Planie produkcji prezentowane jest w odrębnej sekcji na dokumencie PP. Sekcja ta jest rozwijalna, zatem może być prezentowana na życzenie Użytkownika:
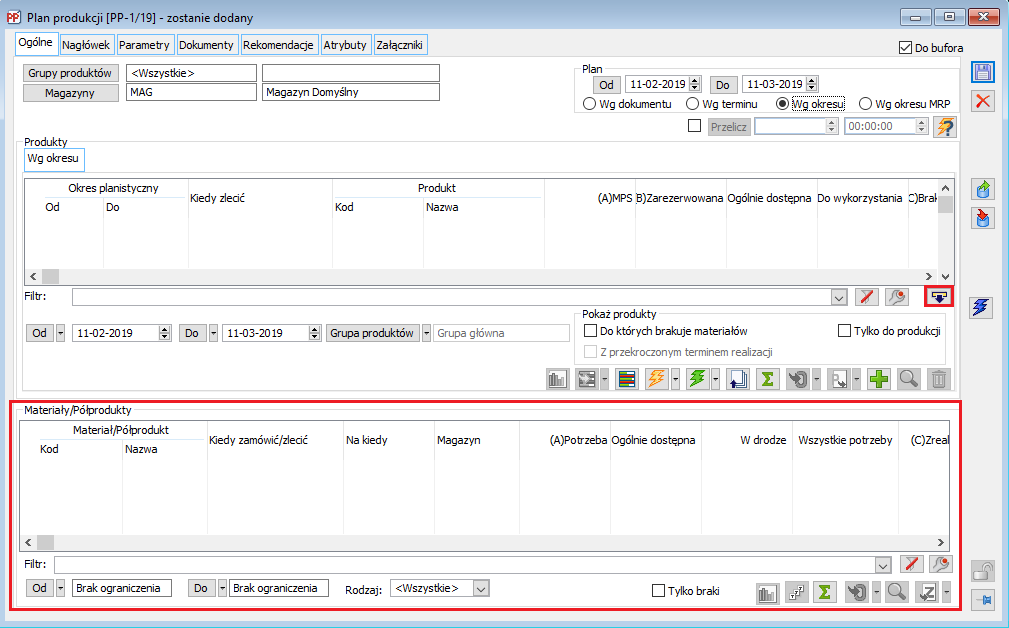
Elementy zapotrzebowania materiałowego prezentowane są dla zaznaczonych w sekcji: Produkty pozycji. W zależności od rodzaju składnika MPS (ZS, ZW, PLZ, ZP), ilość w oparciu o którą liczone jest zapotrzebowanie materiałowe, może wynikać kolumn: Do produkcji, Na ZP, Brak dostępnych. Zapotrzebowanie materiałowe obliczane jest wg technologii domyślnej lub tej, którą wskazano na zleceniu produkcyjnym.
Przykład raportowania zapotrzebowania materiałowego na Planie produkcji, dla składników MPS: ZS i ZP
W systemie zdefiniowano dwie technologie produkcji dla produktu P1:
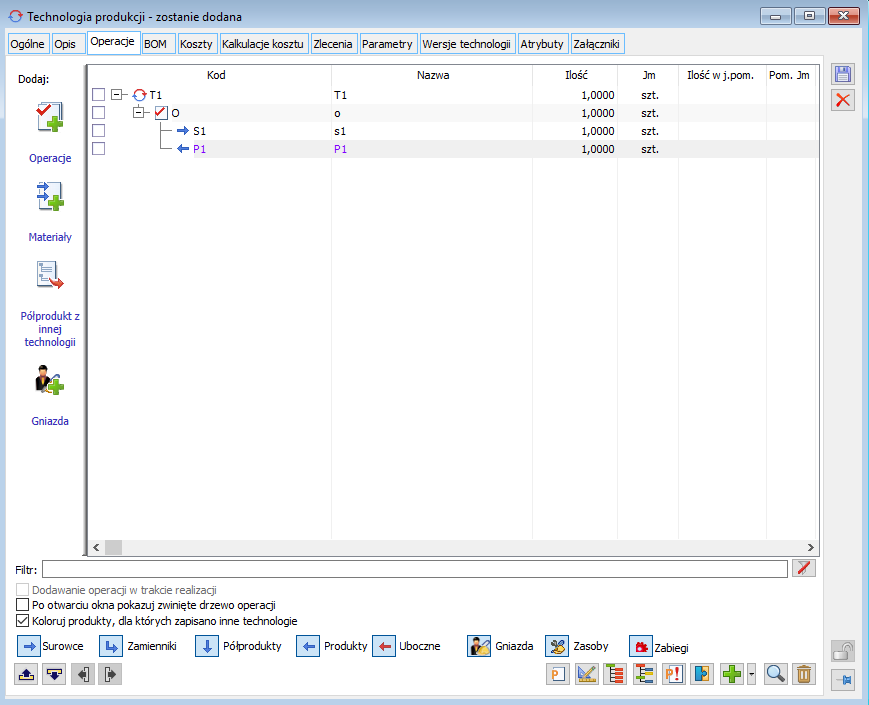
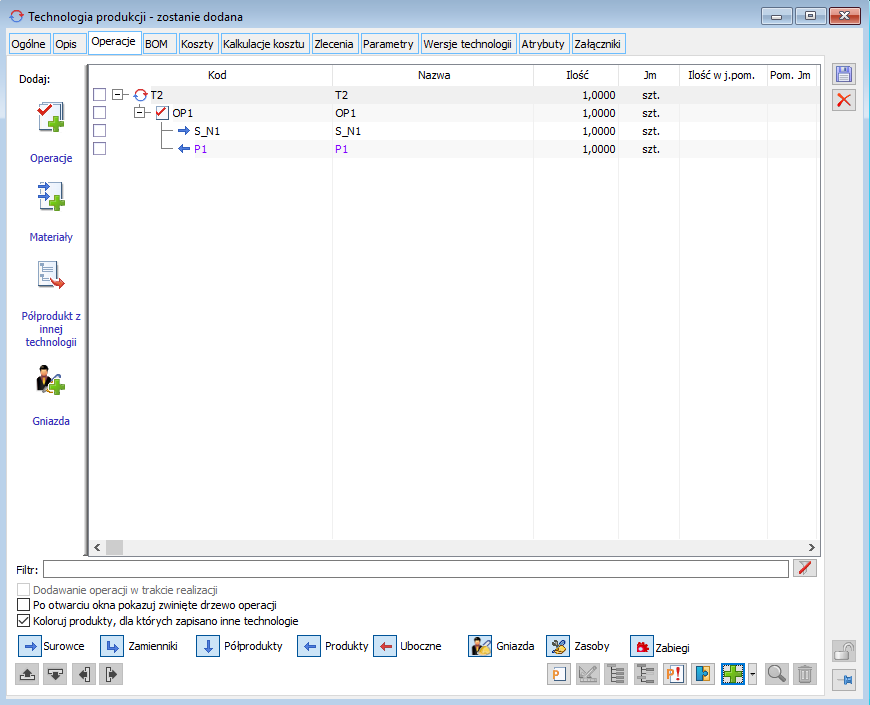
Technologia T1 jest technologią domyślną dla produktu P1.
W systemie zarejestrowano również następujące potwierdzone zamówienia sprzedaży:
ZS-1 na 10 szt. produktu P1 z datą realizacji 20-02-2019
ZS-2 na 30 szt. produktu P1 z datą realizacji 25-02-2019
Dodatkowo zaplanowano w oparciu o technologię T2 zlecenie ZP-1 na 30 szt. produktu z datą realizacji 12‑02‑2019.
Na magazynie nie ma produktu P1, ani też materiałów potrzebnych do wytworzenia produktu P1.
Dodano nowy Plan produkcji i przeliczono go „Wg dokumentów”, wskazując odpowiedni zakres dat, oraz odpowiednie parametry, by uwzględnić zapotrzebowanie produkcyjne wynikające z ww. dokumentów:
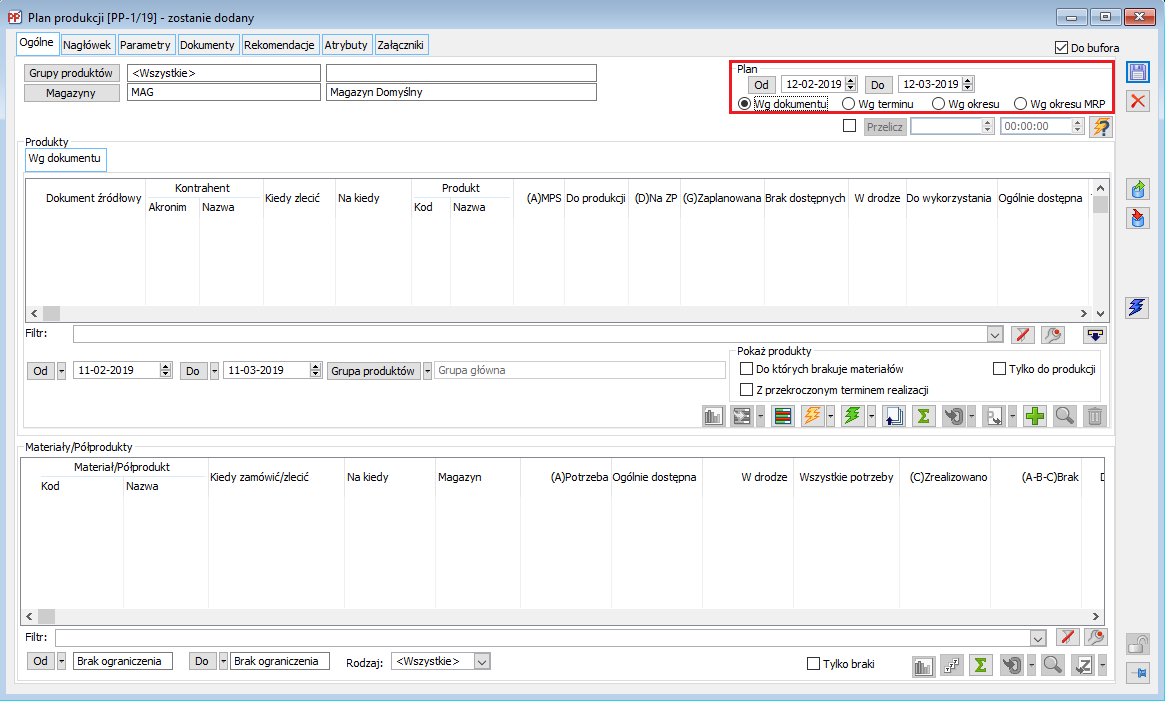
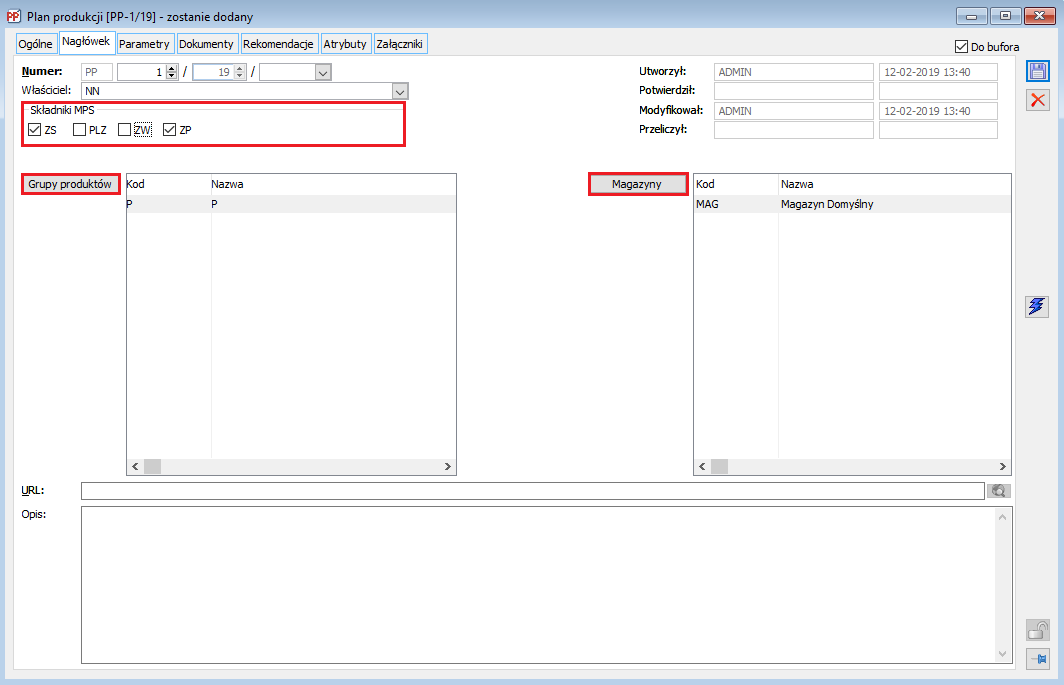
Zapotrzebowanie materiałowe, w zależności od typu dokumentu źródłowego, jest obliczane w tym przypadku dla ilości produktu prezentowanej w kolumnie: Do produkcji (w przypadku ZS) lub Brak dostępnych (w przypadku ZP).
Potrzeba materiałowa obliczona została następująco:
Dla zamówień sprzedaży potrzeba materiałowa liczona jest w oparciu o technologie domyślną T1 dla produktu P1, natomiast dla zaplanowanego zlecenia produkcyjnego, potrzeba materiałowa liczona jest w oparciu o technologię T2, użytą na tym zleceniu.
Do wytworzenia 10 szt. produktu P1, zamówionego dokumentem ZS-1, potrzeba 10 szt. materiału S1.
Do wytworzenia 30 szt. produktu P1, zamówionego dokumentem ZS-2, potrzeba 30 szt. materiału S1.
Do wytworzenia 30 szt. produktu P1, zaplanowanego w ramach ZP-1, potrzeba 30 szt. materiału S_N1.
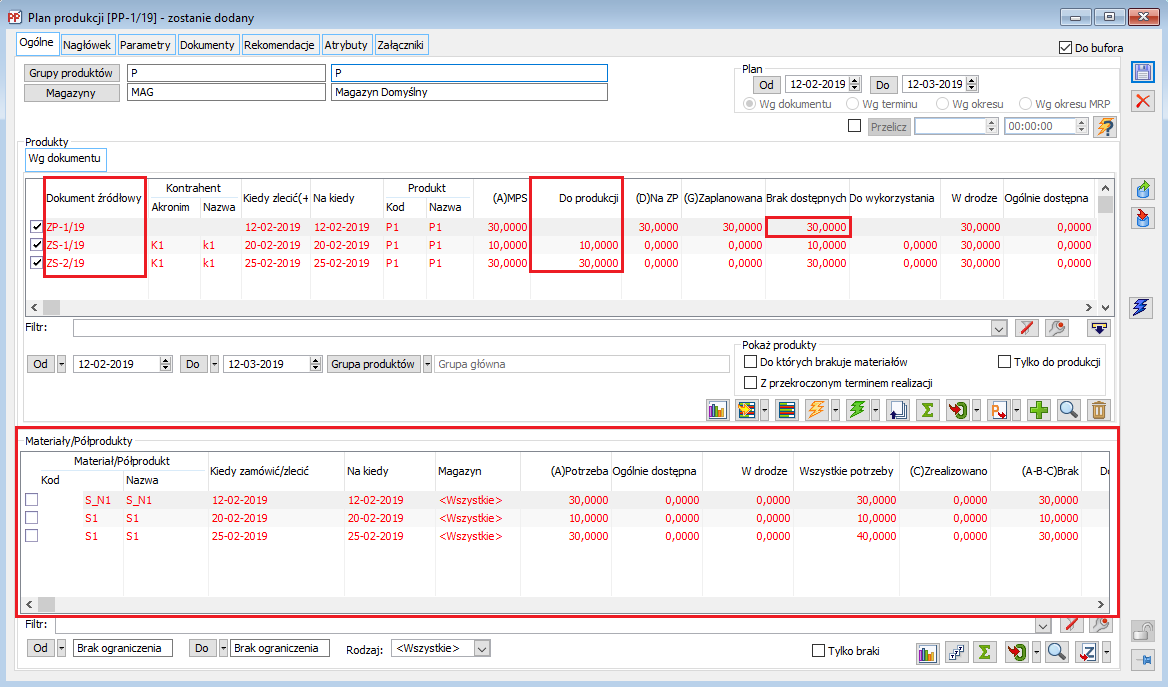
Dalej, z poziomu sekcji Materiały można generować dokumenty uzupełniające braki materiałowe. Dokumenty te generowane będą na ilość wyświetloną w kolumnie: Brak:
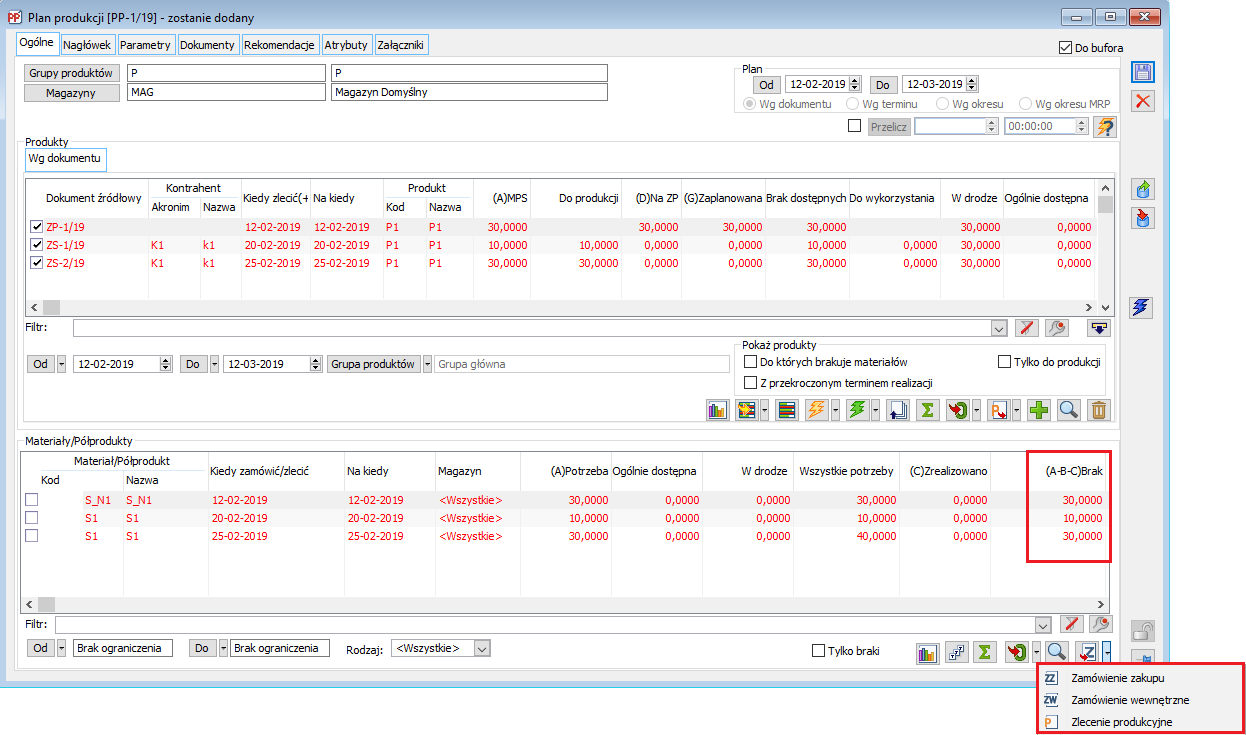
Przykład obliczania zapotrzebowania materiałowego na Planie produkcji, dla elementu wynikającego z ZS oraz z wygenerowanego z niego ZP.
W systemie zdefiniowano 2 technologie, jak w punkcie 4.1 oraz zarejestrowano potwierdzony dokument ZS-1 na 10 szt. produktu P1 z datą realizacji 20-02-2019.
Z ww. zamówienia wygenerowano ZP na 2 szt. produktu P1 i na pozycji zlecenia ustawiono technologię T2.
Na magazynie nie ma P1, ani też materiałów potrzebnych do wytworzenia produktu P1.
Przeliczono Plan produkcji „Wg dokumentów”, wskazując odpowiedni zakres dat, by uwzględnić ww. składniki MPS.
Obliczone na Planie produkcji zapotrzebowanie materiałowe obejmuje: materiał S1 w ilości 8 szt. oraz materiał S_N1 w ilości 2 szt. Zapotrzebowanie materiałowe dotyczy pozycji Planu wynikającej z dokumentu ZS-1, jednak, ponieważ z tego zamówienia wygenerowano dodatkowo zlecenie produkcyjne oraz wskazano na nim inną, niż domyślna, technologię, to Plan produkcji uwzględnił zarówno materiał wynikający z technologii T1, jak i z technologii T2.
8 szt. materiału S1 jest potrzebne do wytworzenia 8 szt. produktu P1 (ilość określona w kolumnie: Do produkcji, dla elementu wynikającego z ZS-1) w oparciu o technologię domyślną T1.
2 szt. materiału S_N1 jest potrzebne do wytworzenia 2 szt. produktu (ilość określona w kolumnie: Na ZP, wynikająca z ilości produktu P1, znajdującej się zleceniu produkcyjnym, wygenerowanym z ZS-1) w oparciu o technologię T2, którą wskazano na zleceniu produkcyjnym:
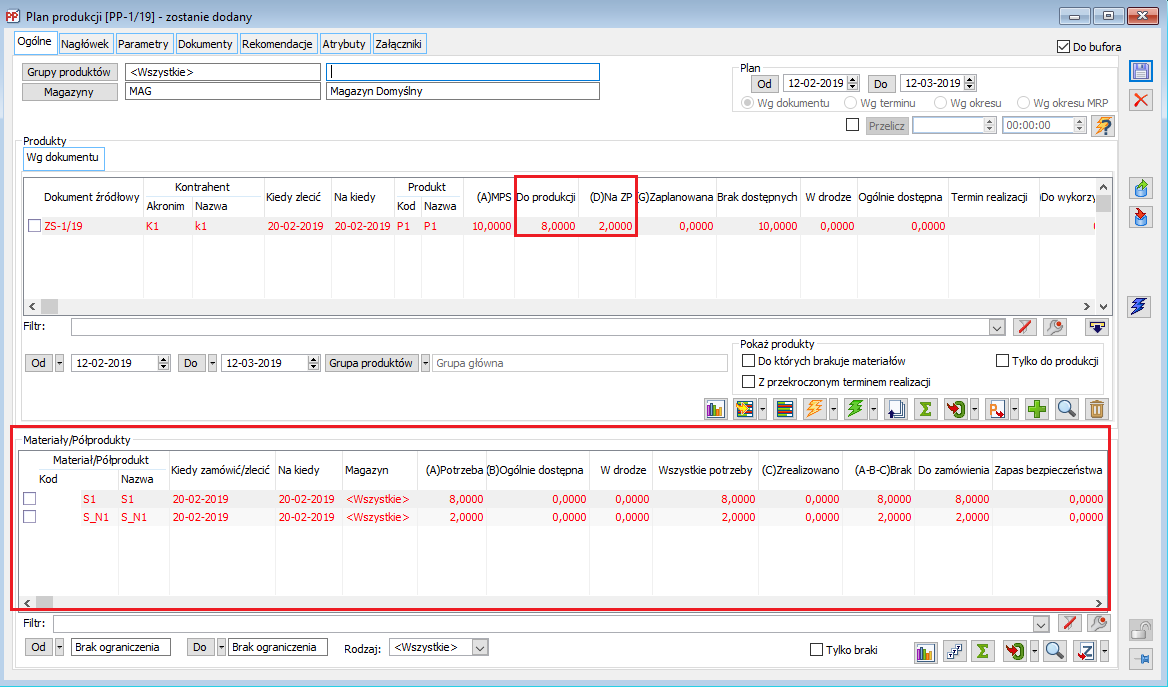
Jak na Planie produkcji uzyskać informację o ilości produktu koniecznej do wytworzenia uwzględniając ilości minimalną produktu?
Istnieje możliwość sparametryzowania Planu produkcji w ten sposób, by podczas obliczania ilości produktu, jaką należy wytworzyć w danym terminie, brana była pod uwagę również minimalna ilość tego produktu, określona w technologii.
Parametryzacja definicji dokumentu PP
Jeśli chcemy by domyślnie na dokumencie PP, ilość do produkcji była obliczana na podstawie minimalnej ilości produktu, określonej w technologii, to na definicji dokumentu PP, w odpowiednim centrum struktury firmy, należy zaznaczyć parametr: Ilość do produkcji na podstawie ilości minimalnej:
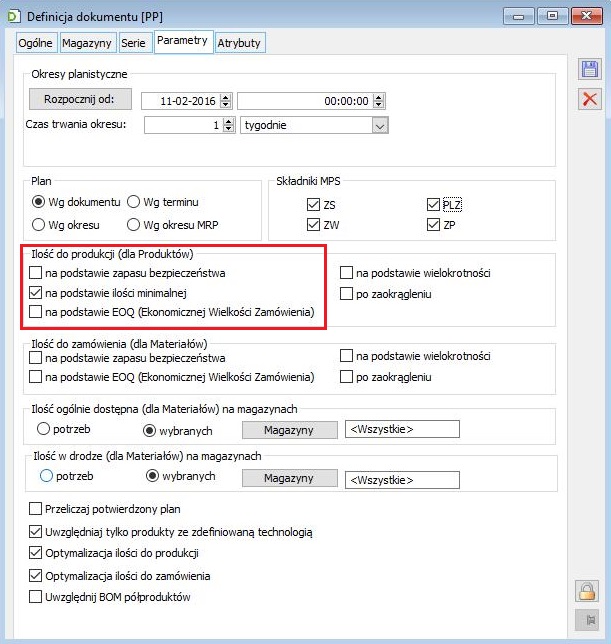
Ustawienie ww. parametru jest dodatkowo możliwe do zmiany z poziomu dokumentu PP:
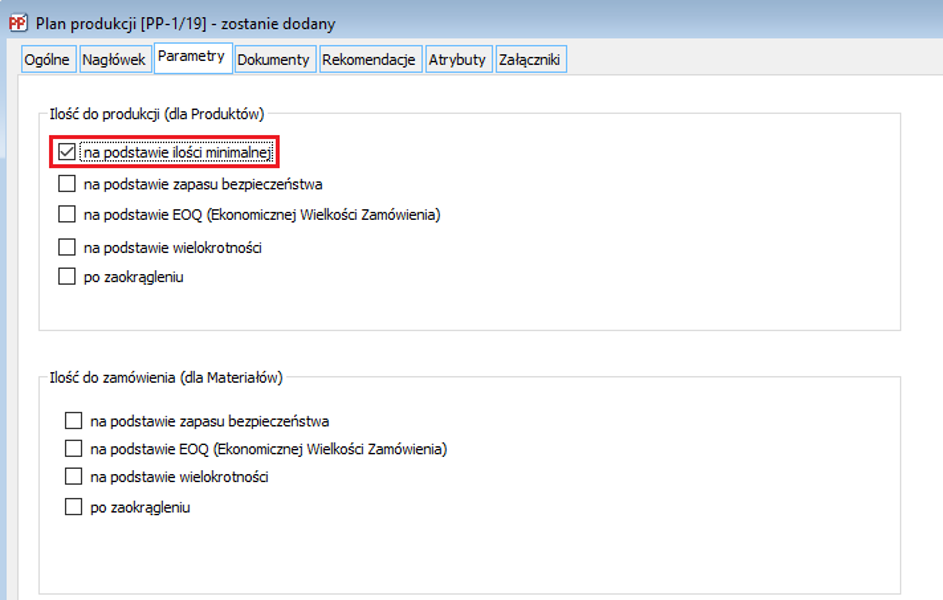
Przykład obliczania ilości do produkcji, na podstawie ilości minimalnej
W systemie zdefiniowano technologię produkcji dla produktu P1:
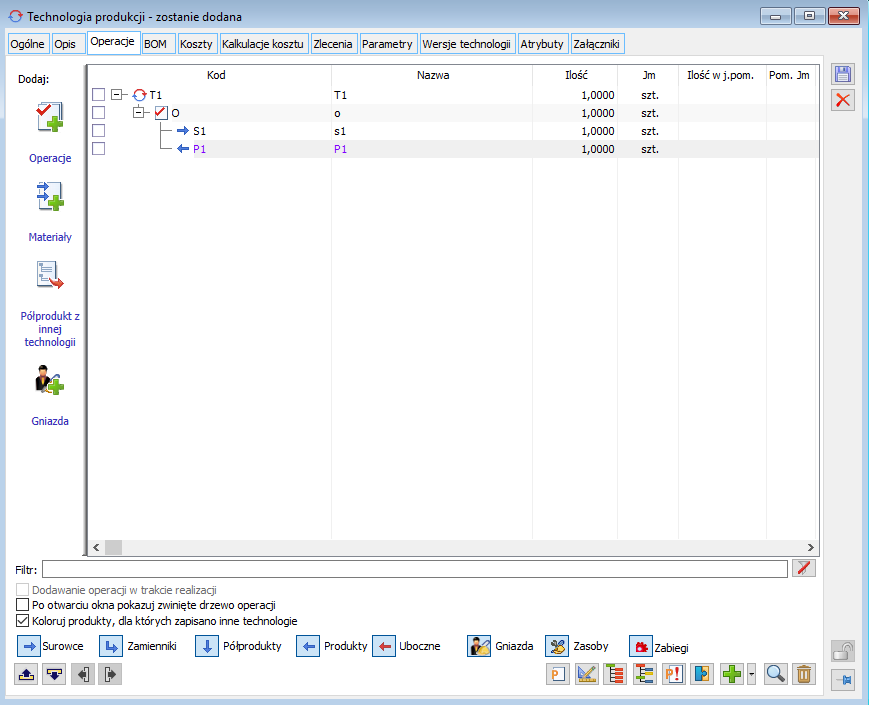
Dla produktu P1 w ramach ww. technologii określono ilość minimalną na poziomie 20 szt.:
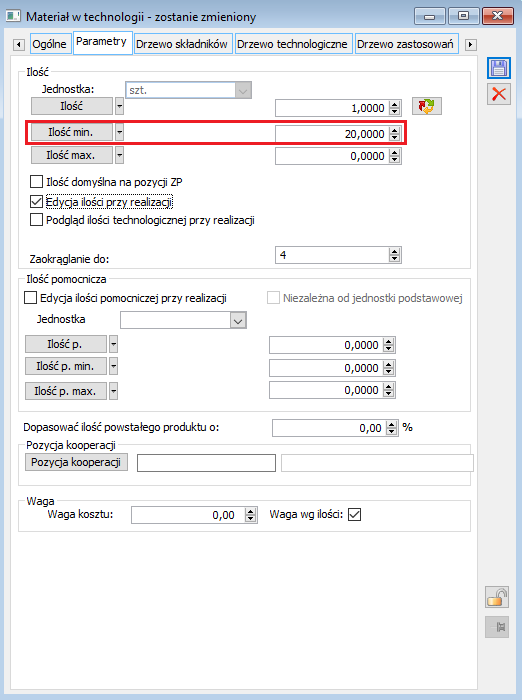
W systemie zarejestrowano dodatkowo 2 potwierdzone dokumenty ZS:
ZS-1 na 5 szt. P1 z datą realizacji 20-02-2019
ZS-2 na 30 szt. P1 z datą realizacji 25-02-2019
Na magazynie nie ma produktu P1.
Wystawiamy dokument PP z zaznaczonym parametrem: Ilość do produkcji na podstawie ilości minimalnej. Na dokumencie PP ustawiamy odpowiedni zakres dat, by uwzględnić ww. dokumenty ZS. Następnie przeliczamy PP Wg dokumentu.
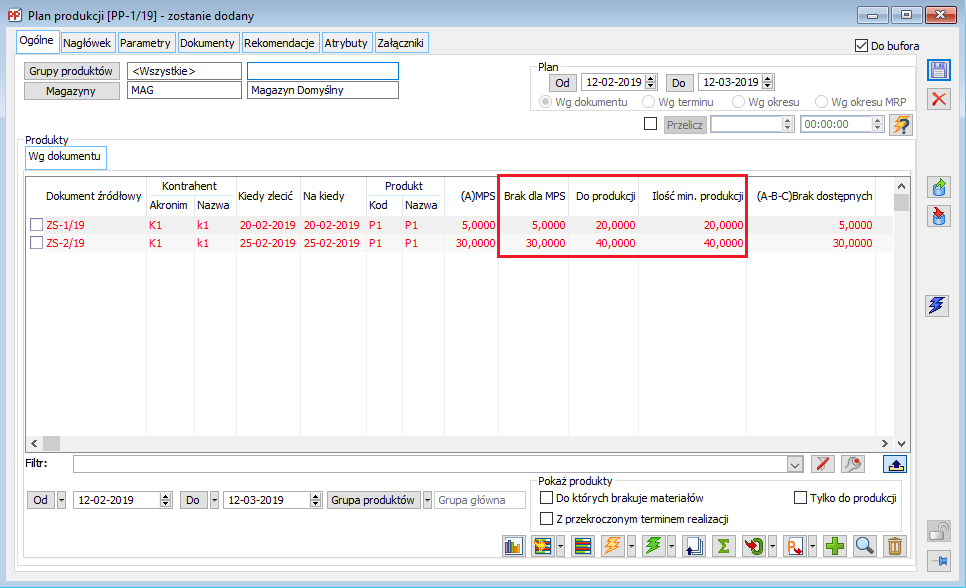
Ilość do produkcji dla pierwszej pozycji Planu produkcji została obliczona na poziomie 20 (widoczna w kolumnie: Do produkcji). Brak produktu, jaki należy uzupełnić, by pokryć potrzebę produkcyjną wynikająca z dokumentu ZS‑1 to 5 szt. produktu (ilość widoczna w kolumnie: Brak dla MPS), jednak w technologii domyślnej dla tego produktu określono ilość minimalną na poziomie 20 szt. (widoczna w kolumnie: Ilość min. produkcji) Do tej ilości została „unormowana” proponowana do produkcji ilość dla pierwszego elementu Planu produkcji.
Podobnie, jak dla pierwszego elementu Planu, ilość do produkcji dla drugiej pozycji została obliczona na poziomie 40.
Kiedy za pomocą Planu produkcji można zoptymalizować proponowaną do produkcji ilość produktu?
Podczas obliczania na Planie produkcji ilości produktu, jaką należy wytworzyć, by pokryć potrzebę produkcyjną system uwzględnia także „nadmiarowe” ilości, zadeklarowane w kolumnie: Do produkcji dla poprzednich pozycji Planu produkcji. Powstające „nadwyżki” w kolumnie: Do produkcji mogą wynikać z obliczenia ilości: Do produkcji na podstawie ilości minimalnej produktu, jak również z ręcznego określania w kolumnie: Do produkcji ilości większej niż wynika z danej potrzeby.
Jeśli we wcześniejszym terminie dla jakiegoś produktu Plan produkcji proponuje ilość do produkcji większą niż wynika z potrzeby MPS lub też Użytkownik zwiększa ręcznie proponowaną ilość do produkcji, wówczas powstały „nadmiar” może zostać uwzględniony w kolejnych terminach dla tego samego produktu.
Przykład optymalizacji ilości w kolumnie: Do produkcji na Planie produkcji
W systemie zdefiniowano technologię produkcji dla produktu P1:
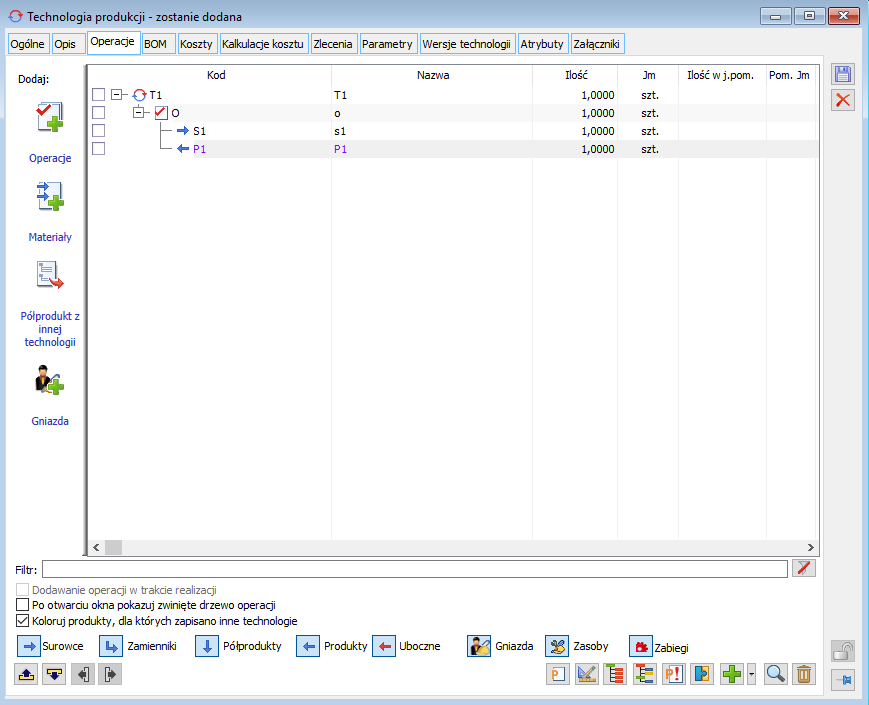
Dla produktu P1 w ramach ww. technologii określono ilość minimalną na poziomie 10 szt.:
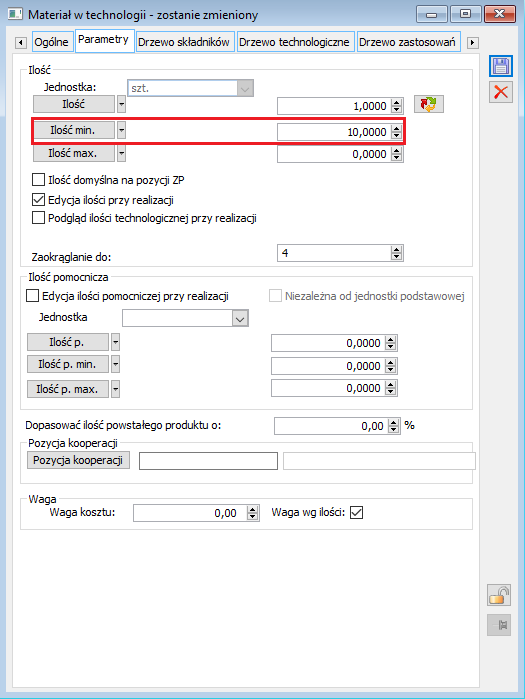
Zarejestrowano również następujące potwierdzone dokumenty ZS:
ZS-1 na 1 szt. P1 z datą realizacji 20-02-2019
ZS-2 na 2 szt. P1 z datą realizacji 21-02-2019
ZS-3 na 3 szt. P1 z datą realizacji 22-02-2019
ZS-4 na 4 szt. P1 z datą realizacji 23-02-2019
ZS-5 na 5 szt. P1 z datą realizacji 24-02-2019
Na magazynie nie ma produktu P1.
Wystawiamy dokument PP, na którym ustawiamy odpowiedni zakres dat, by uwzględnić ww. dokumenty ZS. Na PP zaznaczamy parametr: Ilość do produkcji na podstawie ilości minimalnej. Następnie przeliczamy PP Wg dokumentu.
Kolumna „Do produkcji” wypełniana jest następująco dla kolejnych elementów Planu produkcji:
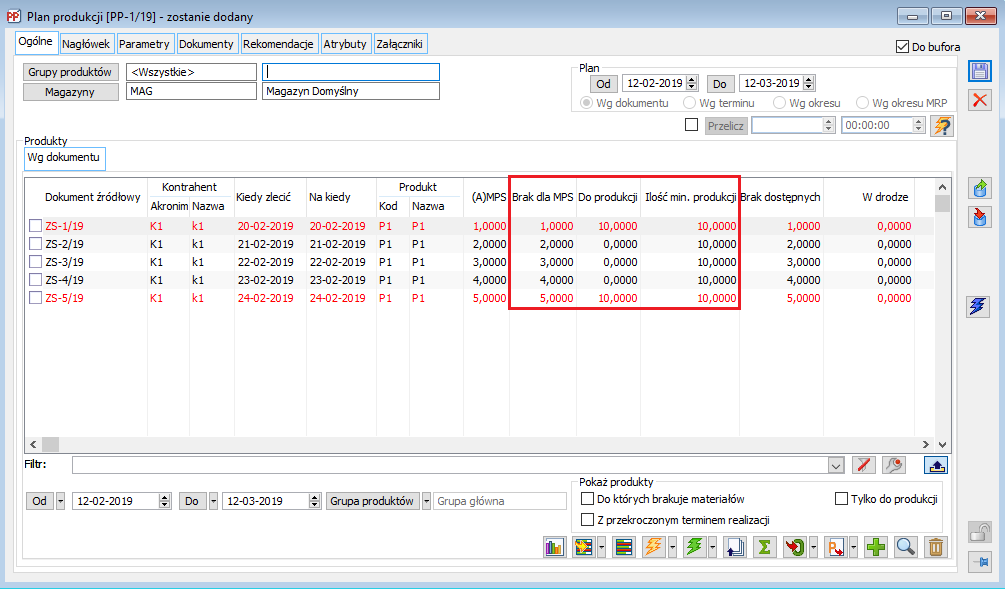
Dla elementu wynikającego z ZS‑1, ilość: Do produkcji została obliczona na poziomie 10 dlatego, że potrzeba produkcyjna wynosi 1 szt., ale ilość minimalna określona w technologii to 10. Ponieważ na PP zaznaczony był parametr: Ilość do produkcji na podstawie ilości minimalnej, to ilość do produkcji została unormowana do ilości minimalnej.
Dla elementu wynikającego z ZS‑2, ilość: Do produkcji została obliczona na poziomie 0, dlatego, że w poprzednim terminie, dla potrzeby wynikającej z ZS‑1 zaproponowana ilość do produkcji to 10. Ilość ta wystarczy by pokryć potrzebę wynikającą łącznie z ZS‑1 oraz ZS‑2, dlatego dla elementu Planu wynikającego z ZS-2 nie jest już konieczne dodatkowe uzupełnianie zapotrzebowania.
Dla elementu wynikającego z ZS‑3 oraz ZS‑4 również ilość: Do produkcji obliczono na poziomie 0, gdyż potrzebę produkcyjną także pokryje ilość obliczona: Do produkcji dla ZS‑1.
Dla elementu wynikającego z ZS‑5, ilość: Do produkcji obliczono na poziomie 10, dlatego, że nie ma już „nadwyżek produkcyjnych” wynikających ze wcześniejszych terminów, jakie można byłoby wykorzystać na poczet realizacji ZS‑5. Potrzeba jaką należy uzupełnić, by zrealizować ZS-5 to 5 szt. produktu P1, jednak ilość minimalna dla tego produktu, to 10 szt., zatem ilość do produkcji obliczona na podstawie ilości minimalnej=10.
Czy dla pozycji Planu produkcji można ręcznie zmienić ilość do produkcji?
Dostępna na Planie produkcji kolumna: Do produkcji, w której prezentowane jest ostateczne zapotrzebowanie na produkt, podlega ręcznej edycji. Oznacza to, że Użytkownik może ręcznie skorygować wynik, jaki zwraca w tej kolumnie przeliczenie Planu. W przeciwieństwie do ilości automatycznie obliczonej i zwróconej w kolumnie: Do produkcji, ilość zmieniona ręcznie przez Użytkownika nie będzie automatycznie aktualizowana podczas kolejnego przeliczania Planu produkcji. Oznacza to, że jeśli w systemie zmienią się jakieś warunki, które mogłyby wpływać na zapotrzebowanie, na produkt, np. na magazyn przyjęta zostanie pewna ilość analizowanego produktu lub wprowadzone zostaną dodatkowe dokumenty, które zmieniają potrzebę produkcyjną itd., to ilość wprowadzona ręcznie w kolumnie: Do produkcji pozostanie bez zmian, podczas kolejnego przeliczania dokumentu.
Przykład
W systemie zarejestrowano następujące dokumenty:
Potwierdzony dokument ZS-1 na 100 szt. P1 z datą realizacji 20-02-2019 na magazyn MAG
Potwierdzony dokument ZW-1 na 20 szt. P1 z datą realizacji 21-02-2019 z magazynu MAG na M1
Na magazynie MAG nie ma produktu P1.
Wystawiono i przeliczono „Wg dokumentu” Plan produkcji uwzględniając ww. dokumenty. W kolumnie: Do produkcji przeliczenie Planu zwróciło ilości: 100 i 20 wynikające z zapotrzebowania zarejestrowanego ww. dokumentami:
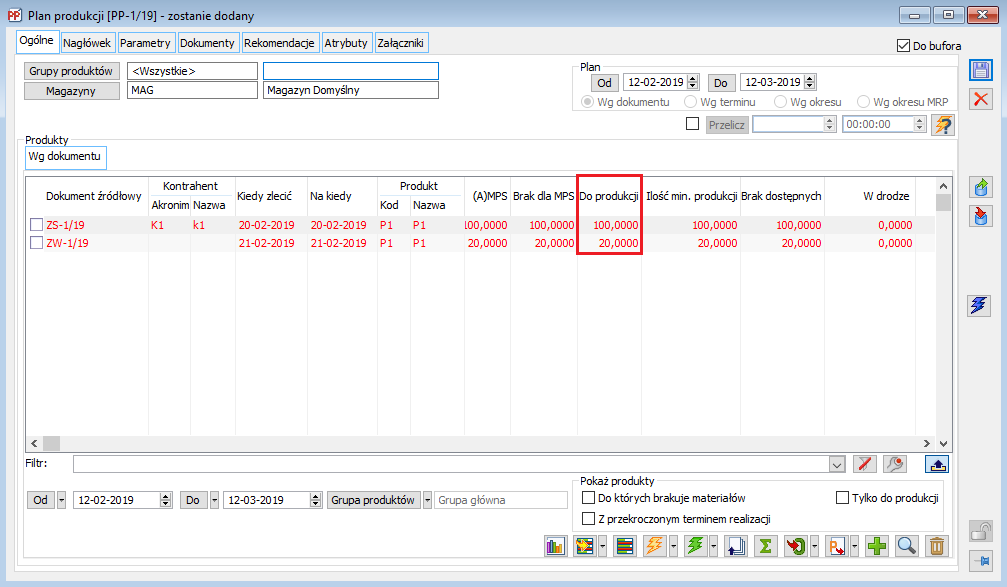
Następnie dla pozycji Planu produkcji, wynikającej z dokumentu ZS‑1 zmieniono ręcznie ilość w kolumnie: Do produkcji ze 100 na 80:
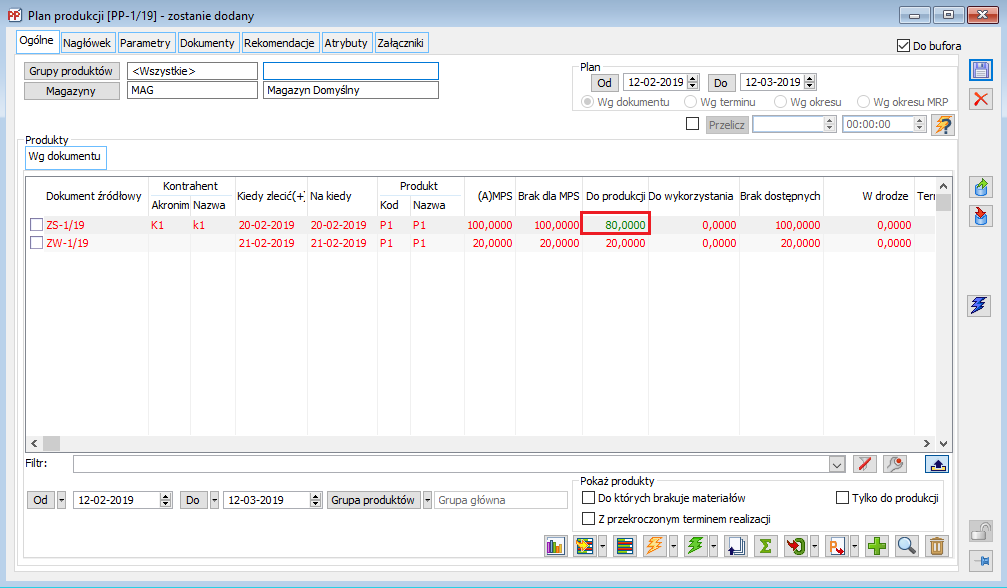
Kolejno, na magazyn MAG przyjęto dokumentem PW 15 szt. produktu P1 i przeliczono ponownie ww. Plan produkcji.
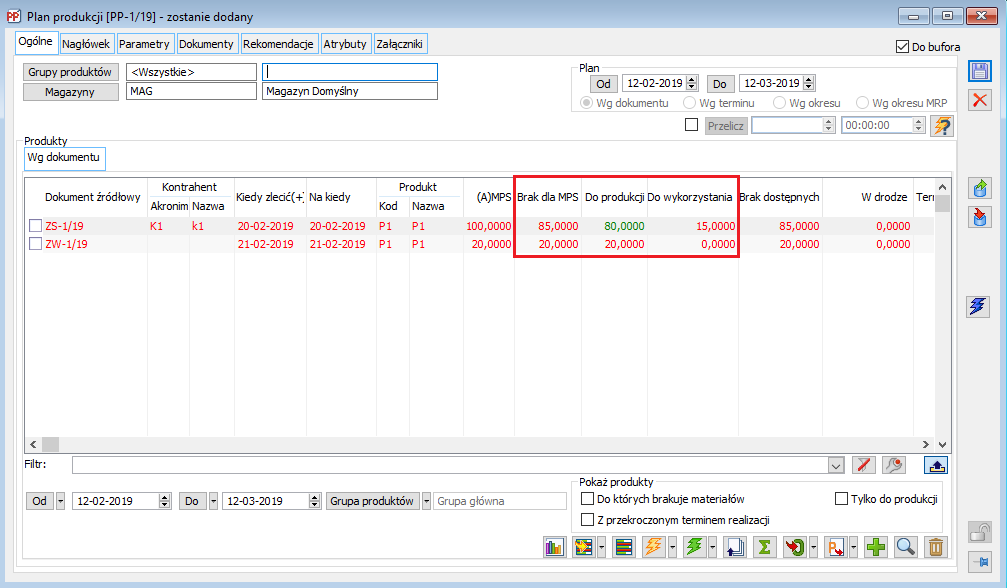
Pomimo, że system zwraca inną, niż poprzednio, informację o braku produktu (w kolumnie: Brak dla MPS) nadal kolumna: Do produkcji pozostaje bez zmian dla pozycji, dla której Użytkownik ręcznie określił ilość.
Jak zablokować dla kolejnych przeliczeń Planu, automatycznie obliczoną ilość w kolumnie: Do produkcji?
Poszczególne ilości, jakie automatycznie wyliczane są na Planie produkcji mogą się zmieniać podczas kolejnych przeliczeń Planu, na skutek zmiany warunków systemowych. Jeśli jednak Użytkownik w pewnym momencie chce zachować informację o ilości w kolumnie: Do produkcji, na jaką generowane mają być dokumenty dla danej pozycji Planu i nie aktualizować tej ilości automatycznie podczas kolejnych przeliczeń dokumentów, może taką ilość „zablokować” za pomocą opcji: Potwierdź ilość do produkcji:
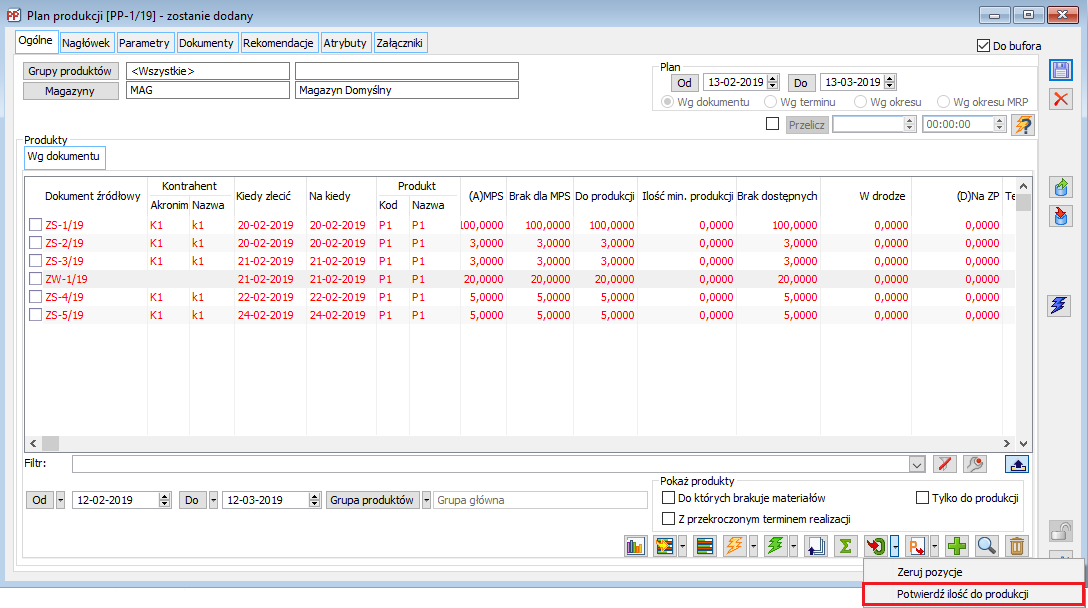
Opcję można uruchomić dla pojedynczej lub wielu zaznaczonych pozycji Planu produkcji. Ilość z kolumny: Do produkcji, która zostanie „potwierdzona do produkcji” będzie traktowana jak zmieniona ręcznie przez Użytkownika. Oznacza to, że nadal będzie można ją ręcznie zmieniać, jednak przeliczanie Planu produkcji nie będzie na nią wpływało.
Przykład użycia opcji: Potwierdź ilość do produkcji.
W systemie zarejestrowano następujące dokumenty:
Potwierdzony dokument ZS-1 na 100 szt. P1 z datą realizacji 20-02-2019
Potwierdzony dokument ZS-2 na 10 szt. P1 z datą realizacji 21-02-2019
Potwierdzony dokument ZS-3 na 40 szt. P1 z datą realizacji 22-02-2019
Na analizowanym magazynie jest dodatkowo 15 szt. produktu P1.
Wystawiono i przeliczono Plan produkcji „Wg dokumentów” uwzględniając ww. dokumenty źródłowe.
W wyniku przeliczenia Planu produkcji, w kolumnie: Do produkcji zwrócona została informacja o ilościach koniecznych do produkcji, wynikających z ww. zamówień z uwzględnieniem stanu produktu P1 na magazynie:
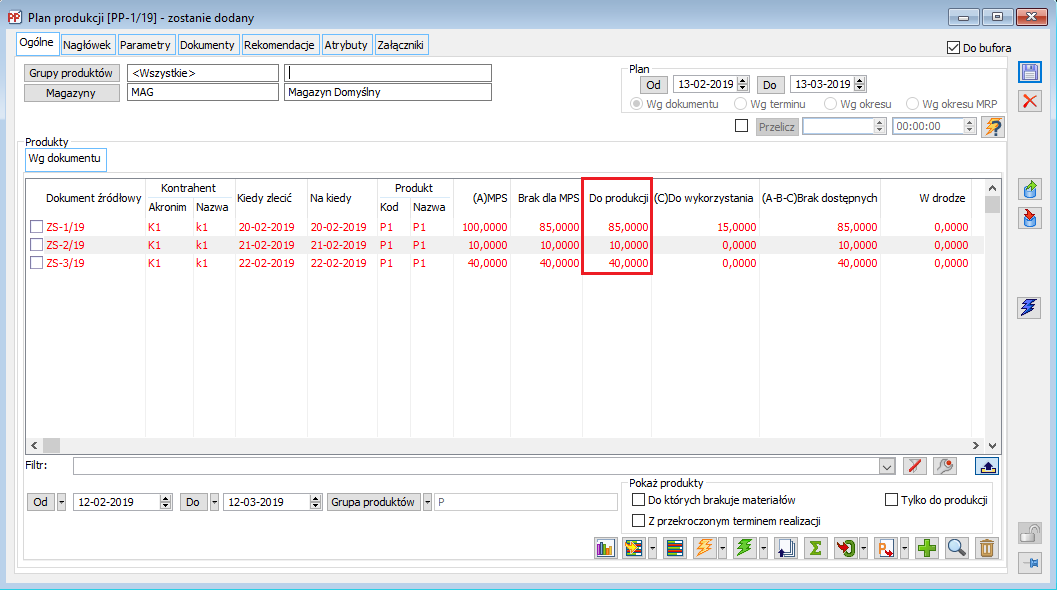
Następnie w kolumnie: Do produkcji, dla elementu wynikającego z ZS‑1 zmieniona zostaje ręcznie ilość z 85 na 200, czyli zostaje w tym wierszu ustalona „nadwyżka produkcyjna” na poziomie 115 szt., którą można wykorzystać na poczet realizacji kolejnych pozycji Planu produkcji. Ustalona ręcznie wartość pozostanie niezmieniona podczas kolejnego przeliczania Planu.
Dodatkowo w kolumnie: Do produkcji, dla elementu wynikającego z ZS‑2 zastosowana zostaje opcja: Potwierdź ilość do produkcji, zatem ilość jaką obliczył system, ma pozostać niezmieniona podczas kolejnych przeliczeń Planu.
W kolumnie: Do produkcji, dla elementu wynikającego z ZS‑3 nie wykonano żadnych zmian.
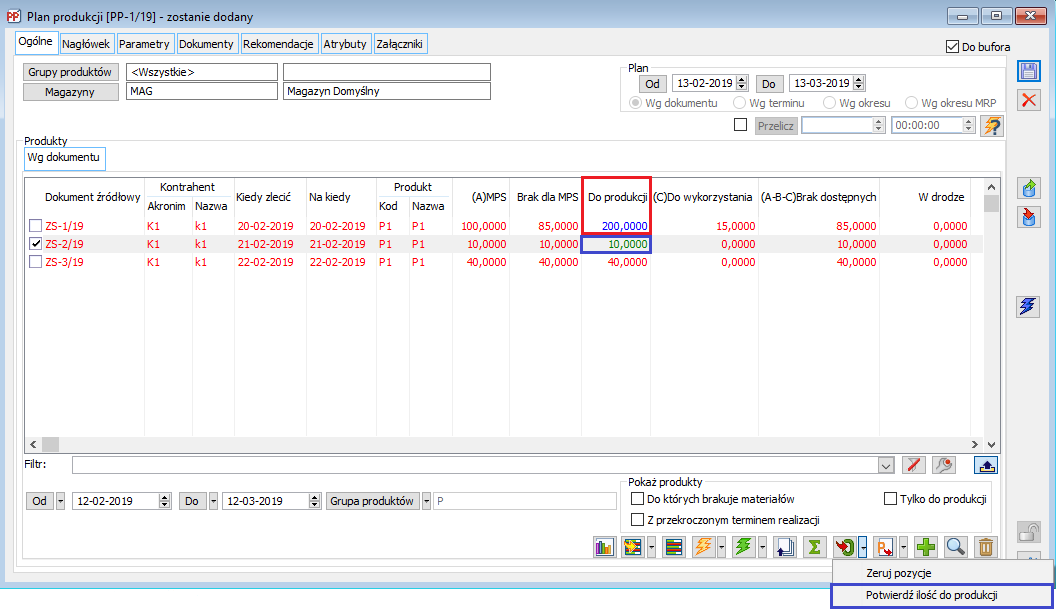
Następnie ponownie przeliczono Plan produkcji. W wyniku tego przeliczenia, system zwrócił następujący wynik:
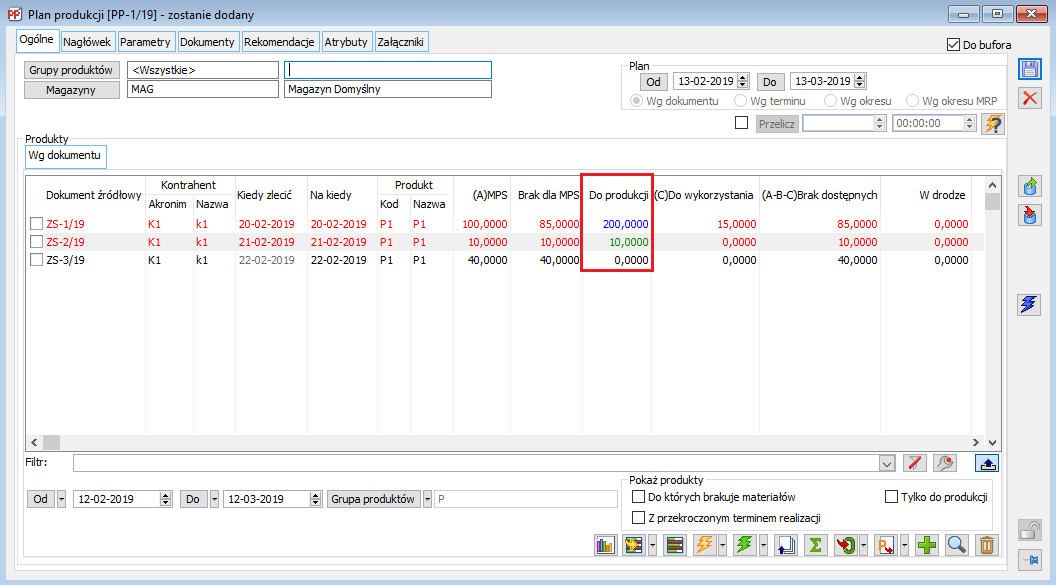
Dla elementu wynikającego z ZS‑1 ilość ustalona ręcznie na poziomie 200 nie uległa zmianie.
Nie uległa także zmianie ilość, jaką „potwierdzono do produkcji” dla elementu wynikającego z ZS‑2, chociaż w wierszu pierwszym powstała nadwyżka produkcyjna (200-85=115), która mogłaby pokryć zapotrzebowanie wynikające z ZS‑2.
Zmianie uległa jedynie ilość w kolumnie: Do produkcji dla elementu wynikającego z ZS‑3. Ilość ta nie była korygowana ręcznie, ani też „potwierdzana do produkcji”, dlatego kolejne przeliczenie Planu uwzględniło w tym wierszu występujące we wcześniejszych terminach nadwyżki produkcyjne.
Jak odblokować na Planie Produkcji ustaloną do produkcji ilość, by była aktualizowana podczas kolejnego przeliczania Planu produkcji?
Ilość w kolumnie: Do produkcji, która została ręcznie zmieniona przez Użytkownika lub potwierdzona za pomocą opcji: Potwierdź ilość do produkcji, nie jest aktualizowana podczas kolejnego przeliczania Planu produkcji.
Na Planie produkcji istnieje jednak opcja, za pomocą której można przywrócić „ustalone” w kolumnie: Do produkcji ilości do stanu, który pozwala na ich automatyczną aktualizację wg bieżących warunków systemowych. Jest to opcja: Zeruj pozycje:
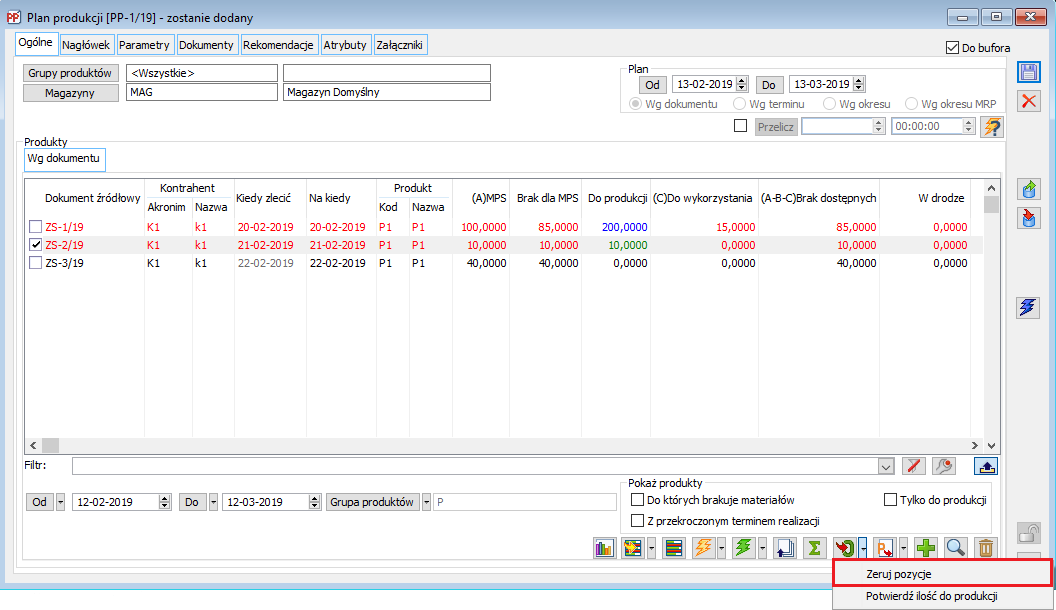
Za pomocą opcji: Zeruj pozycje, można wyzerować ilość w kolumnie: Do produkcji dla pojedynczego lub zaznaczonych elementów Planu produkcji. Wyzerowane za pomocą tej opcji elementy będą podlegały dalszym zmianom podczas kolejnego przeliczania Planu, tzn., jeśli użyto tej opcji dla jakiejś pozycji Planu, to podczas kolejnego przeliczania Planu, ilość w kolumnie: Do produkcji będzie aktualizowana wg istniejących w danej chwili warunków systemowych.
Przykład zastosowania opcji: Zeruj pozycje
W systemie zarejestrowano następujące dokumenty:
Potwierdzony dokument ZS-1 na 100 szt. P1 z datą realizacji 20-11-2015
Potwierdzony dokument ZS-2 na 10 szt. P1 z datą realizacji 21-11-2015
Potwierdzony dokument ZS-3 na 40 szt. P1 z datą realizacji 22-11-2015
Na analizowanym magazynie jest dodatkowo 15 szt. produktu P1.
Wystawiono i przeliczono Plan produkcji „Wg dokumentów” uwzględniając ww. dokumenty źródłowe.
W wyniku przeliczenia Planu produkcji, w kolumnie: Do produkcji zwrócona została informacja o ilościach koniecznych do produkcji, wynikających z ww. zamówień z uwzględnieniem stanu produktu P1 na magazynie:
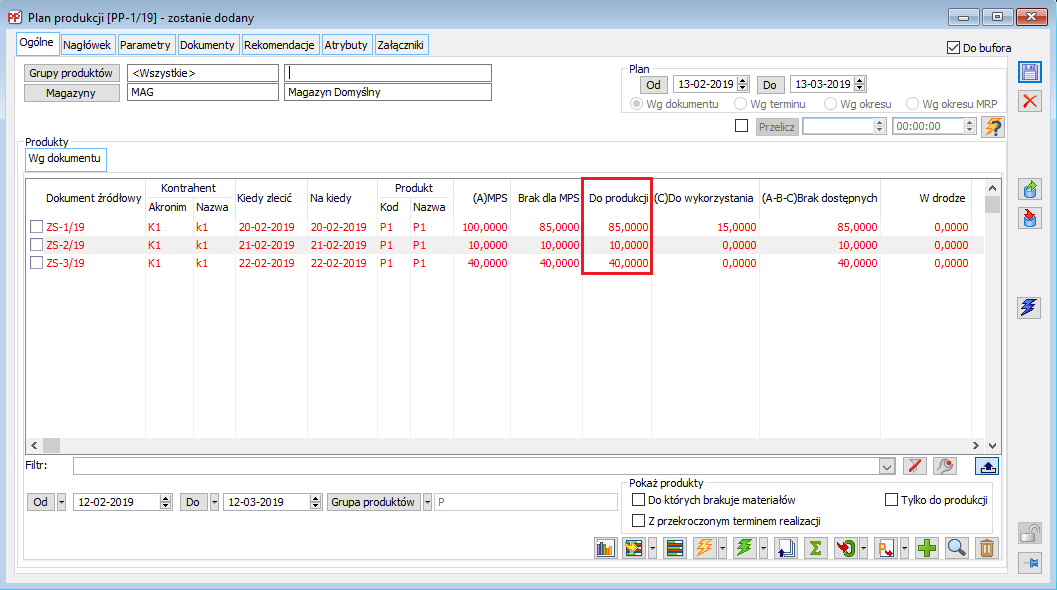
Następnie zaznaczone zostały wszystkie elementy Planu i potwierdzono dla nich ilość do produkcji:
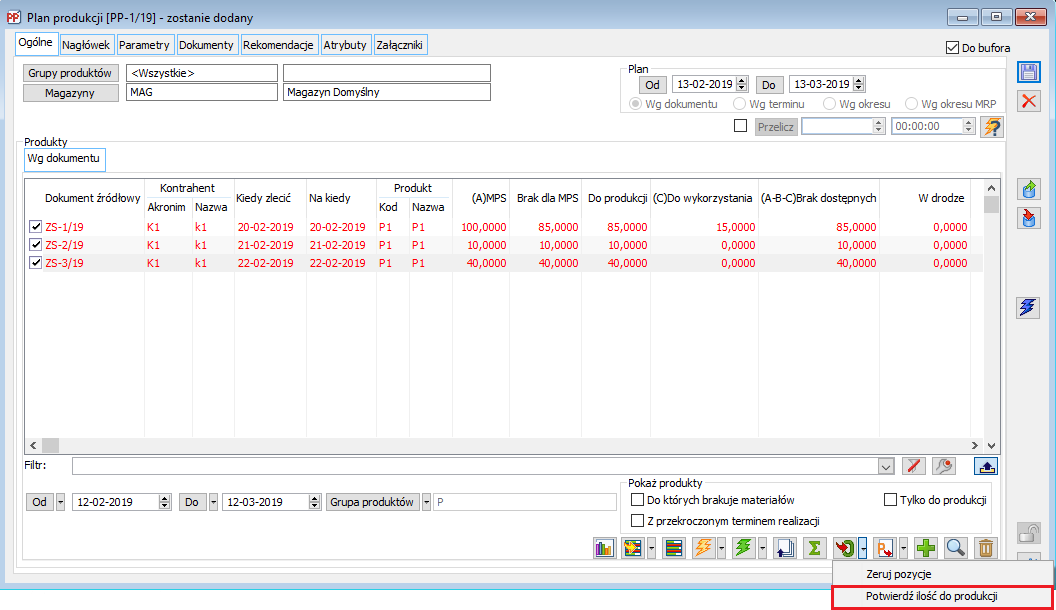
Kolejno dla dokumentu ZS‑1 zmieniła się zamówiona ilość produktu ze 100 na 50.
Następne przeliczenie Planu produkcji uwzględnia zmianę ilości zamówionego produktu P1 (zmiana widoczna w kolumnie: MPS oraz Brak dla MPS), jednak nie aktualizuje ilości w kolumnie: Do produkcji, ponieważ ilość ta została zablokowana dla aktualizacji Planu:
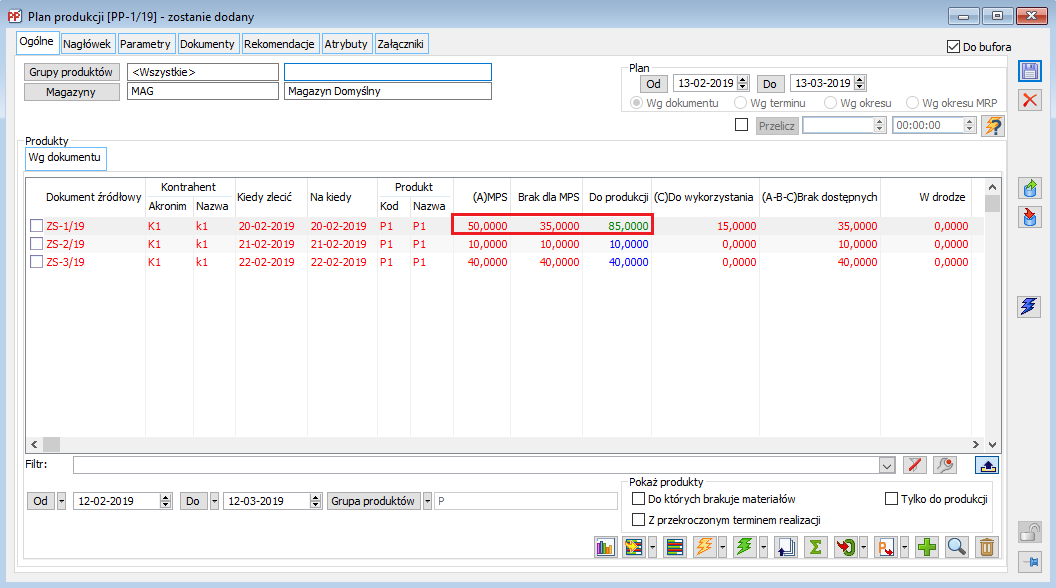
Jeśli w ww. sytuacji Użytkownik chce, by ilości w kolumnie: Do produkcji dla wybranych elementów Planu były z powrotem aktualizowane, podczas przeliczania dokumentu, może je wyzerować za pomocą opcji: Zeruj pozycje. Użycie tej opcji dla wybranych elementów Planu spowoduje, że ich ilość w kolumnie: Do produkcji będzie aktualizowana podczas kolejnego przeliczania Planu produkcji:
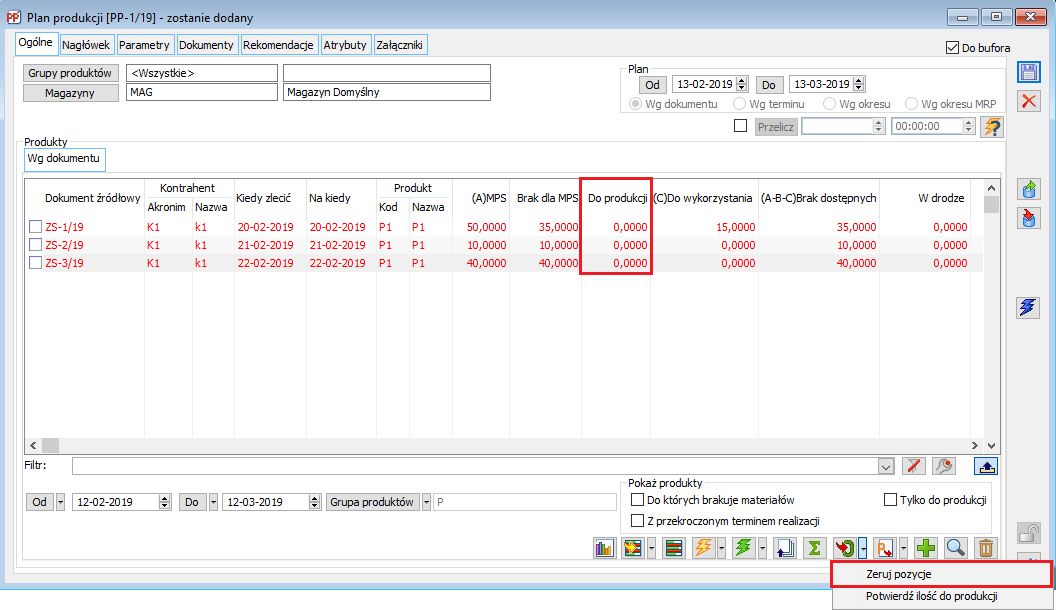
Kolejne przeliczenie Planu aktualizuje „odblokowane” ilości w kolumnie: Do produkcji:
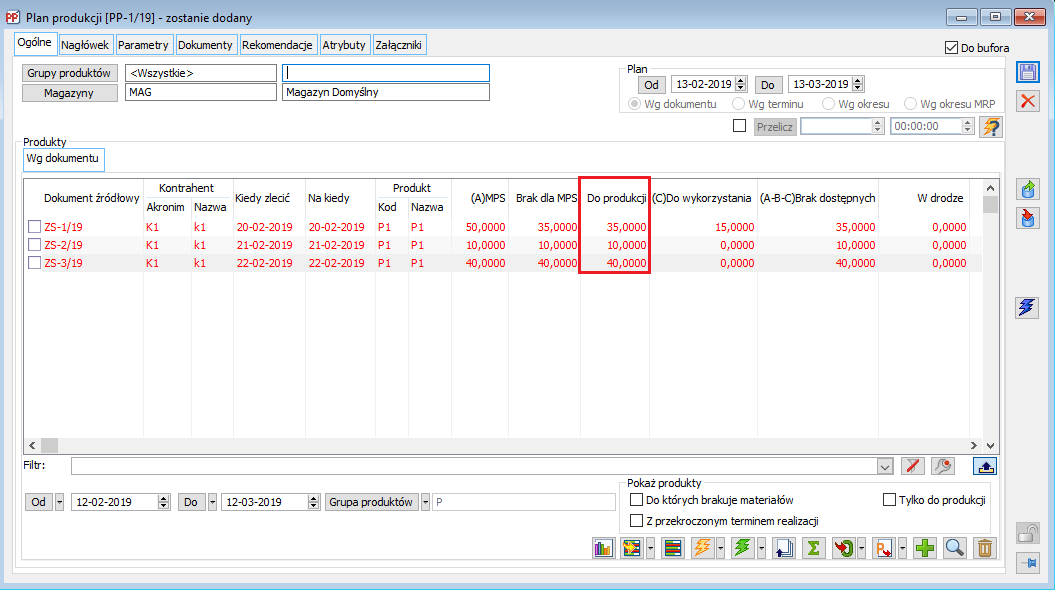
Jak na Planie produkcji uzyskać informację o pełnym zapotrzebowaniu na wszystkie półprodukty oraz materiały potrzebne do wytworzenia wyrobu gotowego?
Aby na Planie produkcji, w zapotrzebowaniu materiałowym uwzględnione zostały wszystkie półprodukty i materiały potrzebne do produkcji wyrobu gotowego na każdym etapie jego wytworzenia, należy odpowiednio skonfigurować system.
Na definicji dokumentu PP należy zaznaczyć parametr: Uwzględniaj BOM półproduktów, wówczas w zapotrzebowaniu materiałowym na Planie produkcji uwzględnione zostaną materiały i półprodukty, znajdujące się na wszystkich poziomach rozwinięcia materiałowego wyrobu gotowego: W technologiach, w których materiałami są półprodukty (towary/produkty posiadające własne technologie), należy w polu: Materiał, wskazać dla nich kartę towaru oraz nie wskazywać pochodzenia z innych operacji. Półprodukty raportowane na Planie produkcji nie są fantomami/półproduktami wirtualnymi, lecz materiałami pobieranymi z magazynu. Dodatkowo należy na karcie towarowej półproduktu zaznaczyć, która technologia wytworzenia jest dla niego technologią podstawową: W systemie zdefiniowano technologię wytworzenia wyrobu gotowego D: Materiałem potrzebnym do produkcji ww. wyrobu jest półprodukt C, posiadający własną technologię wytworzenia: W technologii wytworzenia półproduktu: C, materiałem jest półprodukt: B, który także posiada dalsze rozwinięcie materiałowe i własną technologię produkcji: Materiałem niezbędnym do produkcji półproduktu: B jest surowiec A, który nie posiada własnej technologii produkcji. Każdy półprodukt (B i C) ma na karcie towarowej zaznaczoną technologie podstawową: W systemie zarejestrowano zamówienie sprzedaży na wyrób gotowy: D w ilości 5 szt. Dodano i przeliczono Plan produkcji, na którym uwzględnione zostało ww. zamówienia – przy zaznaczonym parametrze: Uwzględniaj BOM półproduktów, na definicji dokumentu PP, w zapotrzebowaniu materiałowym znajdują się wszystkie materiały (surowce i półprodukty) potrzebne do wytworzenia wyrobu gotowego D, na każdym etapie jego produkcji: Aby na Planie produkcji zgrupować zapotrzebowanie na produkty i materiały w indywidualne okresy MRP, należy zdefiniować/przypisać odpowiedni okres MRP dla każdego towaru/produktu, a następnie przeliczyć Plan produkcji wg odpowiedniej metody, która będzie uwzględniała okresy MRP. W sytuacji, gdy każdy lub większość towarów/produktów ma inny okres planistyczny, najlepiej definiować okresy MRP bezpośrednio na kartach poszczególnych towarów. Na karcie towaru, na zakładce: MRP, możliwe jest określenie, od kiedy dany okres ma obowiązywać dla wybranego towaru oraz ile ma trwać. Przedstawione na rysunku ustawienie oznacza, że pojedynczy okres MRP dla towaru: MATERIAŁ_1 ma trwać 2 tygodnie, a jego „odliczanie” rozpoczyna się 10-12-2016. Jeśli okresy planistyczne są takie same dla wielu towarów/produktów, wówczas najlepiej skorzystać z funkcjonalności definiowania i przypisywania do odpowiednich kartotek, okresów MRP zdefiniowanych na liście kalendarzy. Na Liście kalendarzy, na zakładce: Okresy MRP, można dodawać okresy planistyczne, a następnie przypisywać te okresy do wybranych towarów lub do grup towarowych: Aby raportowane na Planie produkcji zapotrzebowanie grupowane było w odpowiednie okresy MRP, należy na dokumencie PP zaznaczyć metodę przeliczania Planu: Wg okresu MRP, a następnie przeliczyć dokument: Wartości parametrów MRP, definiowanych na kartach towarów/produktów, na zakładce: MRP, są prezentowane na Planie produkcji w osobnych kolumnach jako dodatkowa informacja o towarze/produkcie, ale mogą one także wpływać na obliczaną w kolumnie: Do produkcji (w sekcji: Produkty), czy Do zamówienia (w sekcji: Materiały) ilość. Wybrane parametry MRP należy zdefiniować ręcznie na karcie towaru/produktu, na zakładce: MRP: Każdemu parametrowi MRP z karty towaru, odpowiada osobna kolumna na Planie produkcji, zarówno w sekcji: Produkty, jak i w sekcji: Materiały, w której prezentowana jest wartość odpowiedniego parametru MRP: Jeśli chcemy, by wartość kolumny: Do produkcji lub/i Do zamówienia, na Planie produkcji, była automatycznie obliczana z uwzględnieniem wybranych parametrów MRP, należy na dokumencie PP, na zakładce: Parametry, wprowadzić odpowiednie ustawienia: Na karcie towarowej produktu P1, dla którego na Planie produkcji w ilości: Do produkcji, ma być uwzględniana wartość parametru EOQ, określono tą wartość na poziomie 100: W systemie zarejestrowano dokument ZS na 3 szt. wyrobu gotowego P1. Na dokumencie PP, na którym uwzględnione będzie zapotrzebowanie, na produkt P1, zaznaczono parametr: Ilość do produkcji (dla Produktów) na podstawie EOQ (Ekonomicznej Wielkości Zamówienia) Podczas przeliczania Planu produkcji, ilość Do produkcji, została obliczona na podstawie parametru EOQ i wynosi 100. Ilość EOQ jest tutaj traktowana jako minimalna ilość, którą opłaca się wyprodukować. W opisanym przykładzie, brak (Bak dla MPS), jaki należy uzupełnić wynosi 3, ale ponieważ minimalnie opłaca się uruchomić produkcję na 100 szt. wyrobu (wg wartości parametru EOQ), to system podpowiada ilość Do produkcji jako 100: Przy ustawienie parametru EOQ na karcie produktu P1, jak wcześniej. W systemie zarejestrowano dokument ZS na 101 szt. wyrobu gotowego P1. Na dokumencie PP, na którym uwzględnione będzie zapotrzebowanie, na produkt P1, zaznaczono parametr: Ilość do produkcji (dla Produktów) na podstawie EOQ (Ekonomicznej Wielkości Zamówienia). Podczas przeliczania Planu produkcji, ilość Do produkcji, została obliczona z uwzględnieniem parametru EOQ i wynosi ona 101, ponieważ w opisanym przykładzie, brak (Bak dla MPS), jaki należy uzupełnić wynosi 101. Minimalnie opłaca się uruchomić produkcję na 100 szt. wyrobu gotowego (wg wartości parametru EOQ), zatem by pokryć zapotrzebowanie wynikające z zamówienia i jednocześnie uwzględnić wartość parametru EOQ, system podpowiada ilość Do produkcji jako 101: Na karcie towarowej produktu P1, dla którego w ilości: Do produkcji, ma być uwzględniana wartość parametru Zapas bezpieczeństwa, określono tą wartość na poziomie 200: W systemie zarejestrowano dokument ZS na 101 szt. wyrobu gotowego P1. Na dokumencie PP, na którym uwzględnione będzie zapotrzebowanie, na produkt P1, zaznaczono parametr: Ilość do produkcji (dla Produktów) na podstawie zapasu bezpieczeństwa. Podczas przeliczania Planu produkcji, ilość Do produkcji, została obliczona z uwzględnieniem parametru Zapas bezpieczeństwa i wynosi ona 301, ponieważ w opisanym przykładzie, brak (Bak dla MPS), jaki należy uzupełnić wynosi 101, a zapas bezpieczeństwa, jaki ma być stale utrzymany na magazynie to 200. Zatem w opisanym przykładzie należy wyprodukować 301 szt. wyrobu gotowego, by pokryć zapotrzebowanie oraz zapewnić ustalony zapas bezpieczeństwa: Na karcie towarowej produktu P1, dla którego w ilości: Do produkcji, ma być uwzględniana wartość parametru Wielokrotność, określono tą wartość na poziomie 30: W systemie zarejestrowano dokument ZS na 101 szt. wyrobu gotowego P1. Na dokumencie PP, na którym uwzględnione będzie zapotrzebowanie, na produkt P1, zaznaczono parametr: Ilość do produkcji (dla Produktów) na podstawie wielokrotności: Podczas przeliczania Planu produkcji, ilość Do produkcji, została obliczona z uwzględnieniem parametru Wielokrotność i wynosi ona 120, ponieważ w opisanym przykładzie, brak (Brak dla MPS), jaki należy uzupełnić wynosi 101, a wielokrotność ilości, w jakiej produkowany może być wyrób gotowy wynosi 30. Zatem w opisanym przykładzie potrzeba 101 została unormowana do najmniejszej możliwie liczby, która jest wielokrotnością 30 i jednocześnie pokryje obliczone zapotrzebowanie na produkt w ilości 101: Na karcie towarowej produktu P1, dla którego w ilości: Do produkcji, ma być uwzględniana wartość parametru Zaokrąglenie, określono tą wartość na poziomie 1,0000, co oznacza, że ilość wyrobu gotowego powinna być zaokrąglana do ilości całkowitych: W systemie zarejestrowano dokument ZS na 101.1234 szt. wyrobu gotowego P1. Na dokumencie PP, na którym uwzględnione będzie zapotrzebowanie na produkt P1, zaznaczono parametr: Ilość do produkcji (dla Produktów) po zaokrągleniu: Podczas przeliczania Planu produkcji, ilość Do produkcji, została obliczona z uwzględnieniem parametru Zaokrąglenie i wynosi ona 101: Za pomocą parametrów MRP definiowanych na kartach towarowych można sterować ilością Do zamówienia (w sekcji: Materiały na Planie produkcji) analogicznie, jak ilością Do produkcji (w sekcji: Produkty). Parametry MRP działają podobnie w obu przypadkach, z taką jednak różnicą, że w przypadku materiałów, dla parametrów: Wielokrotność i Zapas bezpieczeństwa, magazyn, dla którego określamy te parametry na karcie towaru, będzie odpowiadał magazynowi ustawionemu na materiale w technologii, w oparciu o którą obliczane jest zapotrzebowanie na Planie produkcji (w sekcji: Materiały) – inaczej, niż w przypadku produktów raportowanych w sekcji: Produkty – tutaj sprawdzany jest magazyn ustawiony na nagłówku Planu produkcji. Na karcie towarowej materiału S1 określono parametr: Wielokrotność na poziomie 5. Jako magazyn pozostawiono opcję <brak>. Nie wskazano konkretnego magazynu, zatem parametr: Wielokrotność będzie traktowany jako normatyw globalny i będzie uwzględniany w tej sytuacji, gdy na materiale w technologii, w oparciu o którą liczone będzie zapotrzebowanie na Planie produkcji, ustawiono magazyn: <Wszystkie> lub <Wybrane>. W technologii, w oparciu o którą liczone będzie zapotrzebowanie na materiał S1 ustawiono dla niego magazyn: <Wszystkie>. Na Planie produkcji, na zakładce: Parametry, zaznaczono parametr: Ilość do zamówienia (dla Materiałów) na podstawie wielokrotności. Podczas przeliczania Planu produkcji, Brak dla danego surowca został obliczony na poziomie 101.1234, natomiast ilość Do zamówienia, została obliczona z uwzględnieniem parametru Wielokrotność i wynosi ona 105, ponieważ jest to najmniejsza wielokrotność liczby 5, która pokrywa obliczony brak. Na karcie towarowej materiału S1 określono parametr: Wielokrotność na poziomie 100. Jako magazyn ustawiono: MAG. Wskazano konkretny magazyn, zatem normatyw będzie dotyczył tylko tego magazynu i będzie uwzględniany w tej sytuacji, gdy na materiale w technologii, w oparciu o którą liczone będzie zapotrzebowanie na Planie produkcji, ustawiono magazyn: MAG. W technologii, w oparciu o którą liczone będzie zapotrzebowanie na materiał S1 ustawiono dla niego magazyn: MAG. Na Planie produkcji, na zakładce: Parametry, zaznaczono parametr: Ilość do zamówienia (dla Materiałów) na podstawie wielokrotności. Podczas przeliczania Planu produkcji, Brak dla danego surowca został obliczony na poziomie 101.1234, natomiast ilość Do zamówienia, została obliczona z uwzględnieniem parametru Wielokrotność i wynosi ona 200, ponieważ jest to najmniejsza wielokrotność liczby 100, która pokrywa obliczony. Na karcie towarowej materiału S1 ustawiono Zapas bezpieczeństwa na magazynie MAG na poziomi 500. Na Planie produkcji, na zakładce: Parametry, zaznaczono parametr: Ilość do zamówienia (dla Materiałów) na podstawie zapasu bezpieczeństwa. Podczas przeliczania Planu produkcji, Brak dla danego surowca został obliczony na poziomie 101, natomiast ilość Do zamówienia, została obliczona z uwzględnieniem parametru Zapas bezpieczeństwa i wynosi ona 601, co zapewnia Zapas bezpieczeństwa (500) i pokrywa obliczony brak (101): Przeliczanie Planu produkcji powoduje aktualizację danych na dokumencie, na podstawie bieżących warunków systemowych. W przypadku przeliczania niepotwierdzonego Planu produkcji, oprócz aktualizacji danych, dotyczących istniejących pozycji Planu, na dokument dodawane są nowe potrzeby produkcyjne, wynikające z wystawionych w międzyczasie dokumentów (składników MPS). Do zaktualizowanego zapotrzebowania na produkty generowane jest nowe zapotrzebowanie na materiały, a wcześniejsze (nieaktualne już) zapotrzebowanie materiałowe w momencie przeliczania Planu jest usuwane. Działanie to z jednej strony daje aktualny obraz stanów materiałów potrzebnych do produkcji wyrobów gotowych, wyświetlonych na Planie produkcji, ale z drugiej strony uniemożliwia zachowanie informacji o ewentualnych wprowadzonych przez Użytkownika w międzyczasie zmianach w sekcji: Materiały – tracona jest, np. informacja o tym, do której konkretnie pozycji wygenerowano dokument (ilość w kolumnie: Związane, zostaje wyzerowana), czy też informacja o ręcznych zmianach ilości w kolumnie: Do zamówienia (ilość: Do zamówienia, obliczana jest na nowo wg aktualnych warunków systemowych). Dlatego po ustaleniu Planu produkcji wyrobów gotowych w danym okresie, zaleca się potwierdzenie dokumentu PP, by móc dodatkowo zarządzać zapotrzebowaniem materiałowym, które dotyczy konkretnego potwierdzonego Planu. Przeliczanie potwierdzonego Planu produkcji nie będzie powodowało aktualizacji potrzeb MPS, ani też doczytywania nowych pozycji do Planu produkcji. Nie będzie także powodowało usuwania i generowania nowego zapotrzebowania materiałowego, ustalonego w momencie potwierdzenia dokumentu, a co za tym idzie umożliwi zachowanie informacji o pewnych zmianach, wprowadzonych pomiędzy jednym, a drugim przeliczaniem dokumentu. Możliwość przeliczania potwierdzonego Planu produkcji ma głównie zastosowanie w przypadkach: W przypadku potrzeb produkcyjnych raportowanych na Planie produkcji w sekcji: Produkty, przeliczanie potwierdzonego Planu produkcji wpływa na aktualizację danych w kolumnach: W przypadku potrzeb materiałowych raportowanych na Planie produkcji w sekcji: Materiały, przeliczanie potwierdzonego Planu produkcji wpływa na aktualizację danych w kolumnach: Aby możliwe było przeliczanie potwierdzonego Planu produkcji, należy na definicji dokumentu PP, w odpowiednim centrum struktury firmy, zaznaczyć parametr: Przeliczaj potwierdzony plan: Na definicji dokumentu PP zaznaczono parametr: Przeliczaj potwierdzony plan. W systemie zarejestrowano 3 zamówienia sprzedaży na wyrób gotowy P1: ZS-1 na 5 szt. P1 ZS-2 na 10 szt. P1 ZS-3 na 15 szt. P1 W systemie nie ma zarejestrowanych innych dokumentów na wyrób gotowy P1, nie ma także tego wyrobu na magazynach. Wystawiono i przeliczono Plan produkcji, na którym uwzględnione zostały ww. zamówienia: Ilości proponowane Do produkcji są w tym przypadku takie, jak odpowiednie potrzeby MPS, wynikające z ww. zamówień. Po potwierdzeniu Planu produkcji wygenerowano 3 dokumenty ZP, na odpowiednie ilości określone w kolumnie: Do produkcji: W kolumnie: Związane, prezentowana jest informacja o ilości, na jaką wygenerowano dokument do danej pozycji Planu. Kontekstowo z poziomu tej kolumny, można dla każdego wiersza sprawdzić, jakie dokumenty zostały już do niej wygenerowane: Dodatkowo, wszystkie dokumenty wygenerowane z Planu produkcji są widoczne na zakładce: Dokumenty: Po przeliczeniu dokumentu PP, zaktualizowana została kolumna: Na ZP, w której prezentowana jest informacja o ilościach znajdujących się na dokumentach ZP wygenerowanych do danej pozycji Planu: Z poziomu Planu produkcji można uruchomić Planowanie zleceń, które zostały wygenerowane z Planu produkcji: Po zaplanowaniu zleceń produkcyjnych i przeliczeniu Planu produkcji, informacja o zaplanowanych ilościach jest prezentowana w kolumnie: Zaplanowana: Po wykonaniu realizacji operacji na dokumentach ZP wygenerowanych do danych pozycji Planu oraz po przeliczeniu Planu produkcji, informacja o ilościach produktu zrealizowanych, ale nie przyjętych jeszcze dokumentami PW na magazyn, będzie widoczna w kolumnie: W toku: Po wygenerowaniu z ZP i potwierdzeniu dokumentów PW, a następnie po przeliczeniu Planu, odpowiednia ilość wynikająca z dokumentów PW, uwzględniana jest na Planie produkcji w kolumnie: Przyjęta na magazyn: Jeśli, na którymś z ww. zamówień sprzedaży, uwzględnionych na przykładowym Planie produkcji, zmieniona zostanie ilość produktu P1, np. na ZS‑1 ilość 5 zostanie zmieniona na 40, to po przeliczeniu potwierdzonego dokumentu PP, ilość MPS wynikająca z ZS‑1 nie zmieni się. Natomiast na nowym dokumencie PP ilość ta zostanie odpowiednio uwzględniona w ramach kolumny MPS.: Na definicji dokumentu PP zaznaczono parametr: Przeliczaj potwierdzony plan. W systemie zarejestrowano 3 zamówienia sprzedaży na wyrób gotowy P1: ZS-1 na 40 szt. P1 ZS-2 na 10 szt. P1 ZS-3 na 15 szt. P1 Technologia wytworzenia wyrobu gotowego P1, składa się z jednej operacji, trwającej 1 dzień, w ramach której pobierany jest materiał S1 w ilości 1 i wytwarzany jest produkt P1 w ilości 1. Wystawiono i przeliczono Plan produkcji, na którym uwzględnione zostały ww. zamówienia. Ilości: Do produkcji, wynikające z ww. zamówień zostały obliczone odpowiednio jako: 40, 10, 15 i dla tych ilości wyliczone zostały odpowiednie potrzeby materiałowe w ilościach odpowiednio: 40, 10, 15, oraz w tych samych ilościach obliczona została ilość materiału proponowana Do zamówienia: Następnie Plan produkcji został potwierdzony i ręcznie zmieniona została ilość: Do zamówienia dla pierwszego wiersza w sekcji: Materiały, z 40 na 1000, a dla dwóch pozostałych na 0: Następnie w celu uzupełnienia zapotrzebowania materiałowego, z poziomu pierwszej pozycji w sekcji: Materiały, wygenerowano dokument ZZ: Kolejno przeliczono Plan produkcji – ponieważ dokument PP był potwierdzony w momencie przeliczania, nie zostały na nim utracone informacje o ręcznych zmianach ilości: Do zamówienia oraz o wygenerowanym dokumencie ZZ i jednocześnie zaktualizowane zostały informacje o ilościach danego towaru w drodze, wynikających z wygenerowanego dokumentu ZZ: Aby na wszystkich zleceniach produkcyjnych, generowanych z poziomu dokumentu PP, domyślnie podpowiadał się odpowiedni, w odniesieniu do terminu potrzeby, termin zakończenia produkcji, należy zaznaczyć parametr: Wstecz od daty ustalonej na PP/PLZ/BST, na definicji dokumentu ZP, na zakładce: Inne: Na definicji Planu produkcji w danym centrum zaznaczono parametr: Wstecz od daty ustalonej na PP/PLZ/BST pomniejszonej o 1 dni. Na przeliczonym Wg dokumentu Planie produkcji, zaznaczono 2 pierwsze rekordy, w których potrzeba produkcyjna została wykazana odpowiednio na terminy: 03-04-2019 i 05-04-2019, a następnie wygenerowano do nich zlecenie produkcyjne: Na pozycjach dokumentu ZP zostały ustalone odpowiednio terminy planowania wstecz dla obu pozycji: dla pierwszej jest to 02-04-2019, czyli termin z pierwszej zaznaczonej pozycji PP, pomniejszony o 1 dzień (wg ustawienia na definicji dokumentu ZP): natomiast dla drugiej pozycji jest to 04-04-2019, czyli termin drugiej zaznaczonej pozycji PP, pomniejszony o 1 dzień (wg ustawienia na definicji dokumentu ZP): Na Planie produkcji przeliczonym Wg dokumentu, w zapotrzebowaniu materiałowym uwzględniono półprodukt B, potrzebny na termin 07-04-2019 do produkcji wyrobu gotowego. Zaznaczono pozycje z tym półproduktem i wygenerowano dokument ZP: Na pozycji wygenerowanego dokumentu ZP jako data planowania wstecz podpowiada się automatycznie data 06‑04‑2019, czyli termin, na który uwzględniono na Planie produkcji potrzebę materiałową B, pomniejszony o 1 dzień (wg ustawienia na definicji dokumentu ZP): Na Planie produkcji przeliczonym Wg okresu, w zapotrzebowaniu produkcyjnym uwzględniono w okresie planistycznym od: 04-04-2019 do: 10-04-2019, zapotrzebowanie na wyrób gotowy P1. Zaznaczono daną pozycje i uruchomiono generowanie dokumentu ZP: Jeśli w oknie: Wybierz sposób generowania zleceń, zaznaczona zostanie opcja: Wg definicji ZP, wówczas na pozycji wygenerowanego dokumentu ZP jako data planowania wstecz podpowie się termin wyznaczający koniec okresu planistycznego, pomniejszony o 1 dzień, wg ustawienia na definicji dokumentu ZP: Jeśli chcemy by podczas przeliczania Planu produkcji, automatycznie optymalizowane były ilości w kolumnach Do produkcji lub/i Do zamówienia dla kolejnych terminów wskazanych na Planie, należy wprowadzić odpowiednie ustawienia na definicji dokumentu PP. Optymalizacja ilości oznacza tutaj redukcję proponowanych do produkcji, czy do zamówienia ilości tego samego produktu/materiału w kolejnych terminach, gdy we wcześniejszych terminach ilość do produkcji, czy do zamówienia była nadmiarowa, tzn. była większa niż konieczna do pokrycia braku (z uwzględnieniem ewentualnych parametrów MRP). Przykładowo, jeśli w terminie 08‑04‑2019 dla produktu P1 na Planie produkcji wyświetlona została ilość do produkcji na poziomie 100, a w terminie 09-04-2019 dla produktu P1 ilość do produkcji na poziomie 200 i jeśli, np. w pierwszym terminie (08-04-2019) Użytkownik zmienił ręcznie ilość do produkcji ze 100 na 150, to podczas przeliczenia Planu, ilość Do produkcji w drugim/późniejszym terminie (09‑04‑2019) zostanie automatycznie zredukowana do 150, by nie produkować niepotrzebnych nadwyżek. Optymalizacja ilości w kolumnie: Do produkcji z uwzględnieniem parametrów MRP będzie polegała na wykonaniu takiej redukcji odpowiednich ilości w kolumnie: Do produkcji na Planie produkcji, by dla każdego optymalizowanego rekordu zapewnić pokrycie obliczonego braku, unormowanego do wybranych parametrów MRP. Na definicji Planu produkcji zaznaczono parametr: Optymalizacja ilości do produkcji. Na karcie towarowej produktu P3, określono wartość parametru EOQ na poziomie 10: W systemie zarejestrowano następujące zamówienia sprzedaży na produkt P3: ZS-1 na 01-04-2019 na 5 szt. ZS-2 na 02-04-2019 na 2 szt. ZS-3 na 04-04-2019 na 1 szt. ZS-4 na 06-04-2019 na 12 szt. Na Planie produkcji zaznaczono parametr: Ilość do produkcji (dla Produktów) na podstawie EOQ (Ekonomicznej Wielkości Zamówienia): Przeliczono Plan produkcji, na którym uwzględnione zostały potrzeby na produkt P3, wynikające z wystawionych zamówień: Ilość do produkcji w kolejnych terminach została odpowiednio zoptymalizowana z uwzględnieniem parametru EOQ: W pierwszym terminie 01-04-2019, Brak dla MPS wynosi 5 i taką ilość musimy wyprodukować by pokryć brak, ale parametr EOQ „mówi nam”, że minimalnie możemy uruchomić produkcję na 10 szt., zatem ilość: Do produkcji, automatycznie obliczona została jako 10. W drugim terminie 02-04-2019, Brak dla MPS wynosi 2 i taką ilość musimy zapewnić, by pokryć brak, ale ponieważ, w terminie 01-04-2019, po zapewnieniu braku, pozostanie nam nadwyżka produkcyjna w ilości 5 szt. (Do produkcji (10) – Brak dla MPS (5) = nadwyżka (5)), to na termin 02-04-2019 nie musimy nic produkować, ponieważ wcześniejsza nadwyżka produkcyjna pokryje nam obliczony brak. Zatem w terminie 02-04-2019 ilość: Do produkcji, została ustalona na poziomie 0. W trzecim terminie 04-04-2019, Brak dla MPS wynosi 1 i taką ilość produktu musimy zapewnić, by pokryć brak, ale ponieważ z nadwyżki produkcyjnej, jaka powstanie w terminie 01-04-2019 (5 szt. nadwyżki), po zapewnieniu obliczonego braku w terminie 02-04-2019 (2 szt.), pozostanie jeszcze do wykorzystania 3 szt., to tą ilość możemy także wykorzystać do zapewnienia potrzeby w terminie 04-04-2019 (w ilości 1szt.). Zatem w terminie 04-04-2019 ilość: Do produkcji, została ustalona na poziomie 0. W czwartym terminie 06-04-2019, Brak dla MPS wynosi 12 i taką ilość musimy zapewnić, by pokryć brak, ale ponieważ z nadwyżki produkcyjnej, jaka powstanie w terminie 01-04-2019 (5 szt. nadwyżki), po zapewnieniu obliczonego braku w terminie 02-04-2019 (2 szt.) oraz w terminie 04-04-2019 (1 szt.) pozostanie jeszcze do wykorzystania 2 szt., to tą ilość możemy także wykorzystać do częściowego zapewnienia potrzeby w terminie 06‑04‑2019. Po uwzględnieniu nadwyżki produkcyjnej z wcześniejszych terminów, konieczne będzie wyprodukowanie na termin 06-04-2019, 10 szt. wyrobu gotowego. Parametr EOQ wynosi 10, zatem wyprodukowanie 10 szt. produktu na termin 06-04-2019 wystarczy, by pokryć brak i uwzględnić parametr EOQ. Dlatego ilość Do produkcji w terminie 06-04-2019 została obliczona na poziomie 10. Na definicji Planu produkcji zaznaczono parametr: Optymalizacja ilości do produkcji. Na karcie towarowej produktu P3, określono wartość parametru Zapas bezpieczeństwa na poziomie 500, dla wszystkich magazynów: W systemie zarejestrowano następujące zamówienia sprzedaży na produkt P3: ZS-1 na 01-04-2019 na 50 szt. ZS-2 na 02-04-2019 na 300 szt. ZS-3 na 04-04-2019 na 200 szt. ZS-4 na 06-04-2019 na 100 szt. Na Planie produkcji zaznaczono parametr: Ilość do produkcji (dla Produktów) na podstawie zapasu bezpieczeństwa: Przeliczono Plan produkcji, na którym uwzględnione zostały potrzeby na produkt P3 wynikające z wystawionych zamówień: W pierwszym terminie 01-04-2019, Brak dla MPS wynosi 50 i taką ilość musimy wyprodukować by pokryć brak, ale parametr Zapas bezpieczeństwa „mówi nam”, że na magazynie musi stale pozostawać zapas produktu w ilości 500, zatem ilość: Do produkcji, automatycznie obliczona została jako 550 (50, by pokryć brak + 500, by zapewnić zapas bezpieczeństwa). W drugim terminie 02-04-2019, Brak dla MPS wynosi 300 i taką ilość musimy zapewnić, by pokryć brak, ale parametr Zapas bezpieczeństwa dodatkowo wymaga zapewnienia 500 szt. produktu na magazynie. System jednak nie podpowiada w tym wierszu dodatkowych 500 szt. do produkcji, ponieważ zapas bezpieczeństwa został zapewniony już w terminie 01-04-2019, zatem po wyprodukowaniu 300 szt. produktu na termin 02-04-2019 będziemy mieć w sumie 300 szt. – do zapewnienia braku w tym terminie oraz 500 szt. zapasu bezpieczeństwa, wyprodukowanego w terminie 01-04-2019. W trzecim terminie 04-04-2019, Brak dla MPS wynosi 200 i taką ilość produktu musimy zapewnić, by pokryć brak. Tak jak w poprzednim terminie, zapas bezpieczeństwa nadal pozostaje na magazynie w ilości 500, zatem by zapewnić potrzebę produkcyjną i nadal pozostawić zapas na magazynie, należy na termin 04-04-2019 wyprodukować 200 szt. wyrobu P3, stąd ilość Do produkcji została obliczona na poziomie 200. W czwartym terminie 06-04-2019, Brak dla MPS wynosi 100 i taką ilość musimy zapewnić, by pokryć brak. Analogicznie, jak w poprzednim terminie, nie musimy dodatkowo produkować ilości potrzebnej do zapewnienia zapasu bezpieczeństwa, ponieważ ten zapas nadal pozostaje na magazynie w ilości 500. Należy wyprodukować zatem tyle wyrobu gotowego na ten termin, by pokryć obliczony brak. Zatem ilość: Do produkcji w ostatnim raportowanym terminie została obliczona na poziomie 100. Jeśli optymalizacja ilości Do produkcji nie byłaby włączona, wówczas w każdym z ww. terminów, zapas bezpieczeństwa doliczany byłby do braku i w kolejnych terminach, ilość Do produkcji raportowana byłaby w następujących ilościach: 01-04-2019 Do produkcji: 550 (Brak dla MPS (50) + Zapas bezpieczeństwa (500)) 02-04-2019 Do produkcji: 800 (Brak dla MPS (300) + Zapas bezpieczeństwa (500)) 04-04-2019 Do produkcji: 700 (Brak dla MPS (200) + Zapas bezpieczeństwa (500)) 06-04-2019 Do produkcji: 600 (Brak dla MPS (100) + Zapas bezpieczeństwa (500)) Optymalizacja ilości w kolumnie: Do zamówienia, w sekcji: Materiały na Planie produkcji, działa na analogicznej zasadzie, jak optymalizacja ilości: Do produkcji, w sekcji: Produkty. Różnica będzie w przypadku, gdy nadwyżki produkcyjne, wynikają z ręcznego określana ilości: Do produkcji/Do zamówienia. Należy tutaj pamiętać, że ręczna zmiana ilości w sekcji: Materiały jest zapamiętywana, podczas przeliczania Planu, ale tylko w sytuacji, gdy jest on potwierdzony. Zatem jeśli ręcznie modyfikujemy ilości Do zamówienia i przeliczamy ponownie dokument, warto wcześniej potwierdzić Plan produkcji. Na definicji dokumentu PP, zaznaczono parametr: Optymalizacja ilości do zamówienia. Na karcie materiału, którego zapotrzebowanie będzie optymalizowane na Planie produkcji, określono wartość parametru EOQ na poziomie 20: Na dokumencie PP, zaznaczono parametr: Ilość do zamówienia (dla Materiałów) na podstawie EOQ (Ekonomicznej Wielkości Zamówienia): Przeliczono Plan produkcji, na którym wyświetlone zostało zapotrzebowanie na materiał S4. Ilość: Do zamówienia została obliczona następująco: W pierwszym terminie: 10-04-2019 brak, jaki należy uzupełnić, to 10 szt., jednak ze względu na wartość parametru EOQ, określoną na poziomie 20, ilość: Do zamówienia, została obliczona jako 20 szt. W drugim terminie: 12-04-2019 brak, jaki należy uzupełnić, to także 10 szt., jednak, przy włączonej optymalizacji ilości, system obliczył ilość: Do zamówienia, na poziomie 0, ponieważ zapas, jaki powstanie po wykorzystaniu Ilości: Do zamówienia, zarekomendowanej w pierwszym terminie (Do zamówienia (20) ‑ Brak (10) = Zapas (10)), wystarczy, by zapewnić potrzebę materiałową także w terminie drugim. W trzecim terminie: 14-04-2019 brak, jaki należy uzupełnić to 10 szt., nie mamy już zapasu z poprzednich terminów, który można byłoby wykorzystać w analizowanym terminie. Dodatkowo wg wartości parametru EOQ, ilość, jaką opłaca się zamówić, wynosi 20 zatem ilość: Do zamówienia, została obliczona w tym wierszu jako 20. Następnie, w celu ewentualnego zmodyfikowania obliczonych przez system ilości: Do zamówienia i uwzględnienia wprowadzonych zmian w raportowanym, we wszystkich terminach, zapotrzebowaniu na materiał S4, należy potwierdzić Plan, dokonać zmiany ilości: Do zamówienia w wybranych rekordach i przeliczyć ponownie Plan: W ramach opisywanego przykładu, zmieniono ilość: Do zamówienia, obliczoną w pierwszym terminie z 20 na 30 i przeliczono ponownie Plan. Po przeliczeniu dokumentu: W pierwszym terminie: 10-04-2019, ilość: Do zamówienia, pozostała na poziomie 30 – jest to ilość wprowadzona ręcznie, zatem przeliczanie (potwierdzonego) Planu nie powinno tej ilości zmieniać. W drugim terminie: 12-04-2019, ilość: Do zamówienia, została obliczona, jak poprzednio jako 0, ponieważ nadwyżka, wynikająca z pierwszego terminu (Do zamówienia (30) – Brak (10) = Nadwyżka (20)) zapewnia pokrycie braku w drugim terminie. W trzecim terminie: 14-04-2019, ilość: Do zamówienia, została obliczona jako 0, ponieważ nadwyżka, wynikająca z pierwszego terminu zapewnia pokrycie zarówno braku obliczonego w terminie drugim, jak i trzecim. Istnieje możliwość sparametryzowania Planu produkcji w ten sposób, by podczas obliczania ilości materiału ogólnie dostępnego i materiału w drodze, brana była pod uwagę ilość tego materiału na magazynie, określonym w technologii. Jeśli chcemy by domyślnie na dokumencie PP, w wyliczaniu ilości ogólnie dostępnej oraz ilości w drodze dla materiału brany był pod uwagę jedynie magazyn, wskazany na danym materiale w odpowiedniej technologii, to na definicji dokumentu PP, w odpowiednim centrum struktury firmy, należy zaznaczyć parametry: Ilość ogólnie dostępna (dla Materiałów) na magazynach potrzeb oraz Ilość w drodze (dla Materiałów) na magazynach potrzeb. Ustawienie ww. parametru jest dodatkowo możliwe do zmiany z poziomu dokumentu PP: W systemie zdefiniowano technologię produkcji dla produktu P1 z materiałem S1: Na materiale S1 w ramach ww. technologii wybrano magazyn MAG: W systemie zarejestrowany ZP na 10 sztuk produktu P1. Na magazynie MAG jest 8 sztuk materiału S1, a na magazynie MAG2 dostępne są 4 sztuki. W systemie zarejestrowano dodatkowo dokument ZZ: ZZ-1 na 5 szt. S1 na magazyn MAG Wystawiamy dokument PP z zaznaczonymi parametrami: Ilość ogólnie dostępna (dla Materiałów) na magazynach potrzeb oraz Ilość w drodze (dla Materiałów) na magazynach potrzeb. Następnie przeliczamy PP Wg dokumentu. W ilości ogólnie dostępnej oraz w drodze zostały uwzględnione tylko ilości z magazynu potrzeb z technologii, który jest wskazany w kolumnie Magazyn.Ustawienia na definicji dokumentu PP
Odpowiednie zdefiniowanie półproduktów w technologiach
Raportowanie pełnego zapotrzebowania na Planie produkcji
Jak na Planie produkcji grupować zapotrzebowanie na produkty i materiały w indywidualne okresy MRP?
Definiowanie okresów MRP, gdy każdy towar ma inny okres planistyczny
Definiowanie okresów MRP, gdy wiele towarów ma ten sam okres planistyczny
Grupowanie zapotrzebowania w indywidualne okresy MRP na Planie produkcji
Jak za pomocą parametrów MRP wpływać na ilość proponowaną do produkcji i do zamówienia na Planie produkcji?
Definiowanie parametrów MRP
Prezentowanie wartości parametrów MRP na Planie produkcji
Ustawienia odpowiadające za automatyczne obliczanie wartości w kolumnach: Do produkcji i Do zamówienia, na podstawie parametrów MRP, na Planie produkcji
Przykłady obliczania ilości Do produkcji, na podstawie parametrów MRP
Przykłady obliczania ilości Do zamówienia, na podstawie parametrów MRP
Zastosowanie opcji: Przeliczaj potwierdzony plan
Ustawienie na definicji dokumentu PP
Przykład przeliczania potwierdzonego Planu produkcji – aktualizacja postępów produkcji wg ustalonego Planu
Przykład przeliczania potwierdzonego Planu produkcji – dopasowywanie zapotrzebowania materiałowego do ustalonego Planu
Jak zautomatyzować dopasowywanie daty planowania zleceń do terminów potrzeb produkcyjnych, określonych na Planie produkcji?
Ustawienie na definicji dokumentu ZP
Zasady automatycznego podpowiadania daty zakończenia produkcji, na dokumentach ZP generowanych z Planu produkcji
Przykłady automatycznego ustawiania odpowiedniej daty planowania wstecz na dokumentach ZP, generowanych z Planu produkcji:
Jak automatycznie optymalizować ilości: Do produkcji i Do zamówienia, na Planie produkcji, uwzględniając dodatkowe parametry MRP?
Ustawienia na definicji dokumentu PP
Optymalizacja ilości w kolumnie: Do produkcji z uwzględnieniem parametrów MRP
Optymalizacja ilości w kolumnie: Do zamówienia z uwzględnieniem parametrów MRP
Jak na Planie produkcji uzyskać informacje o dostępności materiału na magazynie wskazanym w technologii?
Parametryzacja definicji dokumentu PP
Przykład obliczania ilości materiału na magazynie wskazanym w technologii