Zlecenia produkcyjne
Informacje ogólne
Za pomocą zlecenia produkcyjnego realizowany jest proces produkcji – planowanie operacji, jakie mają zostać wykonane, generowanie rezerwacji, realizacja zaplanowanych operacji. Z poziomu tego dokumentu możliwe jest również wykonanie takich operacji, jak: generowanie RW i PW, rozliczanie zlecenia i jego zamknięcie. Funkcje te zostały szczegółowe omówione w kolejnych rozdziałach. Operacje do wykonania w ramach zlecenia produkcyjnego są również dostępne z poziomu Harmonogramu operacji.
Na karcie operatora znajduje się parametr „Widzi koszty zlecenia”. Dotyczy on podglądu kosztu na zleceniach kompletacji jak i na zleceniach produkcyjnych (od wersji 2017.1). Po odznaczeniu parametru zostaną ukryte pola informujące o koszcie wyrobu gotowego oraz jego składników.
Kod oraz nazwa materiału oraz produktów są wyświetlane na podstawie karty towaru (nie na podstawie danych materiału w technologii). Zmiany zostały naniesione na zleceniu produkcyjnym na zakładce Procesy oraz Materiały, na realizacji zakładka Materiały, w szczegółach zlecenia zakładka Produktu uboczne, w oknie operacji planowanej zakładka Półprodukty, w oknie Lista zasobów przy wiązaniu ze sobą zasobów, w oknie Harmonogram operacji zakładka Materiały.
Definicja dokumentu zlecenia produkcyjnego
Dokument: Zlecenie produkcyjne, ma swoją definicję, dostępną do edycji z poziomu modułu: Administrator. Podczas analizowania opisu, należy zwrócić uwagę na parametry, które dotyczą definicji dokumentu zlecenia produkcyjnego (aktywne pola na definicji tego dokumentu).
Definicja dokumentu ZP, zakładka: Ogólne
Ustal koszt przy zamykaniu zlecenia – zaznaczenie spowoduje, że na zleceniach produkcyjnych koszt produktu będzie ustalany dopiero po uruchomieniu dla tych zleceń funkcji ich zamykania, czyli dopiero zamknięcie zlecenie spowoduje na produkcie ustalenie kosztu. Parametr ten można edytować jeszcze bezpośrednio na zleceniu produkcyjnym. W przypadku ustalenia kosztu produktu przez zamknięciem zlecenia. Parametr ten ma wpływ na możliwość generowania dokumentów PWK ze zlecenia produkcyjnego.
Definicja dokumentu ZP, zakładka: Inne
Na definicji dokumentu zlecenia produkcyjnego znajduje się pole: Rezerwacje aktywne przed terminem, które nie występuje na definicji innego dokumentu. Ustawienie parametru decyduje o terminie generowania rezerwacji na planowanej operacji. Data ustawiona w tym polu zostanie wprowadzona na planowaną operację, na zakładkę: Rezerwacje. Należy również zwrócić uwagę na datę ważności rezerwacji określaną na definicji dokumentu. Data taka może zostać określona jako nieograniczona, co oznacza, że wygaśnie ona dopiero wtedy, gdy zostanie zrealizowana lub usunięta. Niezależnie od ustawień na definicji dokumentu, możliwe jest ręczne określanie dla konkretnych rezerwacji innych dat aktywności i ważności.
Istotne jest również określenie parametru: Rezerwuj zasoby oraz Rezerwacje blokują towar na magazynie.
Odznaczenie parametru: Rezerwuj zasoby, powoduje, że podczas planowania zlecenia produkcyjnego do generowanych rezerwacji nie będą automatycznie przypisywane zasoby. Na dokumencie zlecenia produkcyjnego znajduje się jednak parametr: Rezerwuj zasoby, którego zaznaczenie umożliwia przypisanie zasobów do rezerwacji generowanych w trakcie planowania tego dokumentu.
Jeżeli odznaczony jest zarówno parametr: Rezerwuj zasoby oraz Rezerwacje blokują towar na magazynie, wtedy podczas planowania zlecenia produkcyjnego w ogóle nie będzie możliwości automatycznego przypisywania zasobów do wygenerowanych rezerwacji.
Należy jednak pamiętać, że odznaczenie tych parametrów na definicji dokumentu zlecenia, w sytuacji, gdy rezerwacje na zleceniu mają już przypisane zasoby, nie zwolni tych zasobów.
Na definicji dokumentu ZP wprowadzono parametr decydujący o ustawieniu proponowanej daty planowania zlecenia, jeśli zlecenie wygenerowano z ZS lub ZW. Dla nowego parametru można dodatkowo określić ilość dni oraz godzin, o jaką pomniejszona ma być proponowana data planowania zlecenia wstecz:
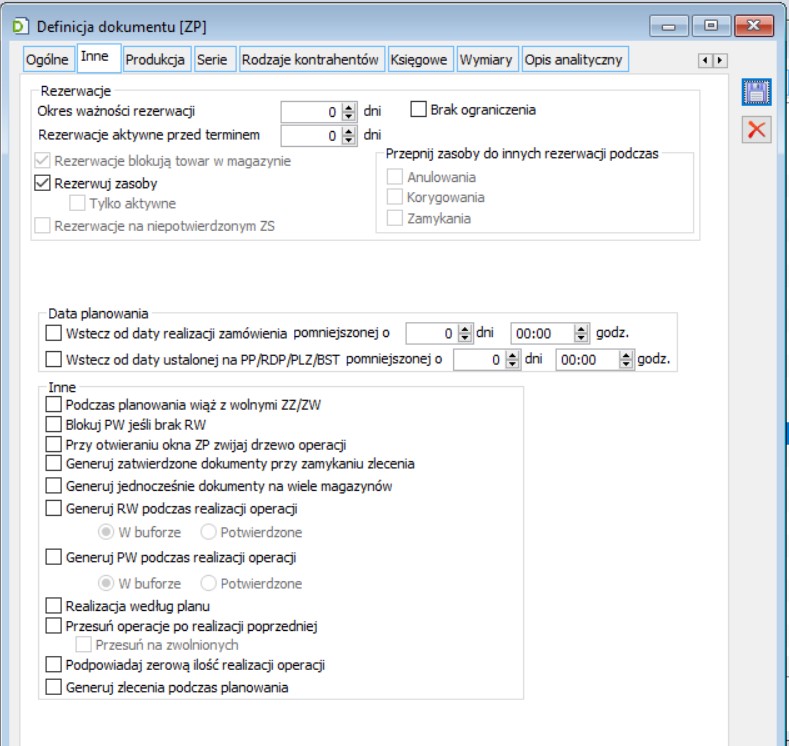
Przy zaznaczonym parametrze, podczas generowania zleceń produkcyjnych z zamówień sprzedaży lub z zamówień wewnętrznych data w polu: Planować od na pozycji zlecenia będzie datą realizacji odpowiedniej pozycji zamówienia pomniejszoną o ewentualną ilość dni i godzin, zadeklarowaną na definicji dokumentu ZP. Dodatkowo na takiej pozycji ZP zaznaczany będzie automatycznie parametr: Wstecz:
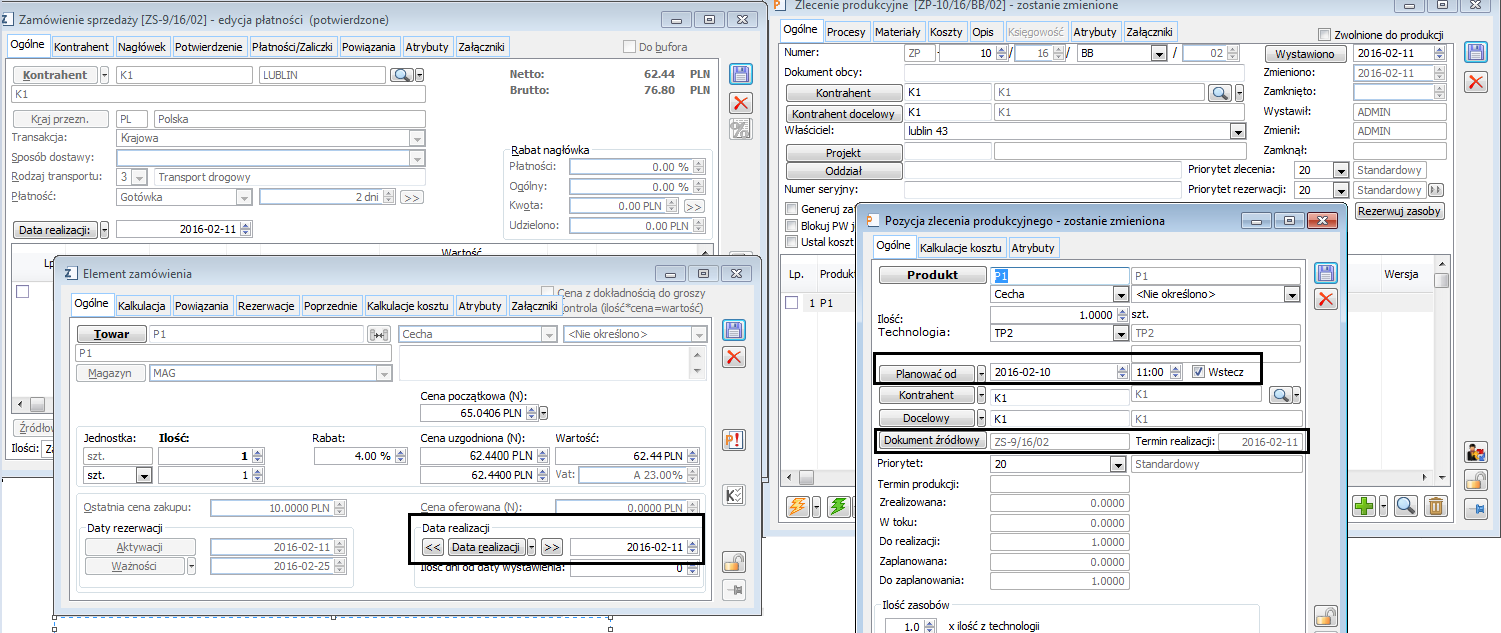
Uwaga: Analogiczna funkcjonalność została obsłużona również dla dokumentów HPR (generowanych z ZS). Uwaga: W przypadku, gdy na elemencie zamówienia data realizacji jest nieokreślona, wówczas na pozycji ZP generowanego z tego zamówienia data rozpoczęcia planowania ustawiana jest jako „Planuj od teraz”. Na wzór istniejącej już funkcjonalności ustawiania, na elemencie dokumentu ZP, daty planowania jako terminu realizacji odpowiedniego elementu zamówienia, z którego wygenerowano ZP, została w systemie wprowadzona możliwość automatycznego podpowiadania na dokumencie ZP daty planowania, jako odpowiedniego terminu z dokumentów: PLZ, PP lub BST. Parametr Wstecz od daty ustalonej na PP/PLZ/BST. Sekcja Inne: Podczas planowania wiąż z wolnymi ZZ/ZW – zaznaczenie tego parametru decyduje o tym, że podczas planowania dowolną metodą sprawdzane będą dodatkowe warunki i funkcje wiążące wolne elementy zamówień zakupu i wewnętrznych ze zleceniami produkcyjnymi. Blokuj PW jeśli brak RW – funkcjonalność umożliwiająca opcjonalną blokadę generowania dokumentu PW ze zlecenia w przypadku, gdy nie wygenerowano i zatwierdzono dokumenty RW. Parametr odznaczony nie powoduje zmian w stosunku do dotychczasowej funkcjonalności. Zaznaczenie parametru będzie skutkowało tym, że dokument PW będzie generowany wyłącznie wtedy, gdy zostanie wygenerowany i zatwierdzony dokument RW w ramach operacji na ZP. Przy otwieraniu okna ZP zwijaj drzewo operacji – parametr umożliwia zaczytywanie przy otwieraniu zakładki tylko części danych, co powinno przyspieszyć otwieranie zakładki. Skutkiem ubocznym może być zwolnienie działania filtrowania przed pierwszym rozwinięciem zwiniętych gałęziach operacji. Przy dodawaniu nowego centrum, domyślnie przenoszone są ustawienie parametru z centrum nadrzędnego z możliwością zmiany na centrum podrzędnym. W przypadku zaznaczonego parametru, przy otwieraniu zakładki: Procesy na dokumencie ZP, zostaną wczytane na zakładkę: Procesy, wyłącznie procesy wraz z operacjami planowanymi. Dla operacji planowanych wyświetlany jest plus umożliwiający rozwinięcie szczegółów operacji. Po rozwinięciu operacji doczytywane są szczegóły operacji. W przypadku, gdy dla zakładki: Procesy, uruchomione zostanie filtrowanie, system doczytanie do operacji pozostałe dane, aby umożliwić filtrowanie. Analogiczne zmiany jak na definicji dokumentu zlecenia produkcyjnego, zostały wprowadzone w definicji dokumentu harmonogramu projektu z wyjątkiem: Zamiast nazwy parametru: „Przy otwieraniu okna ZP zwijaj drzewo operacji”, na harmonogramie dodano parametr: „Przy otwieraniu okna HPR zwijaj drzewo operacji”. Jego działanie zostało obsłużone w analogiczny sposób jak na ZP. Generuj zatwierdzone dokumenty przy zamykaniu zlecenia – parametr, który decyduje o ustawieniu domyślnym na dokumencie Zlecenia produkcyjnego na zakładce Ogólne. Przy zaznaczonym parametrze, podczas zamykania zlecenia zostaną wygenerowane i zatwierdzone wszystkie dokumenty, których brakuje do zamknięcia zlecenia. Dodatkowo przy zaznaczonym parametrze, przy zamykaniu zlecenia, jeśli zostaną spełnione inne warunki do wygenerowania dokumentu PWK, to dokument taki będzie zawsze automatycznie wygenerowany i zatwierdzony. Generuj RW podczas realizacji operacji/ Generuj PW podczas realizacji operacji –możliwość automatycznego generowania dokumentów RW/PW, podczas wykonywania realizacji operacji. Dokumnety generowane w tle. Jeśli wykonywanych będzie jednocześnie wiele realizacji operacji, wówczas generowany będzie jeden zbiorczy dokument RW/PW do tych realizacji, o ile inne ustawienia systemu będą na to pozwalały. Mozliwośc generowania dokumentu do bufora lub potwierdzonego. Realizacja wg planu – parametr decydujący o ustawieniu domyślnym na dokumencie ZP, dotyczy realizacji zlecenia produkcyjnego na podstawie informacji zawartych na zaplanowanym zleceniu (do wersji 2015.1 Systemu Comarch ERP XL realizacja zlecenia odbywała się zawsze na podstawie informacji zawartych w technologii). Parametr obsługuje tylko surowce, czyli przykładowo na zaplanowanym zleceniu produkcyjnym po usunięciu jednego z surowców i zrealizowaniu operacji, danego surowca nie będzie. Na definicji dokumentu zlecenia produkcyjnego, na zakładce: Opis analityczny, udostępniona jest data wystawienia i zamknięcia zlecenia produkcyjnego z domyślnym ustawieniem na datę zamknięcia. Ustawienie to jest przenoszone na zlecenie produkcyjne. Przesuń operacje po realizacji poprzedniej– zaznaczenie parametru umożliwi automatyczne dostosowanie planu do realizacji/ przesunięcie terminów kolejnych operacji planowanych po rejestracji wcześniejszej lub późniejszej realizacji operacji poprzedniej. Przesunięcie to odbywa się automatycznie, co oznacza, że sama rejestracja wykonania operacji w terminie innym, niż planowany, powoduje przesuniecie terminów planowanych operacji następnych. Przesunięte zostaną te operacje, które korzystają z półproduktów wytworzonych za pomocą zarejestrowanej realizacji oraz operacje następne po tych operacjach. Przesuń na zwolnionych– po zaznaczeniu parametru przeplanowaniu mogą podlegać również operacje zwolnione do produkcji. Podpowiadaj zerową ilość realizacji operacji – po zaznaczeniu parametru, podczas uruchamiania, kończenia, wykonywania realizacji operacji wszystkimi metodami, dostępnymi w systemie (oprócz opcji: Realizuj etap) domyślnie podpowiadana będzie zerowa ilość realizacji. Wyjątkiem będzie sytuacja, gdy uruchomiono operację i na tej operacji wprowadzono ilość > 0, w takiej sytuacji, podczas kończenia uruchomionej realizacji, podpowiadana będzie ilość wynikająca z realizacji uruchomionej. Generuj zlecenia podczas planowania – po zaznaczeniu parametru podczas planowania zlecenia, jeżeli potrzebne będzie więcej niż jeden proces, każdy proces będzie się znajdował na osobnym zleceniu produkcyjnym. Na jednym zleceniu znajdować się będą procesy prowadzące do wytworzenia tego samego wyrobu z tej samej technologii. Jeśli Plan produkcji przeliczany jest: Wg dokumentów, Wg terminu, lub Wg okresu MRP, to przy zaznaczonym parametrze Wstecz od daty ustalonej na PP/PLZ/BST, na pozycji ZP ustawiona zostanie data planowania wstecz, jako odpowiednia data z kolumny: Termin, zarówno w przypadku generowania ZP z sekcji: Produkty, jak również w przypadku generowania ZP z sekcji: Materiały: Jeśli Plan produkcji przeliczany jest: Wg okresu, wówczas przy zaznaczonym parametrze Wstecz od daty ustalonej na PP/PLZ/BST, podczas generowania ZP z PP, z sekcji: Produkty, dostępny jest dodatkowy parametr: Planowanie zlecenia na początek okresu planistycznego, który decyduje o tym, czy datą planowania wstecz na pozycji ZP ma być początek, czy koniec okresu, pomniejszony o ewentualną ilość dni i godzin, określone na def. PP. Natomiast, jeśli ZP generowane jest z sekcji: Materiały, to datą planowania wstecz będzie odpowiedni termin, z kolumny termin, pomniejszony o ew. ilość dni i godzin. Jeśli parametr Wstecz od daty ustalonej na PP/PLZ/BST będzie zaznaczony na definicji dokumentu ZP, wówczas, podczas generowania ZP z PLZ, datą planowania wstecz na elemencie ZP będzie domyślna data końcowa okresu, ustawionego dla danej pozycji na dokumencie PLZ, pomniejszona o ewentualną ilość dni i godzin, określoną na definicji ZP: Jeśli parametr Wstecz od daty ustalonej na PP/PLZ/BST będzie zaznaczony na definicji dokumentu ZP, wówczas, podczas generowania ZP z BST, datą planowania wstecz na elemencie ZP będzie domyślna data dostawy z BST, pomniejszona o ilość dni i godzin, określoną na definicji dokumentu ZP: BST- Generowanie ZP- Przy zaznaczonym parametrze, data planowania wstecz na pozycji ZP Na definicji dokumentu Zlecenia produkcyjnego na zakładce Planowanie znajduje się obszar: Dostępne metody planowania. Zaznaczenie poszczególnych pozycji spowoduje możliwość korzystania z nich na Zleceniu produkcyjnym. Pozostałe pozycje zostaną zablokowane dla Operatorów z danego centrum. Istnieje możliwość ustawienia planowania domyślnego za pomocą przycisku Sekcja Domyślny sposób realizacji operacji: Uruchamianie realizacji- istnieje możliwość wybrania domyślnego sposobu realizacji na ZP pod przyciskiem Rejestrowanie realizacji – istnieje możliwość wyboru sposobu realizacji na ZP pod przyciskiem Istnieje możliwość ustawienia parametrów związanych z planowaniem zgrubnym: Obszar „Automatyczne przeplanowanie zleceń o niższym priorytecie” umożliwia wybór opcji przeplanowywania zleceń: Na liście znajdują się zlecenia produkcyjne zarejestrowane w systemie. Z poziomu okna można generować zlecenia, otwierać je do podglądu i edycji oraz usuwać. Ponadto, na liście znajdują się funkcje, które umożliwiają planowanie i realizację zleceń. W oknie wyświetlane są dane kontrahenta, kontrahenta docelowego (o ile został zaznaczony parametr w konfiguracji: Pokazuj kontrahenta docelowego), data wystawienia i zamknięcia zlecenia oraz status, czyli stan jego realizacji. Okno podzielone jest na dwie zakładki, które umożliwiają wyświetlenie wszystkich zarejestrowanych zleceń (zakładka: Wg daty) lub tych, które zostały wygenerowane przez wybranego operatora (zakładka: Wg operatora). Wyświetlone zlecenia można sortować, opcja udostępniona jest w kolumnach: Informacje na liście wskazują numer dokumentu, kontrahenta i numer dokumentu obcego, datę wystawienia i zamknięcia zlecenia, produkt (czyli pozycje zlecenia produkcyjnego z zakładki: Ogólne, ZP).), jego status, czy zlecenie jest zwolnione do produkcji, a także projekt, w ramach którego realizowane jest zlecenie. Dla Listy Zleceń produkcyjnych jest możliwy eksport danych do arkusza kalkulacyjnego W oknie znajdują się pola i funkcje: Idź do (tylko na zakładce: Wg daty) – funkcja umożliwia odnalezienie na liście zlecenia produkcyjnego po wprowadzeniu numeru zlecenia i naciśnięciu przycisku: Właściciel – funkcja umożliwia zawężenie listy zleceń według centrum, w którym zostały one wygenerowane. Lista za – funkcja umożliwia zawężenie listy wyświetlanych zleceń według okresu, w którym zostały one wygenerowane. Pokaż status realizacji – funkcja umożliwiająca wyświetlenie bądź ukrycie statusu realizacji zleceń. Po zaznaczeniu parametru dostępny jest również filtr, który umożliwia zawężanie zleceń do wybranego rodzaju statusu realizacji. Filtr zawiera następujące opcje do wyboru: Wszystkie, Zgrubnie, Zaplanowane, Zrealizowane, Rozliczono, Do zamknięcia, Zamknięte. W filtrze nie są uwzględnione procenty statusów, czyli filtrujemy wszystkie rozliczone, albo wszystkie zaplanowane, niezależnie od tego w ilu procentach są rozliczone lub zaplanowane. Operator (tylko na zakładce: Wg operatora) – funkcja umożliwia zawężenie listy wyświetlanych zleceń do wygenerowanych przez wybranego operatora. Produkty – funkcja umożliwiająca wyświetlenie bądź ukrycie kolumny z kodem produktu. Możliwe jest również wskazanie konkretnego kodu produktu, uwzględnione również zostaną te zlecenia na których znajdują się zaplanowane półprodukty zgodne z kodem produktu wskazanym w filtrze Wyświetlaj– umożliwia filtrowanie zleceń ze względu na stan. Możliwe do wyboru opcje: Wszystkie/Zwolnione do produkcji/Niezwolnione do produkcji. Czynności te wykonywane będą dla wszystkich zleceń, które zostały zaznaczone na liście (przy których został postawiony znak: Z poziomu listy zleceń dostępne jest funkcja: Historia kontrahenta. Od wersji 2013.4 Lista zleceń produkcyjnych została rozbudowana. Za pomocą przycisku Raport wykonania Dla materiałów rezerwacje pochodzące z operacji zaplanowanych, materiały pochodzące z realizacji operacji, o ile nie są powiązane na całość z zatwierdzonym dokumentem handlowym (RW). Na zakładce Materiały udostępniono parametr, który decyduje o tym, czy na ZP mają zostać przeniesione tylko te materiały dla których występuje brak, czy też wszystkie materiały: Jeśli ww. parametr będzie zaznaczony, wówczas na ZP generowanym z ZP przeniesione zostaną tylko te spośród zaznaczonych materiałów, dla których Brak>0 Generowanie ZP tylko na materiały z technologią W oknie optymalizacyjnym, wyświetlanym podczas generowania ZP z zakładki: Materiały, wprowadzono również parametr, który decyduje o tym, czy na ZP mają zostać przeniesione takie materiały, dla których zdefiniowana jest technologia, czy też wszystkie materiały: Jeśli ww. parametr będzie zaznaczony, wówczas, na ZP wygenerowanym z ZP przeniesione zostaną tylko te pozycje, które mają zdefiniowaną przynajmniej jedną zatwierdzoną technologię. Dla produktów: w tabeli Prodlinki nie ma powiązań na pełną ilość z ProdZasobami i/lub w ProdLinki są zapisane powiązania na pełną ilość z ProdZasobami, ale te ProdZasoby, nie mają powiązań na pełną ilość z TrasElem zatwierdzonych dokumentów PW Dla produktów ubocznych: Dla półproduktów wchodzących: W przypadku, gdy półprodukt wchodzący jest zamiennikiem, czyli został zaplanowany w sytuacji, gdy brak jest materiału podstawowego, wtedy wyświetlamy ilości dotyczące półproduktu w kolumnach tak, jak w przypadku, gdy półprodukt jest materiałem podstawowym. Jeśli półprodukt wyświetlany na zakładce: Półprodukty wchodzące, jest zamiennikiem, wtedy wyświetlany jest jego kod (wartość w kolumnie Półprodukt/Kod) w kolorze niebieskim. Na zakładce półprodukty wchodzące dodano przycisk W przypadku, gdy zlecenie zostało wygenerowane dla półproduktów, na które zabrakło ilości do wygenerowania, wówczas pojawi się stosowny komunikat i ZP nie zostanie wygenerowane. W przypadku, gdy do generowania ZP zaznaczono wiele półproduktów – takich, na których jest ilość do wygenerowania i takie, dla których brak jest tej ilości, wówczas wyświetlany jest najpierw log informujący o braku ilości, po czym generowane jest ZP na te półprodukty, dla których ilość w kolumnie: Ilość/Brak związanych jest większa niż 0. Przy generowaniu ZP sprawdzane jest w pierwszej kolejności, czy półprodukt posiada kartę magazynową, a dopiero jeśli ma, wówczas sprawdzane jest, czy jest ilość na jaką można wygenerować zlecenie. Zatem w przypadku, gdy zlecenie jest wygenerowane dla półproduktu, który nie posiada karty magazynowej i który nie posiada ilości, na którą można wygenerować ZP, wtedy po sprawdzeniu, że półprodukt nie posiada karty magazynowej przerywane generowanie zlecenia na ten półprodukt. W przypadku, gdy zlecenie zostało wygenerowane na ten sam półprodukt (czyli o tym samym PZA_TechnologiaZasob), będący wyświetlony na wielu różnych pozycjach, wówczas po wygenerowaniu zlecenia produkcyjnego na ten półprodukt, będzie grupowany na tym zleceniu. Po wygenerowaniu zlecenia na półprodukty, nie jest tworzone powiązanie między wygenerowanym zleceniem, a półproduktami, dla których zlecenie zostało wygenerowane. Dla półproduktów wychodzących, czyli takich, które planujemy wytworzyć i które wytworzyliśmy: W przypadku półproduktów posiadających kartę magazynową – wyświetlane są zlecenia, na którym zaznaczony został półprodukt. Zlecenie otwierane jest na zakładce: Materiały, z wyfiltrowanym półproduktem (czyli tak samo, jak w przypadku edycji zaznaczonej pozycji z poziomu zakładki: Materiały lub Produkty). W przypadku półproduktów nie posiadających karty magazynowej – dla takich półproduktów, otwierane jest zlecenie produkcyjne, na zakładce: Procesy, z ustawionym filtrem na kodzie półproduktu. Przykład: Przykład wypełnienia wartości kolumn na liście półproduktów wychodzących: Zaplanowanie zlecenia, które zawiera dwie operacje – na operacji pierwszej zaplanowano wytworzenie 12 szt. półproduktu PP1, które zostały w wyniku planowania powiązane z 12 szt. półproduktu PP1 zaplanowanemu na operacji drugiej, wykorzystującej ten półprodukt, Zostanie zarejestrowana realizacja w całości operacji pierwszej, Zostanie zarejestrowana realizacja w całości operacji drugiej.
Okno wywoływane jest z poziomu listy zleceń produkcyjnych po naciśnięciu przycisku: Jego funkcjonalność umożliwia wskazanie przez Użytkownika kolejności, w jakiej planowane/przeplanowane będą zlecenia produkcyjne. Kolejność tą ustawia się za pomocą przycisków: Modyfikacja zleceń wyświetlonych w oknie, dla których ustalana będzie kolejności odbywa się za pomocą przycisków: Na liście zleceń produkcyjnych, w sekcji rozwijanej, na zakładce: Materiały, dodano filtr: Pokaż, umożliwiający filtrowanie materiałów na materiały i na półprodukty. Udostępniono trzy opcje: Zwiększenie ilości kolumn i możliwość dodawania swoich powoduje, że na listach mamy coraz więcej informacji. Aby łatwiej było je odnaleźć wprowadzone zostało kolorowanie wybranych kolumn. Zmiany takie zostały wprowadzone na liście zleceń – w obszarze głównym listy oraz na sekcjach, na których wyświetlane są listy pomocnicze do zleceń – a więc materiałów, produktów i półproduktów. Wyróżnione zostały kolumny, które stanowią pewną grupę – np. na liście zleceń są to kolumny na kod i nazwę produktu, natomiast na liście półproduktów są to kolumny z kodem i nazwą produktu oraz kolumny w grupie: Ilość półproduktów do wykorzystania. Okno: Kolejka zleceń, umożliwia układanie kolejności, w jakiej zostaną zaplanowane zlecenia produkcyjne. Dotychczas, kolejność taką ustalało się jedynie ręcznie, zmieniając Lp. danego zlecenia na liście – za pomocą przycisków: Definicja kolejki zawiera zapytanie SQL, wg którego zostanie ustawiona kolejka zleceń. Na poniższym rysunku pokazano przykładowe zapytanie, które ustawi zlecenia, wg daty ich wystawienia. Wyniki zapytania można ograniczyć do listy zleceń, które zostały przekazane do okna (np. poprzez zaznaczenie na liście zleceń i wywołanie okna kolejkowania) dopisując w warunku WHERE frazę: {FiltrSQL}, która w momencie wywołania zapytania będzie zastępowana przez frazę: PZL_Id in (x,y …) gdzie x,y, … to identyfikatory zleceń, dla których uruchomione zostało okno. Podobnie, jak w przypadku dodawaniu własnych kolumn, poza frazą {filtrsql} można użyć również: Należy pamiętać, że jeśli takie ograniczenie nie zostanie wprowadzone, symulowana kolejka obejmie wszystkie aktywne zlecenia, a nie tylko te, które będą wyświetlone w górnej części okna: Kolejka zleceń. Po wybraniu definicji kolejki, w sekcji: Ustaw nową kolejkę, zostanie uaktywniona opcja: Uruchom symulację kolejki. Naciśnięcie tego przycisku spowoduje, że w tej sekcji zostanie wyświetlona lista zleceń ułożona w kolejce wynikającej z uruchomienia zapytania SQL, zawartego w wybranej definicji. Ustawiona w ten sposób lista zleceń to propozycja kolejki. Porównanie LP zleceń symulowanej (wyświetlonej w dolnej sekcji okna) w stosunku do obecnej (a więc wyświetlonej w górnej sekcji okna) wyświetlone jest w kolumnach: Nowe Lp. i Poprzednie Lp. Strzałki wyświetlone na lewo od kolumny: Dokument, oznaczają: Porównanie kolejki symulowanej (wyświetlonej w dolnej części okna) i bieżącej (wyświetlonej w górnej części okna), umożliwia analizę zmian, jakie zajdą w kolejności planowanych zleceń.Jeśli symulowana kolejka zostanie zatwierdzona przez Użytkownika, należy nacisnąć przycisk: Na zakładce określa się produkt, będący przedmiotem zlecenia oraz podstawowe dane nagłówkowe zlecenia: Numer – numer dokumentu zlecenia produkcyjnego. Domyślnie podpowiadany będzie kolejny numer dokumentu, jednak podlega on modyfikacji, podobnie jak seria dokumentu. Kontrahent – kontrahent, na którego generowane jest zlecenie. Podanie kontrahenta nie jest wymagane dla zarejestrowania zlecenia. Od wersji 11.0 Systemu Comarch ERP XL udostępniono funkcjonalność polegającą na wystawienie zlecenia produkcyjnego (ZP) dla więcej niż jednego kontrahenta. Dotychczas na ZP było możliwe przypisanie jednego wskazanego kontrahenta dla kilku rożnych zamówień sprzedaży. Właściciel – w polu wprowadzane jest domyślnie centrum, w którym wystawiane jest zlecenie produkcyjne. Podczas planowania zlecenia, kontrolowane są uprawnienia centrum do magazynów, które przypisano do zasobów zdefiniowanych w technologii. Na zleceniu uwzględniane będą tylko te magazyny, które znajdują się na definicji dokumentu RW dla centrum (dla zasobu-surowca) i te, które znajdują się na definicji dokumentu PW (dla zasobu-produktu). Data wystawienia – data wygenerowanie zlecenia produkcyjnego. Domyślnie podpowiadana jest data bieżąca, jednak podlega ona modyfikacji (również po wystawieniu zlecenia). Oddział – oddział, w którym realizowane jest zlecenie. Należy jednak pamiętać, że wskazanie oddziału w tym polu ma charakter pomocniczy: na planowanych procesach i operacjach domyślnie będą podpowiadane oddziały: Dopiero, gdy na technologii nie ma wskazanego oddziału, na procesy i operacje wprowadzany jest oddział wybrany na zleceniu. Projekt – zlecenie może być opisane za pomocą projektu wybieranego ze struktury projektów. Podczas wybierania projektu na zlecenie, który ma wskazanego kontrahenta pojawi się zapytanie: ‘Na przypisywanym projekcie znajduje się kontrahent. Czy wprowadzić go na bieżące zlecenie?’ Po wybraniu odpowiedzi TAK, zostanie przypisany kontrahent z projektu na zlecenie. Po wybraniu odpowiedzi NIE, zostanie przypisany projekt bez przypisanego do niego kontrahenta. Numer seryjny – w polu można wprowadzić numer seryjny, który zostanie przepisany na produkt, uzyskany w wyniku realizacji procesu produkcyjnego, pod warunkiem, że na produkcie w technologii jako wartość cechy ustawiona zostanie wartość <numer seryjny>. Odchylenia – Koszty operacji, zasobu i surowca są rozbijane na otrzymane w wyniku realizacji zlecenia produkty. Koszty, które nie zostały uwzględnione w tym rozbiciu wyświetlone są w części: Odchylenia Wystawiono, Zmieniono, Zamknięto – w polach wprowadzane są daty wykonania odpowiednich operacji na dokumencie. Wystawił, Zmienił, Zamknął – w polach wprowadzany jest identyfikator operatora, który wykonał odpowiednie operacje na zleceniu. Priorytet zlecenia – domyślna wartość priorytet pobierana jest ze Słownika kategorii, definiowanego z poziomu modułu: Administrator (więcej informacji w dokumentacji modułu: Administrator). Możliwa jest jednak zmiana priorytetu dla konkretnego zlecenia. Priorytet ze zlecenia będzie przepisywany na procesy i operacje planowane na zleceniu. Priorytet rezerwacji – priorytet tu określony będzie przepisywany na proces planowany na zleceniu. Generuj zatwierdzone dokumenty przy zamykaniu ZP– parametr, który decyduje o ustawieniu domyślnym na dokumencie Zlecenia produkcyjnego na zakładce Ogólne. Przy zaznaczonym parametrze, podczas zamykania zlecenia zostaną wygenerowane i zatwierdzone wszystkie dokumenty, których brakuje do zamknięcia zlecenia. Generuj jednocześnie dokumenty na wiele magazynów– parametr umożliwia automatyczne generowanie dokumentów na kilka magazynów. Blokuj PW jeśli brak RW – funkcjonalność polegająca na blokadzie generowania dokumentu PW dotyczącego produktów jeśli nie wygenerowano dla niego dokumentu RW na surowce z kartą magazynową na ilość wynikającą z realizacji operacji. Ustal koszt przy zamykaniu zlecenia – domyślne ustawienie parametru przenoszone jest z definicji dokumentu zlecenia produkcyjnego. Przy zaznaczonym parametrze, koszt na produktach zostanie ustalony dopiero wtedy, gdy zostanie zamknięte zlecenie. Przy odznaczonym, ustalenie kosztu nastąpi wtedy, gdy zostanie ustalony koszt na surowcach tej samej realizacji, w której uczestniczy produkt. W przypadku ustalenia kosztu przed zamknięciem zlecenia i wygenerowaniu dokumentu PW na ten produkt z ustaloną wartością dostawy, możliwe jest nadal przypisywanie kosztów do takiego produktu, rozbijanie na ten produkt kosztów itd. Jeśli po kolejnym rozliczeniu, koszt takiego produktu będzie inny niż wynosi wartość produktu na spiętym PW, wtedy możliwe będzie wygenerowanie do takiego PW korekty kosztu na różnicę. Generowanie zlecenia podczas planowania – domyślne zaznaczenie parametru przenoszone jest z definicji dokumentu zlecenia produkcyjnego (parametr: Generowanie zlecenia podczas planowania, na zakładce: Inne). Przy zaznaczonym parametrze sprawdzane będzie czy przy planowaniu zlecenia konieczne jest wygenerowanie więcej niż jednego procesu, aby wytworzyć półprodukty potrzebne do wyrobu. Jeżeli potrzebne będzie więcej niż jeden proces, każdy proces będzie się znajdował na osobnym zleceniu produkcyjnym. Na jednym zleceniu będą procesy prowadzące do wytworzenia tego samego wyrobu z tej samej technologii. Przykład : Zdefiniowane są trzy technologie: T1: Operacja: 10 Surowiec: M1 = 1 szt. Produkt: PP1 = 1 szt. T2: Operacja: 20 Surowiec: PP1 (z T1) = 1 szt. Produkt: PP2 – 1 szt. T3 Operacja: 30 Surowiec: PP1 (z T1) = 1 szt. Surowiec: PP2 z (z T2) = 1 szt. Produkt: WG1 = 1 szt. Na zleceniu ZP 1, planowana jest produkcja WG1 w ilości 1 szt. Ilość procesów do zaplanowania: 1 szt. procesu T3 (Operacja: 30). 1 szt. procesu: T2 (Operacja: 20). 2 szt. procesu T1 (Operacja: 10). Podczas planowania zlecenia zostaną wygenerowane: ZP – 2, na produkt PP2 w ilości 1 szt. i zostanie zaplanowany proces T2 ZP – 3, na produkt PP1 w ilości 2 szt. i zostanie zaplanowany proces, umożliwiający wytworzenie 2 szt. PP1. Rezerwuj zasoby – domyślne zaznaczenie parametru przenoszone jest z definicji dokumentu zlecenia produkcyjnego (parametr: Rezerwuj zasoby, na zakładce: Inne). Przy zaznaczonym parametrze, podczas planowania zlecenia produkcyjnego do generowanych rezerwacji będą przypisywane automatycznie zasoby (przy spełnieniu warunków ważności rezerwacji i aktywności rezerwacji przed terminem określanych również na definicji dokumentu zlecenia produkcyjnego). Parametr będzie nieaktywny, jeśli na definicji dokumenty zlecenia produkcyjnego zostaną odznaczone parametry: Rezerwuj zasoby i Rezerwacje blokują towar na magazynie. Należy jednak zauważyć, że odznaczenie tych parametrów na definicji dokumentu zlecenia, w sytuacji, gdy rezerwacje na zleceniu mają już przypisane zasoby, nie zwolni tych zasobów. Stan: Zwolnione do produkcji- Zlecenia oznaczone tym stanem nie podlegają automatycznemu planowaniu ani przeplanowaniu. Ponadto, zasoby dobrane do operacji zaplanowanych na takich zleceniach nie zostaną podmienione. Jeśli zasób jest przypisany do operacji zaplanowanej na zleceniu znajdującym się w stanie: Zwolnione do produkcji, oznacza to, że nie zostanie on zmieniony na tej operacji w wyniku przeplanowania innego zlecenia, nawet jeśli będzie to zlecenie o wyższym priorytecie. Na zleceniu znajdującym się w stanie: Zwolnione do produkcji, nie jest możliwa edycja pozycji zlecenia produkcyjnego – a więc dodanie, modyfikacja oraz usuwanie pozycji zleceń. Możliwa jest natomiast ręczna modyfikacja operacji zaplanowanych – a więc ręczna zmiana terminu realizacji, czy ręczna podmiana zasobów produkcyjnych. Zlecenie może zostać cofnięte ze stanu: Zwolnione do produkcji, co przywraca możliwość edycji zlecenia i możliwości jego przeplanowania. Nowy stan zlecenia umożliwia sprawniejsze zarządzanie zleceniami, wpływa na większą stabilność zaplanowanej produkcji, przeznaczonej do realizacji. Poprzez zmniejszenie liczby zleceń, które będą przeplanowywane, wpływa również na skrócenie czasu przeplanowywania innych zleceń. Edycja checku: Zwolnione do produkcji, możliwa jest niezależnie od tego, czy uruchomiono już realizację zlecenia czy też nie. Zatem warunkami, które powodują, że parametr: Zwolnione do produkcji, będzie zablokowany do edycji będzie to, że: W przypadku, gdy wśród zaznaczonych zleceń będą zlecenia zamknięte i niezamknięte, funkcja będzie aktywna. Jednak po wywołaniu funkcji, dla zleceń, które znajdują się w stanie zamknięte zostanie w logu wyświetlona informacja: „Zlecenie <numer zlecenia> nie zostało zwolnione. Zlecenie jest zamknięte”. Funkcja: Zwolnij do produkcji/Cofnij do produkcji dostępna w menu kontekstowym. Funkcja: Cofnij z produkcji jest funkcją odwrotną do funkcji Zwolnij do produkcji. Czyli jej użycie spowoduje odznaczenie checku: Zwolnione do produkcji na zaznaczonych zleceniach. Funkcja: Cofnij z produkcji zostanie wyszarzona, jeśli na liście zaznaczono jedno zlecenie i to zlecenie nie znajduje się w stanie: Zwolnione do produkcji lub znajduje się w stanie: Zamknięte. W przypadku, gdy zaznaczono wiele zleceń, wśród których są zlecenia, które nie znajdują się w stanie: Zwolnione do produkcji i takie, które są, opcja: Cofnij z produkcji będzie aktywna. W przypadku gdy funkcję uruchomiono dla zleceń znajdujących się w stanie: Zwolnione do produkcji zamknięte lub parametr nie jest zaznaczony, wówczas po jej uruchomieniu pojawi się stosowny komunikat. Realizacja wg planu – parametr dotyczy realizacji zlecenia produkcyjnego na podstawie informacji zawartych na zaplanowanym zleceniu (do wersji 2015.1 Systemu Comarch ERP XL realizacja zlecenia odbywała się zawsze na podstawie informacji zawartych w technologii). Przy zaznaczonym parametrze podczas realizacji zlecenia są więc brane pod uwagę wyłącznie te materiały i wyłącznie w takich ilościach, jakie znalazły się na zaplanowanym zleceniu produkcyjnym. Parametr można edytować do momentu wprowadzenia na zlecenie pierwszej realizacji. W przypadku, gdy zajdzie potrzeba przeplanowania zlecenia produkcyjnego, zaznaczony parametr pozwala na przeplanowanie według danych zawartych na zaplanowanym zleceniu. Przesuń operacje po realizacji poprzedniej- Automatyczne dostosowanie planu do realizacji (tzw. przeplanowanie „w locie”) umożliwia przesunięcie terminów kolejnych operacji planowanych po rejestracji wcześniejszej lub późniejszej realizacji operacji poprzedniej. Przesunięcie to odbywa się automatycznie, co oznacza, że sama rejestracja wykonania operacji w terminie innym, niż planowany, powoduje przesuniecie terminów planowanych operacji następnych. Przesunięte zostaną te operacje, które korzystają z półproduktów wytworzonych za pomocą zarejestrowanej realizacji oraz operacje następne po tych operacjach (również te, które znajdują się na innych zleceniach). Funkcjonalność została udostępniona jako opcjonalna. Aby z niej skorzystać, należy zaznaczyć parametr na zleceniu: Przesuń operacje po realizacji poprzednich. Domyślne ustawienie tego parametru przenosi się z definicji dokumentu zlecenia produkcyjnego. Przesuń na zwolnionych- Przy użyciu tej funkcjonalności przeplanowaniu mogą podlegać również operacje zwolnione do produkcji. Aby po zarejestrowaniu realizacji, przeplanowywane były operacje pochodzące z takich zleceń, należy na takim zleceniu mieć zaznaczony parametr: Przesuń na zwolnionych. Przykład: Zaplanowano wstecz trzy operacje na Maszynę 01, w godzinach: Operacja 10 – godz.: 9-10 Operacja 20 – w godz.: 10-11 Operacja 30 – w godz.: 11-12 Operację 30 rozpoczęto wcześniej – o godzinie 10:45. Wywołanie funkcji Wyszukiwanie nowych terminów spowoduje automatyczne przesunięcie zadań o 15 minut wcześniej, dzięki czemu harmonogram poprzednich operacji będzie wyglądał, jak następuje: Operacja 1- w godz.: 8:45 – 9:45 Operacja 2 – w godz.: 9:45 – 10:45 Na zakładce ‘Ogólne’ ZP dodano funkcjonalność ‘Edit in place’ dzięki której w kolumnach „Produkt”, „Ilość”, „Technologia”, „Klasa” i „Cecha” możliwe będzie edytowanie informacji w tym miejscu, bez konieczności podnoszenia do edycji elementu ZP. Dodatkowo umożliwiono użycie przycisku [Insert] z klawiatury w celu dodania nowej pozycji ZP jeżeli aktywny (zaznaczony na niebiesko) jest wiersz. Dodatkowo umieszczenie kursora na wierszu + ENTER prowadzi do edycji wiersza w pierwszej kolumnie w której możliwa jest edycja EIP tu w polu Produkt. Klawisz Tab przenosi edycję pola do kolejnego w którym istnieje taka możliwość. Wciśnięcie klawisza Enter podczas edycji pola w trybie EIP zapisuje wprowadzone dane, w sytuacji gdy nie odbywa się edycja w trybie EIP naciśnięcie klawisza Enter zapisuje całe okno. W momencie edycji pola w trybie EIP wybranie klawisza ESC cofa wprowadzone zmiany poprzez anulowanie całej akcji EIP w edytowanym polu. Na zakładce Ogólne wprowadzono możliwość sortowania wyświetlonych pozycji na liście, sortowanie dostępne jest w kolumnach: Na liście produktów w kolejnych kolumnach prezentowane są informacje dotyczące pozycji: Na oknie Zlecenia produkcyjnego, zakładka Ogólne dostępny jest filtr oraz konstruktor filtra, umożliwiający szybkie wyszukanie określonej pozycji. Ponadto, na zakładce znajdują się funkcje: Dla elementów zlecenia produkcyjnego, z poziomu zakładki: Ogólne, na pasku narzędzi dostępne są funkcje: Na zakładce Operacje wyświetlana jest płaska lista operacji zaplanowanych. Celem zakładki jest umożliwienie raportowania zadań do wykonania i stopnia ich realizacji w kontekście zlecenia produkcyjnego. Zakładka została podzielona na dwie sekcje, w sekcji Operacje planowane wyświetlane są operacje planowane wraz ze stopniem postępu realizacji operacji, w sekcji Raport wykonania wyświetlane są dane kontekstowe dla operacji zaznaczonej w sekcji: Operacje planowane, dane kontekstowe dotyczą zarejestrowanych realizacji operacji. Analogicznie do zakładek Ogólne i Procesy udostępniono skróty klawiaturowe dla planowania, przeplanowania, realizacji operacji, aktualizacji rezerwacji, rozliczania zlecenia, zamykania/otwierania zlecenia, generowania RW, generowania PW, generowania ZZ i uruchamiania wykresu Gantt’ Operacje planowane W sekcji wyświetlane są zaplanowane operacje znajdujące się na zleceniu produkcyjnym. Operacje wyświetlane są według daty planowanego rozpoczęcia tj. w g kolumny Start, Prezentowane są kolumny: Operacja, Kod i Nazwa – zawierająca kod i nazwę planowanej operacji, jeżeli na dole zakładki zaznaczono parametr ‘Wyświetlaj konflikty’, w sytuacji gdy na operacji występuje konflikt jej kod będzie wyświetlany w kolorze czerwonym. Proces – zawiera kod procesu, w ramach którego zaplanowano operację. Start – prezentuje planowaną datę rozpoczęcia operacji, data wyświetlana jest w kolorze czerwonym, jeżeli minął termin startu. Koniec – prezentuje planowaną datę zakończenia operacji, data wyświetlana jest w kolorze czerwonym, jeżeli termin zakończenia realizacji jest późniejszy niż termin zakończenia operacji planowanej lub zarejestrowano realizację uruchomioną, która nie została zakończona, pomimo że minął termin zakończenia na operacji planowanej. Czas – prezentuje czas realizacji operacji (prezentowany w sekcji Terminy w oknie Operacja – edycja) Ilość – prezentuje ilość zaplanowanej operacji, możliwa jest zmiana ilości planowanej poprzez edycję pola bezpośrednio w kolumnie Ilość. Status – w kolumnie prezentowany jest status danej operacji. Postęp realizacji – w kolumnie prezentowany jest pasek postępu realizacji danej operacji. Pasek wyświetlany jest w kolorze zielonym Procent realizacji – prezentuje wartość liczbową wskazującą w procentach postęp realizacji w stosunku do planu. Dodatkowo po zaznaczeniu w sekcji ‘Wyświetlaj’ parametry Zasoby, Wyroby, Konflikty prezentowane są dodatkowo kolumny: Zasoby – kolumna prezentuje kody zasobów dobranych do zaplanowanej operacji. Wyroby – kolumna prezentuje kody i nazwy półproduktów i produktów wychodzących z danej operacji, w przypadku, gdy wyrobów jest więcej niż jeden ich kody i nazwy wyświetlane są po przecinku. Konflikty – w kolumnie prezentowane są konflikty dla zaplanowanych operacji. W sekcji dostępne są funkcje: Raport wykonania W sekcji prezentowane są realizacje do zaplanowanych operacji zaznaczonych w górnej części zakładki. Prezentowane są kolumny: Operacja (Kod, Nazwa) – wyświetla kod i nazwę realizowanej operacji. Start – w kolumnie prezentowany jest termin startu na realizacji operacji. Koniec – w kolumnie prezentowany jest termin zakończenia realizacji operacji, w przypadku gdy realizacja operacji jeszcze się nie zakończyła kolumna jest pusta. Czas – czas trwania realizacji operacji, dla operacji niezakończonych wyświetlane jest 0m. Ilość – Informacja o ilości danej realizacji. Dodatkowo po zaznaczeniu w sekcji ‘Wyświetlaj’ parametry Zasoby, Wyroby, prezentowane są dodatkowo kolumny: Zasoby – kolumna wyświetla kody zasobów wykorzystanych do realizacji operacji. Wyroby – kolumna prezentuje kody i nazwy półproduktów i produktów wychodzących z danej operacji, w przypadku, gdy wyrobów jest więcej niż jeden ich kody i nazwy wyświetlane są po przecinku. Produkty uboczne – prezentuje kody produktów ubocznych zarejestrowanych w ramach realizacji danej operacji. Proces – zawiera kod procesu, w ramach którego wykonano realizację. Pod listą realizacji udostępniono filtr prosty, który po wpisaniu wartości, sprawdza kolumny Operacja: Kod, Operacja: Nazwa i Proces. Udostępniono również filtr Dostępne są również funkcje: Na zakładce będą wyświetlone (po zaznaczeniu odpowiednich opcji): -zaplanowane procesy produkcyjne (czyli technologie, które wybrano do wytworzenia produktu, określonego na zakładce: Ogólne; wyświetlone ze znakiem: -zaplanowane operacji (wyświetlone ze znakiem -zasoby, których udział został zaplanowany dla operacji (wyświetlone ze znakiem: -realizacje operacji (wyświetlone ze znakiem: -surowce użyte podczas realizacji zlecenia (wyświetlone ze znakiem -półprodukty uzyskane podczas realizacji zlecenia (wyświetlone ze znakiem: -produkty uzyskane podczas realizacji zlecenia (wyświetlone ze znakiem: -surowce będące zamiennikami (wyświetlone ze znakiem: -zasoby, które wzięły udział w realizacji operacji (wyświetlone ze znakiem: -operacje zdefiniowane jako etap (wyświetlone na liście jako: -produkty uboczne ( wyświetlone jako -zabiegi ( Kod oraz nazwa materiału oraz produktów są wyświetlane na podstawie karty towaru (nie na podstawie danych materiału w technologii). Na zakładce, w kolejnych kolumnach wyświetlone są informacje o kodach i nazwach procesów, operacji, realizacji, pobranych zasobów, materiałów (surowców i produktów), ich ilościach, ilościach w jednostkach pomocniczych, terminach rozpoczęcia i zakończenia operacji i ilościach zrealizowanych. Kolumna: Konflikt, prezentuje informacje o konfliktach, które stanowią przeszkodę w terminowej realizacji produkcji. Możliwe jest jej ukrycie, poprzez odznaczenie parametru: Wyświetlaj konflikty. W kolumnie: Koszt, wyświetlone są wszystkie koszty, przypisane do produkcji w ramach takich kategorii, które mają zaznaczony w swojej definicji parametr: Uwzględniaj w wartości produktu na PW. Zablokowane Zasoby zostaną wyświetlone w kolorze niebieskim (po zaznaczeniu na gnieździe roboczym parametru Blokuj po zaplanowaniu). W kolumnie Zrealizowano ilość dla rezerwacji niezasobowych wyświetla się jako ilość: 0 w kolorze zielonym. Natomiast ilość na jaką został zarezerwowany towar dla rezerwacji zasobowych wyświetla się w kolorze czarnym. Na zakładce: Procesy, na ZP wprowadzono informację o terminach, na jakie podzielona została operacja. Jeśli do operacji na zleceniu dobrane zostaną zasoby produkcyjne, wówczas w kolumnach: Termin rozpoczęcia i Termin zakończenia na zakładce: Procesy, na ZP, obok tych zasobów, prezentowane będą odpowiednie terminy, w jakich poszczególne zasoby wykonują daną operację. Zostały dodane pola, w których prezentowane są informacje na temat: Planowanego czasu trwania zlecenia – liczony od terminu: ‘Od’ na najwcześniej operacji na zleceniu, do terminu ‘Do’, najpóźniejszej operacji na zleceniu. Łącznego czasu operacji na zleceniu – łączny czas wszystkich operacji na zleceniu. W przypadku, gdy operacja planowana jest na wiele terminów, liczona jest suma terminów. Na zleceniu produkcyjnym, na zakładce: procesy została dodana kolumna: Zamiennik do, w której wyświetlana jest informacja, dla jakiego materiału jest zamiennikiem pozycja wyświetlona na tej zakładce. Na zakładce udostępniono filtr prosty, filtrowane są zarówno obiekty nadrzędne jak i podrzędne na drzewie procesu. Na zakładce: Procesy są udostępnione funkcje, służące do filtrowania pozycji znajdujących się na zleceniu produkcyjnym: Możliwe jest również połączenie kilku filtrów na raz np. Surowce + Półprodukty, Półprodukty + Produkty, Surowce + Półprodukty + Produkty. Na zakładce znajdują się pola i funkcje: Planować od – domyślnie produkcja zostanie zaplanowana od bieżącego momentu (opcja: Planuj od teraz), jednak za pomocą przycisku: Planować od można wskazać konkretną datę, od której ma zostać uruchomione planowanie zlecenia. Wstecz – zaznaczenie tej opcji umożliwia zaplanowanie produkcji tak, aby produkt był gotowy na konkretny termin, np. produkt o krótkim terminie ważności ma być wyprodukowany na konkretny dzień (1 września), w którym trafi do odbiorcy. Zaznaczenie parametru umożliwi zaplanowanie „wstecz” produkcji tego produktu od 1 września. Kolejność materiałów wg technologii – zaznaczenie parametru umożliwia wyświetlanie materiałów na zleceniu w takiej samej kolejności, w jakiej zostały one ułożone na technologii. Pozostawienie odznaczonego parametru spowoduje wyświetlenie materiałów według porządku alfabetycznego. Wyświetlaj konflikty – po zaznaczeniu parametru, na zleceniu zostanie wyświetlona kolumna: Konflikt, w której wyświetlane będą znalezione konflikty. „1 Brak surowców” – Oznacza brak surowców we wskazanym magazynie do realizacji zlecenia. W planowaniu zgrubnym nie jest uwzględniany konflikt: Brak półproduktów (surowców z innych operacji). „2 Brak dostaw” – Oznacza brak dostaw do realizacji zlecenia. W planowaniu zgrubnym konflikt nie jest uwzględniany. Brak rezerwacji nie jest konfliktem. Podczas aktualizacji rezerwacji dla operacji zaplanowanych zgrubnie, uwzględniany jest parametr: Rezerwuj zasoby, na definicji dokumentu. „2A Brak dostaw” – Ten konflikt pojawia się w sytuacji, gdy brak jest dostaw na materiał, jednak istnieją zarejestrowane zamówienia zakupu lub zamówienie wewnętrzne na ten materiał. „2B Brak dostaw” – Konflikt pojawia się w sytuacji, gdy operacja planowana jest powiązana z zamówieniem zakupu lub zamówieniem wewnętrznym, a data realizacji na powiązanym elemencie ZZ/ZW późniejsza niż termin rozpoczęcia operacji. Opóźnienie z ZZ lub ZW uniemożliwia rozpoczęcie operacji planowanej w terminie. „3 Brak zasobów” – Oznacza brak zasobów do realizacji zlecenia. Komunikat uwzględnia rodzaj planowania i parametr na gnieździe roboczym – czyli np. podczas planowania szczegółowego wyświetla się konflikt w przypadku braku zasobów przypisanych do gniazda roboczego z zaznaczonym parametrem: Planowana – szczegółowo, podczas planowania zgrubnego wyświetla się konflikt w przypadku braku zasobów przypisanych do gniazda roboczego z zaznaczonym parametrem: Planowana – zgrubnie. „4A Zasoby w innych operacjach” – przy planowaniu zgrubnym konflikt nie jest uwzględniony, pojawia się w sytuacji, gdy zasób został zaplanowany w innym zleceniu w tym samym czasie. „4B Zasoby w innych zadaniach” – Konflikt pojawia się w sytuacji, gdy zasób został zaplanowany w tym samym czasie do innych zadań niż zadania produkcyjne (czyli do zadań wynikających z terminarza lub ze zleceń serwisowych). „5 Ilość min/max gniazda roboczego” – Konflikt wystąpi w sytuacji, gdy zasób zostanie zaplanowany do realizacji zlecenia, na którym ilość jest mniejsza od ilości minimalnej lub większa od ilości maksymalnej zdefiniowanej w oknie: Edycja gniazda roboczego dla zasobu. „6 Czas zmiany gniazda roboczego” – Konflikt zostanie wyświetlony w sytuacji, gdy zostanie naruszony czas, potrzebny na zmianę gniazda roboczego (przezbrojenie) dla zasobu między operacjami. Przykład: Do operacji 1 i operacji 2 został dobrany ten zasób, jednak w operacji 1 zasób pracuje jako gniazdo robocze: Gniazdo 1, a w operacji 2 pracuje jako Gniazdo 2. Czas potrzebny na przezbrojenie zasobu z Gniazda 1 na Gniazdo 2 wynosi 2 godziny. W przypadku, gdy okres ten w wyniku planowania będzie mniejszy niż 2 godziny, wtedy pojawi się konflikt 6. „7 Brak realizacji operacji po terminie” – Konflikt uwzględniony w każdym rodzaju planowania, pojawia się w sytuacji, gdy minął zaplanowany termin realizacji zlecenia. „8A Zasoby nie są dostępne w tym okresie” – Konflikt pojawi się w sytuacji, gdy dla Zasobu wskazanego na technologii w okresie jego niedostępności zostanie zaplanowane wykonanie jakiejś operacji. W tej sytuacji System oprócz wyświetlenia komunikatu, zaplanuje wykonanie operacji w pierwszym okresie dostępności zasobu. „8B Okres niedostępny wg okresów wspólnych firmy” – Konflikt pojawia się w sytuacji, gdy na ustalony w okresach wspólnych okres niedostępności będzie planowana realizacja zlecenia. „9 Zasoby w operacjach o niższym priorytecie” – Oznacza, że zasoby zostały przydzielone do zlecenia o wyższym priorytecie. W planowaniu zgrubnym nie uwzględnia się tego konfliktu. „10 Operacja zaplanowana po wyznaczonym terminie” – Konflikt pojawi się w sytuacji, w której ze względu na inne zlecenia, planowanie na konkretny termin będzie musiało mieć przesunięty plan realizacji na później. „11 Niezgodne terminy zakończenia/rozpoczęcia operacji” – Konflikt powstaje w sytuacji, gdy początek operacji następnej jest wcześniejszy niż koniec operacji poprzedniej powiązanej z następną. Przy niezgodności terminów uwzględniany jest parametr: Zezwalaj na przesunięcia między operacjami. Zostały dodane pola, w których prezentowana są informacje na temat: Planowanego czasu trwania zlecenia – liczonego jako czas od startu planowanego najwcześniejszego procesu na zleceniu, do końca najpóźniejszego procesu na zleceniu Łącznego czasu operacji na zleceniu – czyli łączny czas wszystkich operacji na zleceniu. Na zakładce znajdują się funkcje: usunięcie operacji jest możliwe jeżeli nie ma do niej przypisanej realizacji usunięcie zasobu jest możliwe, jeżeli nie jest on powiązany z innym zasobem lub dokumentem (powiązanie to usuwa się poprzez edycję zasobu, czyli otworzenie okna: Edycja Surowca/Produktu, wybraniu zakładki: Związane, zaznaczenie powiązania i naciśnięcie przycisku: Dla elementów zlecenia produkcyjnego, z poziomu zakładki: Ogólne, na pasku narzędzi dostępne są funkcje: Na zakładce wyświetlane są wszystkie rezerwacje surowców i surowce, które mają wskazane pochodzenie z magazynu (nie są półproduktami innych operacji). Jeżeli ten sam surowiec jest wykorzystywany w różnych operacjach, to ten surowiec wyświetla się dla każdej operacji osobno. W celu ułatwienia pracy z oknem na liście materiałów wprowadzono sortowanie w kolumnach: Na zakładce: Materiały udostępniono następujące funkcje: Na zakładce pojawią się wszystkie koszty, które zostały przypisane na zleceniu, poprzez dodanie jako koszt dodatkowy i rozbicie według zleceń produkcyjnych. Na zakładce możliwe jest odpięcie kosztu dodatkowego, a także podgląd dokumentu spiętego – wskazanego jako źródło kosztu dodatkowego. Na zakładce widoczne są wszystkie dokumenty nadzlecenia produkcyjnego, do których zostało przypisane zlecenie. Z zakładki możliwe jest dołączenie i odłączenie zlecenia od NZP oraz wygenerowania nowego nadzlecenia. Pole tekstowe w którym można umieścić dodatkowe informacje. Z poziomu zakładki możliwe jest zaksięgowanie zlecenia. Na zakładce istnieje możliwość opisania zlecenia za pomocą atrybutów. Dodawanie atrybutów odbywa się na ogólnych zasadach (więcej w dokumentacji modułu: Administrator). Aby atrybut mógł zostać wykorzystany na zleceniu, musi on zostać przypisany do Obiektu: Technologia (moduł: Administrator>okno: Definicje atrybutów>zakładka: Obiekty>folder: Produkcja>gałąź: Zlecenia produkcyjne). Możliwe jest odwołanie się do zleceń produkcyjnych jako atrybutów, co umożliwia typ atrybutu: Zlecenie produkcyjne. Do Zlecenia produkcyjnego można przypisać załączniki, czyli zaimportować (oraz wyeksportować) pliki w formatach zdefiniowanych w oknie: Słowniki kategorii, w folderze: Inne, gałąź: Typy załączników. Mogą być to np. obrazy w formatach: .bmp; .jpg; dokumenty w formacie: .doc, arkusze kalkulacyjne itd. Za pomocą nadzlecenia produkcyjnego, dodanego w wersji 2019.0, możliwe jest spięcie zleceń produkcyjnych, do jednego dokumentu nadrzędnego. Dokument NZP posiada własną definicję dokumentu. Na NZP dostępne są informację na temat operacji i realizacji wchodzących w skład zleceń oraz materiałów, które się na nich znajdują. Na dokumencie nadzlecenia produkcyjnego widoczny jest postęp realizacji związanych z nim zleceń produkcyjnych. Po zamknięciu takiego dokumentu nie będzie możliwości dołączania i odłączania zleceń. Możliwe jest wiązanie zleceń z wieloma nadzleceniami. Dokumenty NZP oznaczany jest stanem wynikającym ze stanów zleceń wchodzących w jego skład. Dodatkowo możliwe jest oznaczenie nadzlecenia statusem zdefiniowanym w słownikach kategorii w Statusy nadzleceń. Lista nadzleceń produkcyjnych uruchamiana jest przyciskiem Informacje na liście wskazują numer dokumentu, akronim oraz miasto kontrahenta, numer dokumentu obcego, datę wystawienia, datę planowanego startu i końca nadzlecenia, stan oraz status NZP. Numer dokumentu nadzelecenia wyświetlany jest w kolorze: W oknie znajdują się pola i funkcje: Idź do – funkcja umożliwia odnalezienie na liście nadzlecenia produkcyjnego po wprowadzeniu numeru nadzlecenia i naciśnięciu przycisku: Właściciel – funkcja umożliwia zawężenie listy nadzleceń według centrum, w którym zostały one wygenerowane. Lista za – funkcja umożliwia zawężenie listy wyświetlanych dokumentów według okresu, w którym zostały one wygenerowane. Stan – funkcja umożliwiająca wyświetlenie dokumentów ze stanem : Nierozpoczęte, W realizacji, Zrealizowane, Zamknięte. Status – umożliwia filtrowanie nadzleceń ze względu na statusy pochodzące ze słownika kategorii. Operator (tylko na zakładce: Wg operatora) – funkcja umożliwia zawężenie listy wyświetlanych nadzleceń do wygenerowanych przez wybranego operatora. Otwarcie nadzlecenia możliwe jest tylko dla zamkniętych zleceń. Dokument nadzlecenia produkcyjnego można dodać przyciskiem Na zakładce widoczny jest stan nadzlecenia, postęp realizacji oraz dostępne są funkcje: Stan – w polu widoczny jest stan dokumentu uwzględniający realizację zleceń: Nierozpoczęte – stan dokumentu, na którym przypisane do niego zlecenia produkcyjne nie mają zarejestrowanych realizacji operacji. W realizacji – stan dokumentu od momentu zarejestrowania pierwszej realizacji na zleceniu dołączonym do NZP do momentu zamknięcia wszystkich zleceń związanych z dokumentem. Zrealizowane – stan dokumentu, na którym wszystkie powiązane ZP są zamknięte. Zamknięte – stan dokumentu uruchamiany przyciskiem: Status – funkcja umożliwia wybór statusu nadzlecenia, zdefiniowanego w słownikach kategorii. Ilość zleceń – w polu widoczna jest ilość zleceń związanych z NZP. Ilość operacji – ilość operacji planowanych znajdujących się na zleceniach. Start nadzlecenia – w polach widoczne są informacje na temat rozpoczęcia zleceń: Przykład I: Start nadzlecenia: Planowany: 10.06.2018; 12:00 Faktyczny: 10.06.2018; 12:15 Różnica: 15 min. Przykład II: Start nadzlecenia: Planowany: 10.06.2018; 12:00 Faktyczny: 10.06.2018; 13:15 Różnica: 1 godz. 15 min. Przykład III: Start nadzlecenia: Planowany: 10.06.2018; 12:00 Faktyczny: 11.06.2018; 13:15 Różnica: 1 d. 15 min. Koniec nadzlecenia – w polach widoczne są informacje na temat zakończenia zleceń: Czas trwania nadzlecenia – w polach widoczne są informacje na temat czasu trwania zlecenia: Ponadto w obszarze Statystyki zlecenia widoczne są wykresy kołowe dotyczące zleceń: Wykres realizacji operacji prezentuje dane dotyczące ilości zrealizowanych operacji. Na wykresie widoczne są operacje: Przykład : Na nadzleceniu jest 10 zleceń produkcyjnych. Na każdym zleceniu jest po jednej operacji planowanej, każda w ilości 5 szt (razem 10 operacji planowanych). Dla jednej z operacji zarejestrowana została realizacja na 3 szt. – operacja niezrealizowana w całości. Dla dwóch operacji zarejestrowana została realizacja na 5 szt. – operacje zrealizowane w całości. Dla kolejnej operacji zarejestrowana została realizacja na 8 szt. – operacja zrealizowana w całości. Dla pozostałych sześciu operacji nie zarejestrowano realizacji. Na wykresie widoczne będą operacje: Zrealizowane – 3 (30%) Niezrealizowane – 6 (60%) W realizacji – 1 (10%) Wykres realizacji operacji prezentuje dane dotyczące czasu realizacji operacji. Na wykresie widoczne są operacje: Przykład : Na nadzleceniu są 2 zlecenia produkcyjne, które razem mają 5 operacji, każda w ilości 10 szt. Dla dwóch operacji zarejestrowano realizację po terminie start na operacji planowanej. Dla trzech operacji niezarejestrowano realizacji operacji, ale nie upłynął termin planowanego startu tych operacji. Na wykresie widoczne będą operacje: Opóźnione – 2 (45%) W terminie – 3 (55%) Na nadzleceniu produkcyjnym na zakładce: Ogólne udostępnione zostały zakładki: Zlecenia, Pozycje zleceń, Operacje, Raport wykonania, Materiały. Prezentowane są następujące dane: Zlecenia: W oknie znajdują się filtry i funkcje: Właściciel – funkcja umożliwia zawężenie listy zleceń według centrum, w którym zostały one wygenerowane. Lista za – funkcja umożliwia zawężenie listy wyświetlanych zleceń według okresu, w którym zostały one wygenerowane. Pokaż status realizacji – funkcja umożliwiająca wyświetlenie bądź ukrycie statusu realizacji zleceń. Po zaznaczeniu parametru dostępny jest również filtr, który umożliwia zawężanie zleceń do wybranego rodzaju statusu realizacji. Filtr zawiera następujące opcje do wyboru: Wszystkie, Zgrubnie, Zaplanowane, Zrealizowane, Rozliczono, Do zamknięcia, Zamknięte. W filtrze nie są uwzględnione procenty statusów, czyli filtrujemy wszystkie rozliczone, albo wszystkie zaplanowane, niezależnie od tego w ilu procentach są rozliczone lub zaplanowane. Wyroby – funkcja umożliwiająca wyświetlenie bądź ukrycie kolumny z kodem produktu. Możliwe jest również wskazanie konkretnego kodu produktu, uwzględnione również zostaną te zlecenia na których znajdują się zaplanowane półprodukty zgodne z kodem produktu wskazanym w filtrze Wyświetlaj – umożliwia filtrowanie zleceń ze względu na stan. Możliwe do wyboru opcje: Wszystkie/Zwolnione do produkcji/Niezwolnione do produkcji. Pozycje zleceń: Na zakładce znajdują się pola i funkcje: Pozycje z zamkniętych zleceń – funkcja umożliwia wyświetlenie bądź ukrycie produktów z zamkniętych zleceń produkcyjnych. Operacje: Operacje z zamkniętych zleceń –funkcja umożliwia wyświetlenie/ukrycie operacji z zamkniętych zleceń produkcyjnych. Tylko opóźnione – umożliwia wyświetlenie/ukrycie operacji opóźnionych. Status – filtrowanie operacji ze względu na status: Wszystkie, Zaplanowana, Uruchomiona, W realizacji, Zrealizowana. Operacje – umożliwia wyświetlenie wszystkich operacji, operacji wykonanych i do wykonania. Raport wykonania: Realizacje z zamkniętych zleceń –funkcja umożliwia wyświetlenie/ukrycie realizacji operacji z zamkniętych zleceń produkcyjnych. Tylko niezrealizowane (bez RW/PW) – funkcja umożliwia filtrowanie realizacji operacji, dla których nie zostały wygenerowane dokumenty RW/PW na całą ilość. Materiały: Materiały z zamkniętych zleceń – funkcja umożliwia wyświetlenie/ukrycie materiałów z zamkniętych zleceń produkcyjnych. Wyświetlaj tylko niezrealizowane – po zaznaczeniu parametr na liście materiałów wyświetlane są: rezerwacje pochodzące z operacji zaplanowanych, materiały pochodzące z realizacji operacji, o ile nie są powiązane na całość z zatwierdzonym dokumentem handlowym (RW). Tylko braki – po zaznaczeniu wyświetlane są te pozycje, dla których ilość w kolumnę Brak jest większa od 0 (różnicą pomiędzy kolumną Ilość a Dostępna dla magazynu źródłowego) Pokaż – pole umożliwia wybór typu materiałów: Wszystkie, Materiały, Półprodukty. Na zakładce określa się podstawowe dane nagłówkowe nadzlecenia: Numer – numer dokumentu nadzlecenia produkcyjnego. Domyślnie podpowiadany będzie kolejny numer dokumentu, jednak podlega on modyfikacji, podobnie jak seria dokumentu. Dokument obcy – numer dokumentu obcego Kontrahent – kontrahent, na którego generowane jest nadzlecenie. Podanie kontrahenta nie jest wymagane dla zarejestrowania nadzlecenia. Kontrahent docelowy – kontrahent, dla którego przeznaczony jest realizowany produkt, będący przedmiotem nadzlecenia. Podanie kontrahenta docelowego nie jest wymagane dla zarejestrowania nadzlecenia. Właściciel – w polu wprowadzane jest domyślnie centrum, w którym wystawiane jest zlecenie produkcyjne. Projekt – nadzlecenie może być opisane za pomocą projektu wybieranego ze struktury projektów. Oddział – oddział, w którym realizowane jest nadzlecenie. Wystawiono, Zmieniono – w polach wprowadzane są daty wykonania odpowiednich operacji na dokumencie. Wystawił, Zmienił – w polach wprowadzany jest identyfikator operatora, który wykonał odpowiednie operacje na nadzleceniu. Na zakładce możliwe jest przypisanie atrybutów dla Nadzlecenia. Dodawanie atrybutów odbywa się na ogólnych zasadach (więcej w dokumentacji modułu: Administrator). Aby atrybut mógł zostać wykorzystany na Nadzleceniu, musi on zostać przypisany do Obiektu: Nadzlecenie produkcyjne (moduł: Administrator>okno: Definicje atrybutów>zakładka: Obiekty>folder: Produkcja>Nadzlecenie produkcyjne). Do Nadzlecenia produkcyjnego można przypisać załączniki, czyli zaimportować (oraz wyeksportować) pliki w formatach zdefiniowanych w oknie: Słowniki kategorii, w folderze: Inne, gałąź: Typy załączników. Mogą być to np. obrazy w formatach: .bmp; .jpg; dokumenty w formacie: .doc, arkusze kalkulacyjne itd Dla nadzleceń zostało udostępnione analogiczne narzędzie do ustawiania ich kolejności, jak w przypadku samych zleceń produkcyjnych, czyli zostało udostępnione nowe okno: Kolejka nadzleceń. Okno mozna otworzyć z menu Produkcja- Kolejka nadzleceń oraz zaznaczając nadzlecenie, które chcemy kolejkować w oknie Lista nadzleceń i wybierając w nim przycisk Ustawianie kolejki nadzleceń będzie decydowało o tym, w jakiej kolejności będą planowane zlecenia do przypisanych – zakolejkowanych nadzleceń. Ustawienie to będzie możliwe zarówno ręcznie – za pomocą przycisków: Przesuń w górę i Przesuń w dół oraz automatycznie. Dla nadzleceń udostępniono bowiem również od razu możliwość budowania kolejki za pomocą zapytań SQL. Należy pamiętać, że aby móc wykorzystać definicję kolejki przy kolejkowaniu nadzleceń, na definicji takiej kolejki należy zaznaczyć parametr Kolejka dla NZP. Realizacja zlecenia polega na wykonywaniu czynności, których efektem będzie wytworzenie produktu, wybranego na zleceniu. Generowanie zlecenia produkcyjnego możliwe jest z poziomu: Aby wygenerować zlecenie produkcyjne z poziomu okna: Zlecenia produkcyjne, należy: Produkt – w polu należy wprowadzić produkt, podając jego kod, lub wybierając odpowiednią pozycję z listy towarów, otwieranej po naciśnięciu przycisku: Klasa cechy, Cecha – w polach wprowadza się cechę produktu. Według wskazanej cechy dobierane będą technologie, za pomocą których możliwe będzie wytworzenie produktu o tej cesze (dostępne będą również te technologie, w których produkt ma zaznaczony parametr: Edycja cechy przy realizacji, ze względu na to, że dopuszczalna jest dla nich edycja cechy i można uzyskać produkt o cesze wskazanej na pozycji zlecenia). Jeśli nie zostanie wskazana żadna konkretna klasa cechy, a więc jeśli w polu klasa cechy ustawiona jest fraza ‘Cecha’ to przyciskiem lupki i opcją Edytuj cechę zostanie otwarte okno Podgląd wartości cechy w trybie do podglądu, nie będzie można edytować cechy lub wybrać jej z listy. Ilość/ilość w j. pomocniczej – ilość produktu, która ma zostać wytworzona dla zlecenia. Technologia – w polu następuje wybór technologii, jaka zostanie użyta do wytworzenia wybranego produktu. Na liście rozwijanej za pomocą przycisku: Planować od – domyślnie produkcja zostanie zaplanowana od bieżącego momentu (opcja: Planuj od teraz), jednak za pomocą przycisku: Planować od można wskazać konkretną datę, od której ma zostać uruchomione planowanie produkcji dla tego produktu. Wstecz – zaznaczenie tej opcji umożliwia zaplanowanie produkcji tak, aby produkt był gotowy na konkretny termin, np. produkt o krótkim terminie ważności ma być wyprodukowany na konkretny dzień (1 września), w którym trafi do odbiorcy. Zaznaczenie parametru umożliwi zaplanowanie „wstecz’ produkcji tego produktu od 1 września. Planować w partiach – parametr odpowiedzialny za określenie wielkości partii. W przypadku, gdy wielkość partii zostanie wskazana na pozycji zlecenia produkcyjnego, wtedy przy planowaniu takiej pozycji i operacji prowadzących do jej wytworzenia ignorowana będą ustawienia określające wielkości partii na technologii, w oparciu o którą odbywa się planowanie (czyli wszystkie parametry Planować po, znajdujące się na technologii i operacjach w technologii). Jeśli do wytworzenia wyrobu wskazanego na pozycji zlecenia, potrzebne jest zaplanowanie operacji pochodzących z innych technologii – również operacje pochodzące z tych technologii będą planowane w partiach, których wielkość określono na pozycji zlecenia produkcyjnego, będącego wyrobem końcowym. Przy planowaniu wyrobu, dla której wielkość partii określono na pozycji zlecenia, nie będą brane pod uwagę półprodukty zaplanowane wcześniej lub wytwarzane na innych zleceniach. Czyli planowanie wyrobu, dla którego określamy wielkość partii na pozycji zlecenia będzie zawsze planowało od nowa ilości potrzebnych półproduktów (o ile potrzeba uzyskania takich wynika z technologii). Dla planowania w partiach określonych na zleceniu zostały udostępnione dwie opcje tego planowania: Kontrahent – kontrahent, na którego generowane jest zlecenie. Podanie kontrahenta nie jest wymagane dla zarejestrowania zlecenia. Kontrahent docelowy – kontrahent, dla którego przeznaczony jest realizowany produkt, będący przedmiotem zlecenia. Podanie kontrahenta docelowego nie jest wymagane dla zarejestrowania zlecenia. Priorytet – priorytet z jakim realizowana będzie dana pozycja, priorytety mają trzy wartości 10 – wysoki, 20 – standardowy oraz 30 – niski. Ilość zasobów – pole w którym można wskazać maksymalną wielokrotność zasobów z technologii, która następnie jest dobierana do operacji. Przykładowo, jeśli w technologii liczba zasobów jest określona na 2, a na pozycji zlecenia wskazano wartość pola na 2, to będzie oznaczało, że maksymalnie można dobrać 4 zasoby z tego gniazda roboczego. Na oknie pozycji zlecenia produkcyjnego umieszczono w trybie do podglądu informacje prezentowane na liście pozycji zlecenia produkcyjnego. Na pozycji zlecenia prezentowane są dodatkowo pola: Po wprowadzeniu danych zlecenia można je zapisać, używając przycisku: Tak, jak w przypadku innych dokumentów w systemie Comarch ERP XL, istnieje również możliwość wygenerowania zlecenia produkcyjnego za pomocą skrótu klawiaturowego: <Ctrl+Insert>, na zarejestrowanym zleceniu produkcyjnym. W wersji 11.0 Systemu udostępniono funkcjonalność polegającą na umożliwieniu zapisania pozycji ZP bez zdefiniowanej technologii, co dotychczas nie było możliwe w Systemie, wówczas w polu Technologia pojawi się wpis <Nie określono>. Pozycja zlecenia produkcyjnego zakładka Kalkulacje kosztu. Zostaną wyświetlone wszystkie kalkulacje na dany produkt, możliwe jest również dodanie kalkulacji z tego poziomu. Pozycja zlecenia produkcyjnego zakładka Atrybuty Wyświetlenie atrybutów dodanych do pozycji zlecenia, możliwość dodania kolejnych atrybutów. Podczas dodawania pozycji na Zlecenie produkcyjne technologia podpowiada się według poniższych zasad: Przykład: Zdefiniowane są trzy technologie do wyprodukowania produktu P1, na TP-1 nie ma dodanego kontrahenta, na TP-2 jest dodany kontrahent K1, lecz z wybraną opcją Technologia domyślna na NIE, na TP-3 jest dodany kontrahent K2, z zaznaczoną opcją Technologia domyślna na TAK. Na zamówieniu jest kontrahent K2. Po przekształceniu ZS do ZP, na pozycji zlecenia podpowie się domyślna technologia TP-3. Przykład: Zdefiniowane są trzy technologie do wyprodukowania produktu P1, na TP-1 jest dodany kontrahent K1, na TP-2 jest dodany kontrahent K2, na TP-3 jest dodany kontrahent K3, na wszystkich technologiach zaznaczona jest opcja Technologia domyślna na TAK. Na pozycji zlecenia produkcyjnego zostaje dodany produkt P1 oraz kontrahent K1 – podpowie się technologia TP-1, po zmianie na kontrahenta K1 – technologia zmieni się na TP-2, po zmianie na kontrahenta K3 – technologia zmieni się na TP-3. Domyślność technologii obowiązuje wyłącznie dla towaru i kontrahenta głównego. Zatem wprowadzenie w technologii domyślnej kontrahenta docelowego innego niż jest na pozycji zlecenia, nie ma żadnego znaczenia dla podpowiadania domyślnej technologii – ogólnie nie jest sprawdzany kontrahent docelowy podczas wyszukiwania technologii domyślnej. Planowanie zlecenia polega na zaplanowaniu procesów produkcyjnych i operacji (a w ich ramach – zasobów) w ilościach odpowiednich dla wytworzenia wymaganej ilości produktu określonego na zleceniu. Możliwe jest uruchomienie planowania Wybór rodzaju planowania następuje z menu rozwijanego przyciskiem: Podczas planowania zlecenia system wykonuje następujące czynności: W przypadku, gdy na operacji w technologii zostało wskazane gniazdo robocze, dla którego określono wartość parametru Zasoby/Zwiększać na Tak, wówczas system wyszukuje zasoby dla gniazda roboczego na okres, jaki wynika z operacji w technologii. Zasoby dobierane są w ilości: Nie mniejszej, niż wskazana jako minimalna ilość na operacji w technologii (czyli ilość wskazana na operacji w technologii, na zakładce Gniazda robocze, w kolumnie: Ile) Nie większej, niż wynika to ze wzoru: minimalna ilość zasobów x ilość partii Po odnalezieniu zasobów według powyższych zasad wyliczany jest czas trwania operacji według następującego wzoru: Tc = X / (n * w) * Ti * Z Gdzie: Tc – planowany czas operacji X – całkowita ilość do wyprodukowania – ilość wyrobu gotowego na ZP n – ilość znalezionych zasobów we wskazanym terminie w – średnia wydajność zasobów dobranych do operacji Ti – czas trwania operacji z technologii produkcji dla minimalnej ilości zasobów (czyli czas operacji z technologii) Z – ilość zasobów z operacji w technologii (wartość z kolumny ile) Przy wyliczaniu czasu operacji wyliczane jest wszystko w godzinach. Wyliczając czas operacji może się zdarzyć, że dla każdego gniazda roboczego, przypisanego do operacji czasy te wyjdą różne – w tej sytuacji czas operacji powinien być taki, jaki jest najdłuższy czas gniazda roboczego dla tej operacji. Przykład: Czas trwania operacji w technologii dla 1 szt. produktu to 2 godziny (Ti=2) Całkowita ilość do wyprodukowania to 4szt. (x=4) Ilość znalezionych zasobów to 4 (n=4) Ilość zasobów w operacji w technologii to 2 (Z=2) Planowany czas operacji wyniesie 4 godziny (Tc=4) Jeśli na definicji dokumentu ZP, na zakładce Planowanie zostanie zaznaczony parametr ‘Podczas planowania wiąż z wolnymi ZZ/ZW’, wówczas w planie produkcji zostanie uwzględniony czas potrzebny na dostawę surowców zamówionych dokumentami zamówień do dostawców lub zamówień wewnętrznych do innych oddziałów. Podczas planowania zleceń, system sprawdza czy są zarejestrowane jakiekolwiek ZZ lub ZW na surowce, nie powiązane jeszcze z żadnym ZP lub innym obiektem w systemie, a następnie ustala termin realizacji operacji produkcyjnych zgodnie z planowaną dostępnością surowców na podstawie dat realizacji pozycji zamówienia. Po zaplanowaniu zlecenia na podstawie dokumentów ZZ i ZW następuje powiązanie zamówienia ze zleceniem tak, że przy kolejnym planowaniu innego zlecenia nie są uwzględniane te same zamówienia. Jeśli w momencie planowania zlecenia produkcyjnego nie ma w systemie zarejestrowanych zamówień zakupu lub wewnętrznych na potrzebny do procesu produkcyjnego surowiec, to ZP zaplanuje się wyłącznie w oparciu o dostępność zasobów produkcyjnych. Po wygenerowaniu zamówień na brakujące materiały i przeplanowaniu zlecenia, system uwzględni czas realizacji określony na pozycjach zamówień i odpowiednio je powiąże. Przy planowaniu niezmiennie sprawdzana jest dostępność zasobów. W związku z funkcjonalnością sprawdzania i wiązania zamówień ze zleceniami produkcyjnymi rozbudowana została lista konfliktów o nowy konflikt: Brak dostaw. Są zarejestrowane ZZ/ZW na surowce. Informacja o konflikcie wyświetla się w sytuacji, gdy ilość z elementów zamówień ZZ/ZW w całości wystarcza na potrzeby zlecenia. Podczas planowania szczegółowego, planowana jest produkcja takiej ilości produktu, jaka została przewidziana na zleceniu. Wykorzystane zostaną te półprodukty, których udział nie jest potrzebny do realizacji innych zleceń (nie są półproduktami wykorzystywanymi w procesach produkcyjnych na innym zleceniu). System sprawdza, z których wolnych półproduktów można otrzymać produkt i produkty końcowe. Jeżeli technologia przewiduje powstanie wielu produktów, wtedy podczas planowania ilości produktów, które powstaną brane jest pod uwagę zapotrzebowanie na te produkty. Zapotrzebowanie to jest liczone według rezerwacji na dane towary (produkty) i planu zapotrzebowania z uwzględnieniem normatywów towaru (ilości minimalnej i maksymalnej) określonych na karcie towaru. Przy określeniu tego zapotrzebowaniu uwzględniana jest zawsze rotacja liczona według obrotu danym towarem z ostatniego półrocza (wg dokumentów rozchodowych). Po uruchomieniu tej funkcji do zaplanowanych operacji będą dobierane tylko zasoby z zaznaczonym parametrem na technologii: Planowana zawsze oraz szczegółowo. Planowanie uproszczone polega na określeniu terminu planowanych operacji, jednak bez wyszukiwania do zaplanowanych operacji żadnych zasobów. Dobieranie zasobów będzie możliwe bądź poprzez ewidencję ręczną (dokonywaną przez np. brygadzistę) lub automatycznie przez funkcje: Dobierz zasoby szczegółowo lub Dobierz zasoby wszystkie. Planowanie zgrubne będzie polegało na planowaniu na definiowane przez użytkownika okresy planistyczne. Ten rodzaj planowania będzie umożliwiał zaplanowanie operacji poprzez umiejscowienie jej w określonym przez Operatora okresie planistycznym. Dzięki temu możliwe będzie otrzymanie szybkiej odpowiedzi na pytanie, czy produkt danego rodzaju (np. zamówiony przez Klienta) jesteśmy w stanie otrzymać w tym, czy w następnym okresie planistycznym (czyli np. w tym lub w następnym tygodniu, miesiącu, kwartale). Planowanie na okresy planistyczne zostanie udostępnione w różnych opcjach: Wybór opcji będzie możliwy na definicji dokumentu zlecenia produkcyjnego. W odróżnieniu od innych rodzajów planowania, planowanie na okresy planistyczne nie będzie planowało operacji na konkretny termin, a także nie będą wyszukiwane konflikty. Okresy planistyczne będą dowolnie definiowane przez Użytkownika na poziomie definicji dokumentu każdego centrum. O tym, czy do operacji zaplanowanych zgrubnie będą dobierane zasoby, będzie decydował parametr na gnieździe roboczym. Zatem o tym, czy przy planowaniu operacji będą dobierane zasoby odpowiedniego gniazda roboczego, będzie decydował sam Użytkownik. Operacje zaplanowane zgrubnie będzie można przeplanowywać w pełnym zakresie, a więc ustalić konkretny termin jej realizacji wraz z dobraniem do nowego terminu zasobów. Gdy zlecenie produkcyjne planowane jest zgrubnie i czas trwania operacji jest dłuższy od okresu planistycznego, wówczas po zaplanowaniu w logu pojawi się odpowiednia informacja: „Czas trwania operacji jest dłuższy od okresu planistycznego z definicji dokumentu”. Funkcjonalność ma na celu usuniecie konfliktów, które powstały w wyniku planowania zlecenia produkcyjnego. Przykładowo - umożliwia przeplanowanie zleceń o niższym priorytecie, jeśli w wyniku zaplanowania zlecenia o priorytecie wyższym powstał konflikt uniemożliwiający realizację zlecenia o priorytecie niższym, np. ze względu na to, że do zlecenia o priorytecie wyższym zostały pobrane zasoby, które zostały wcześniej dobrane do zlecenia o priorytecie niższym. Funkcję przeplanowania zleceń uruchamia się z poziomu okna: Zlecenie produkcyjne (funkcja dostępna w menu rozwijanym za pomocą przycisku: Przykład wykorzystania tej funkcjonalności przedstawiony został w poniższym scenariuszu. W dniu 25.04.2017 o godz. 18:00, wygenerowane zostało zlecenie z normalnym (średnim) priorytecie na produkcję Produktu: Stół. Rozpoczęcie realizacji zlecenia zostało zaplanowane na 25.04.2017 od godziny 18:00. Do zlecenia w wyniku planowania został dobrany zasób – piła. Jednak tego samego dnia, czyli 25.04.2017, ale o godz. 18:00, w związku z pilnym zamówieniem od klienta, wygenerowano zlecenie o wysokim priorytecie, którego termin rozpoczęcia również wypadł na 25.04.2017 od godziny 18:00. Do tego zlecenia ponownie został dobrany zasób: piła (gdyż podczas planowania zlecenia o wysokim priorytecie analizowane są wszystkie zasoby – również te, które zostały „zajęte” przez zlecenia o niższym priorytecie). W wyniku planowania uzyskujemy zlecenie jak na poniższym rysunku. Ze względu na to, że do zlecenia z wyższym priorytetem został dobrany ten sam zasób, co do zlecenia z niższym priorytetem, odpowiednia informacja o konflikcie zostanie wyświetlona w oknie: Zlecenie produkcyjne, na zakładce: Procesy, w kolumnie: Konflikt dla operacji, w których wystąpi konflikt zostanie wyświetlona na zleceniu na czerwono. Te właśnie operacje – ze zlecenia o niższym priorytecie nadają się do przeplanowania. Jeżeli teraz podejrzymy poprzednie zlecenie – to zaplanowane z niższym priorytetem, okaże się, że również tam został zarejestrowany konflikt, a operacje, w dla których wystąpił konflikt wyświetlone są na czerwono. Ze względu na to, że pierwszeństwo w realizacji ma zlecenie z wyższym priorytetem, przeplanowania wymaga zlecenie z priorytetem niższym. Aby je przeplanować, należy uruchomić funkcję: Przeplanowywanie konfliktów, która jest dostępna z poziomu okna: Zlecenia produkcyjne, po rozwinięciu menu znajdującego się obok przycisku: W wyniku przeplanowania, konflikt na obydwu zleceniach zostanie usunięty – albo poprzez dobranie innego zasobu na zlecenie o niższym priorytecie, dzięki czemu możliwa będzie realizacja tego zlecenia we wskazanym terminie, lub poprzez zmianę terminu realizacji zlecenia. Dodawanie procesu i operacji może się odbywać ręcznie, po wybraniu na zleceniu produkcyjnym, z menu rozwijanego przyciskiem: Dodawanie procesu i operacji może służyć jako ręczne planowanie operacji. Umożliwia też planowanie samego procesu produkcyjnego (bez wskazania produktu na zakładce: Ogólne, zlecenia produkcyjnego). Planowanie w partiach polega na zaplanowaniu procesu i operacji w porcjach określonych: Dla procesu – w Technologii, na zakładce: Ogólne, pole: Plan. po: Dla operacji – na Operacji w technologii, na zakładce: Ogólne, pole: Plan. po: Zarówno proces jak i operacje będą się planowały w ilościach wynikających z planowania częściowego lub całościowego – jedyną różnicą będzie to, że będą się planowały w partiach, np. jeżeli ilość procesu na zleceniu wynosi 20, a w Technologii ustalono planowanie po 5 procesów, to zaplanowane procesy zostaną wyświetlone w 4 partiach – po 5 procesów każda. W zależności od planowania, kontrolowany jest jeden z parametrów – w planowaniu w przód System weryfikuje ustawienie parametru ‘Po poprzedniej’, w planowaniu wstecz sprawdzane jest ustawienie parametru ‘Przed następną’. Przykłady wykorzystania funkcjonalności przedstawione zostały poniżej. Przykład: Utworzona została technologia produkcyjna złożona z pięciu operacji. W ramach technologii produkowane są krzesła. W czwartej operacji krzesła wymagają pomalowania i po tej operacji konieczna jest 2 dniowa przerwa przed ostatnią operacją którą jest pakowanie. Operacja pierwsza trwa 2 godziny, operacja druga 6 godzin, trzecia 20 minut, czwarta 2 godziny, piąta również 2 godziny. Na operacji piątej ustawiono odstęp między operacjami Po poprzedniej = 2 dni. W sytuacji, gdy na podstawie technologii, zlecenie zaplanowane zostanie w przód, System zaplanuje wykonanie operacji piątej nie wcześniej niż 2 dni po zakończeniu operacji 4. W sytuacji gdyby zasoby potrzebne do realizacji piątej operacji były niedostępne dokładnie dwa dni po zakończeniu operacji czwartej, System zaplanuje realizację operacji na pierwszy dostępny termin po upływie ustawionych 2 dni. Przykład: Utworzono technologie produkcyjną na podstawie której drewniane koraliki są dwukrotnie lakierowane i nawlekane na żyłkę tworząc kolorowe drewniane korale. Technologia zbudowana jest z trzech operacji następujących po sobie – Kolorowanie, Lakierowanie , Nawlekanie. W ramach pierwszej operacji kolorowanych jest 100 koralików, kolorowanie jednego trwa 6 s. W ramach drugiej operacji koraliki pokrywane są warstwą lakieru bezbarwnego, lakierowanie 1 koralika trwa 10s. W ramach trzeciej operacji 100 koralików nawleka się na żyłkę o dł. 50 cm, operacja ta trwa w całości 15 minut. Operacja lakierowanie musi rozpocząć się najwcześniej 3 godziny po zakończeniu operacji KOLOROWANIE i zakończyć 6 godzin przed rozpoczęciem operacji NAWLEKANIE – w związku z tym na operacji Lakierowanie ustawiono parametr ‘Odstęp między operacjami, Przed następną = 6h’ na operacji KOLOROWANIE ten sam parametr uzupełniono wartością 3h. Zaplanowano, że na godzinę 15.00 30 listopada 2017 potrzebna jest 1 sztuka korali, w związku z tym wykonano planowanie wstecz: Każdy z zasobów ma zdefiniowany okres, w którym jest niedostępny: IŁ jest niedostępny od 00:00 do 23.59 30 XI, AN jest niedostępny 30 XI w godzinach 00:00 – 12:00, zasób KA jest niedostępny 30 XI w godzinach 08:00-15:00. Biorąc pod uwagę okresy niedostępności zasobów oraz bufory planowania, System zaplanował zlecenie tak, że operacja lakierowanie zaplanowana została w pierwszym dostępnym terminie, jednak nie wcześniej niż 3 godziny po operacji kolorowanie. W związku z niedostępnością zasobu AN operacja została zaplanowana tak aby zakończyć się w ostatniej chwili dostępności zasobu AN tj. 29.11.2017 o godz. 23:59 zachowując jednak zdefiniowany 6 – godzinny odstęp pomiędzy operacjami lakierowanie i nawlekanie oraz okresy niedostępności poszczególnych zasobów. Operacja nawlekanie zakończy się 30.11.2017 o godzinie 07:59 w związku z niedostępnością zasobu KA. Od wersji 2016.3 możliwe jest określanie priorytetów zlecenia poprzez daty planowania na pozycji zlecenia, czyli wcześniejsza data planowania, wskazana na pozycji zlecenia będzie miała wyższy priorytet, niż późniejsza data planowania, wskazana na innej pozycji zlecenia. Planowanie według dat jako priorytetów odbywa się po zaznaczeniu parametru ‘Data planowania pozycji ZP jako priorytet’ na zakładce ‘Produkcja’ na Edycji struktury firmy. Wykorzystanie tego parametru może mieć miejsce w sytuacji, gdy realizowane są zaplanowane zlecenia, a następnie zostanie dodane jedno ważniejsze zlecenie, z wcześniejszą datą planowania. W takiej sytuacji przy planowaniu zlecenia z wcześniejszą datą planowania, inne zlecenia, które mają tę datę późniejszą zostaną przeplanowane. Funkcjonalność powinna być wykorzystywana w powiązaniu z funkcjonalnością automatycznego przeplanowania zleceń o niższym priorytecie podczas planowania zleceń o wyższym priorytecie. W oknie znajdują się pola i funkcje: Technologia – w pole wprowadza się technologię, według której ma być przeprowadzony proces produkcyjny. Ilość procesu – w pole wprowadza się planowaną ilość procesów, które mają zostać uruchomione, aby zrealizować wymaganą ilość produktu wybranego na zleceniu. Podczas określania tej ilości działa kontrola ilości minimalnej i maksymalnej wprowadzonej na zleceniu. Oddział – domyślnie podpowiadany jest oddział, przypisany do Technologii (okno: Technologia, zakładka: Ogólne). Jeśli jednak oddział nie zostanie zdefiniowany na technologii, wtedy na proces zostanie wprowadzony oddział zdefiniowany na zleceniu (na zakładce: Ogólne). Priorytet procesu – domyślna wartość priorytetu pobierana jest ze zlecenia, na którym planowany jest proces. Możliwa jest jednak jego modyfikacja. Priorytet na procesie decyduje o ustawieniu priorytetu na operacjach zaplanowanych w ramach tego procesu (jeżeli nie zostanie zmodyfikowany na procesie, wtedy na operacjach będzie taki jak na zleceniu). Priorytet rezerwacji – priorytet będzie przepisywany z zakładki: Ogólne, zlecenia produkcyjnego. Ze wskazanym priorytetem będę generowane rezerwacje w tym procesie. Numer seryjny – pole służy wskazaniu numeru seryjnego dla produktu, który zostanie wyprodukowany. Na zakładce istnieje możliwość dowiązania kosztu do procesu i podejrzenia już dodanych kosztów. Na zakładce istnieje możliwość dodania Kalkulacji kosztu, podejrzenia już zapisanych kalkulacji. Na zakładce istnieje możliwość wprowadzenia opisu zaplanowanego procesu produkcji. Na zakładce: Atrybuty, można opisać zaplanowany proces atrybutami. Dodawanie atrybutów odbywa się na ogólnych zasadach. Aby atrybut mógł zostać wykorzystany na procesie, musi on zostać przypisany do Obiektu: [Produkcja].[Procesy] (moduł: Administrator>okno: Definicje atrybutów>zakładka: Obiekty>folder: Produkcja>gałąź: Procesy). Oprócz atrybutów dodanych, na zakładkę przenoszone będą automatycznie atrybuty określone na technologii. Do procesu można przypisać załączniki, czyli zaimportować (oraz wyeksportować) pliki w formatach zdefiniowanych w oknie: Słowniki kategorii, w folderze: Inne, gałąź: Typy załączników. Mogą być to np. obrazy w formatach: .bmp; .jpg; dokumenty w formacie: .doc, arkusze kalkulacyjne itd. Niezależnie od tego, czy operacja planowana jest automatycznie, czy ręcznie, parametry operacji na zleceniu produkcyjnym zgrupowane są w takim samym oknie. Sposób planowania ma natomiast wpływ na wypełnienie wartości w tym oknie – dla operacji planowanej ręcznie, konieczne jest ich wprowadzenie przez Użytkownika. W oknie znajdują się pola i funkcje: Etap – pole informujące o tym, czy edytowana operacja jest „kamieniem milowym” czyli operacją główną. Domyślne ustawienie parametru na operacji planowanej przepisywane jest z operacji w technologii, lecz mamy możliwość jego modyfikacji. Zamrożona- podobną funkcjonalnością, jak stan zlecenia: Zwolnione do produkcji, charakteryzuje się możliwość „mrożenia” operacji zaplanowanych. Wykorzystując tą funkcjonalność, możemy wyłączyć konkretne operacje na zleceniu z przeplanowywania, niezależnie od tego, czy zlecenie, z którego operacja pochodzi, znajduje się w stanie: Zwolnione do produkcji. Zaznaczenie na operacji checku: Zamrożona, nie będzie blokować przeplanowania operacji powiązanych – czyli jeśli zostanie uruchomione przeplanowanie wielu operacji, wśród których znajdą się operacje zamrożone, wówczas są przeplanowywane tylko te, które są niezamrożone, nawet jeśli między tym zamrożonymi a innymi operacjami powiązanymi są konflikty. W przypadku operacji następnych po operacji „zamrożonej” przeplanowywane są wg standardowych zasad przeplanowania operacji, nie ruszając operacji „Zamrożonej”. Zamrożenie operacji będzie miało znaczenie wyłącznie podczas automatycznego przeplanowania operacji produkcyjnych. Zatem przy ręcznej edycji operacji, możliwości edycji pozostaną bez zmian. W przypadku operacji oznaczonej jako: Zamrożona, czyli dla której PCZ_Zamrozona = 1 będzie możliwość edycji operacji wg standardowych reguł, czyli system zezwoli na dowolną zmianę ilości operacji, rezerwacji na niej, zwalnianie zarezerwowanych materiałów, modyfikację listy zasobów itd. Czyli parametr: Zamrożona będzie jedynie wpływał na to, czy operacja będzie podlegała automatycznemu przeplanowaniu czy też nie. Jeżeli na zamrożonej operacji zaplanowanej zostaną usunięte ręcznie zasoby (maszyny, pracownicy itd.) wtedy po wywołaniu planowania lub przeplanowania, nie będą dobierane do takiej operacji zasoby. Dla zamrożonej operacji zaplanowanej aktywne są funkcje: Stan zlecenia zwolnione do produkcji ma priorytet nad stanem operacji: Zamrożona. Oznacza to, że po zwolnieniu zlecenia, parametr ten nie ma już znaczenie, bo na operacji powinny od tego momentu obowiązywać reguły dla operacji na zwolnionym zleceniu. Zlecenie - w polu tym wyświetlany jest numer edytowanego zlecenia. Pole nie podlega edycji. Proces – w polu wyświetlany jest proces, do którego planowana jest operacja. Operacja – w polu wyświetlona jest nazwa operacji. Po naciśnięciu przycisku: Operacja, zostanie wyświetlona do podglądu operacja z technologii, na podstawie której zostało wykonane planowanie. Priorytet operacji – priorytet operacji, przenoszony ze zlecenia produkcyjnego (zakładka: Ogólne). Priorytet decyduje o tym, czy zasoby pobrane do operacji będą mogły być przypisane do innych operacji (w tym samym terminie) – z innym priorytetem – jeżeli na innych operacjach będą wyższe priorytety – wtedy zasoby zostaną pobrane do operacji z wyższym priorytetem (nawet, jeśli operacja z wyższym priorytetem została zaplanowana później). Oddział – oddział, w którym ma nastąpić realizacja operacji. Domyślnie, oddział ten jest przepisywany z Operacji w technologii, a jeśli nie został tam wskazany – wtedy przenosi się z procesu. Niezależnie od ustawienia domyślnego, oddział może na konkretnej operacji zostać zmieniony. Ilość – zaplanowana ilość operacji. Nr instrukcji - w polu można wprowadzić numer instrukcji, wg której będzie zdefiniowana i wykonywana operacja. Koszt – (koszt własny operacji) wartość wyliczana automatycznie podczas rozliczania zlecenia. Pole wypełniane na realizacji operacji. Terminy – w polach OD, DO wskazany jest przedział, w jakim została zaplanowana operacja. Jeżeli na operacji w technologii zaznaczony został parametr: Wiele terminów (zakładka: Ogólne), wtedy w panelu u dołu formatki zostaną wyświetlone terminy, na jakie podzielona została realizacja operacji (odpowiednio do okresów dostępności zasobów). Dla operacji zaplanowanej jako pierwszej w procesie, terminem rozpoczęcia będzie termin, w którym uruchomione zostało jej planowanie (o ile pozwala na to czas dostępności zasobu, którego udział został zaplanowany w realizacji operacji). Dla następnych operacji terminem rozpoczęcia będzie planowany czas zakończenia operacji poprzedniej, również przy zachowaniu warunku dostępności zasobu. Możliwe jest również wskazanie planowania od określonego terminu oraz planowanie wstecz. Czas realizacji – planowany czas realizacji operacji, domyślnie pobrany z Operacji w technologii (pole: Czas planowany). Czas realizacji powiązany jest z czasem rozliczeniowym – w przypadku zmiany czasu realizacji będzie odpowiednio aktualizowany czas rozliczeniowy. Powiązanie nie działa w przypadku modyfikacji czasu rozliczeniowego, co umożliwia określenie odrębnego czasy rozliczeniowego dla operacji lub poszczególnych terminów. Czas rozliczeniowy – czas, który zostanie pobrany do rozliczenia operacji podczas rozliczenia zlecenia. Domyślnie będzie on pobrany z Operacji w technologii (pole: Czas rozliczeniowy). Czas rozliczeniowy jest aktualizowany odpowiednio do modyfikacji czasu realizacji. Obok pól: Czas realizacji i Czas rozliczeniowy wyświetlana jest informacja o przeliczeniu czasu tam podanego wg tych samych zasad, w jakich podawany jest czas realizacji na harmonogramie operacji, czyli w przeliczeniu do: dni, godzin, minut, sekund. Czas wyświetlany aktualizowany jest po każdej zmianie czasu w polach: Czas realizacji i Czas rozliczeniowy. Modyfikował – w polu wprowadzane są dane o operatorze modyfikującym operację planowaną oraz dacie modyfikacji. Dla operacji planowanych wprowadzono wyświetlenie statusów, w jakich znajdują się te operacji. Na przykład operacje zaplanowane, dla których nie uruchomiono jeszcze realizacji będą miały wyświetlony status: Zaplanowana, a te dla których uruchomiono już realizację będą miały status: Uruchomiona. Informacja o statusie na oknie operacji wyświetlona będzie w belce okna, jak na poniższym rysunku: Informacja o statusie operacji w oknie operacji Informacje o statusie operacji zostaną wyświetlone również na harmonogramie operacji – w nowej kolumnie: status. Możliwe będzie filtrowanie na tym oknie operacji planowanych ze względu na ich status. Dzięki tej funkcjonalności możliwa będzie łatwiejsza analiza, które z zaplanowanych operacji są już realizowane. Na zakładce wyświetlone są listy operacji, z którymi powiązana jest bieżąca operacja. W obszarze ‘Poprzednie’ informacje o poprzednich operacjach wyświetlane są w kolumnach: Kod i nazwa - powiązanej operacji poprzedniej zapisane na zakładce Ogólne tej operacji. Zlecenie – Numer zlecenia z którego pochodzi powiązana operacja. Termin zakończenia – planowany termin zakończenia operacji. Czas trwania – planowany czas trwania operacji. Stopień realizacji – wyrażona w procentach wartość wyliczona dla operacji. Konflikt – w kolumnie wyświetlane są konflikty dla operacji. W obszarze ‘Następne’ informacje o następnych operacjach wyświetlane są w kolumnach: Kod i nazwa – powiązanej operacji następnej zapisane na zakładce Ogólne tej operacji. Zlecenie – Numer zlecenia na którym znajduje się powiązana następna operacja. Termin rozpoczęcia – planowany termin rozpoczęcia realizacji następnej operacji Czas trwania – planowany czas trwania wyświetlonej operacji Konflikt – istniejące konflikty dla operacji. W oknie dla każdego obszaru udostępniono pod przyciskami: Na zakładce wyświetlone są gniazda robocze i zasoby zarezerwowane do wykonania operacji. Jeżeli operacja jest zaplanowana automatycznie, gniazda robocze i zasoby są wprowadzane przez system po sprawdzeniu okresu dostępności zasobów przypisanych do wymaganego gniazda roboczego. W przypadku planowania uproszczonego, a także planowania szczegółowego i zgrubnego, bez zaznaczonego odpowiedniego parametru na gnieździe roboczym, zarówno gniazdo, jak i zasób należy dodać ręcznie. W kolumnie: Termin wyświetlone są informacje o terminie, w którym zasób został pobrany do realizacji zaplanowanej operacji. Na zakładce znajdują się funkcje: Aby usprawnić sposób rejestrowania udziału zasobu na operacji/realizacji operacji, udostępniona została możliwość rejestracji pracy zasobu poprzez podanie w pierwszej kolejności jego akronimu. Po wybraniu zasobu, do operacji/realizacji automatycznie zostanie przypisane gniazdo, z którym powiązany jest zasób, a wskazane na technologii. Okno: Operacja, zakładka Rezerwacje składa się z dwóch paneli, w panelu górnym prezentowane są rezerwacje na surowce, natomiast w panelu dolnym na produkty. Podczas automatycznego planowania operacji generowane są automatycznie rezerwacje. Data aktywacji oraz data ważności dla tych rezerwacji domyślnie pobierana jest z definicji dokumentu zlecenia produkcyjnego (dostępnej z poziomu modułu: Administrator) i wyświetlana jest na zakładce. Data ważności może zostać określona jako nieograniczona, co oznacza, że wygaśnie ona dopiero wtedy, gdy zostanie zrealizowana lub usunięta. O ustawieniu domyślnym nieograniczonej daty ważności rezerwacji zadecyduje ustawienie na definicji dokumentu zlecenia produkcyjnego parametru: Okres ważności rezerwacji – brak ograniczenia. W przypadku ręcznego dodania operacji, rezerwacje należy wygenerować za pomocą przycisku: W przypadku zmiany daty aktywacji lub ważności wyświetli się zapytanie: Czy zastosować do istniejących rezerwacji? Na zakładce znajdują się pola i funkcje: Ręczne wskazanie rezerwacji na towar (surowiec) odbywa się po naciśnięciu przycisku: Towar można wybrać bądź z listy towarów bądź z listy zasobów. Menu, z którego można wybrać odpowiednią funkcję, otwiera się po naciśnięciu przycisku: Okno zostało podzielone na dwie sekcje: ‘Przychodzące’ i ‘Wychodzące’. Sekcje odpowiednio zawierają informacje o pochodzeniu i przeznaczeniu półproduktów na operacji. Na listach półproduktów zapisywane są informacje: Kod i Nazwa – w kolumnie wyświetlany jest kod i nazwa materiału zapisana w technologii w oknie ‘materiał w technologii’ Ilość – W kolumnie wyświetlana jest ilość na jaką dana operacja związana jest z wyświetlanym półproduktem. Jm. – jednostka miary dla ilości. Operacja – w kolumnie wyświetlany jest kod operacji z jakiej pochodzi półprodukt (dla sekcji ‘Przychodzące’) lub kod operacji w której przewidziano wykorzystanie półproduktu. Zlecenie – w kolumnie wyświetlany jest numer zlecenia z której pochodzi powiązana operacja, jeżeli operacja pochodzi z tego samego zlecenia, zamiast numeru wyświetlana jest informacja ‘Bieżące’. Cecha – w kolumnie wyświetlana jest klasa i wartość cechy dla danego półproduktu. Pod każdą z sekcji umieszczono również przyciski: Na zakładce wyświetlone są zabiegi występujące na danej operacji. Na zakładce wyświetlone są koszty przypisane do operacji planowanej. Z poziomu zakładki istnieje możliwość przypisywania kolejnych kosztów. Zakładka obsługiwana jest na analogicznych zasadach co zakładki: Koszty, na innych obiektach produkcyjnych. Zakładka: Związane jest stale aktywna, wyświetlone są na niej dokumenty: W przypadku wygenerowania dokumentów RW do dokumentów WM, wygenerowanych z operacji planowanej, wówczas będą one wyświetlane jako dokumenty powiązane w kolejności RW – WM. Z menu kontekstowego do zaznaczonych na liście dokumentów będą dostępne następujące opcje: Z poziomu zakładki dostępne są funkcje: Zakładka umożliwia wprowadzenie obszernego opisu do planowanej operacji. Podczas automatycznego planowania operacji oraz dodawania operacji do zlecenia ręcznie zostanie przeniesiony opis z operacji w technologii. W przypadku przeplanowania zostanie przeniesiony opis z operacji w technologii na operacją zaplanowaną tylko wtedy, gdy opis na operacji w zleceniu jest niewypełniony. Na zakładce: Atrybuty, można opisać zaplanowaną operację atrybutami. Dodawanie atrybutów odbywa się na ogólnych zasadach. Aby atrybut mógł zostać wykorzystany na planowanej operacji, musi on zostać przypisany do Obiektu: [Produkcja]. [Procesy].[Operacje] (moduł: Administrator>okno: Definicje atrybutów>zakładka: Obiekty>folder: Produkcja>gałąź: Procesy>Operacje). Oprócz atrybutów dodanych, na zakładkę przenoszone będą automatycznie atrybuty określone na operacji w technologii. Do Operacji można przypisać załączniki, czyli zaimportować (oraz wyeksportować) pliki w formatach zdefiniowanych w oknie: Słowniki kategorii, w folderze: Inne, gałąź: Typy załączników. Mogą być to np. obrazy w formatach: .bmp; .jpg; dokumenty w formacie: .doc, arkusze kalkulacyjne itd. Materiały i produkty na zaplanowanej operacji prezentowane są jako rezerwacje materiałów które będą pobierane i produktów które będą realizowane. W przypadku półproduktów od wersji 2015.0 Systemu Comarch ERP XL rejestrowane jest w bazie powiązanie między półproduktem planowanym a operacjami, na których półprodukt będzie wykorzystywany, a więc powiązanie do operacji z której półprodukt pochodzi oraz powiązanie do operacji wykorzystującej półprodukt. Planowane pochodzenie oraz planowane dalsze wykorzystanie półproduktu prezentowane jest w oknie o nazwie ‘Edycja półproduktu’, wyglądającym nieco inaczej w zależności czy jest to półprodukt wychodzący, czy przychodzący. Okno ‘Edycja półproduktu’ posiada dwie zakładki: Ogólne oraz Atrybuty. Na zakładce Ogólne dostępne są dane: Kod i nazwa – dotyczy kodu i nazwy półproduktu zdefiniowanego na technologii. Towar – wyświetlany jest kod towaru pochodzący z kartoteki towarowej powiązanej z półproduktem. Pole obok przycisku Cecha – w polu wyświetlana jest klasa i wartośc cechy nadanej półproduktowi. W sekcji Ilość prezentowane są wartości dla ilości podstawowych: W sekcji ‘Planowane wykorzystanie półproduktu’ wyświetlana jest lista operacji do których powiązano półprodukt. W tabeli rejestrowane są informacje: Okno ‘Edycja półproduktu’ posiada dwie zakładki: Ogólne oraz Atrybuty. Na zakładce Ogólne dostępne są dane: Kod i nazwa – dotyczy kodu i nazwy półproduktu zdefiniowanego na technologii. Towar – wyświetlany jest kod towaru pochodzący z kartoteki towarowej powiązanej z półproduktem. Pole obok przycisku Cecha – w polu wyświetlana jest klasa i wartośc cechy nadanej półproduktowi. W sekcji Ilość prezentowana jest ilość podstawowa i pomocnicza na jaką półproduklt związany jest z zaplanowaną operacją. W sekcji ‘Planowane pochodzenie półproduktu’ wyświetlana jest lista operacji do których powiązano półprodukt. W tabeli rejestrowane są informacje: Za pomocą przycisku Podczas planowania operacji generowane są rezerwacje. W zależności od ustawień parametrów: Rezerwuj zasoby (na definicji dokumentu ZP oraz na ZP) oraz Rezerwacje blokują towar na magazynie, generowane rezerwacje mogą mieć przypisane zasoby. Funkcja: Aktualizuj rezerwacje, generuje rezerwacje dla operacji (jeżeli na operacji takich rezerwacji brakuje) lub przypisuje zasoby do już wygenerowanych rezerwacji. Operacje te wykonywane są zgodnie z ustawieniami wymienionych wyżej parametrów. Funkcja jest przydatna w sytuacji, gdy podczas planowania zlecenia nie zostały wygenerowane rezerwacje, np. ze względu na to, że termin zaplanowanej operacji jest zbyt odległy, by został spełniony warunek aktywności rezerwacji przed terminem jej wykonania (na definicji zlecenia produkcyjnego, wartość parametru: Aktywuj rezerwacje przed terminem, określono na 7 dni, a zlecenie, w dniu 01.12.2017 zostało zaplanowane na 30.01.2018). W takiej sytuacji uruchomienie funkcji: Aktualizuj rezerwacje, powoduje wygenerowanie rezerwacji, jeśli zostanie ona uruchomiona w dniu: 23.01.2018. Aby uruchomić funkcję, należy na zakładce: Procesy, rozwinąć menu za pomocą przycisku: Realizacja operacji rejestruje realizację wykonania zaplanowanej operacji. Z poziomu okna: Zlecenie produkcyjne, z zakładki: Procesy, możliwe jest uruchomienie realizacji: Realizacja wszystkich zadań na zleceniu jest możliwa również z poziomu okna: Zlecenia produkcyjne, po zaznaczeniu odpowiedniego zlecenia i wybraniu funkcji: Realizuj zlecenia, z menu rozwijanego za pomocą przycisku: Możliwe jest zrealizowanie innej ilości operacji niż zostało zaplanowanych, gdyż planowanie wskazuje tylko zakładaną ilość operacji, które powinny być wykonane. W trakcie produkcji może się jednak okazać, że zaszła potrzeba zrealizowania innej ilości operacji – mniejszej lub większej. Zarejestrowanie rzeczywistej ilość zrealizowanych operacji i innych parametrów realizacji odbywa się w oknie: Realizacja. Realizacja jest możliwa do momentu zamknięcia zlecenia. Po wykonaniu realizacji operacji, zostaną one wyświetlone w oknie: Zlecenie produkcyjne, na zakładce: Procesy. Aby były one widoczne, należy zaznaczyć parametr: Realizacje. Realizacje oznaczone są ikoną: Uwaga: Od wersji 2013 Systemu Comarch ERP XL udostępniono zakazy dla operatora związane z realizacją operacji, Powtórna realizacja terminu – nadanie operatorowi tego zakazu będzie blokowało mu możliwość realizacji terminu operacji, który został już wcześniej zrealizowany w całości. Jeśli czynność podzielona jest na terminy, wtedy zakaz będzie działał w zależności od uruchamianej funkcji – jeśli została zrealizowana czynność, to nie będzie można jej powtórnie zrealizować ani zrealizować żadnego jej terminu. Jeśli natomiast w tym przypadku został zrealizowany np. jeden termin, wtedy można zrealizować czynność tylko w zakresie jeszcze niezrealizowanym. Działanie zakazu skutkuje komunikatem o treści: „Realizacja nie zostanie dodana. Termin został zrealizowany w całości” Realizacja operacji przy braku surowców - W przypadku, gdy operatorowi nadano zakaz, podczas uruchamiania funkcji realizujących operację, System sprawdza, czy uruchamiana realizacja operacji, bądź terminu, ma surowce na magazynie potrzebne do jej realizacji, gdy stwierdza brak odpowiedniej ilości nie zezwala na taką realizację wyświetlając komunikat: „Realizacja nie zostanie dodana. Brak surowców do realizacji”. Realizacja operacji przy braku półproduktów – w przypadku, gdy operatorowi nadano zakaz, podczas uruchamiania funkcji realizujących operację nastąpi blokada, jeśli nie zrealizowano wszystkich półproduktów potrzebnych do jej uruchomiania w pełnej planowanej ilości. W systemie zostało wprowadzone rozwiązanie polegające na ogólnej blokadzie możliwości realizacji następnej operacji, jeśli nie zrealizowano wszystkich półproduktów poprzednich do tej operacji. Blokada taka będzie obowiązywała tylko dla tych operatorów, którzy mają ustawiony zakaz: Realizacja operacji przy braku półproduktów. Możliwość rejestracji realizacji operacji jest uzależniona od tego, czy w operacji lub operacjach dostarczających jej półprodukty uzyskano tyle półproduktów ile trzeba do jej uruchomienia w pełnej planowanej ilości. Kontrolowana jest przy tym wartość parametru: Dopasować ilość produktu o, czyli jeśli ilość uzyskanego półproduktu zmieści się w założonych tym parametrem widełkach, wtedy realizacja następnej operacji będzie możliwa. Przykład: Technologia składa się z dwóch operacji powiązanych półproduktem PP1. Zostało zaplanowane zlecenie na 10szt. produktu PK. Została zrealizowana pierwsza operacja w ilości 5 szt. Jeśli teraz operator, który ma ustawiony zakaz, spróbuje uruchomić realizację operacji drugiej, nie będzie mógł tego zrobić, gdyż aby zrealizować pełną ilość tej operacji brakuje mu półproduktów w ilości 5 szt. z poprzedniej operacji. Pojawi się komunikat: „Realizacja nie zostanie dodana. Brak półproduktów do realizacji. PP1 (brakująca ilość: 5). Przykład: Uwzględnienie parametru: Dopasować ilość powstałego półproduktu w kontroli możliwości realizacji następnej operacji. Technologia składa się z dwóch operacji, pierwsza w ilości 1szt. wykorzystuje 1 szt. surowca i powstaje 10szt. półproduktu PP1. Na półprodukcie PP1, ustawiono wartość parametru: Dopasować ilość powstałego produktu o: 20%. Ustawienie tego parametru powoduje, że dopuszczalna jest realizacja drugiej operacji, jeśli w poprzedniej operacji uzyskano półprodukt w ilości pomiędzy 8 i 12 szt. (20% +/- 10 szt. z technologii). Wariant 1: Zlecenie zostało zaplanowane, pierwsza operacja została zrealizowana w całości, jednak zamiast zakładanych w technologii 10szt. PP1 uzyskano 9szt. Ze względu jednak na to, że parametr: Dopasuj ilość powstałego produktu został ustawiony na 20%, to 9szt. jest wartością wystarczającą do realizacji następnej operacji. Czyli rejestracja operacji drugiej może być wykonana zarówno przez operatora bez zakazu: Realizacja operacji przy braku półproduktów, jak i przez operatora, który ma taki zakaz. Wariant 2: Zlecenie zostało zaplanowane, pierwsza operacja została zrealizowana w całości, jednak zamiast zakładanych w technologii 10szt. PP1 uzyskano 7szt. Jednak ze względu na to, że parametr: Dopasuj ilość powstałego produktu został ustawiony na 20%,, to 7szt. jest wartością niewystarczającą do realizacji następnej operacji. Czyli rejestracja operacji drugiej może być wykonana tyko przez operatora bez zakazu: Realizacja operacji przy braku półproduktów. Dla operatora, który ma ustawiony taki zakaz, należy zablokować możliwość realizacji operacji o wyświetlić odpowiedni komunikat. W module istnieje możliwość rejestracja wykonania części realizacji – jednego, lub wielu terminów operacji. Konieczność częściowej realizacji zachodzi w sytuacji, gdy operacja podzielona jest na wiele terminów, odpowiednio do trybu pracy zmianowej i każda zmiana po zakończeniu swojej części powinna odnotować wykonanie swojej części planu, czyli realizację „swojego” terminu. Możliwość realizacji poszczególnych terminów operacji dostępna jest z poziomu: Na zleceniu produkcyjnym, na zakładce: Procesy, w menu rozwijanym obok przycisku: Po uruchomieniu funkcji: Realizuj termin: Po dodaniu realizacji terminu i przejściu na zakładkę Materiały, System odpowiednio modyfikuje rezerwacje, aby część z nich mogła przejść na realizację Przykład: Mam operację zaplanowaną na 1 termin w ilości 3 szt. Realizuję tą operację w ilości 1 szt., a następnie dodaję kolejną realizację (przez Realizuj termin). Podpowie się ilość 3 szt. Do tej ilości dodaję 1 szt. już zrealizowaną, czyli w efekcie suma ilości operacji do realizacji (3 szt.) i już zrealizowanej (1 szt.) wynosi więcej niż ilość operacji zaplanowanej. W związku z tym od ilości do realizacji odejmujemy ilość już zrealizowaną i wychodzi nam ilość jaką podpowiadamy na dodawanej realizacji: 3-1 = 2. Przykład: Mamy operację zaplanowaną na 3 terminy w ilości 3 szt. Realizuję tą operację w ilości 1 szt. – pierwszy termin, a następnie dodaję kolejną realizację (przez Realizuj termin). Podpowie się ilość 1szt. do realizacji. Do tej ilości dodaję 1 szt. już zrealizowaną czyli w efekcie suma ilości operacji do realizacji (1 szt.) i już zrealizowanej (1 szt.) wynosi mniej niż ilość operacji zaplanowanej. W takiej sytuacji pozostawiamy do realizacji taką ilość, jaka podpowiedziała nam się do realizacji – czyli wynikająca z tego terminu – czyli 1 szt. Funkcja uruchamiana jest dla operacji oznaczonych jako operacje „milowe”. Po jej uruchomieniu dodawane są realizacje wszystkich operacji należących do etapu. Przez operacje należące do etapu należy rozumieć wszystkie operacje połączone półproduktami od operacji etapowej (dla której została uruchomiona realizacja) do poprzedniej operacji etapowej, niezależnie od tego, czy poprzednia operacja etapowa została zrealizowana. Jeżeli nie ma poprzedniej operacji „milowej”, wtedy realizujemy wszystko, co prowadzi do realizacji operacji etapowej. Po uruchomieniu funkcji: Realizuj wszystkie zostanie otworzone okno: Realizacja, w którym wyświetlone będą wszystkie terminy realizacji (według terminów które są na zaplanowanej operacji). Lista terminów wyświetlona jest w trybie multiselect, co umożliwia usuwanie niektórych terminów i rejestrację tylko niektórych z nich. Proporcjonalnie do usuwania terminów z okna: Realizacja, przeliczane będą ilości na realizacji oraz ilości wykorzystanego surowca i otrzymanego produktu. Funkcja: Realizuj wszystkie, zawsze wywołuje realizację wszystkich terminów, nawet wtedy, gdy jest uruchamiana do operacji, do której zarejestrowano już jakąś realizację. Użytkownik może jednak usunąć terminy wcześniej zrealizowane z okna, które otwiera się podczas realizacji wszystkich terminów. Funkcja: Realizuj wszystkie, umożliwia zatem realizację nie tylko wszystkich, ale również wielu terminów. Po zapisaniu okna, realizacja zostanie dodana na zlecenie. Funkcja: Realizuj termin bez edycji, wywołuje te same skutki, co funkcja: Realizuj termin, czyli realizuje pierwszy niezrealizowany termin operacji, a jeśli zostały zrealizowane wszystkie, dodaje realizację na ostatni termin tej operacji. Po uruchomieniu tej funkcji, nie jest jednak wyświetlane okno: Realizacja – realizacja dodaje się bezpośrednio po jej wywołaniu. Dodaną w ten sposób realizację można oczywiście edytować oraz usunąć. Funkcja: Realizuj wszystkie bez edycji, wywołuje te same skutki, co funkcja: Realizuj wszystkie, czyli realizuje wszystkie terminy operacji, dla której została uruchomiona, niezależnie od tego, czy jakiś termin tej operacji został wcześniej zrealizowany. Podobnie jak w przypadku funkcji: Realizuj termin bez edycji, uruchomienie funkcji: Realizuj wszystkie bez edycji, nie spowoduje otworzenia okna: Realizacja, z listą wszystkich terminów; realizacja zostanie bezpośrednio zapisana na zlecenie. Funkcja realizuje pozostałą ilość realizacji pokazując okno Realizacja operacji w ramach danej operacji. Funkcja realizuje pozostała ilość do zrealizowania bez możliwości edycji realizacji w ramach danej operacji. Uwaga: Od wersji 2017.01 Systemu Comarch ERP XL zmieniono przeliczanie czasu rozliczeniowego w stosunku do czasu realizacji w aplikacjach służących do uruchomienia i rejestracji realizacji produkcji: Jeśli realizacja jest uruchamiana – wtedy jako czas relizacji podajemy 0 (znamy wtedy tylko termin uruchomienia operacji, a nie mamy terminu zakończenia). W związku z tym, czas rozliczeniowy również będzie wynosił 0. Jeśli kończymy realizację wcześniej uruchomioną, wtedy wyliczamy czas realizacji na podstawie – od termin uruchomienia do termin zakończenia. Na podstawie czas realizacji przeliczamy czas rozliczeniowy. Jeśli tylko rejestrujemy zakończenie operacji (czyli dodajemy realizację bez jej uprzedniego uruchomienia), wtedy znamy czas realizacji i w stosunku do niego od razu przeliczamy czas rozliczeniowy. W oknie znajdują się parametry zrealizowanej operacji. W związku z tym, okno jest bardzo podobne do okna operacji planowanej. Jednak w odróżnieniu od okna operacji planowanej, w oknie operacji realizowanej rejestruje się rzeczywiste parametry będące wynikiem realizacji operacji. Etap – pole informujące o tym, czy edytowana operacja jest „kamieniem milowym” czyli czynnością główną. Ustawienie parametru na realizacji czynności przepisywane jest z czynności planowanej i nie mamy możliwości jego modyfikacji. Zlecenie – w polu tym wyświetlany jest numer edytowanego zlecenia. Pole nie podlega edycji. Proces – w polu wyświetlany jest proces, do którego planowana jest operacja. Operacja – w polu wyświetlona jest nazwa czynności. Po naciśnięciu przycisku: Operacja, zostanie wyświetlona do podglądy operacja z technologii, na podstawie której zostało wykonane planowanie. Priorytet czynności – priorytet czynności, przenoszony ze zlecenia produkcyjnego (zakładka: Ogólne). Priorytet decyduje o tym, czy zasoby pobrane do czynności będą mogły być przypisane do innych czynności (w tym samym terminie) – z innym priorytetem – jeżeli na innych czynnościach będą wyższe priorytety – wtedy zasoby zostaną pobrane do czynności z wyższym priorytetem (nawet, jeśli operacja z wyższym priorytetem została zaplanowana później). Oddział – oddział, w którym ma nastąpić realizacja czynności. Domyślnie, oddział ten jest przepisywany z Czynności w technologii, a jeśli nie został tam wskazany – wtedy przenosi się z procesu. Niezależnie od ustawienia domyślnego, oddział może na konkretnej czynności zostać zmieniony. Ilość – zaplanowana ilość czynności. Terminy – w polach OD, DO wskazany jest przedział, w jakim została zaplanowana operacja. Jeżeli na operacji w technologii zaznaczony został parametr: Wiele terminów (zakładka: Ogólne), wtedy w panelu u dołu formatki zostaną wyświetlone terminy, na jakie podzielona została realizacja operacji (odpowiednio do okresów dostępności zasobów). Za pomocą przycisku: Czas realizacji – łączny czas realizacji operacji. Pole zostanie domyślnie wypełnione wartością określoną w polu: Czas realizacji, na operacji planowanej. Jeżeli zostanie zmodyfikowany termin rozpoczęcia lub zakończenia realizacji, zmianie ulegnie automatycznie czas realizacji. Czas realizacji powiązany jest z czasem rozliczeniowym – w przypadku zmiany czasu realizacji będzie odpowiednio aktualizowany czas rozliczeniowy. Powiązanie nie działa w przypadku modyfikacji czasu rozliczeniowego, co umożliwia określenie odrębnego czasy rozliczeniowego dla operacji lub poszczególnych terminów. Czas rozliczeniowy – wartość w tym polu będzie pobierana zgodne z ustawieniem na Operacji w technologii, pola: Czas rozliczeniowy. Może on jednak zostać zmodyfikowany. Czas rozliczeniowy będzie uwzględniany podczas rozliczania. Czas rozliczeniowy jest aktualizowany odpowiednio do modyfikacji czasu realizacji (patrz opis powyżej). Modyfikował – w polu wprowadzane są dane o operatorze modyfikującym realizację oraz dacie modyfikacji Na zakładce znajduje się lista zasobów, wykorzystanych do realizacji operacji. Domyślnie będą to zasoby przepisane z operacji planowanej. Na realizacji możliwe jest jednak wskazanie innych zasobów (jeżeli zostały użyte podczas realizacji produkcji). Na zakładce wyświetlone będą koszty wykorzystania zasobu (po przeprowadzeniu rozliczenia) w podziale na koszty użycia zasobu, koszty przygotowania i zakończenia pracy w gnieździe roboczym. W kolumnie: Termin, wyświetlone są informacje o terminie, w którym zasób został pobrany do realizacji zaplanowanej operacji. Na zakładce znajdują się funkcje: Na zakładce wyświetlone są materiały, pobrane i wydane w wyniku realizacji operacji (zgodnie z ustawieniami na Operacji w technologii). Możliwe jest dodanie nowych zasobów (surowców i produktów), za pomocą przycisków: Na zakładce znajdują się także funkcje: Możliwe jest również skorzystanie z filtra i wyszukanie materiały po kodzie, nazwie. W przypadku gdy na zakładce: Materiały, zmieniony zostanie kod lub typ surowca, wtedy przy zapisywaniu okna: Realizacja, usuwane są rezerwacje na „poprzedni” surowiec i tworzone są one na nowo dla surowca zmienionego (jeżeli nie jest materiałem pomocniczym). Na zakładce rejestrowane są zabiegi do wykonania i wykonane w ramach realizacji. Wykonanie zabiegu nie jest wymagane do realizacji operacji i zamknięcia zlecenia. Obecnie ma charakter wyłącznie informacyjny. Rejestracja wykonania zabiegu następuje po naciśnięciu przycisku: Na zakładce istnieje możliwość wprowadzenia opisu dla realizacji operacji. Realizacja może zostać opisana atrybutami. Dodawanie atrybutów odbywa się na ogólnych zasadach. Aby atrybut mógł zostać wykorzystany na planowanej operacji, musi on zostać przypisany do Obiektu: [Produkcja]. [Procesy].[Operacje] (moduł: Administrator>okno: Definicje atrybutów>zakładka: Obiekty>folder: Produkcja>gałąź: Procesy>Operacje). Oprócz atrybutów dodanych, na zakładkę przenoszone będą automatycznie atrybuty określone na operacji w technologii. Do Realizacji można przypisać załączniki, czyli zaimportować (oraz wyeksportować) pliki w formatach zdefiniowanych w oknie: Słowniki kategorii, w folderze: Inne, gałąź: Typy załączników. Mogą być to np. obrazy w formatach: .bmp; .jpg; dokumenty w formacie: .doc, arkusze kalkulacyjne itd. Okno zasobu zarówno dla surowca i produktu ma ten sam układ pól, dlatego zostanie opisane razem. Okno otwierane jest z poziomu okna: Realizacja, z zakładki: Materiały. Na zakładce znajdują się pola: Kod – kod materiału. Nazwa – nazwa materiału. Magazyn – magazyn z którego został pobrany materiał (w przypadku surowca) lub na który został wydany produkt. Typ materiału – domyślnie zostanie wprowadzony odpowiedni typ (surowiec lub zasób), jednak możliwe jest też określenie typu materiału jako materiał pomocniczy. Materiał pomocniczy nie zdefiniowany dla Operacji w technologii, a pobrany na zlecenie będzie miał rozliczany według kosztu zgodnego z ostatnią ceną zakupu. Towar – w polu wprowadzana jest nazwa towaru (jeśli materiał ma zarejestrowaną kartę magazynową). Podczas dodawania materiału, który nie został zdefiniowany na Operacji w technologii, aktywny będzie przycisk: Pozycja kooperacji – materiał może być pozycją kooperacji – w zależności od ustawienia odpowiedniego parametru na materiale w technologii. Klasa cechy/ Cecha – w polach znajduje się klasa cechy i cecha, za pomocą której opisywany jest produkt. Pola będą dostępne do edycji jeżeli na materiale w technologii zostanie zaznaczony parametr: Edycja cechy przy realizacji. Cecha na materiale zostanie uwzględniona na dokumentach: Ilość – w pole wprowadzana jest ilość surowca/produktu wynikająca z ilości realizacji i ilości określonych dla Zasobu w technologii. Ilość ta dostępna jest do edycji (zmniejszenia/zwiększenia) jeśli w technologii dla tego zasobu (surowca/produktu) zaznaczony został parametr: Edycja ilości przy realizacji (okno: Zasób w technologii, zakładka: Parametry). W przypadku zmniejszenia ilości, zmiana nie pociągnie ze sobą zmiany w ilościach związanych (zasobach i rezerwacjach). Pomocnicza – pomocnicza ilość surowca/produktu. Pole będzie dostępne do edycji, jeśli na Zasobie w technologii zaznaczony został parametr: Edycja ilości pomocniczej przy realizacji. Podczas edycji tej ilości kontrolowane będą ilość minimalna i maksymalna dla zasobu, zdefiniowane na Zasobie w technologii. Podczas edycji ilości w jednostce pomocniczej System odpowiednio przeliczy ilość w jednostce podstawowej, edycja ilości w jednostce podstawowej nie będzie pociągała za sobą zmian w ilości prezentowanej w jednostce pomocniczej. Z tego poziomu dostępna jest obsługa jednostek pomocniczych z karty towaru dla surowca/produktu na realizacji zlecenia produkcyjnego. Obsługa jednostek przebiega w ten sam sposób, jak na technologii: Technologiczna – wartość pobierana z technologii produkcji i wyliczana proporcjonalnie do ilości na konkretnej realizacji. Zmiana wartości w grupie Ilość w polach ‘Ilość’ i ‘Pomocnicza’ nie powinna mieć wpływu na zmianę wartości ilości technologicznej w grupie ‘Ilość. (ilość widoczna po zaznaczeniu na operacji w technologii Podgląd ilości technologicznej przy realizacji) Numer partii/seryjny – Domyślnie, wartość pola jest przepisywana z pola: Numer seryjny, zdefiniowanego na zleceniu produkcyjnym, na zakładce: Ogólne lub numer partii/seryjny według wzorca. Przycisk Wzorzec nr partii/ser. – jeżeli jako cecha wybrane jest <Nr partii/ser. wg wzorca> dostępne jest pole do wyboru wzorca numeru partii/serii. Po wybraniu wzorca aktywny jest przycisk Przeliczaj wg jednostki pomocniczej- jeśli w TP został zaznaczony parametr Niezależna od jednostki podstawowej, wówczas jest możliwość modyfikacji ilości w jednostce pomocniczej, niezależnie od ilości w jednostce podstawowej i na odwrót. Koszt ustalono – parametr zostanie zaznaczony po przeprowadzeniu rozliczenia: Dla surowca: Dla produktu: Koszt – koszt własny surowca lub produktu. Dla produktu jest to koszt, który zostanie wprowadzony jako koszt produktu na PW. Ten sam koszt jest wyświetlony w kolumnie: Koszt, na zakładce: Procesy, w oknie: Zlecenie produkcyjne. Koszt surowca – w polu wprowadzany jest koszt surowca. Rodzaj kosztu/Cena ewidencyjna – w polu wyświetlony jest rodzaj kosztu (zgodnie z ustawieniem na zasobie w technologii). W przypadku zdefiniowania na zasobie w technologii ceny ewidencyjnej dla zasobu, zostanie wyświetlona ta cena. Istnieje możliwość wyboru typu ceny, o ile surowiec nie jest półproduktem z innej operacji, na którym określono cenę ewidencyjną. W takim przypadku na surowiec zostanie przepisana ta cena bez możliwości edycji. Waga Kosztu/ Waga wg ilości – ustawienie pobierane z technologii, dostępne do edycji dla produktu Produkt uboczny – sekcja aktywna wyłącznie dla materiałów typu: Produkt uboczny. W sekcji możliwe jest określenie rodzaju produktu ubocznego oraz wskazanie kodu niezgodności dla produktu. Kod niezgodności wybierany jest z listy, którą Użytkownik może dowolnie rozbudowywać w oknie: Słowniki kategorii (gałąź: Kody niezgodności), dostępnej w module: Administrator. Na zakładce wyświetlone są rezerwacje wygenerowane na bieżący zasób. Zakładki nie ma w oknie: Edycja produktu. Na zakładce dostępne są funkcje: Zakładka widoczna dla produktów, wyświetla kontrahenta dodanego na pozycję zlecenia. Na zakładce wyświetlone są koszty przypisane do surowca/produktu. Z poziomu zakładki istnieje również możliwość przypisywania kosztów. Zakładka służy wyświetleniu dokumentów związanych z zasobem, czyli dokumentów RW/WM, którymi pobrano surowce lub dokumentów PW/PM, którym wydano produkt. Jeżeli zasób jest powiązany z półproduktem otrzymanym w wyniku realizacji innej operacji, wtedy wyświetlone zostanie to powiązanie. Na zakładce wyświetlone będą również dokumenty RW/PW na kooperację, o ile są związane z surowcem/produktem. Z poziomu zakładki możliwe jest również wiązanie dokumentów RW/PW na kooperację. Na zakładce znajdują się funkcje: W przypadku wybrania opcji: Zwiąż z pozycją dokumentu RW, zostanie wyświetlona historia towaru, na której wyświetlone są dokumenty RW, które można spiąć z zasobem. Na liście (w kolumnie LP) wyświetlony jest numer pozycji dokumentu, wiązanej z zasobem. Po rozwinięciu menu obok przycisku Realizacja może zostać opisana atrybutami. Dodawanie atrybutów odbywa się na ogólnych zasadach (więcej w dokumentacji modułu: Administrator). Aby atrybut mógł zostać wykorzystany na planowanej operacji, musi on zostać przypisany do Obiektu: [Produkcja]. [Procesy].[Zasoby] (moduł: Administrator>okno: Definicje atrybutów>zakładka: Obiekty>folder: Produkcja>gałąź: Procesy>Zasoby). Oprócz atrybutów dodanych, na zakładkę przenoszone będą automatycznie atrybuty określone na odpowiednim zasobie w technologii. Funkcja aktualizuje numery partii/seryjne na wyrobach gotowych/półproduktach/produktach ubocznych. W zależności od ustawień parametrów (na strukturze firmy, na zakładce Produkcja): Blokuj dla pozycji związanych z pokumentem PW oraz Wykonuj również dla PW w buforze, funkcja nie będzie aktualizowała cechy na produkcie, do którego wystawiono PW lub będzie aktualizowała cechę na dokumencie PW w buforze. Dokument RW można powiązać z zasobem – surowcem, który został pobrany do wytworzenia z półproduktu bądź produktu. Moment dla wiązania zasobu z dokumentem RW nie jest ściśle określony – wygenerowanie dokumentu RW nie zostało obłożone rygorem konieczności wykonania tej operacji przed podjęciem kolejnych kroków realizacji produkcji. Zalecaną ścieżką realizacji produkcji jest pobranie surowca i powiązanie go z dokumentem RW, przeprowadzenie częściowego rozliczenia, a następnie wydanie produktu i powiązanie go z dokumentem PW. Możliwa jest jednak również inna ścieżka, w której najpierw wygenerowany zostanie dokument PW, którym zostanie wydany wytworzony już produkt, a dopiero potem nastąpi wygenerowanie dokumentu RW na surowiec, który został wykorzystany do wytworzenia tego produktu. Taka elastyczność w kolejności rejestrowania poszczególnych operacji nie paraliżuje procesu produkcji, gdy zachodzi potrzeba szybkiego wytworzenia i wydania produktu Klientowi. Jednocześnie system nie pozwoli zamknąć zlecenia, gdy nie zostaną spełnione wszystkie formalne wymagania – jednak można ich dokonać już po zakończeniu rzeczywistego procesu produkcji. Dokumenty RW generowane ze zlecenia produkcyjnego będą miały taką serię, jaka jest na źródłowym zleceniu. Po zamknięciu zlecenia produkcyjnego, nie będzie możliwości anulowania dokumentów RW, wygenerowanych z tego zlecenia. Generowanie dokumentu RW odbywa się przez: Uwaga: Możliwe jest wygenerowanie dokumentu RW na Zasób, jeżeli ma on zaznaczony parametr: Dokumenty RW. Uwaga: Możliwe jest generowanie dokumentu RW na kontrahenta, co ułatwia wyszukiwanie dokumentów związanych z produkcją Uruchomienie funkcji: Generowanie RW z planu powoduje aktualizację rezerwacji, przypisanie zasobów do wygenerowanych rezerwacji, a następnie generowanie RW na zarezerwowane zasoby. W logu wyświetlanym po aktualizacji rezerwacji przedstawione będą rezerwacje, które nie mają przypisanych zasobów. Czyli podczas generowania RW z planu, wykonywane będą te same operacje co w przypadku dodania realizacji do operacji. Dokument RW zostanie wygenerowany na te surowce, które zostały zarezerwowane. Funkcja umożliwia generowanie RW z operacji planowanej również na te zarezerwowane zasoby, które zostały dodane ręcznie do operacji planowanej, a których nie ma w technologii. Warunkiem na dodawanie ręczne zasobów do zlecenia jest zaznaczenie w technologii, na operacji, parametru: Dowolne materiały. Funkcja: Generowanie RW z planu jest dostępna z poziomu: Dokumenty RW wygenerowane z operacji planowanej wyświetlane są na zakładce: Związane. Po dodaniu realizacji zostaną przepięte wygenerowane RW na surowce, uwzględniając ilość surowca na realizacji. Jeżeli dla towaru (surowca) ustawiono na karcie towaru jednostkę pomocniczą jako proponowaną przy sprzedaży i dla tej jednostki ustawiono sprzedaż w jednostkach całkowitych, wtedy RW generowane jest na całkowitą ilość pomocniczą, nawet jeśli z technologii wynika inna ilość potrzebnego surowca w jednostce podstawowej. Surowce i produkty ze Zlecenia Produkcyjnego, które nie zostały powiązane z żadnymi dokumentami RW/PW możemy spinać z pozycjami wcześniej wygenerowanych dokumentów RW/PW. Funkcję: Spinaj z pozycją dokumentu RW/Spinaj z pozycją z pozycją PW możemy uruchomić z poziomu: Po zaznaczeniu na liście surowców i wywołaniu funkcji: Spinanie z pozycją dokumentu RW zostanie wyświetlone okno: Lista dokumentów RW. Funkcja: Spinanie z pozycją dokumentu RW zawiera dodatkowe opcje, które umożliwiają spinanie zleceń z elementami dokumentu RW według cechy wydawanego towaru. Możliwe opcje to: bez kontroli cechy, wg cechy dostawy, według cechy towaru. Po wybraniu odpowiedniej opcji, zostaną spięte materiały na wybranych zleceniach produkcyjnych tylko z tymi pozycjami RW, które mają wskazaną cechę (dostawy lub towaru). W przypadku niemożności związania wybranego RW z żadnym surowcem wyświetlany będzie odpowiedni komunikat. Funkcja będzie możliwa do wywołania dla tych surowców, które nie zostały jeszcze całościowo spięte z dokumentami RW. Funkcję możemy także uruchomić w sytuacji, gdy został zaznaczony proces. Wtedy należy wiązać wybrane RW z surowcem w tym procesie. Surowiec, który zostanie spięty z dokumentem będzie wyświetlany w oknie: Edycja surowca, na zakładce: Związane. Funkcja: Spinanie z pozycją dokumentu PW działa analogicznie jak funkcja: Spinaj z pozycją dokumentu RW, oczywiście z uwzględnieniem spinania z produktem. Funkcja: Generowanie RWK pozwala na zmniejszenie ilości surowca, jeśli ilość ta jest spięta z dokumentem RW. W przypadku niezgodności między ilością surowca, a ilością spiętą na dokumencie RW udostępniono możliwość generowania dokumentu RWK na tą różnicę. Pod warunkiem jednak gdy, ilość surowca jest mniejsza niż ilość na spiętym z surowcem dokumencie RW. W przypadku, gdy z surowcem związanych jest kilka dokumentów RW, w pierwszej kolejności korygowany jest dokument RW najpóźniej wystawiony, do jego pełnej ilości. Jeśli na nim zabraknie już ilości, korygowany jest kolejny dokument RW. Surowiec, który zostanie skorygowany dokumentem RWK będzie wyświetlany w oknie: Edycja surowca, na zakładce: Związane. Funkcja: Generowanie RWK jest dostępna z poziomu: Funkcja: Generowanie WM z planu umożliwia wygenerowanie dokumentów magazynowych na surowce dla operacji zaplanowanych w zleceniu produkcyjnym. Po uruchomieniu funkcji następuje aktualizacja rezerwacji i przypisanie zasobów do wygenerowanej rezerwacji, a następnie wygenerowanie dokumentu WM na zarezerwowane zasoby. Dokument WM możemy wygenerować pod warunkiem, że nie został on wcześniej utworzony razem z RW. Ponadto dokument WM zostanie wygenerowany tylko na te surowce, które zostały zarezerwowane. Podczas generowania dokumentu WM zostanie wskazany magazyn źródłowy taki, jaki został wskazany na rezerwacji utworzonej dla surowca, który ma zostać wydany. Z dokumentu WM wygenerowanego z poziomu ZP, możliwe jest generowanie tylko dokumentu RW. W przypadku generowania dokumentu RW z planu, do którego został wygenerowany dokument WM, generowany jest dokument RW ze wskazaniem na ten dokument WM. Jeżeli do operacji planowanie zostało wygenerowanych więcej dokumentów magazynowych, zostanie wyświetlona lista tych dokumentów z możliwością wyboru. Funkcję: Generowanie WM z planu możemy wywołać z poziomu: Funkcja: Generowanie WM umożliwia wygenerowanie dokumentów magazynowych na surowce dla operacji realizowanych. Po wywołaniu funkcji zostanie utworzony dokument WM na zarezerwowane surowce, o ile dokument taki nie został wygenerowany już razem z RW. W przypadku generowania dokumentu RW z realizacji, do której został wygenerowany dokument WM, wygeneruje się dokument RW ze wskazaniem na tą WM. Jeżeli do realizacji (surowca) zostało wygenerowanych więcej dokumentów magazynowych, wówczas zostanie wyświetlona lista tych dokumentów z możliwością wyboru. Jeżeli dokument RW jest powiązany z WM, to dokumenty te będą wyświetlane jako powiązane w kolejności RW – WM. Funkcję: Generowanie WM można uruchomić z poziomu: Funkcja: Generowanie PM umożliwia wygenerowanie dokumentu magazynowego na produkty uzyskane ze zlecenia produkcyjnego. Po wywołaniu funkcji zostanie utworzony dokument PM na produkty, o ile taki dokument nie został wygenerowany razem z PW. W przypadku generowania dokumentu PW z realizacji, do której został wygenerowany dokument PM, powstanie dokument PW ze wskazaniem na tą PM. Jeżeli do realizacji produktów zostało wygenerowanych więcej dokumentów magazynowych, wyświetlona zostanie lista tych dokumentów z możliwością wyboru. Jeżeli dokument PW jest powiązany z PM, to dokumenty te będą wyświetlane w kolejności PW – PM. Funkcja: Generowanie PM jest dostępna z poziomu: Podobnie jak ma to miejsce w przypadku dokumentu RW, nie został ściśle zdeterminowany moment na wygenerowanie dokumentu PW. Musi on jednak zostać wygenerowany przed zamknięciem zlecenia. Dokumenty PW generowane ze zlecenia produkcyjnego będą miały taką serię, jaka jest na źródłowym zleceniu. Generowanie dokumentu PW odbywa się poprzez: Po zamknięciu zlecenia produkcyjnego, nie będzie możliwości anulowania dokumentów PW, wygenerowanych z tego zlecenia. Uwaga: Generowanie korekty do dokumentu PW, nie ma znaczenia dla realizacji procesu produkcji i nie jest odnotowywane na zleceniu. Uwaga: Na PW generowanym ze zlecenia produkcyjnego nie jest uwzględniane ustawienie w definicji dokumentu parametru: Ustalona wartość dostawy. Parametr ten, na PW generowanym ze zlecenia produkcyjnego zostanie zaznaczony wtedy, gdy zostanie ustalony koszt na produkcie (okno: Edycja produktu, pole: Koszt ustalono). Jeżeli na PW wprowadzanych jest kilka produktów, to aby na dokumencie został zaznaczony parametr: Ustalona wartość dostawy, koszt musi być ustalony na wszystkich tych produktach. Uwaga: Możliwe jest generowanie dokumentu PW na kontrahenta, co ułatwia wyszukiwanie dokumentów związanych z produkcją. Funkcja: Generowanie PW po rozliczeniu zlecenia umożliwia wygenerowanie dokumentu PW wraz z rozliczeniem zlecenia. Funkcja dostępna jest z poziomu: Listy zleceń produkcyjnych, Zlecenia produkcyjnego (zakładka Ogólne i Procesy), Harmonogramu operacji. System pozwala na wygenerowanie korekty ilościowej, jak i wartościowej do dokumentu PW. Dokument korekty może zostać wygenerowanie automatycznie podczas zamykania zlecenia lub ręcznie, o ile istnieją ilości lub wartości do skorygowania. W pierwszej kolejności system sprawdza, czy istnieją ilości do skorygowania, i jeżeli istnieją, zostanie utworzony dokument PWK ilościowy. W drugiej kolejności system sprawdza, czy istnieją wartości do skorygowania, i jeżeli istnieją zostanie utworzony dokument PWK wartościowy. Funkcja: Generowanie PWK pozwala na zmniejszenie ilości produktu, jeśli ilość ta jest spięta z dokumentem PW. W przypadku niezgodności między ilością produktu, a ilością spiętą na dokumencie PW udostępniono możliwość generowania dokumentu PWK na tą różnicę. Pod warunkiem jednak gdy, ilość produktu jest mniejsza niż ilość na spiętym z produktem dokumencie PW. Funkcja generowania PWK ze zlecenia produkcyjnego powoduje wygenerowanie korekty wartościowej do dokumentu PW, powiązanego ze zleceniem produkcyjnym. Generowanie PWK jest możliwe w sytuacji, gdy koszt produktu po dokonanym rozliczeniu jest różny od kosztu tego produktu na PW powiązanym ze zleceniem, przy uwzględnieniu wszystkich innych korekt do tego PW. A więc przy określaniu tej różnicy brane są pod uwagę wszystkie korekty do tego PW zarejestrowane w systemie. Dokument PWK można wygenerować ręcznie, za pomocą funkcji: Generowanie PWK, w przypadku różnicy między wartością produktu, a wartością produktu na PW, z uwzględnieniem innych korekt do tego PW. Jeżeli dla takich PW nie zostanie wygenerowana ręcznie PWK, zostanie ona wygenerowana automatycznie podczas zamykania zlecenia. Wygenerowanie dokumentu PWK nie jest jednak wymagane dla zamknięcia zlecenia – operator może anulować generowanie takich PWK. Produkt, który zostanie skorygowany dokumentem PWK będzie wyświetlany w oknie: Edycja produktu, na zakładce: Związane. Funkcja: Generowanie PWK jest dostępna z poziomu: Udostępniono możliwość dołączania odpowiednich elementów zleceń/ harmonogramów do dokumentów AWD i ZWM. Przy realizacji tej funkcjonalności przyjęte zostały jednak pewne ograniczenia – do dokumentów AWD/ZWM można dołączyć elementy pochodzące z dokumentów ZP lub HPR ale tylko wówczas, gdy na tym dokumencie nie dodano jeszcze elementów pochodzących z innych dokumentów. W przeciwnym przypadku, opcje dołączania elementów zleceń będą nieaktywne. Jednocześnie przyjęto również, że jeśli na dokumencie AWD/ZWM dodano już elementy zleceń lub harmonogramów, to dołączenie do takich dokumentów elementów pochodzących z innych dokumentów, niż ZP/HPR nie będzie możliwe. Na dokumentach AWD/ZWM dodano opcje: W module: Produkcja, istnieje możliwość rejestrowania operacji polegających na kooperacji, czyli wykonywania dowolnych prac produkcyjnych przez kontrahenta zewnętrznego w ramach kooperacji. W technologii kooperację można zarejestrować dla: Aby zdefiniować operację kooperacji z technologii należy: Oznaczenie operacji jako kooperacji spowoduje, że po zaplanowaniu zlecenia produkcyjnego w oparciu o technologię, dla której zdefiniowano operację kooperacji, możliwe będzie wygenerowanie z takiego zlecenia, zamówienia zakupu. Po realizacji takiego zamówienia, czyli wygenerowaniu z niego faktury zakupu, koszt wynikający z tej faktury zostanie po przeprowadzeniu rozliczenia automatycznie uwzględniony na zleceniu produkcyjnym źródłowym dla zamówienia zakupu. Aby zdefiniować surowce lub półprodukty/produkty jako pozycje kooperacji należy: Pozycję kooperacji można zdefiniować dla surowców/produktów, które mają przypisaną kartę magazynową, ale również takich, które takiej karty nie mają. Pozycją kooperacji może być tylko koszt lub usługa. Wydanie i przyjęcie z kooperacji nie rejestruje w tym przypadku ruchu magazynowego, a jedynie fakt wydania i przyjęcia półproduktów z kooperacji. Do obsługi kooperacji na zleceniu produkcyjnym służą funkcje dostępne z poziomu Listy zleceń produkcyjnych, Zlecenia produkcyjnego oraz Harmonogramu operacji: Oprócz nich możliwe jest skorzystanie z poziomu listy zleceń produkcyjnych, samego zlecenia oraz harmonogramu operacji z funkcji: Po uruchomieniu funkcji: Wydanie na kooperację, zostanie wygenerowany dokument RW na kooperację. Dokument ten zostanie wygenerowany na pozycje kooperacji zdefiniowane dla surowców, dla których wskazano taką pozycję kooperacji w oknie: Zasób w technologii. Wygenerowanie dokumentu RW na kooperację jest możliwe już po zaplanowaniu operacji, a jeszcze przed jej realizacją. Wygenerowane w takim przypadku RW będzie widoczne w oknie: Operacja, na zakładce: Związane. Dokument zostanie wygenerowany na pozycję kooperacji tej operacji, na której znajduje się kursor. Jeśli kursor znajduje się na procesie, wtedy dokumenty RW na kooperację zostaną wygenerowane do wszystkich operacji w tym procesie. Po uruchomieniu funkcji: Przyjęcie z kooperacji zostanie wygenerowany dokument PW na kooperację. Dokument ten zostanie wygenerowany na pozycje kooperacji zdefiniowane dla produktów, dla których wskazano taką pozycję kooperacji w oknie: Zasób w technologii. Wygenerowanie dokumentu PW na kooperację jest możliwe już po zaplanowaniu operacji, a jeszcze przed jej realizacją. Ze względu na to, że dokument PW rejestruje przyjęcie pozycji kooperacji, a więc dokumentuje przyjęcie półproduktu po kooperacji, w przypadku wygenerowania dokumentu PW na kooperację z operacji planowanej, automatycznie zostanie dodana realizacja tej operacji, jako potwierdzenie jej wykonania. Dokument zostanie wygenerowany na pozycję kooperacji tej operacji, na której znajduje się kursor. Jeśli kursor znajduje się na procesie, wtedy dokumenty PW na kooperację zostaną wygenerowane do wszystkich operacji w tym procesie. Po uruchomieniu funkcji: Zamówienie zakupu na kooperację zostanie wygenerowane zamówienie zakupu na te usługi, które zostały użyte do zdefiniowania operacji w technologii. Aby usługi te były wprowadzone jako pozycje na takie zamówienie, operacji, którą określają, muszą mieć zaznaczony parametr: Kooperacja. Możliwe jest wygenerowanie zamówienia zakupu na kooperację również do takiej operacji, która jeszcze nie została zrealizowana. Na wygenerowane w ten sposób zamówienie można wprowadzać oczywiście również inne pozycje ręcznie. Podczas rozliczania zlecenia zostaną wyszukane te faktury zakupu, które realizują zamówienie zamku wygenerowane z rozliczanego zlecenia. W przypadku odnalezienia takiej faktury koszt z nich wynikający zostanie automatycznie dodany do operacji kooperacja na zleceniu produkcyjnym, w ramach kategorii: Kooperacja. Oczywiście podczas przypisywania kosztu, zostanie przypisana wartość, odpowiadająca ilości operacji na zleceniu produkcyjnym, czyli np. jeżeli na zleceniu jest operacja kooperacji (usługa: Obrabianie) zrealizowana w ilości 3 szt., a na zamówieniu zakupu widnieje ta usługa w ilości 5 szt., to do operacji na zleceniu produkcyjnym zostanie przypisana kwota równa wartości 3 szt. tej usługi. Jeśli na dokumencie realizującym zamówienie na kooperacje TrN_OdliczeniaVat = 0 lub 1 lub 3 to brana jest jego kwota netto, a jeśli TrN_OdliczeniaVat=2 to brana jest jego kwota brutto. Do zamykania zlecenia produkcyjnego dostępne są funkcje: Podczas zamykania zlecenia wykonywane są następujące czynności: W przypadku zamykania zleceń bez rozliczenia i zamykania zleceń niezrealizowanych bez rozliczenia wykonywane są czynności: Na zamkniętym zleceniu, jego pozycje będą dostępne jedynie do podglądu; nie będzie można również wykonywać żadnych operacji z poziomu takiego zlecenia (rozliczania, generowania dokumentów PW, RW itd.). Po zamknięciu zlecenia produkcyjnego, nie będzie możliwości anulowania dokumentów RW i PW, wygenerowanych z tego zlecenia. Zamknięte zlecenie można otwierać. Aby tego dokonać, należy w oknie zamkniętego zlecenia produkcyjnego, na zakładce: Procesy, rozwinąć menu za pomocą przycisku: Podczas zamykania zlecenia, jeżeli na dokumencie RW koszt nie jest ustalony to system sprawdza czy dostawa ma ustaloną wartość. Jeżeli na dokumencie RW jest koszt ustalony to system pozwoli zamknąć zlecenie. W sytuacji, gdy na dokumencie RW wygenerowanym ze ZP jest nieustalona wartość dostawy to w logu informacyjnym podczas zamykania zlecenia produkcyjnego zostaną wyświetlone szczegółowe informacje. W logu będą zawarte informacje na temat przyczyny z powodu której nie można zamknąć zlecenia oraz kod towaru i numer dokumentu. Jeżeli podczas zamykania zlecenia: Od wersji 2015 w Systemie Comarch ERP XL dodano możliwość zamykania niezrealizowanych zleceń produkcyjnych. Funkcja umożliwia zamykanie wszystkich zleceń, tych które można zamknąć za pomocą funkcji „Zamykanie zleceń” oraz tych, na których albo nie zrealizowano wszystkich operacji, albo nie zrealizowano wszystkich pozycji. W dokumencie BST został udostępniony składnik: ZP – S W trakcie produkcji (ZK, ZD, ZP, HPR). Składnik ten prezentuje ilości półproduktów wytworzonych w trakcie produkcji, a jednocześnie takich, które nie są powiązane z innym operacjami (czyli nie są wykorzystane w innych operacjach) i nie zostały wydane do magazynu. Są to zatem półprodukty do wykorzystania. Ilość z tego składnika, ujmowana jest na Bilansie stanu towarów, w kolumnie: Ilość – w drodze. Udostępniono składnik ZP-P Niewykorzystane półprodukty w trakcie produkcji (ZP, HPR). Ten składnik będzie zbierał informacje o półproduktach zaplanowanych i zrealizowanych, dla których nie przewidziano wykorzystania (czyli nie są związane z innymi półproduktami) lub które nie są związane z dokumentami. Jako datę uzyskania tego półproduktu uwzględnia datę: Do, z operacji planowanej, lub realizacji, w której zaplanowano wytworzenie lub wytworzono produkt. Magazyn uwzględniany wg PZA_Magazyn. Składnik ZP-Z Na potrzeby produkcji (ZK, ZD, ZP, HPR) uwzględnia na BST ilości składników zarezerwowanych na potrzeby kompletacji (znajdujących się na potwierdzonym dokumencie ZK), produktów znajdujących się na potwierdzonym dokumencie ZD oraz surowców zarezerwowanych do produkcji (ZP musi być zaplanowane). Ilość uwzględniona jest w kolumnie „zamówiona(-)” oraz w kolumnie „saldo”. Na BST zaznaczenie składnika PLZ Plan zapotrzebowania, spowoduje uwzględnienie na BST ilości towarów wynikającą z planu zapotrzebowania, czyli dokumentów PLZ. Ilość wyświetlana jest w kolumnie „zaplanowana(-)” i uwzględniana w kolumnie „saldo”. Plan zapotrzebowania jest uwzględniany w bilansie rezerwacji towarów, gdy bilans wykonywany jest dla wszystkich magazynów Składnik PLZ-R Realizacja planu zapotrzebowania uwzględnia na BST ilości towarów, które zostały wydane dokumentem WZ/FS/PA/FSE/WZE w ciągu okresu zdefiniowanego w Planie zapotrzebowania na te towary. Ilość uwzględniona jest w kolumnie „zaplanowana” i w kolumnie „saldo”. W sytuacji, gdy na liście dokumentów wewnętrznych istnieje dokument PW, można do niego wygenerować zlecenie produkcyjne. Takie zlecenie służy do ustalenia kosztu produktu przyjętego na tym PW. Uruchomienie funkcji: Generuj ZP jest możliwe z poziomu okna: Lista dokumentów PW: Podczas generowania dokumentu ZP z PW, na zlecenie produkcyjne będą przepisywane wszystkie pozycje znajdujące się na PW. Jeżeli pozycje te nie będą miały zdefiniowanej technologii, na zleceniu nie będzie można ich zaplanować. Brak możliwości planowania dla konkretnych pozycji będzie się utrzymywał do momentu ustalenia technologii według której dany materiał ma być wytwarzany. Po realizacji zlecenia, wygenerowanego z PW, produkty otrzymane na tym zleceniu zostaną automatycznie spięte z pozycjami PW. Wykorzystanie funkcji: Generuj ZP jest możliwe tylko dla potwierdzonych dokumentów PW. W sytuacji, gdy z PW zostało już wygenerowane zlecenie produkcyjne system będzie blokował możliwość wygenerowania kolejnego ZP na te pozycje. W związku z tym, że możliwe jest generowanie ZP z wielu PW został udostępniony mechanizm parametryzacji generowania ZP. Po uruchomieniu funkcji: Generuj ZP, z poziomu listy dokumentów zostanie otworzone okno: Wybierz sposób generowania zleceń. W oknie tym będą znajdować się następujące opcje: Sparametryzowano dotychczasowe działanie systemu w zakresie przenoszenia na dokument ZP elementów ZS/ZW. Do tej pory, na dokument ZP generowany z zamówień, przenoszone były wszystkie towary znajdujące się na tych zamówieniach, niezależnie od tego, czy miały one zdefiniowaną technologię, czy nie. Od wersji 2016.1 Użytkownik może zadecydować, czy na zlecenie mają być przenoszone wszystkie elementy zmówienia, czy tylko te z określoną technologią. W oknie: Generowanie zamówień, wyświetlanym podczas generowania ZP z zamówień, udostępniono parametr: Uwzględniaj tylko pozycje ze zdefiniowaną technologią, którego wartość będzie decydowała o tym, które elementy zamówień zostaną przeniesione na wygenerowane z tych zamówień zlecenie produkcyjne. Z poziomu listy zleceń produkcyjnych możliwe jest generowanie zamówienia zakupu z zaznaczonego zlecenia produkcyjnego. Aby wygenerować zamówienie zakupu ze zlecenia produkcyjnego, należy: W zależności od zaznaczenia na definicji dokumentu realizującego wygenerowane zamówienie, parametru: Przydzielaj tworzone zasoby do rezerwacji, po przyjęciu dostawy zostanie ona przypięta do rezerwacji wynikającej ze zlecenia produkcyjnego. Z poziomu listy zleceń produkcyjnych możliwe jest generowanie zamówienia wewnętrznego z zaznaczonego zlecenia produkcyjnego. Aby wygenerować zamówienie wewnętrzne ze zlecenia produkcyjnego, należy: Lista operacji produkcyjnych umożliwia wyświetlenie listy operacji zaplanowanych i realizacji wyfiltrowanej według wybranego kryterium. Dzięki temu możliwa jest kontrola prawidłowości i terminowości przebiegu procesów produkcyjnych prowadzonych dla różnych zleceń. Z poziomu harmonogramu możliwe jest również wykonywanie operacji do wyświetlonych zadań, takich jak: rozliczenie operacji, generowanie dokumentów PW/RW, realizacja operacji, realizacja terminów oraz dodawanie nowych operacji/realizacji i edycja zarejestrowanych operacji. Na liście wyświetlane są operacje w układzie: W celu udogodnienia pracy z harmonogramem operacji umożliwiono sortowanie wyświetlonych informacji w poszczególnych kolumnach. Od wersji 2018.2.0 zostały dodane nowe kolumny: Postęp i procent realizacji wyświetlamy wg następujących zasad: Dla operacji planowanych – to postęp wynikający z ilości realizacji zarejestrowanych do tej operacji. Te same zasady wyświetlania postępu realizacji stosowane są również na zakładkach [Operacje] oraz [Raport wykonania], udostępnionych w sekcji rozwijanej na liście zleceń produkcyjnych. Dzięki sumowaniu w kolumnie: Czas realizacji możliwe jest np. podsumowanie czasu, w jakim zajęty jest zasób do operacji we wskazanym okresie. Czas realizacji jest prezentowany z podaniem cyfr i liter czyli np.: 2d, 4g, 13m, 15s, jeżeli któraś z wartości wynosi 0, nie jest wyświetlana, sekundy wyświetlane są do 59 sekundy, minuty do 59 minuty, godziny do 23 godzin, czyli jeśli czas operacji wynosi 70 minut, to będzie wyświetlany: 1g 10m. Informacje o statusie operacji na harmonogramie operacji wyświetlone w nowej kolumnie: status. Możliwe filtrowanie na tym oknie operacji planowanych ze względu na ich status. Dzięki tej funkcjonalności możliwa będzie łatwiejsza analiza, które z zaplanowanych operacji są już realizowane. W wersji 2015.0 Systemu Comarch ERP XL harmonogram operacji został wzbogacony o dodatkowe filtry ułatwiające prace z harmonogramem. Dodano filtry wyświetlające operacje niezrealizowane, zrealizowane lub trakcie realizacji. Dodane zostały również parametry służące wyświetlaniu na harmonogramie operacji informacji o operacji poprzedniej i operacji następnej. Funkcje do wykonania na harmonogramie operacji W oknie możliwe jest filtrowanie wyświetlanych operacji według następujących kryteriów: Filtr – za pomocą konstruktora filtra możliwe jest zbudowanie własnego filtra. Termin – w polach: od, do możliwe jest wskazanie przedziału czasowego, który obejmuje część lub całość planowanej/lub zrealizowanej operacji (w zależności od zaznaczenia opcji: Operacji i/lub Realizacje). Zlecenia produkcyjne – po zaznaczeniu opcji na liście będą wyświetlone zlecenia produkcyjne. Harmonogramy projektów – po zaznaczeniu opcji na liście będą wyświetlone harmonogramy projektów. Operacje – po zaznaczeniu opcji na liście będą wyświetlone operacje planowane. Operacje zgrubne – po zaznaczeniu opcji na liście będą wyświetlone operacje zgubne. Realizacja operacji – po zaznaczeniu opcji, na liście będą wyświetlane operacje zrealizowane. Etapy – po zaznaczeniu będą wyświetlane operacje określone jako etapy. Tylko z konfliktami – po zaznaczeniu opcji, na liście będą wyświetlone tylko operacje, dla których po zaplanowaniu został znaleziony konflikt. Parametr będzie aktywny, jeśli zaznaczony zostanie parametr: Wyświetlaj konflikty. Wyświetlaj produkty – po zaznaczeniu parametru w oknie Harmonogramu wyświetlać się będą dodatkowe kolumny: Kod i Nazwa produktu/półproduktu uzyskiwanego w danej operacji. W przypadku operacji zaplanowanych raportowane są tu faktyczne rezerwacje zakupowe na produkty. Jeśli dany wyrób/półprodukt nie ma karty magazynowej, w kolumnie pokazywane są wyroby, jakich zgodnie z technologią, oczekujemy po wykonaniu danej operacji. Dla realizacji operacji w kolumnach wyświetlane są kody wyrobów zrealizowanych. Wyświetlaj konflikty – funkcja umożliwia ograniczenie wyświetlonych informacji – po jego odznaczeniu konflikty nie będą wyświetlane na harmonogramie. Wyświetlaj Operacje poprzednie/następne – po zaznaczeniu parametrów zostaną wyświetlone kolumny poprzednia/następna Rodzaj zasobu– możliwe filtrowanie po rodzaju zasobu przypisanego do gniazda. Pokaż operacje/realizacje z zamkniętych ZP – zaznaczenie spowoduje wyfiltrowanie operacji/realizacji z zamkniętych ZP. Ponadto, na liście możliwe jest wykonanie następujących operacji: W oknie: Lista operacji produkcyjnych na zakładce: Materiały prezentowane są surowce wykorzystane w Zleceniach produkcyjnych. Funkcje dostępne na tej zakładce są analogiczne jak na zakładce: Ogólne. Na zakładce Materiały został dodany parametr Wyświetlaj materiały bez karty magazynowej. Po zaznaczeniu parametru zostaną wyświetlone materiały i półprodukty bez karty magazynowej. Na liście operacji produkcyjnych, w kolumnie: Konflikt, wyświetlane są informacji na temat ewentualnych problemów, które uniemożliwiają realizację produkcji. Informacje te wyświetlane są po sprawdzeniu następujących sytuacji: Konflikty na harmonogramie operacji nie będą uwzględniały braku surowca typu: Koszt i usługa oraz braku materiałów pomocniczych (ze względu na to, że na takie towary, podczas planowania, nie są generowane rezerwacje). Na liście konfliktów uwzględnione są również konflikty wynikające z różnych priorytetów zleceń, np. w przypadku zaplanowania w tym samym czasie dwóch zleceń o różnym priorytecie, do których został dobrany ten sam zasób, zostanie wyświetlona informacja o konflikcie polegającym na tym, że zasób ten został dobrany do operacji o niższym priorytecie. Informacja o takim konflikcie jest wskazówką, że należy wykorzystać funkcję przeplanowania zleceń aby konflikt usunąćDziałanie parametru Wstecz od daty ustalonej na PP/PLZ/BST podczas generowania ZP z PP
Działanie parametru podczas generowania ZP z PLZ
Działanie parametru podczas generowania ZP z BST
Definicja dokumentu ZP, zakładka: Produkcja
[Ustaw domyślny]. Planowane domyślne będzie się wyświetlać na liście w kolorze zielonym.
. Do wyboru:
. Dostępne do wyboru:
Lista zleceń produkcyjnych
. W arkuszu będą znajdować się następujące kolumny: Dokument, Kontrahent – akronim, Kontrahent – miasto, Dokument obcy, Data wystawienia, Data zamknięcia, Produkt, Produkt – nazwa, Zwolnione do produkcji, Status, Projekt.
[Szukaj].
[Planowanie] – obok przycisku znajduje się funkcja
, która rozwija menu, umożliwiająca wykonanie następujących czynności:
[Przeplanowywanie] – obok przycisku znajduje się funkcja
, która rozwija menu, umożliwiająca wykonanie następujących czynności:
[Kolejkowanie zleceń] – okno: Kolejkowanie zleceń, otwierane jest dla zaznaczonych zleceń. Możliwe jest też dodanie zleceń do tego okna. Okno służy ustawieniu kolejności, w jakiej mają zostać planowane/przeplanowane zlecenia. W takiej sytuacji ignorowane będą priorytety na zleceniach, a planowanie będzie się odbywało wg kolejności wskazanej ręcznie przez Użytkownika.
[Ustaw datę planowania]- po zaznaczeniu zlecenie i uruchomieniu funkcji pojawi się okno Ustaw datę planowania, można wskazać datę na jaką dane zlecenie ma zostać zaplanowane.
[Realizacja operacji] – obok przycisku znajduje się funkcja
, która rozwija menu, umożliwiająca wykonanie następujących czynności:
).
[Dołącz do nadzlecenia] – użycie funkcji pozwala na dołączenie zleceń produkcyjnych do nadzlecenia.
[Odłącz od nadzlecenia] – użycie funkcji pozwala na odłączenie zleceń produkcyjnych od nadzleceń.
[Włącz/Wyłącz sumowanie] prezentowanie ilości rekordów w kolumnie LP.
[Zablokuj zasoby] – użycie funkcji powoduje, że zasoby na operacjach planowanych należących do zaznaczonych na liście zleceń zostaną zablokowane, tzn. po przeplanowaniu tych zleceń nie zostaną już zmienione. Funkcjonalność umożliwia realizacje scenariusza, w którym po dobraniu zasobów do operacji chcemy, aby te zasoby realizowały tą operację bez względu na to, czy zmieni się jej termin czy nie. Zasoby pozostaną na operacji mimo przeplanowania i zmiany terminów operacji, o ile zostaną na operacji „zablokowane”.
[Odblokuj zasoby] – użycie funkcji powoduje, że zasoby zostaną odblokowane z operacji, czyli podczas ich przeplanowania mogą zostać zmienione przez inne zasoby, które mogłyby wykonać tą operację szybciej. Funkcja zwolni zasoby z operacji, pochodzących z zaznaczonych zleceń, dla których ta funkcja została uruchomiona.
[Przypisywanie kosztów] – za pomocą funkcji możliwe jest przypisanie kosztów do zlecenia lub wielu zleceń jednocześnie.
[Normatyw a realizacja] – po naciśnięciu przycisku zostanie wyświetlony raport NAR.
[Wykres obciążenia zasobów] zostanie wyświetlony wykres dotyczący obciążenia zasobów.
[Wykres Gantta] – po naciśnięciu przycisku zostanie wyświetlony wykres Gantta dla zleceń produkcyjnych.
[Eksport danych do Excel’a] – po naciśnięciu przycisku:
, możliwe będzie wybranie opcji: Eksport akordów/Eksport czasu przepracowanego, za pomocą których możliwy jest eksport odpowiednich danych do modułu kadrowo – płacowego dokonywany za pośrednictwem arkuszy MS Excel.
[Lista związanych] – po naciśnięciu przycisku zostanie wyświetlona lista dokumentów związanych z zaznaczonym zleceniem produkcyjnym. Z okna Historia związanych możliwy jest również podgląd związanych dokumentów PKJ. Lista dokumentów związanych dostępna jest również po wybraniu odpowiedniej opcji z menu rozwijanego prawym klawiszem myszy.
[Generowanie RW] – obok przycisku znajduje się funkcja:
, która rozwija menu, umożliwiająca wykonanie następujących czynności:
[Zlecenie produkcyjne na materiały/ Zlecenie produkcyjne na półprodukty]- umożliwia wygenerowanie zlecenia produkcyjnego na brakujące materiały, jeśli na zleceniu produkcyjnym zarejestrowano brak potrzebnych materiałów do jego realizacji. Dla pozycji zlecenia będzie podpowiadała się technologia, która jest technologię domyślną dla danego materiału. W przypadku braku takiej, zostanie wprowadzana ostatnia technologia, na jaką zdefiniowano dany materiał.
[Nowy] – funkcja służy wygenerowaniu zlecenia produkcyjnego.
[Karta] – umożliwia podgląd i edycję zaznaczonego na liście zlecenia.
[Usuń] – usuwa zaznaczone na liście zlecenie.
[Rozwiń] rozwijana jest nowa sekcja, w której prezentowana jest lista produktów, materiałów, produktów ubocznych oraz półproduktów wchodzących i wychodzących dla zlecenia zaznaczonego bezpośrednio na głównej liście jak również Operacje i Raport wykonania gdzie wyświetlany jest postęp realizacji. W formie tabelarycznej prezentowane są następujące dane:
Po zaznaczeniu checku, na liście materiałów mają się wyświetlać:
wyświetlane te pozycje dla których ilość w kolumnę Brak jest większa od 0 (różnicą pomiędzy kolumną Ilość a Dostępna dla magazynu źródłowego
[Zlecenie produkcyjne]- zostanie wygenerowane Zlecenie produkcyjne na dany materiał
[Sumuj] – sumowane kolumny Materiały, Ilość, Zrealizowana, Zarezerwowana
[Edycja] – podniesie się okno danego ZP na zakładce Materiały
Po jego zaznaczeniu mają się wyświetlać pozycje zlecenia, dla których:
[Sumuj] –sumowane kolumny Produkt, Ilość na ZP, Zrealizowana, W toku, Do realizacji, Zaplanowana, Do zaplanowania
[Edycja] – zostanie podniesione dane Zlecenie Produkcyjne na zakładce Procesy
[Sumuj] – sumowane kolumny Produkt, kolumny Ilość, Wartość
[Edycja] – podniesie się okno danego ZP na zakładce Procesy
[Usuń] – zostanie usunięty produkt uboczny z danego zlecenia
– zostanie zawężona lista wyświetlanych produktów tylko do tych które mają w kolumnie Brak związanych ilość większą od 0
[Zlecenie produkcyjne]- zostanie wygenerowane Zlecenie produkcyjne na dany półprodukt
[Sumuj] – sumowane kolumny Półprodukt, kolumny Ilość
[Edycja] – podniesie się okno danego ZP na zakładce Procesy
[Zlecenie produkcyjne] – po naciśnięciu przycisku następuje generowanie zlecenie na zaznaczone półprodukty niezależnie od tego, czy są to półprodukty planowane czy zrealizowane. Nie zostało obsłużone generowanie ZP na półprodukty wirtualne. Generowanie ZP na półprodukty wchodzące ma na celu umożliwienie pokrycia zapotrzebowania na brakujące półprodukty. W związku z tym będzie można generować dokumenty dla zaznaczonych półproduktów i będą one generowane na ilość półproduktów wyświetlonych w kolumnie: Ilość/Brak związanych.
[Zlecenie produkcyjne]- zostanie wygenerowane Zlecenie produkcyjne na dany półprodukt
[Sumuj] – sumowane kolumny Półprodukt, kolumny Ilość
[Podgląd] – po jego naciśnięciu:
Czynność Kod półproduktu Zaplanowana Wytworzona Związana Wolna Wykorzystana na innych operacjach Wydana na PW
ZP zostało zaplanowane. Po zaplanowaniu zostało utworzone powiązanie na całość, tj. na 12 szt. między PP1 na operacji poprzedniej (i ten półprodukt wyświetlamy), a PP1 na operacji następnej PP1 12 0 12 0 0 0
Zarejestrowano w całości operację poprzednią, na której zrealizowano w całości PP1 na 12 szt. 0 12 12 0 0 0
Zarejestrowano w całości operację następną, wykorzystano w całości (12 szt.) zrealizowany PP1 w operacji poprzedniej 0 12 12 0 12 0
Kolejkowanie zleceń
.
[Przesuń w górę] i [Przesuń w dół]. Dla zaznaczonych zleceń, dla których ustawiono kolejność można uruchomić planowanie lub przeplanowanie.
[Dodaj do kolejki] i [Usuń z kolejki]. Należy pamiętać, że funkcja:
[Usuń z kolejki] nie powoduje usunięcia zlecenia z bazy (czyli nie powoduje jego wykasowania), a jedynie usunięcie z kolejki zleceń do planowania/przeplanowania.
Filtr na liście materiałów
Kolorowanie wybranych kolumn na liście zleceń produkcyjnych
Budowanie kolejki zleceń za pomocą zapytań SQL
Od wersji 2020.1 została wprowadzona możliwość kolejkowania tych zleceń również automatycznie, wg kryteriów zdefiniowanych przez operatora. W oknie: Kolejka zleceń została dodana sekcja: Ustaw nową kolejkę. W sekcji, w pierwszej kolejności, w combo: Ustaw kolejkę wg, wybieramy zapytanie, wg którego zostanie ustawiona definicja kolejki (opcja: Definicji kolejki) lub dodajemy w tym celu nowe zapytanie (opcja: Nowego zapytania SQL).
Naciśniecie przycisku spowoduje ustawienie kolejki zleceń w górnej części przez kolejkę zleceń w dolnej części okna. Jednocześnie, sekcja z symulacja zostanie wyczyszczona. Jeśli symulowana kolejka nie zostanie zatwierdzona przez Użytkownika, należy nacisnąć przycisk:
Spowoduje to wyczyszczenie dolnej listy w oknie – górna lista zleceń pozostanie bez zmian.
Zlecenie produkcyjne
Zlecenie produkcyjne, zakładka: Ogólne
[Edycja kontrahenta] – umożliwia podgląd i edycję karty kontrahenta głównego lub docelowego. Kontrahent docelowy – kontrahent, dla którego przeznaczony jest realizowany produkt, będący przedmiotem zlecenia. Podanie kontrahenta docelowego nie jest wymagane dla zarejestrowania zlecenia.
– po naciśnięciu przycisku zostaną przypisane zasoby do wygenerowanych rezerwacji, które jeszcze takich zasobów nie maja przypisanych. Parametr będzie nieaktywny, jeśli na definicji dokumenty zlecenia produkcyjnego zostaną odznaczone parametry: Rezerwuj zasoby i Rezerwacje blokują towar na magazynie.
[Planowanie] – obok przycisku znajduje się funkcja
, która rozwija menu, umożliwiająca wykonanie następujących czynności:
[Przeplanowywanie] – obok przycisku znajduje się funkcja
, która rozwija menu, umożliwiająca wykonanie następujących czynności:
[Realizacja operacji] – obok przycisku znajduje się funkcja
, która rozwija menu, umożliwiająca wykonanie następujących czynności:
[Generowanie RW] – obok przycisku znajduje się funkcja:
, która rozwija menu, umożliwiająca wykonanie następujących czynności:
[Włącz/Wyłącz sumowanie] – zostaną zsumowane kolumny LP, Ilość, Ilość w j. pom., Zrealizowana, W toku, Do realizacji, Zaplanowana, Do zaplanowania
[Kalkulacja kosztów] – raport kosztów umożliwiający symulację kosztów produktu.
[Nowy] – umożliwia wprowadzenie na zlecenie produktu. Po naciśnięciu przycisku zostanie otworzone okno: Pozycja zlecenia produkcyjnego, w którym wybiera się produkt, określa jego ilość oraz technologię, jaka zostanie użyta na bieżącym zleceniu do jego realizacji. Po naciśnięciu przycisku:
, zostanie rozwinięte menu, z którego można wybrać opcję: Dodaj produkt oraz Dodaj listę produktów. Umożliwia ona dodanie jednoczenie na zlecenie wielu produktów.
[Karta] – umożliwia podgląd i edycję zaznaczonej na liście pozycji zlecenia (produktu). Po naciśnięciu przycisku, zostanie otworzone okno: Pozycja zlecenia produkcyjnego. W oknie, w do momentu zamknięcia zlecenia, można modyfikować
[Usuń] – umożliwia usunięcie zaznaczonej pozycji zlecenia (produktu)
Zlecenie produkcyjne, zakładka: Operacje
jeżeli operacja została zrealizowana w calości oraz w kolorze czerwonym
jeżeli zostały zarejestrowane już jakieś realizacje. Dla operacji bez realizacji pole jest puste. W przypadku operacji które mają tylko uruchomioną realizację, pasek postępu nie jest wyświetlany.
[Planowanie szczegółowe] – funkcja domyśnie uruchamia planowanie szczegółowe zlecenia, przycisk
umożliwia wybranie funkcji Planowanie uproszczone, Planowanie zgrubne, Planowanie wszystkie zasoby, Planowanie całościowe szczegółowe, Planowanie całościowe uproszczone, Planowanie całościowe zgrubne, Planowanie całościowe wszystkie zasoby.
[Przeplanowywanie szczegółowe] – funkcja domyśnie uruchamia przeplanowywanie szczegółowe zlecenia, przycisk
umożliwia wybranie funkcji Przeplanowywanie uproszczone, Przeplanowywanie zgrubne, Przeplanowywanie wszystkie zasoby, Przeplanowywanie konfliktów szczegółowe, Przeplanowywanie konfliktów uproszczone, Przeplanowywanie konfliktów zgrubne, Przeplanowywanie konfliktów wszystkie zasoby, Dobierz zasoby szczegółowo, Dobierz zasoby wszystkie, Wyszukiwanie nowych terminów – szczegółowe, Wyszukiwanie nowych terminów – wszystkie zasoby.
[Realizacja operacji] – uruchamia realizacje wszytskich operacji.
[Aktualizacja rezerwacji] – uruchamia funkjcę aktualizacji rezerwacji dla całego zlecenia.
[Rozlicz zlecenie] – uruchamia funkcje rozliczająca zlecenie produkcyjne.
[Zamknij zlecenie] – przycisk uruchamia funkcję zamykania zlecenia produkcyjnego wraz z rozliczaniem, przycisk
umożliwia wybranie funkcji Zamykanie niezrealizowanego zlecenia, Zamykanie zlecenia bez rozliczenia, Zamykanie niezrealizowanego zlecenie bez rozliczenia.
[Rozchód wewnętrzny] – przycisk uruchamia generowanie dokumentu RW do zaznaczonych operacji lub do całego zlecenia, jeżeli nie zaznaczono żadnej z operacji. Przycisk
umożliwia wybranie funkcji: Rozchód wewnętrzny z planu, Rozchód wewnętrzny, Wydanie magazynowe z planu, Wydanie magazynowe, Zlecenie wydania z magazynu z planu, Zlecenie wydania z magazynu, Korekta rozchodu wewnętrznego, Spinanie z pozycją dokumentu RW, Wydanie na kooperację.
[Przychód wewnętrzny] – uruchamia generowanie dokumentu PW do zaznaczonych operacji lub do całego zlecenia, jeżeli nie zaznaczono żadnej z operacji. Przycisk
umożliwia wybranie funkcji: Przychód wewnętrzny, Przychód wewnętrzny po rozliczeniu zlecenia, Przyjęcie magazynowe, Awizo dostawy, Korekta przychodu wewnętrznego, Spinanie z pozycją dokumentu PW, Przyjęcie z kooperacji.
[Zamówienie na zakup] – uruchamia generowanie zamówienia zakupu do zaznaczonych operacji lub do całego zlecenia, jeżeli nie zaznaczono żadnej z operacji. Przycisk
umożliwia wybranie funkcji: Zamówienie na zakup, Zamówienie wewnętrzne, Zamówienie na kooperację.
[Zablokuj zasoby] – umożliwia zablokowanie zasobów na zaznaczonych operacjach lub do całego zlecenia, jeżeli nie zaznaczono żadnej z operacji
[Odblokuj zasoby] – umożliwia odblokowanie zasobów na zaznaczonych operacjach lub do całego zlecenia, jeżeli nie zaznaczono żadnej z operacji
[Przypisz koszt] – uruchamia okno koszt, w którym można wskazać kategorię kosztu, jego źródło, wartość oraz klucz według którego koszt zostanie rozbity, w tym kontekście domyślnie będzie wybierane rozbijanie koszty według operacji.
[Wykres obciążenia zasobów] – uruchamia wykres obciążenia zasobów dla wszystkich operacji zaplanowanych na zleceniu produkcyjnym.
[Wykres Gantt’a] – uruchamia wykres Gantt’a dla wszystkich operacji zaplanowanych na zleceniu. Przycisk
umożliwia wybranie funkcji: Wykres Gantt’a, Wykres Gantt’a – wg zasobów i Wykres Gantt’a – wg gniazd roboczych.
[Zasoby dla gniazda roboczego] – dla podświetlonej operacji wyświetla okno ‘Zasoby dla gniazda roboczego’ w którym można przepiąć zasoby z innych operacji.
[Kalkulacja kosztu] – dodaje nowy dokument KLK do zlecenia.
[Uruchom realizację terminu] – uruchamia realizację podświetlonej operacji. Przycisk
umożliwia wybranie funkcji Uruchom realizację terminu bez edycji, Uruchom pozostałe i Uruchom pozostałe bez edycji.
[Realizuj termin] – dodanie realizacji terminu do podświetlonej operacji. Przycisk
umożliwia wybranie funkcji: Realizuj termin, Realizuj etap (dla operacji, która jest etapem), Realizuj wszystkie, Realizuj termin bez edycji, Realizuj wszystkie bez edycji, Realizuj pozostałe, Realizuj pozostałe bez edycji.
[Zmień] – podnosi w trybie do edycji okno z podświetloną operacją.
[Usuń] – umożliwia usunięcie zaznaczonych pozycji, w przypadku braku zaznaczenia zostanie usunięta tylko podświetlona pozycja.
, po jego zaznaczeniu na liście realizacji wyświetlane są tylko te realizacje, do których nie wygenerowano na całą ilość materiału/produktu dokumentu RW i PW.
[Włącz/Wyłącz sumowanie] – sumowane kolumny Ilość i Czas w sekcji Operacje planowane oraz Ilość i Czas w sekcji Raport wykonania, ilośc rekordów w kolumnie Operacja
[Rozchód wewnętrzny] – przycisk uruchamia generowanie dokumentu RW do zaznaczonych operacji lub do całego zlecenia, jeżeli nie zaznaczono żadnej z operacji. Przycisk
umożliwia wybranie funkcji: Rozchód wewnętrzny z planu, Rozchód wewnętrzny, Wydanie magazynowe z planu, Wydanie magazynowe, Zlecenie wydania z magazynu z planu, Zlecenie wydania z magazynu, Korekta rozchodu wewnętrznego, Spinanie z pozycją dokumentu RW, Wydanie na kooperację.
[Przychód wewnętrzny] – uruchamia generowanie dokumentu PW do zaznaczonych operacji lub do całego zlecenia, jeżeli nie zaznaczono żadnej z operacji. Przycisk
umożliwia wybranie funkcji: Przychód wewnętrzny, Przychód wewnętrzny po rozliczeniu zlecenia, Przyjęcie magazynowe, Awizo dostawy, Korekta przychodu wewnętrznego, Spinanie z pozycją dokumentu PW, Przyjęcie z kooperacji.
[Realizuj termin] – dodanie realizacji terminu do podświetlonej operacji. Przycisk
umożliwia wybranie funkcji: Realizuj termin, Realizuj etap (dla operacji, która jest etapem), Realizuj wszystkie, Realizuj termin bez edycji, Realizuj wszystkie bez edycji, Realizuj pozostałe, Realizuj pozostałe bez edycji.
[Zmień] – podnosi w trybie do edycji okno z podświetloną operacją.
[Usuń] – umożliwia usunięcie zaznaczonych pozycji, w przypadku braku zaznaczenia zostanie usunięta tylko podświetlona pozycja.
Zlecenie produkcyjne, zakładka: Procesy
)
)
)
)
)
)
)
)
)
)
)
na zaplanowanej operacji, na zrealizowanej operacji
)
[Etap] – wyświetla operacje oznaczone jako Etap,
[Realizacja] – wyświetla operacje zrealizowane,
[Zasoby] – wyświetla zasoby przydzielone do operacji,
[Surowce] – wyświetla surowce z danego Zlecenia produkcyjnego,
[Półprodukty] – wyświetla półprodukty z danego Zlecenia produkcyjnego,
[Zamienniki] – wyświetla zamienniki z danego Zlecenia produkcyjnego,
[Produkty] – wyświetla produkty z danego Zlecenia produkcyjnego,
[Zabiegi planowane]- wyświetla zabiegi na zaplanowanych operacjach,
[Zabiegi realizowane]- wyświetla zabiegi na operacjach realizowanych.
Komunikaty konfliktów:
[Planowanie] – obok przycisku znajduje się funkcja
, która rozwija menu, umożliwiająca wykonanie następujących czynności:
[Przeplanowywanie] – obok przycisku znajduje się funkcja
, która rozwija menu, umożliwiająca wykonanie następujących czynności:
[Realizacja operacji] – obok przycisku znajduje się funkcja
, która rozwija menu, umożliwiająca wykonanie następujących czynności:
[Generowanie RW] – obok przycisku znajduje się funkcja:
, która rozwija menu, umożliwiająca wykonanie następujących czynności:
[Zablokuj zasoby] – użycie funkcji powoduje, że zasoby na zaznaczonych operacjach planowanych zostaną zablokowane, tzn. po przeplanowaniu operacji nie zostaną już zmienione. Funkcjonalność umożliwia realizacje scenariusza, w którym po dobraniu zasobów do operacji chcemy, aby te zasoby realizowały tą operację bez względu na to, czy zmieni się jej termin czy nie. Zasoby pozostaną na operacji mimo przeplanowania i zmiany terminów operacji, o ile zostaną na operacji „zablokowane”.
[Odblokuj zasoby] – użycie funkcji powoduje, że zasoby zostaną odblokowane z operacji, czyli podczas ich przeplanowania mogą zostać zmienione przez inne zasoby, które mogłyby wykonać tą operację szybciej.
[Przypisywanie kosztów] – za pomocą funkcji możliwe jest przypisanie kosztów do zlecenia lub wielu zleceń jednocześnie.
[Wykres obciążenia zasobów] zostanie wyświetlony wykres dotyczący obciążenia zasobów.
[Wykres Gantta] – po naciśnięciu przycisku zostanie wyświetlony wykres Gantta dla edytowanego zlecenia produkcyjnego.
[Zasoby dla gniazda roboczego] – po naciśnięciu przycisku zostanie wyświetlona lista Zasoby dla gniazda roboczego.
[Raport] – raport kosztów umożliwiający symulację kosztów produktu.
[Uruchom realizację terminu] Obok przycisku znajduje się funkcja
, która rozwija menu, umożliwiająca wykonanie następujących czynności:
[Realizuj termin] Obok przycisku znajduje się funkcja
, która rozwija menu, umożliwiająca wykonanie następujących czynności:
[Dodaj] – umożliwia ręczne planowanie: procesu, operacji z technologii, nowej operacji lub też dodanie realizacji terminu/terminów operacji. Wybór jednej z tych funkcji jest możliwy po naciśnięciu przycisku:
, i uruchomieniu odpowiedniej funkcji. Ponadto w menu rozwijanym obok tego przycisku znajdują się funkcje umożliwiające wykonanie zabiegu lub anulowanie wykonania zabiegu. Zabieg wykonany na realizacji wyświetlany jest w kolorze czarnym, natomiast niewykonany – w kolorze niebieskim.
[Zmień] – umożliwia podgląd i edycję zaznaczonej na zakładce pozycji.
[Usuń] – umożliwia usunięcie zaznaczonej na zakładce pozycji, z zachowaniem poniższych zasad:
[Rozłącz pozycję]).
Zlecenie produkcyjne, zakładka: Materiały
[Generowanie RW] – przycisk uruchamia generowanie dokumentu RW na zaznaczone materiały. Z menu rozwijanego obok przycisku dostępne są funkcje: generowanie RW z planu, RW, spinanie z pozycją dokumentu RW, generowanie RWK, WM z planu, WM, ZWM z planu, ZWM, PW po rozliczeniu zlecenia, zamówienie na zakup, zamówienie wewnętrzne.
[Podgląd] – przycisk otwiera okno: Edycja surowca/produktu.
[Usuń] – przycisk usuwa materiał na którym znajduje się kursor.
– filtr pozwalający na zawężenie listy do materiałów już zrealizowanych (związanych z dokumentami) i niezrealizowanych (niezwiązanych z dokumentami).
Zlecenie produkcyjne, zakładka: Koszty
Zlecenie produkcyjne, zakładka: Nadzlecenia
Zlecenie produkcyjne, zakładka: Opis
Zlecenie produkcyjne, zakładka: Księgowość
Zlecenie produkcyjne, zakładka: Atrybuty
Zlecenie produkcyjne, zakładka: Załączniki
Nadzlecenie produkcyjne
Informacje ogólne
Lista nadzleceń produkcyjnych
[Nadzlecenia produkcyjne]. Na liście dostępne są zakładki: Wg daty, Wg operatora
[Szukaj].
[Włącz/Wyłącz sumowanie] prezentowanie ilości rekordów w kolumnie Dokument.
[Zamknij nadzlecenie] – użycie funkcji zmienia stan nadzlecenia na Zamknięte. Możliwe jest zamknięcie tylko zrealizowanych nadzleceń. Obok przycisku znajduje się funkcja:
, która rozwija menu, umożliwiające wykonanie czynności:
[Dołącz zlecenie] – użycie funkcji pozwala na dołączenie zleceń produkcyjnych do nadzlecenia. Po naciśnięciu przycisku otwierana jest lista zleceń produkcyjnych.
[Odłącz zlecenie] – użycie funkcji pozwala na odłączenie wszystkich zleceń produkcyjnych od nadzlecenia.
[Dodaj] – funkcja służy do generowania nadzlecenia produkcyjnego.
[Zmień] – umożliwia podgląd i edycję zaznaczonego na liście nadzlecenia.
[Usuń] – usuwa zaznaczone na liście nadzlecenie. Możliwe jest usunięcie niezrealizowanych nadzleceń. Podczas usuwania nadzlecenia możliwy jest wybór czy przypisane do nadzlecenie ZP maja zostać odpięte czy usunięte.
Nadzlecenie produkcyjne
[Dodaj] na liście nadzleceń lub za pomocą przycisku:
[Dodaj nadzlecenie], dostępnego na wstążce/pasku narzędzi.
Nadzlecenie produkcyjne, zakładka: Ogólne
[Zamknij nadzlecenie]. Zamknięcie nadzlecenia możliwe jest gdy dokumenty ZP związane z nadzleceniem są zamknięte. Gdy ZP zostanie otwarte, stan dokumenty NZP zostanie zmieniony.
– przycisk aktualizuje dane dotyczące startu, końca i czasu trwania nadzlecenia, ilość zleceń, oraz operacji.
[Planowanie zleceń] – obok przycisku znajduje się funkcja
, która rozwija menu, umożliwiająca wykonanie następujących czynności:
[Przeplanowywanie] – obok przycisku znajduje się funkcja
, która rozwija menu, umożliwiająca wykonanie następujących czynności:
[Kolejkowanie zleceń] – okno: Kolejkowanie zleceń, otwierane jest dla zaznaczonych zleceń. Możliwe jest też dodanie zleceń do tego okna. Okno służy ustawieniu kolejności, w jakiej mają zostać planowane/przeplanowane zlecenia. W takiej sytuacji ignorowane będą priorytety na zleceniach, a planowanie będzie się odbywało wg kolejności wskazanej ręcznie przez Użytkownika.
[Ustaw datę planowania]- po zaznaczeniu zlecenia i uruchomieniu funkcji pojawi się okno Ustaw datę planowania, można wskazać datę na jaką dane zlecenie ma zostać zaplanowane.
[Realizacja operacji] – obok przycisku znajduje się funkcja
, która rozwija menu, umożliwiająca wykonanie następujących czynności:
[Dołącz zlecenie] – użycie funkcji pozwala na dołączenie zleceń produkcyjnych do nadzlecenia. Po naciśnięciu przycisku otwierana jest lista zleceń produkcyjnych.
[Odłącz zlecenie] – użycie funkcji pozwala na odłączenie wszystkich zleceń produkcyjnych od nadzlecenia.
[Włącz/Wyłącz sumowanie] prezentowanie ilości rekordów w kolumnie LP.
[Zablokuj zasoby] – użycie funkcji powoduje, że zasoby na operacjach planowanych należących do zaznaczonych na liście zleceń zostaną zablokowane, tzn. po przeplanowaniu tych zleceń nie zostaną już zmienione. Funkcjonalność umożliwia realizacje scenariusza, w którym po dobraniu zasobów do operacji chcemy, aby te zasoby realizowały tą operację bez względu na to, czy zmieni się jej termin czy nie. Zasoby pozostaną na operacji mimo przeplanowania i zmiany terminów operacji, o ile zostaną na operacji „zablokowane”.
[Odblokuj zasoby] – użycie funkcji powoduje, że zasoby zostaną odblokowane z operacji, czyli podczas ich przeplanowania mogą zostać zmienione przez inne zasoby, które mogłyby wykonać tą operację szybciej. Funkcja zwolni zasoby z operacji, pochodzących z zaznaczonych zleceń, dla których ta funkcja została uruchomiona.
[Przypisywanie kosztów] – za pomocą funkcji możliwe jest przypisanie kosztów do zlecenia lub wielu zleceń jednocześnie.
[Normatyw a realizacja] – po naciśnięciu przycisku zostanie wyświetlony raport NAR.
[Wykres obciążenia zasobów] zostanie wyświetlony wykres dotyczący obciążenia zasobów.
[Wykres Gantta] – po naciśnięciu przycisku zostanie wyświetlony wykres Gantta dla zleceń produkcyjnych.
[Eksport danych do Excel’a] – po naciśnięciu przycisku:
, możliwe będzie wybranie opcji: Eksport akordów/Eksport czasu przepracowanego, za pomocą których możliwy jest eksport odpowiednich danych do modułu kadrowo – płacowego dokonywany za pośrednictwem arkuszy MS Excel.
[Lista związanych] – po naciśnięciu przycisku zostanie wyświetlona lista dokumentów związanych z zaznaczonym zleceniem produkcyjnym. Lista dokumentów związanych dostępna jest również po wybraniu odpowiedniej opcji z menu rozwijanego prawym klawiszem myszy.
[Generowanie RW] – obok przycisku znajduje się funkcja:
, która rozwija menu, umożliwiająca wykonanie następujących czynności:
[Zlecenie produkcyjne na materiały/ Zlecenie produkcyjne na półprodukty]- umożliwia wygenerowanie zlecenia produkcyjnego na brakujące materiały, jeśli na zleceniu produkcyjnym zarejestrowano brak potrzebnych materiałów do jego realizacji. Dla pozycji zlecenia będzie podpowiadała się technologia, która jest technologię domyślną dla danego materiału. W przypadku braku takiej, zostanie wprowadzana ostatnia technologia, na jaką zdefiniowano dany materiał.
[Dodaj] – funkcja służy wygenerowaniu zlecenia produkcyjnego.
[Zmień] – umożliwia podgląd i edycję zaznaczonego na liście zlecenia.
[Usuń] – usuwa zaznaczone na liście zlecenie.
[Włącz/Wyłącz sumowanie] – sumowane kolumny Produkt, Ilość, Ilość w j. pom., Zrealizowana, W toku, Do realizacji, Zaplanowana, Do zaplanowania.
[Kalkulacja kosztu] – dodaje nowy dokument KLK do zlecenia.
[Edycja zlecenia] – edycja zlecenia produkcyjnego dla pozycji zlecenia.
[Edycja pozycji] – edycja pozycji zlecenia.
[Usuń] – usuwa zaznaczone pozycje.
[Włącz/Wyłącz sumowanie] prezentowanie ilości rekordów w kolumnie Operacja, Ilość, Czas.
[Zablokuj zasoby] – użycie funkcji powoduje, że zasoby na operacjach planowanych należących do zaznaczonych na liście zleceń zostaną zablokowane, tzn. po przeplanowaniu tych zleceń nie zostaną już zmienione. Funkcjonalność umożliwia realizacje scenariusza, w którym po dobraniu zasobów do operacji chcemy, aby te zasoby realizowały tą operację bez względu na to, czy zmieni się jej termin czy nie. Zasoby pozostaną na operacji mimo przeplanowania i zmiany terminów operacji, o ile zostaną na operacji „zablokowane”.
[Odblokuj zasoby] – użycie funkcji powoduje, że zasoby zostaną odblokowane z operacji, czyli podczas ich przeplanowania mogą zostać zmienione przez inne zasoby, które mogłyby wykonać tą operację szybciej. Funkcja zwolni zasoby z operacji, pochodzących z zaznaczonych zleceń, dla których ta funkcja została uruchomiona.
[Rozchód wewnętrzny z planu] – przycisk uruchamia generowanie dokumentu RW z planu do zaznaczonych operacji. Przycisk
umożliwia wybranie funkcji: Rozchód wewnętrzny z planu, Wydanie magazynowe z planu, Zlecenie wydania z magazynu z planu.
[Zamówienie na zakup] – uruchamia generowanie zamówienia zakupu do zaznaczonych operacji. Przycisk
umożliwia wybranie funkcji: Zamówienie na zakup, Zamówienie wewnętrzne, Zamówienie na kooperację.
[Uruchom realizację terminu] – uruchamia realizację podświetlonej operacji. Przycisk
umożliwia wybranie funkcji Uruchom realizację terminu bez edycji, Uruchom pozostałe i Uruchom pozostałe bez edycji.
[Realizuj termin] – dodanie realizacji terminu do podświetlonej operacji. Przycisk
umożliwia wybranie funkcji: Realizuj termin, Realizuj etap (dla operacji, która jest etapem), Realizuj wszystkie, Realizuj termin bez edycji, Realizuj wszystkie bez edycji, Realizuj pozostałe, Realizuj pozostałe bez edycji.
[Realizuj zaznaczone operacje] – uruchamia realizacje zaznaczonych operacji.
[Edycja zlecenia] – edycja zlecenia produkcyjnego dla operacji.
[Zmień] – podnosi w trybie do edycji okno z podświetloną operacją.
[Usuń] – umożliwia usunięcie zaznaczonych pozycji, w przypadku braku zaznaczenia zostanie usunięta tylko podświetlona pozycja.
[Włącz/Wyłącz sumowanie] prezentowanie ilości rekordów w kolumnie Operacja, Ilość, Czas.
[Rozchód wewnętrzny] – przycisk uruchamia generowanie dokumentu RW do zaznaczonych operacji. Przycisk
umożliwia wybranie funkcji: Rozchód wewnętrzny, Wydanie magazynowe, Zlecenie wydania z magazynu, Korekta rozchodu wewnętrznego, Spinanie z pozycją dokumentu RW, Wydanie na kooperację.
[Przychód wewnętrzny] – przycisk uruchamia generowanie dokumentu PW do zaznaczonych operacji. Przycisk
umożliwia wybranie funkcji: Przychód wewnętrzny, Przychód wewnętrzny po rozliczeniu zlecenia, Przyjęcie magazynowe, Awizo dostawy, Korekta przychodu wewnętrznego, Spinanie z pozycją dokumentu PW, Przyjęcie z kooperacji.
[Realizuj termin] – dodanie realizacji terminu do podświetlonej operacji. Przycisk
umożliwia wybranie funkcji: Realizuj termin, Realizuj etap (dla operacji, która jest etapem), Realizuj wszystkie, Realizuj termin bez edycji, Realizuj wszystkie bez edycji, Realizuj pozostałe, Realizuj pozostałe bez edycji.
[Edycja zlecenia] – edycja zlecenia produkcyjnego dla realizacji.
[Zmień] – podnosi w trybie do edycji okno z podświetloną realizacją.
[Usuń] – umożliwia usunięcie zaznaczonych realizacji, w przypadku braku zaznaczenia zostanie usunięta tylko podświetlona pozycja.
[Zlecenie produkcyjne]- zostanie wygenerowane Zlecenie produkcyjne na dany materiał
[Sumuj] – sumowane kolumny Materiał, Ilość, Zrealizowana, Do realizacji, Zarezerwowana.
[Edycja] – podniesie się okno danego ZP na zakładce Materiały
Nadzlecenie produkcyjne, zakładka: Nagłówek
Nadzlecenie produkcyjne, zakładka: Atrybuty
Operacja w technologii, zakładka: Załączniki
Kolejkowanie nadzleceń i budowanie kolejki nadzleceń za pomocą zapytań SQL
Realizacja zlecenia
Generowanie zlecenia produkcyjnego
; w polu obok zostanie wyświetlona pełna nazwa produktu.
[Przelicz ilość w j. podstawowe]- umożliwia przeliczenie ilości w jednostce podstawowej.
, wyświetlone do wyboru będą wszystkie technologie, które są aktywne (zaznaczony parametr: Aktywny) i które jako produkt wynikowy mają zdefiniowany produkt, będący przedmiotem zlecenia. Na zakres wyświetlanych technologii ma również wpływ wskazanie cechy dla produktu wprowadzanego na zlecenie. Jeżeli cecha zostanie określona, możliwe będzie wybranie tylko takiej technologii, która przewiduje wytworzenie produktu o wskazanej cesze, lub produkt której ma zaznaczony przez wskazanej cesze parametr: Edycja cechy przy realizacji.
[Edycja kontrahenta] – umożliwia podgląd i edycję karty kontrahenta głównego lub docelowego.
[Zapisz zmiany].
Pobieranie domyślnej technologii podczas dodawani pozycji na zlecenie produkcyjne
Planowanie zlecenia produkcyjnego
Informacje ogólne
, znajdującego się obok funkcji:
[Planowanie zlecenia]. Wygenerowanie planowania zlecenia możliwe jest z poziomu zlecenia produkcyjnego, lub z listy zleceń produkcyjnych.
Czynności wykonywane podczas planowania zlecenia
Wyszukiwanie zasobów podczas planowania
Uwzględnienie w planie produkcji czasu potrzebnego na realizację dostaw
Warunki uwzględniane w obsłudze planowania z wiązaniem wolnych ZZ/ZW
Planowanie szczegółowe
Planowanie uproszczone
Planowanie zgrubne
Przeplanowywanie konfliktów
, znajdującego się obok przycisku:
).
.
Dodawanie procesu i operacji
(obok przycisku:
) funkcji:
Planowanie w partiach
Planowanie w określonych odstępach czasowych między operacjami
Planowanie według dat, jako priorytetów
Proces zlecenia produkcyjnego
Proces, zakładka: Ogólne
Proces, zakładka: Koszty
Proces, zakładka: Kalkulacje kosztu
Proces, zakładka: Opis
Proces, zakładka: Atrybuty
Proces, zakładka: Załączniki
Operacja planowana – edycja
Operacja planowana, zakładka: Ogólne
Statusy operacji
Operacja planowana, zakładka: Operacje powiązane
[Wykres Gantt’a] – po naciśnięciu przycisku zostanie wyświetlone okno z wykresem Gantt’a.
dodano możliwość uruchomienia funkcji przeplanowującej dla zaznaczonych na liście operacji. Dodakowo za pomoca przycisku
możliwe jest wyświetlenie w trybie do odczytu okna wskazanej operacji.
Operacja planowana, zakładka: Zasoby
[Zablokuj zasoby] - użycie funkcji powoduje, że zasoby na zaznaczonych operacjach planowanych zostaną zablokowane, tzn. po przeplanowaniu operacji nie zostaną już zmienione. Funkcjonalność umożliwia realizacje scenariusza, w którym po dobraniu zasobów do operacji chcemy, aby te zasoby realizowały tą operację bez względu na to, czy zmieni się jej termin czy nie. Zasoby pozostaną na operacji mimo przeplanowania i zmiany terminów operacji, o ile zostaną na operacji „zablokowane”.
[Odblokuj zasoby] - użycie funkcji powoduje, że zasoby zostaną odblokowane z operacji, czyli podczas ich przeplanowania mogą zostać zmienione przez inne zasoby, które mogłyby wykonać tą operację szybciej
[Przeplanowywanie] – uzycie przeplanuje zasoby, dobierze zasoby
[Lista wykorzystania zasobu] - jeżeli na zasobie został zaznaczony parametr: Rejestrować wydanie, wtedy po naciśnięciu przycisku zostanie wyświetlona lista: Wykorzystanie zasobu, na której możliwe jest rejestrowanie wydania i zdania zaznaczonego zasobu przez wybranego pracownika
[zasoby dla gniazda roboczego] – funkcja otwiera okno wykorzystania wskazanego zasobu.
[Nowy] – umożliwia dodanie gniazda roboczego i przypisanego do niego zasobu do planowanej operacji. Po naciśnięciu przycisku kursor ustawi się w kolumnie: gniazdo robocze, w której należy wskazać odpowiednie gniazdo z menu rozwijanego przyciskiem:
(dostępne będą tylko te gniazda, które zostały przypisane do operacji na technologii – zobacz rozdział: ). Po zatwierdzeniu wyboru gniazda, kursor przenosi się do kolumny: Zasoby, w której należy wskazać zasób, spośród przypisanych do danego gniazda. Do wyboru zostaną wyświetlone te zasoby, które są dostępne na czas planowanej operacji.
[Karta] – po naciśnięciu przycisku zostanie wyświetlone okno: Zasób w produkcji, w którym wyświetlone są dane zasobu oraz koszty przypisane i rozbite na zasób. Z poziomu okna istnieje możliwość przypisywania dodatkowych kosztów.
[Usuń] – usuwa zaznaczoną pozycje z zakładki.
Operacja planowana, zakładka: Rezerwacje
. Gdy minie termin ważności rezerwacji, staną się one nieaktywne. Rezerwacje nie są generowane dla surowców – półproduktów. W przypadku zamykania zlecenia i niezrealizowania dodatkowych (ponad ilość wynikającą z operacji zrealizowanych) rezerwacji na produkty i surowce, zostaną usunięte te rezerwacje.
[Przepnij zasoby z innych rezerwacji] -Otwiera okno Lista zasobów do przepięcia dla danego towaru.
[Wygeneruj rezerwacje] – funkcja pozwala na wygenerowanie rezerwacji sprzedażowych na surowiec (w panelu górnym) oraz zakupowych na produkty (w panelu dolnym). Podczas generowania rezerwacji będą brane pod uwagę ilości surowca i produktu wynikające z ilości zaplanowanych operacji przy uwzględnieniu już zrealizowanych rezerwacji.
[Zarezerwuj zasoby] – funkcja umożliwia powiązanie rezerwacji z zasobem.
[Zwolnij zasoby] – funkcja umożliwia zwolnienie zasobów.
[Nowy] – umożliwia ręczne dodanie rezerwacji na wybrany towar.
[Karta] – wyświetla wybraną rezerwację do edycji.
[Usuń] – usuwa wskazaną rezerwację.
[Dodaj]. Zostanie otworzone okno: Rezerwacja zostanie dodana, w którym należy wskazać nazwę zasobu, określić zarezerwowaną ilość, parametry rezerwacji oraz wskazać zasób z listy zasobów otwieranej za pomocą przycisku:
[Zmień dostawę].
[Rozwija menu dostępnych opcji], znajdującego się obok przycisku:
. Po wybraniu gniazda roboczego Zasób, wyświetlona jest lista zasobów, przewidziana w technologii, co skraca czas wyszukania odpowiedniego towaru.
Operacja planowana, zakładka: Półprodukty
[Podgląd] - Wywołuje okno ‘Edycja półproduktu’
[Suma] – Sumuje ilości w danej kolumnie niezależnie od jednostki w jakiej jest prezentowany.
Operacja planowana, zakładka: Zabiegi
Operacja planowana, zakładka: Koszty
Operacja planowana, zakładka: Związane
[Generowanie RW] – z menu obok przycisku mamy możliwość skorzystania z kliku opcji: Generowanie RW z planu, WM z planu, ZWM z planu.
[Podgląd] – funkcja umożliwia podgląd związanego dokumentu.
[Rozłącz pozycję] – funkcja umożliwia rozłączenie dokumentu RW, WM od zlecenia produkcyjnego.
[Usuń] – przycisk wywołujący usuwanie dokumentów.
Operacja planowana, zakładka: Opis
Operacja planowana, zakładka: Atrybuty
Operacja planowana, zakładka: Załączniki
Operacja planowana – materiały, półprodukty, produkty
Okno: Edycja półproduktu wychodzącego
nie jest dostępne do edycji, przycisk podnosi w trybie do podglądu powiązaną kartotekę towarową.
Okno: Edycja półproduktu przychodzącego
nie jest dostępne do edycji, przycisk podnosi w trybie do podglądu powiązaną kartotekę towarową.
zaznaczona operacja wyświetlana jest w trybie do podglądu.
Aktualizacja rezerwacji
, znajdującego się obok przycisku:
, i wybrać z niego funkcję: Aktualizuj rezerwacje.
Realizacja operacji
Działanie funkcji: Realizacja operacji
, znajdującego się obok przycisku:
.
.
Blokada możliwości realizacji operacji
Realizacja terminów
, znajdują się opcje realizacji terminów:
Realizacja terminu
Realizacja etapu
Realizacja wszystkich terminów
Realizacja terminu bez edycji
Realizacja wszystkich bez edycji
Realizuj pozostałe
Realizuj pozostałe bez edycji
Opis okna: Realizacja
Realizacja, zakładka: Ogólne
[Dodaj] możliwe jest dodanie terminu realizacji, również wtedy, gdy operacja nie jest zaplanowana na wiele terminów (odznaczony parametr: Wiele terminów, w oknie: Operacja w technologii, na zakładce: Ogólne).
Realizacja, zakładka: Zasoby
[Lista wykorzystania zasobu] – jeżeli na zasobie został zaznaczony parametr: Rejestrować wydanie, wtedy po naciśnięciu przycisku zostanie wyświetlona lista: Wykorzystanie zasobu, na której możliwe jest rejestrowanie wydania i zdania zaznaczonego zasobu przez wybranego pracownika
[zasoby dla gniazda roboczego] – funkcja otwiera okno wykorzystania wskazanego zasobu.
[Nowy] – umożliwia dodanie gniazda roboczego i przypisanego do niego zasobu do planowanej operacji. Po naciśnięciu przycisku kursor ustawi się w kolumnie: gniazdo robocze, w której należy wskazać odpowiednie gniazdo z menu rozwijanego przyciskiem:
(dostępne będą tylko te gniazda robocze, które zostały przypisane do Operacji w technologii. Po zatwierdzeniu wyboru gniazda roboczego kursor przenosi się do kolumny: Obiekty, w której należy wskazać obiekt, spośród przypisanych do danej funkcji. Do wyboru zostaną wyświetlone te zasoby, które są dostępne podczas realizacji operacji.
[Karta] – umożliwia zmianę zaznaczonego na zakładce gniazda roboczego lub zasobu.
[Usuń] – usuwa zaznaczoną pozycję z zakładki.
Realizacja, zakładka: Materiały
[Nowy], znajdujących się w odpowiednich panelach. Dodanie zasobów, które nie były uwzględnione na Operacji w technologii, jest możliwe, jeżeli dla tej Operacji został zaznaczony parametr: Dowolne materiały. Na zakładce znajdują się filtry proste umożliwiające wyszukiwania materiałów po kodzie i nazwie.
[Generuj RW] – umożliwia wygenerowanie dokumentów RW na surowce użyte w technologii. Z menu rozwijanego obok przycisku można wygenerować następujące funkcje: generowanie RWK, WM, ZWM, wydanie na kooperację, spinanie z pozycją dokumentu RW. Po wywołaniu funkcji: Spinanie z pozycją dokumentu RW, dla zaznaczonych na liście surowców zostanie wyświetlone okno: Lista dokumentów RW. Po wybraniu RW zostanie on podpięty do zaznaczonych na liście surowców. Funkcja jest możliwa do wywołania dla tych surowców, które nie zostały jeszcze całościowo spięte z dokumentami RW.
[Generuj PW] – umożliwia wygenerowanie dokumentów PW na produkty. Z menu rozwijanego obok przycisku można wygenerować następujące funkcje: generowanie PWK, PM, AWD, przyjęcie z kooperacji, spinaj z pozycją PW. Po wywołaniu funkcji: Spinanie z pozycją dokumentu PW, dla zaznaczonych na liście produktów zostanie wyświetlone okno: Lista dokumentów PW. Po wybraniu PW zostanie on podpięty do zaznaczonych na liście produktów. Funkcja jest możliwa do wywołania dla tych produktów, które nie zostały jeszcze całościowo spięte z dokumentami PW.
[Karta] – otwiera do edycji okno: Karta surowca/Karta produktu.
[Usuń] – usuwa zasób z realizacji (np. gdy w trakcie realizacji okaże się, że dany zasób nie był wykorzystywany).
Realizacja, zakładka: Zabiegi
[Wykonaj zabieg]. Zabiegi wykonane wyświetlane są w kolorze czarnym, natomiast zabiegi niewykonane wyświetlane są w kolorze niebieskim.
Realizacja, zakładka: Opis
Realizacja, zakładka: Atrybuty
Realizacja, zakładka: Załączniki
Edycja Surowca/Produktu
Uwagi ogólne
Edycja Surowca/Produktu, zakładka: Ogólne
, umożliwiający wskazanie jako materiału, towaru z zarejestrowaną kartą towaru (dodanie takiego materiału, będzie możliwe wtedy, gdy na Operacji w technologii, w oparciu o którą następuje realizacja, został zaznaczony parametr: Dowolne materiały lub w przypadku wprowadzania zamiennika – wtedy parametr: Dowolne materiały nie musi być zaznaczony). W przypadku podmiany surowca na zamiennik podpowiadana będzie ilość tego zamiennika zgodnie ze ilością wskazaną w technologii.
[Drukuj] uruchamia domyślny wydruk, podpięty na zakładce: Ogólne w oknie: Edycja Produktu
[Aktualizuj numer partii/seryjny]. Domyślnie wskazany jest wzorzec wybrany na technologii.
Edycja Surowca, zakładka: Rezerwacje
[Zmień dostawę] – funkcja umożliwia przypisanie nowego zasobu do istniejącej rezerwacji.
[Rezerwuj zasoby] – funkcja umożliwia przypisanie zasobu do rezerwacji.
[Zwolnij zasoby] – funkcja powoduje zwolnienie zasobów z rezerwacji.
[Podgląd] – funkcja umożliwia otworzenie do edycji rezerwacji.
[Usuń] – użycie funkcji spowoduje połączenie „usuwanej” rezerwacji z inna rezerwacją. Funkcja jest aktywna, gdy dla zasobu zostało wygenerowano wiele rezerwacji.
Edycja Surowca/Produktu, zakładka: Kontrahenci
Edycja Surowca/Produktu, zakładka: Koszty
Edycja Surowca/Produktu, zakładka: Związane
[Podgląd związanego dokumentu] – funkcja umożliwia podgląd związanego z zasobem dokumentu.
[Zwiąż z innym zasobem/Zwiąż z pozycją dokumentu RW/PW] – w zależności od tego, skąd pochodzi zasób, aktywna będzie odpowiednia funkcja, po użyciu której zostanie wyświetlona do wyboru lista z odpowiednimi obiektami. Podczas spinania dokumentów brana jest pod uwagę ilość zasobu, która już została spięta na innym dokumencie lub zasobie. Niemożliwe jest wiązanie zasobów z dokumentami, które są w buforze. Po związaniu z zasobem lub dokumentem, w oknie wyświetlone są nr zlecenia/kod technologii/kod operacji związanego zasobu lub numer związanego dokumentu.
dostępna jest również opcja wiązania materiału z dokumentem kooperacji.\
[Rozłącz pozycję] – użycie funkcji powoduje usunięcie powiązania ze wskazaną pozycją.
[Usuń] – funkcja umożliwiająca usunięcie dokumentu.
Edycja Surowca/Produktu, zakładka: Atrybuty
Aktualizacja nr partii/seryjnych
Generowanie RW
Generowanie RW z planu
Spinanie RW/PW z realizacją – spinanie do surowców/produktów
Generowanie RWK
Generowanie WM/ZWM z planu
Generowanie WM/ZWM
Generowanie PM/AWD
Generowanie PW
Generowanie PW po rozliczeniu zlecenia
Generowanie PWK
Dołączanie pozycji z ZP i HPR na dokumenty AWD/ZWM
Rejestracja kooperacji
Operacja w technologii – Kooperacja
Pozycje kooperacji
Rejestracja kooperacji na zleceniu produkcyjnym
Wydanie na kooperację
Przyjęcie z kooperacji
Zamówienie zakupu na kooperację
Zamykanie zlecenia
obok przycisku:
i wybrać z niego funkcję: Otwarcie zlecenia.
Składniki w BST
Składnik w BST W trakcie produkcji
Składnik w BST Niewykorzystane półprodukty w trakcie produkcji
Składnik w BST Na potrzeby produkcji
Składnik w BST Plan zapotrzebowania
Składnik w BST Realizacja planu zapotrzebowania
Generowanie ZP z PW
Obsługa funkcji: Generuj ZP
Parametryzacja funkcji: Generuj ZP
Przenoszenia elementów z zamówień na ZP
Uzupełnianie surowców produkcyjnych w trakcie produkcji
Generowanie zamówień zakupu ze zleceń produkcyjnych
Sposób optymalizacji
Uwzględnij pozycje
Uwzględnij
Inne
Generowanie zamówień wewnętrznych ze zleceń produkcyjnych
Uwzględnij pozycje
Uwzględnij
Inne
Wybierz magazyn źródłowy
Harmonogram operacji
Informacje ogólne
– umożliwia zawężenie wyświetlanych operacji/realizacji, w skład których wchodził wybrany towar lub produkt.
– umożliwia zawężenie wyświetlanych operacji/realizacji według projektu wskazanego na zaleceniu, z którego pochodzą.
– możliwe jest wyświetlenie listy operacji, w których użyty został wybrany zasób. Wyboru dokonuje się po naciśnięciu przycisku i wybraniu z listy odpowiedniego zasobu lub wpisaniu jego kodu.
– możliwe jest wyświetlenie listy operacji planowanych/realizowanych w wybranym oddziale. Wyboru się po naciśnięciu przycisku i wybraniu z listy odpowiedniego oddziału lub wpisaniu jego kodu.
– możliwe jest wyświetlenie listy operacji planowanych/realizowanych opartych o wybraną Operację w technologii. Aby wybrać tą Operację, należy najpierw wskazać technologię, w której została ona zdefiniowana.
– na liście można wyświetlić również konkretne zlecenie. Jego wybór następuje poprzez naciśnięcie przycisku i wybór z listy lub wprowadzenie w polu jego numeru. Obok przycisku znajduje się funkcja: , która rozwija menu, umożliwiające wyświetlenie konkretnego nadzlecenia.
[Pozostaw okno na wierzchu] – dane okno nie zostanie zamknięte, będzie na wierzchu okien.
[Zablokuj zasoby] – użycie funkcji powoduje, że zasoby na operacjach planowanych należących do zaznaczonych na liście zleceń zostaną zablokowane, tzn. po przeplanowaniu tych zleceń nie zostaną już zmienione. Funkcjonalność umożliwia realizacje scenariusza, w którym po dobraniu zasobów do operacji chcemy, aby te zasoby realizowały tą operację bez względu na to, czy zmieni się jej termin czy nie. Zasoby pozostaną na operacji mimo przeplanowania i zmiany terminów operacji, o ile zostaną na operacji „zablokowane”.
[Odblokuj zasoby] – użycie funkcji powoduje, że zasoby zostaną odblokowane z operacji, czyli podczas ich przeplanowania mogą zostać zmienione przez inne zasoby, które mogłyby wykonać tą operację szybciej. Funkcja zwolni zasoby z operacji, pochodzących z zaznaczonych zleceń, dla których ta funkcja została uruchomiona.
[Zasoby dla gniazda] – po naciśnięciu przycisku zostanie wyświetlona lista Zasoby dla gniazda roboczego.
[Przeplanowywanie] – funkcja umożliwiająca przeplanowywanie. Z menu rozwijanego obok przycisku, dostępne są opcje umożliwiające planowanie: szczegółowe, uproszczone, zgrubne, wszystkie zasoby, przeplanowywanie konfliktów: szczegółowe, uproszczone, zgrubne, wszystkie zasoby, dobranie zasobów szczegółowe oraz zasobów wszystkich, wyszukiwanie nowych terminów-szczegółowe, wyszukiwanie nowych terminów-wszystkie zasoby.
[Przeplanuj powiązane] – funkcja umożliwia przeplanowywanie powiązanych. Z menu rozwijanego obok przycisku, dostępne są opcje:
[Rozlicz operację] – funkcja służy realizacji zaznaczonej na liście operacji. Z menu rozwijanego obok przycisku, dostępne są opcje umożliwiające: realizację operacji oraz rozliczenie operacji.
[Wykres obciążenia zasobów] zostanie wyświetlony wykres dotyczący obciążenia zasobów.
[Wykres Gantt’a] – po naciśnięciu przycisku zostanie wyświetlone okno z wykresem Gantt’a. Wykres będzie uwzględniał filtry zastosowane w oknie: Harmonogram operacji, np. jeśli harmonogram zostanie wyświetlony dla zasobu: AA, to wykres Gantt’a zostanie wyświetlony również tylko dla tego zasobu.
[Przypisywanie kosztu] – funkcja umożliwiająca dodanie kosztu do wybranych operacji produkcyjnych.
[Włącz/Wyłącz sumowanie] – funkcja sumująca kolumny Operacja, Czas realizacji, Ilość oraz na zakładce Materiały kolumna Kod, Ilość, Zrealizowano.
[Generuj dokument RW] – przycisk służący wygenerowaniu dokumentu RW. Z menu rozwijanego obok przycisku dostępne są następujące funkcje: Generowanie RW z planu, RW, spinanie z pozycją dokumentu RW, generowanie RWK, WM z planu, WM, PW, spinanie z pozycją PW, generowanie PM, PWK, wydanie na kooperację, przyjęcie z kooperacji, zamówienie na zakup, zamówienie wewnętrzne, zamówienie na kooperację.
[Dodaj] – funkcja służy realizacji terminu, dla operacji/realizacji zaznaczonej na liście. Realizacja terminów odbywa się według tych samych zasad, co na zleceniu produkcyjnym. Z menu rozwijanego obok przycisku, dostępne są opcje umożliwiające realizację wszystkich terminów, pojedynczego terminu bez jego edycji, wszystkich terminów bez edycji oraz dodawanie operacji planowanej.
[Karta] – otwiera do podglądu/edycji zaznaczoną na liście realizację/operację
[Usuń] – usuwa zaznaczoną na liście operację lub realizację (jeżeli istnieje realizacja do zaznaczonej operacji, to aby ją usunąć, należy najpierw usunąć realizację).
Informacje o konfliktach