Czy wiesz, że w Comarch ERP XL możliwe jest zdefiniowanie gniazd roboczych w sposób zapewniający kontynuację pracy zasobu w kolejnych operacjach produkcyjnych?
Kontynuacja pracy zasobu
Na karcie gniazda roboczego produkcyjnej został dodany parametr Kontynuacja pracy zasobu.
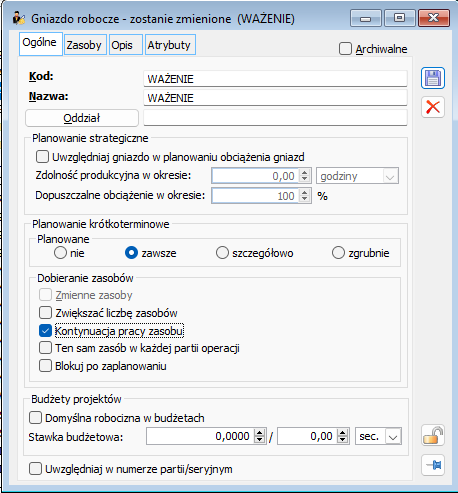
Domyślne ustawienie parametru jest przenoszone na gniazdo dodaną do operacji w technologii.
Na karcie operacji dla przypisanego gniazda roboczego parametr Kontynuacja pracy jest dostępny do edycji.
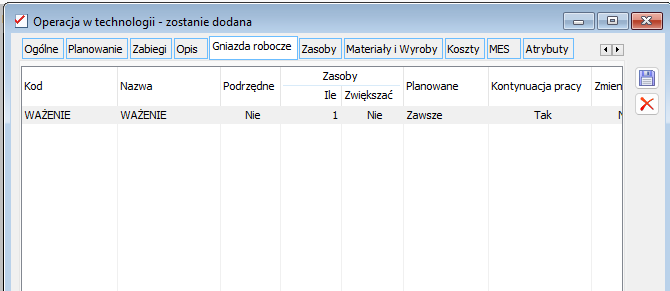
Kontynuacja pracy zasobu jest możliwa, gdy operacje mają przypisane to samo gniazdo robocze oraz są ze sobą powiązane, czyli np. jedna dostarcza półproduktów dla drugiej.
W przypadku, gdy zlecenie jest planowane w przód oraz na gniazdo robocze przypisanej do danej operacji parametr kontynuacji pracy ustawiony jest na Tak, to sprawdzane jest czy na operacjach poprzedzających (dostarczających półprodukty do danej operacji) jest dobrany zasób pełniący to samo gniazdo. Jeżeli spełniony jest opisany warunek, to zasób ten jest dobierany również do danej operacji z uwzględnieniem okresu jego dostępności, a następnie wyznaczany jest termin planowanej operacji. Przy planowaniu wstecz do operacji dobierany jest ten sam zasób, który został dobrany do następnej lub kolejnej operacji po danej, jak poprzednio sprawdzane jest powiązanie operacji półproduktami oraz pełnienie przez zasób tego samego gniazda, uwzględniany jest również okres dostępności zasobu.
Poniżej przykład technologii, w oparciu o którą podczas planowania zlecenia będzie uwzględniona kontynuacja pracy zasobu.
Przykład: Zasób Z1 jest dostępny we wtorki oraz w czwartki godzinach 8.00 – 16.00, zasób Z2 jest dostępny w środy w godzinach 9.00 – 17.00. Na gnieździe roboczym F zaznaczony jest parametr Kontynuacji pracy zasobu oraz dodane są zasoby Z1, Z2. Na operacjach O1, O2 w technologii T1 jest przypisane gniazdo F. Operacje O1, O2 są powiązane półproduktem P1,, na każdej czas planowany i rozliczeniowy wynosi 8 godzin. Na operacjach dla gniazda F parametr kontynuacji pracy ma wartość Tak.
W opisanym przypadku, przy planowaniu w przód, uwzględniane jest ustawienie parametru kontynuacji pracy na gnieździe F w operacji O2, natomiast dla planowania wstecz uwzględniane jest ustawienie parametru kontynuacji pracy na gnieździe F w operacji O1.
Po zaplanowaniu zlecenia w przód na podstawie danej technologii do operacji O1 został dobrany zasób Z1 i na podstawie okresu jego dostępności wyznaczony termin danej operacji. Do operacji O2 również został dobrany zasób Z1 i wyznaczony jej termin z uwzględnieniem okresu dostępności danego zasobu. Jeżeli na operacji O2 wartość parametru Kontynuacji pracy byłaby na Nie, to po zaplanowaniu zlecenia w przód do operacji O2 zostałby dobrany zasób Z2 i termin operacji wyznaczony z uwzględnieniem okresu jego dostępności. Należy zauważyć, że przy włączonej Kontynuacji pracy do operacji O2 zastał dobrany zasób Z1, podczas gdy zasób Z2 mógłby ją realizować wcześniej.
Czy wiesz, że w systemie Comarch ERP XL, możliwe jest przeniesienie materiałów na zlecenie produkcyjne w takiej kolejności jak zostało to ustalone w technologii?
W Systemie Comarch ERP XL umożliwiono wyświetlanie materiałów na zleceniu produkcyjnym w kolejności takiej w jakiej ustawione zostały na technologii produkcyjnej. Jak dotąd osiągnięcie takiego efektu było możliwe wyłącznie w sytuacji gdy kody surowców rozpoczynały się od kolejnych liter alfabetu.
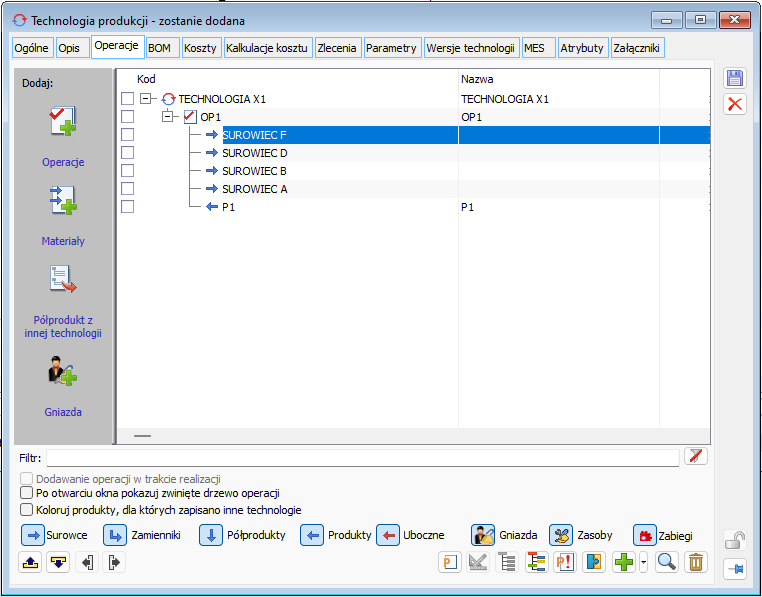
Za funkcjonalność wyświetlania materiałów na ZP w takiej kolejności jak na TP odpowiedzialny jest parametr:

Parametr dostępny jest na zakładce Procesy na zleceniu produkcyjnym obok przycisku
. Przy odznaczonym parametrze System wyświetla materiały jak dotąd, w kolejności alfabetycznej, zaznaczenie parametru powoduje wyswietlenie materiałów w kolejności takiej jak na technologii produkcji.
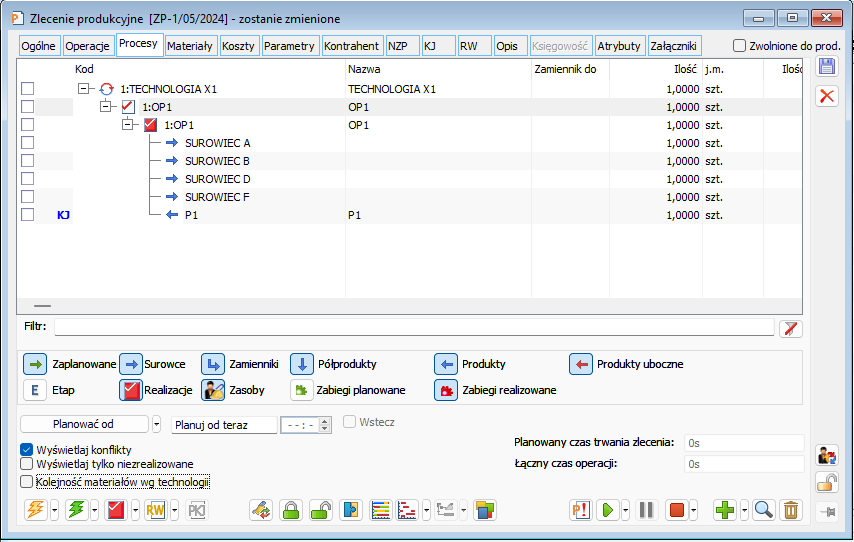
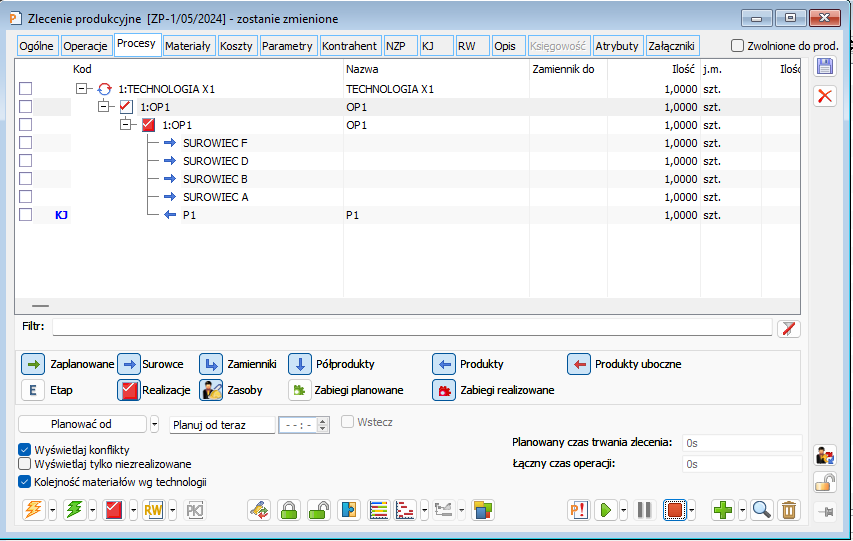
Czy wiesz, że w Comarch ERP XL można planować zlecenia produkcyjne z uwzględnieniem czasu potrzebnego na realizację dostaw?
Uwzględnianie w planie czasu potrzebnego na realizację dostaw
Jeśli na definicji dokumentu ZP, na zakładce Inne zostanie zaznaczony parametr ‘Podczas planowania wiąż z wolnymi ZZ/ZW’, wówczas w planie zostanie uwzględniony czas potrzebny na dostawę surowców zamówionych dokumentami zamówień do dostawców lub zamówień wewnętrznych do innych oddziałów.
Podczas planowania zleceń, system sprawdza czy są zarejestrowane jakiekolwiek ZZ lub ZW na surowce, nie powiązane jeszcze z żadnym ZP lub innym obiektem w systemie, a następnie ustala termin realizacji operacji produkcyjnych zgodnie z planowaną dostępnością surowców na podstawie dat realizacji pozycji zamówienia. Po zaplanowaniu zlecenia na podstawie dokumentów ZZ i ZW następuje powiązanie zamówienia ze zleceniem tak, że przy kolejnym planowaniu innego zlecenia nie są uwzględniane te same zamówienia. Jeśli w momencie planowania zlecenia produkcyjnego nie ma w systemie zarejestrowanych zamówień zakupu lub wewnętrznych na potrzebny do procesu produkcyjnego surowiec, to ZP zaplanuje się wyłącznie w oparciu o dostępność zasobów produkcyjnych. Po wygenerowaniu zamówień na brakujące materiały i przeplanowaniu zlecenia, system uwzględni czas realizacji określony na pozycjach zamówień i odpowiednio je powiąże.
Przykład – Zamówienie zakupu
W systemie zarejestrowane jest ZZ1 na surowiec S1 na ilość 10szt. z datą realizacji 22.07.2024 oraz surowiec S2 na ilość 20szt. z datą realizacji 27.07.2024. Zostaje zaplanowane zlecenie (od teraz, czyli 02.05.2024) na 10szt. Produktu końcowego. Według planu wychodzi, że zgodnie z dostępnością zasobów produkcyjnych operacja, która potrzebuje surowca S1 i S2 mogłaby się rozpocząć w dniu 27.07.2024. W związku z tym, że na żadnym magazynie nie ma surowca to system sprawdza czy są zarejestrowane potwierdzone ZZ nie powiązane z żadnym obiektem. W logu podczas planowania zalecenia pojawia się stosowna informacja o powiązaniu elementów ze zleceniem.
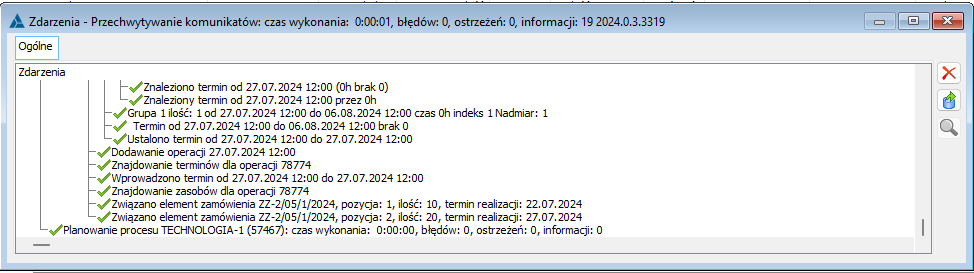
Zlecenie zostaje zaplanowane na dzień 27.07.2013, ponieważ jest to najpóźniejsza data realizacji zamówienia, na godzinę 12:00, ponieważ jest to domyślna godzina.
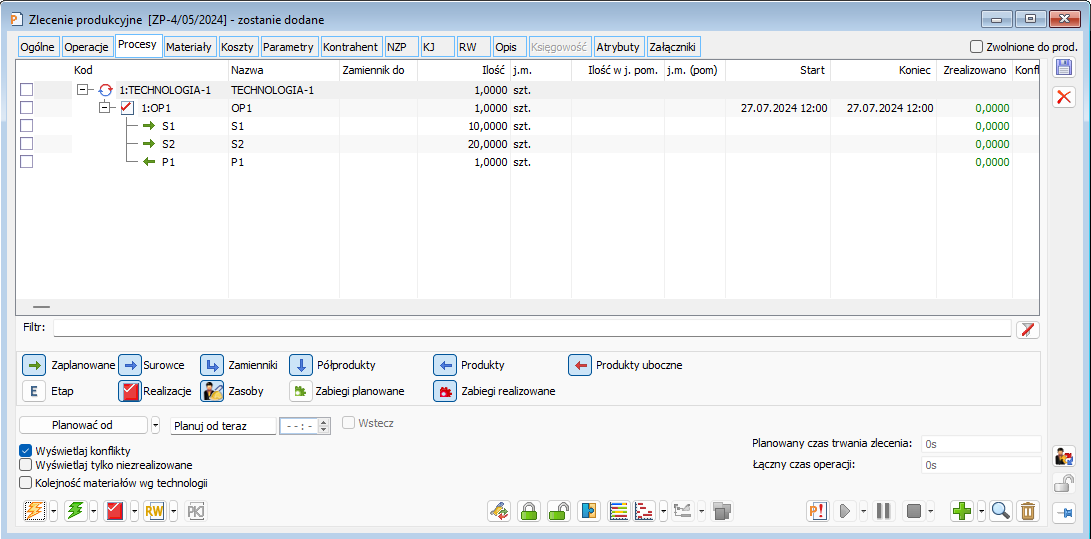
Z poziomu zamówienia z zakładki Powiązania możliwe jest sprawdzenie jakie elementy z jakim zleceniem produkcyjnym zostały powiązane.
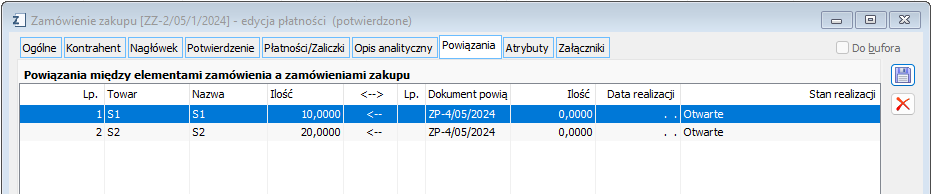
Czy wiesz, że w systemie Comarch ERP XL istnieje możliwość wyświetlania szczegółów wybranej technologii lub zlecenia produkcyjnego w formie tabelarycznej?
W systemie Comarch ERP XL jest udostępniona prezentacja listy zleceń produkcyjnych oraz listy technologii. Funkcjonalność pozwala na wyświetlenie w formie tabelarycznej szczegółów dotyczących dokumentu wybranego na liście.
Aby wyświetlić szczegóły technologii z poziomu listy technologii należy zaznaczyć na liście wybrany dokument,
a następnie nacisnąć przycisk:
[Rozwiń]. Przycisk uruchamia sekcję, w której prezentowana jest lista materiałów dla technologii zaznaczonej na liście.
Na zakładce: Ogólne sekcji wyświetlane są dane nagłówkowe technologii. W przypadku, gdy otwarta jest zakładka: Ogólne, wówczas na liście BOM wyświetlane są wszystkie materiały przewidziane w wybranej technologii.
Jeśli natomiast otwarta jest zakładka: Operacje, która zawiera listę operacji danej technologii, wtedy na liście BOM, materiały wyświetlane są kontekstowo dla zaznaczonej operacji.
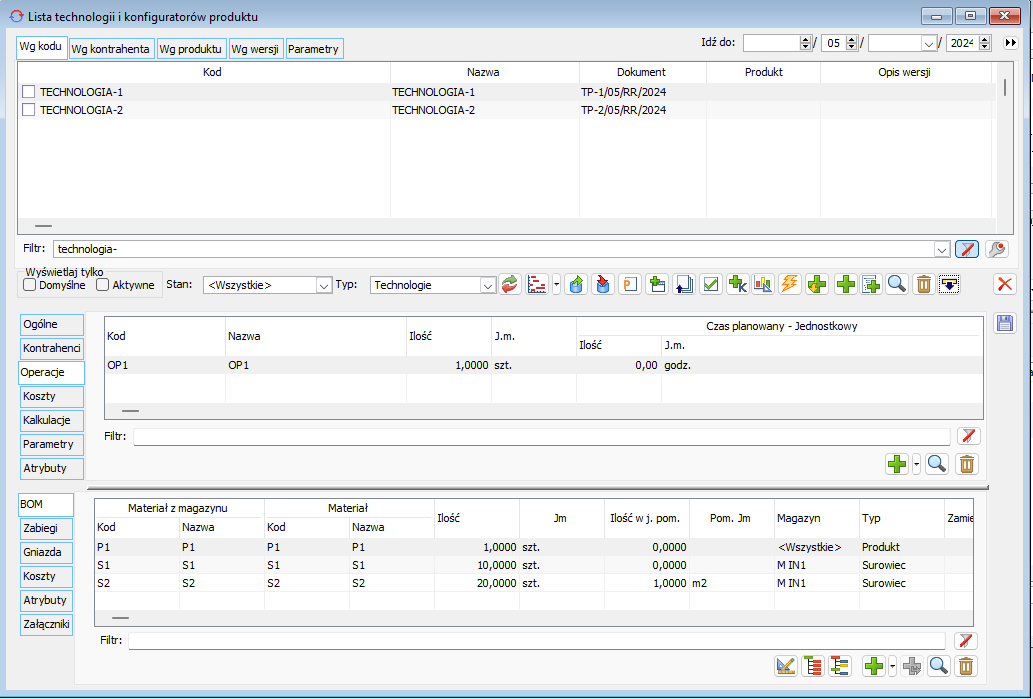
Dodatkowo możliwe jest edytowanie pozycji wyświetlonych w sekcjach.
Podobne jak na liście technologii, prezentacja dokumentów jest na liście zleceń produkcyjnych.
Aby wyświetlić szczegóły zlecenia z poziomu listy zleceń produkcyjnych należy zaznaczyć na liście wybrany dokument:
a następnie nacisnąć przycisk:
[Pokaż szczegóły zlecenia].

W sekcji wyświetlane są zbiorczo stany materiałów danego zlecenia na magazynach źródłowych (z technologii) oraz braki na magazynach źródłowych, wynikające z różnic między ilością, która jest potrzebna do zlecenia, a zrealizowaną ilością materiałów. Oprócz stanów materiałów na magazynach źródłowych, prezentowane są informacje o stanach tych materiałów na wszystkich magazynach.
Czy wiesz, że istnieje możliwość zablokowania realizacji operacji produkcyjnej w przypadku, gdy ilość potrzebnych surowców lub półproduktów jest niewystarczająca?
Blokada realizacji operacji, gdy brakuje surowców
Jeżeli w określonej operacji surowce potrzebne do wytworzenia produktu nie są dostępne w wystarczającej ilości np. nie ma ich w ogóle na magazynach, brakuje lub są już na nie rezerwacje zasobowe, to istnieje możliwość zablokowania realizacji takiej operacji. Blokowanie dodawania realizacji w takim przypadku jest możliwe po przypisaniu na operatorze zakazu o nazwie Realizacja operacji przy braku surowców. Wtedy przy próbie realizacji operacji sprawdzany jest warunek dostępności wszystkich potrzebnych surowców, a gdy nie jest on spełniony realizacja nie zostaje dodana i pojawia się stosowny komunikat.
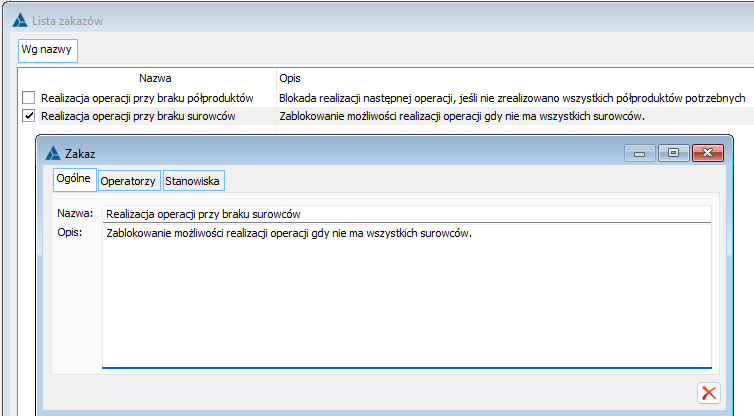
Przykład1: W technologii na operacji do wytworzenia jednej sztuki produktu P1 potrzebne jest 10 sztuk surowca S1 oraz 20 sztuk surowca S2. Surowiec S1 jest dostępny w ilości 7 sztuk, a surowiec S2 w ilości 12 sztuk. Zostało wystawione zlecenie produkcyjne na 1 sztukę P1, następnie zaplanowane w oparciu o technologię . Rezerwacje na surowiec S1 na 7 sztuk oraz S2 na 12 sztuk mają przypisane zasoby. Przy próbie dodania realizacji pojawia się stosowna informacja i realizacja nie zostaje dodana.
Brakuje 3 sztuki surowca S1 oraz 8 sztuk surowca S2. Po uzupełnieniu brakującej ilości surowców dodanie realizacji jest już możliwe.
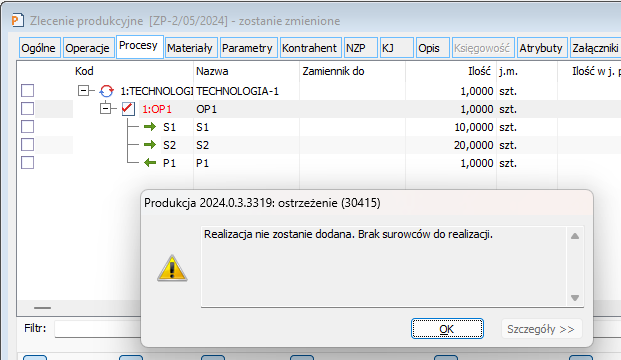
Blokada realizacji, gdy brakuje półproduktów
Jeżeli półprodukty będące surowcami w określonej operacji są powiązane z produktami poprzednich operacji w ilości niewystarczającej do wytworzenia produktu końcowego z tej operacji, to istnieje możliwość zablokowania dodania realizacji takiej operacji. W tym celu należy na operatorze dodać zakaz Realizacji operacji przy braku półproduktów. Wtedy przy dodawaniu operacji sprawdzany jest warunek dostępności półproduktów – czy ich ilość powiązana z produktami w poprzednich operacjach pozwala na realizację całości zaplanowanej operacji. Gdy warunek ten nie jest spełniony realizacja nie zostaje dodana i pojawia się informacja o przyczynie i brakującej ilości półproduktu.
Przykład2: W technologii na operacji wytwarzana jest jedna sztuka półproduktu PP1 potrzebna w następnej operacji do wytworzenia jednej sztuki produktu końcowego P1. Zostało wystawione zlecenie produkcyjne na 10 sztuk produktu P1 następnie zaplanowane w oparciu o technologię. Operacja pierwsza została zrealizowana w ilości trzech sztuk i ilość wytworzonego na niej półproduktu PP1 wynosi 3 sztuki. Dodanie realizacji operacji drugiej na 10 sztuk jest zablokowane w takim przypadku, a przy próbie pojawia się stosowny komunikat. Do pełnej realizacji operacji drugiej i wytworzenia 10 sztuk produktu P1 potrzebne jest jeszcze 7 sztuk surowca-półproduktu PP1 z poprzedniej operacji. Jeżeli zostanie dodana realizacja operacji pierwszej na pozostałe 7 sztuk i łączna ilość wytworzonego półproduktu PP1 będzie równa 10 sztuk, to dodanie realizacji operacji drugiej będzie już możliwe.
Jeżeli na operatorze zostanie dodany każdy z wymienionych zakazów, to przy dodawaniu realizacji będzie sprawdzany warunek dostępności surowców oraz warunek dostępności półproduktów i jak wcześniej w przypadku braku ich spełnienia realizacje nie zostaną dodane. Gdy na operacji pierwszej w technologii z drugiego przykładu do wytworzenia jednej sztuki produktu PP1 będzie potrzebna jedna sztuka surowca S1, który nie jest dostępny, to realizacje operacji pierwszej, drugiej nie zostaną dodane ponieważ brakuje 10 sztuk surowca S1 oraz 10 sztuk półproduktu PP1 z operacji pierwszej.
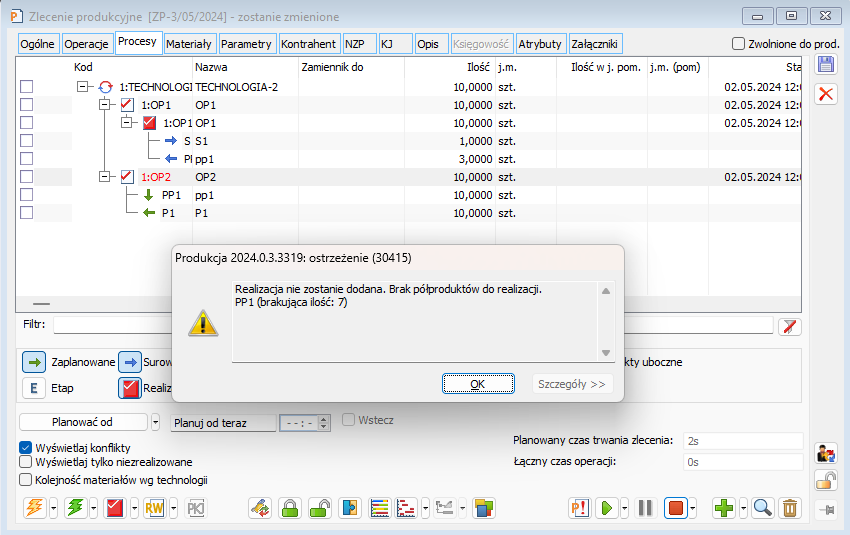
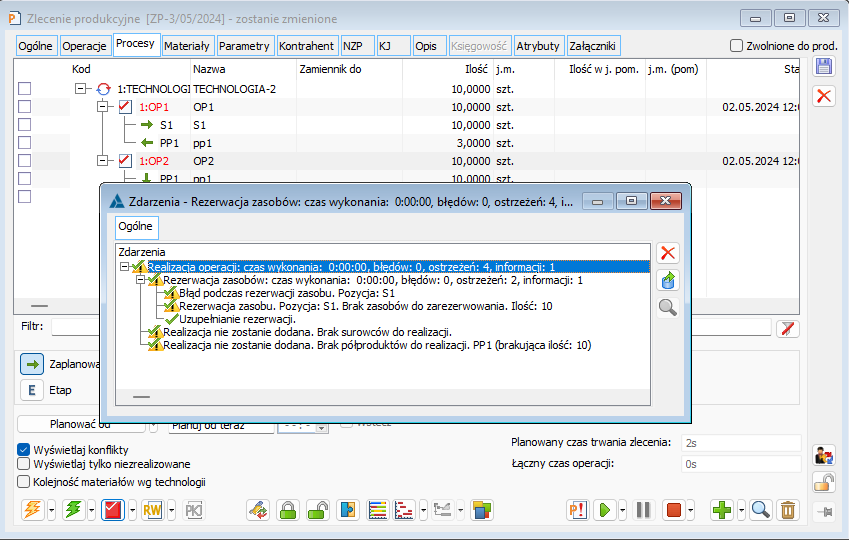
Czy wiesz, że można zablokować możliwość edycji technologii po uruchomieniu zlecenia, na którym zostanie wykorzystana?
Definicje dokumentów TP i KPR
W momencie uruchomienia zlecenia produkcyjnego, tj. po dodaniu pierwszej realizacji operacji, technologia, w oparciu o którą dodana została realizacja, może być w pełni zablokowana do edycji. Odpowiada za to parametr: Edycja po uruchomieniu produkcji, umieszczony na zakładce: Ogólne definicji dokumentów TP i KPR.
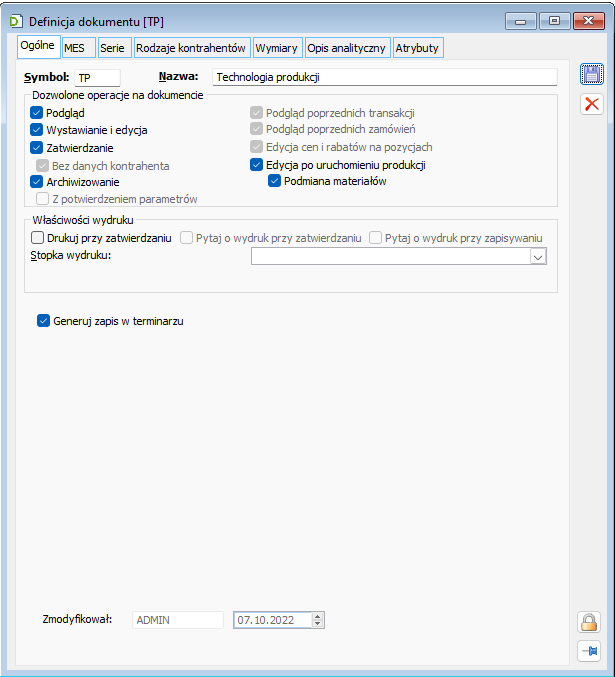
Niezależnie od tego czy umożliwiono edycję technologii po uruchomieniu produkcji, na technologii, na podstawie której uruchomiono produkcję, nie ma możliwości zmiany materiału ani z listy materiałów na operacji, ani poprzez formatkę: Materiał w technologii.
Czy wiesz, że w systemie Comarch ERP XL możliwe jest skonfigurowanie stawki za nadgodziny w produkcji?
Stawka specjalna
W systemie Comarch ERP XL możliwe jest skonfigurowanie stawki za nadgodziny przy wykorzystaniu stawki specjalnej na gnieździe.
Konfiguracja
W module Produkcja na liście zleceń należy dodać dwa gniazda powiązane z tym samym zasobem. Przykładowo gniazdo F1-malowanie powiązana jest z zasobem PR3, oraz gniazdo F2-malowanie powiązana jest zasobem PR3.
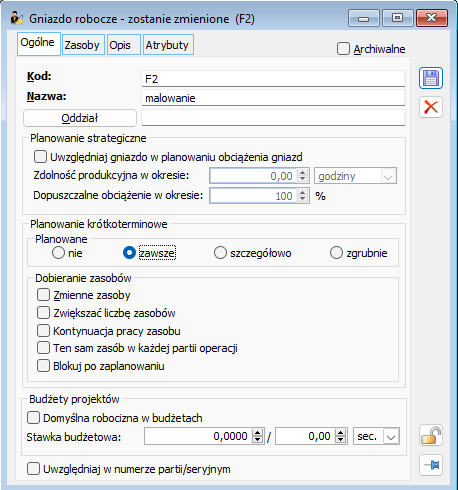
W oknie Zasób należy określić normalną stawkę za godzinę np.10 PLN/1 godzinę.
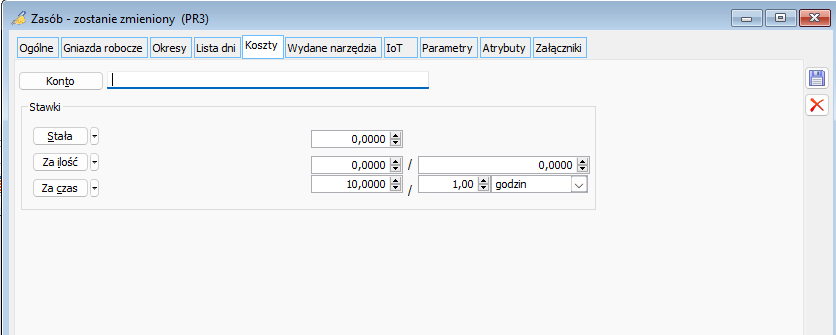
Dodatkowo na zasobie można ustawić kalendarz dostępności pracownika, np. codziennie w dni robocze pomiędzy godziną 7:00 a 15:00.
W oknie Edycja gniazda zasobu należy zaznaczyć parametr „Stosować stawki specjalne dla gniazda” oraz określić stawkę za nadgodziny np. 20 PLN/1 godzinę.
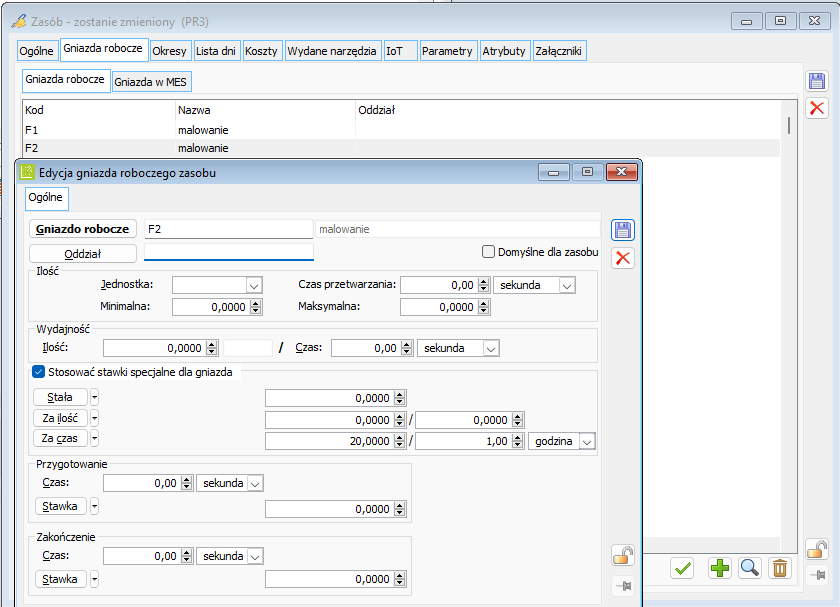
Ustawienia na technologii
Na technologii w oknie operacji w technologii na zakładce Gniazda należy dodać F1-malowanie oraz F2-malowanie oraz na operacji zaznaczyć Wiele terminów.
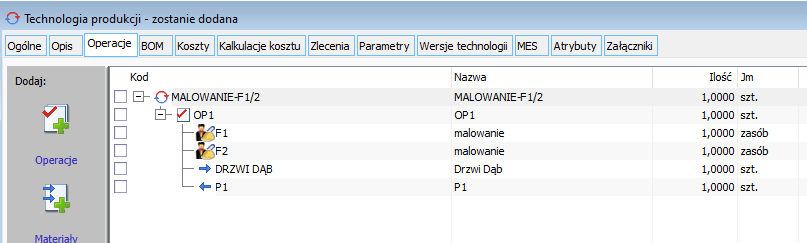
Realizacja na zleceniu produkcyjnym
Na zleceniu produkcyjnym przykładowo zostało zaplanowana 3 szt. wyrobu gotowego.
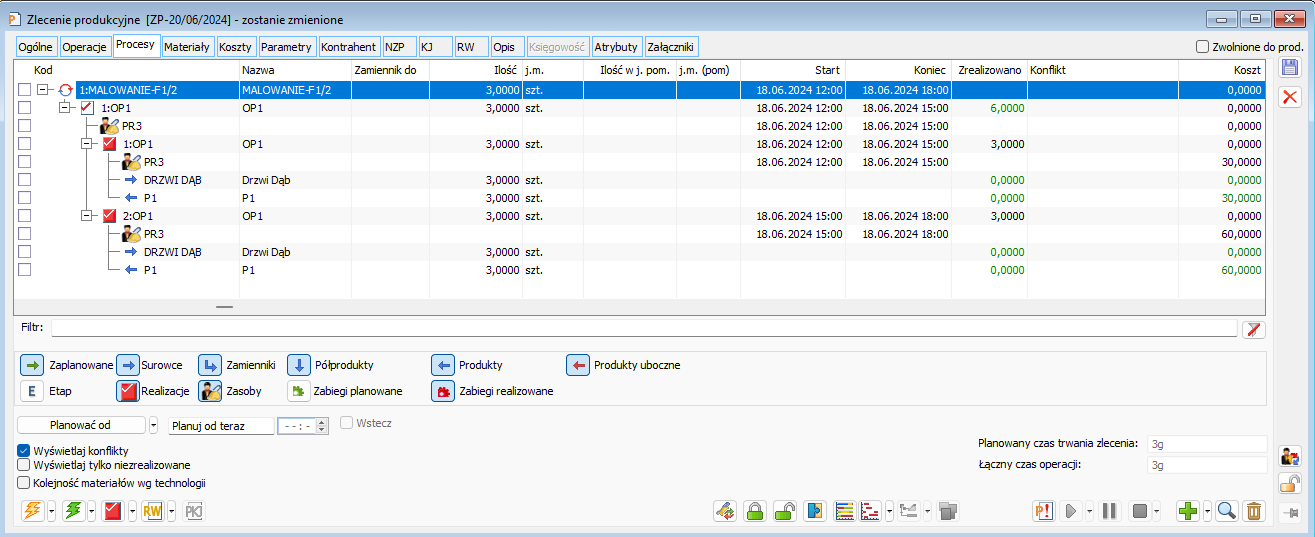
Realizacja operacji została rozbita ręcznie na dwie realizacje, jedna od godz. 12:00 do 15:00, czyli ta w której będzie brana pod uwagę normalna stawka za godzinę według gniazda F1 10PLN/godz., oraz druga od godz. 15:00 do 20:00 z gniazdem F2, czyli ta w której będzie brana pod uwagę stawka specjalna za nadgodziny 20PLN/godz.
Po rozliczeniu koszt związany z gniazdem zostanie prawidłowo przypisany.
Czy wiesz, że w systemie Comarch ERP XL możliwe jest definiowanie w Technologii materiałów o stałej ilości?
W Comarch ERP XL jest funkcjonalność pozwalająca na definiowanie stałej ilości materiałów w Technologii. Na karcie materiału (surowca) w Technologii jest udostępniony parametr: Stała ilość, decydujący o tym, czy surowiec podczas planowania będzie uwzględniany w stałej ilości, czy też ilość będzie przeliczana tak, jak ilość innych surowców w stosunku do ilości produktu i operacji:
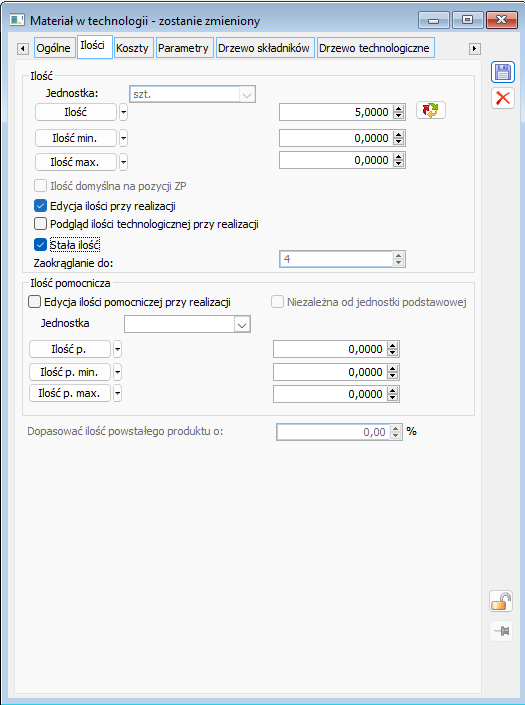
Po zaznaczeniu parametru: Stała ilość dla materiału w Technologii, na zleceniu, które zostanie zaplanowane w oparciu o tą Technologię, zostanie zarezerwowana taka ilość materiału, jaką określono w polu: Ilość na formatce: Materiał w technologii, na zakładce: Parametry.
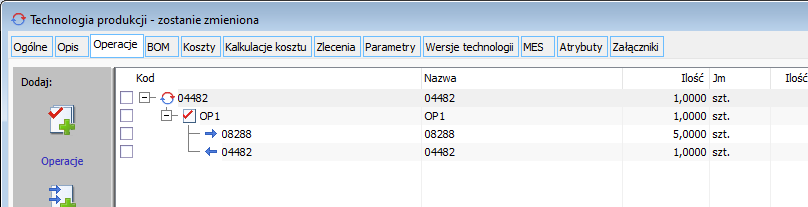
Stała ilość materiału po zaplanowaniu zlecenia jest taka jak zdefiniowana w technologii:
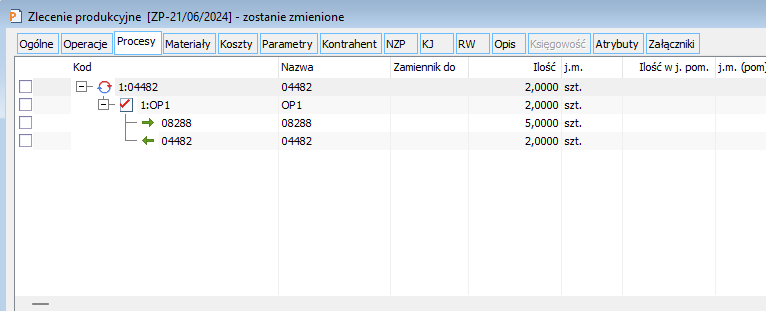
Czy wiesz, że w module Produkcja istnieje możliwość automatycznego przenoszenia numeru seryjnego określonego na zakładce: Ogólne ZP na produkt wytwarzany w ramach tego zlecenia?
W celu uzyskania omawianej funkcjonalności, po dodaniu produktu do technologii, na formatce: Materiał w technologii, jako wartość Cechy należy wybrać <Numer seryjny>:
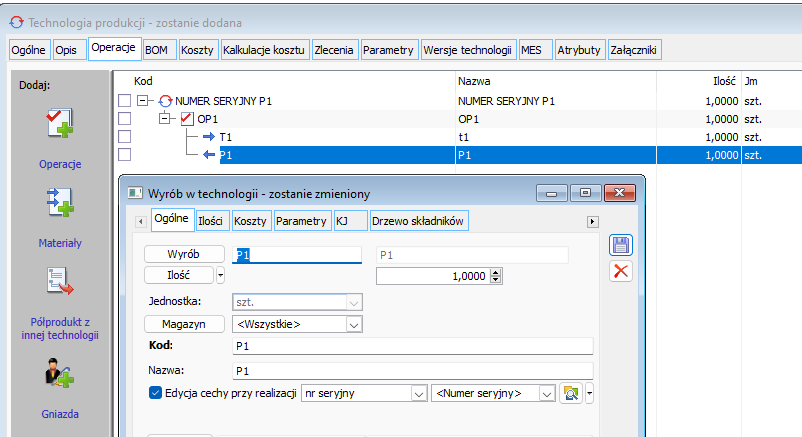
Następnie na zakładce: Ogólne zlecenia produkcyjnego w polu: Numer seryjny należy określić numer, jakim ma być oznaczony materiał, wyprodukowany w ramach danego zlecenia produkcyjnego:
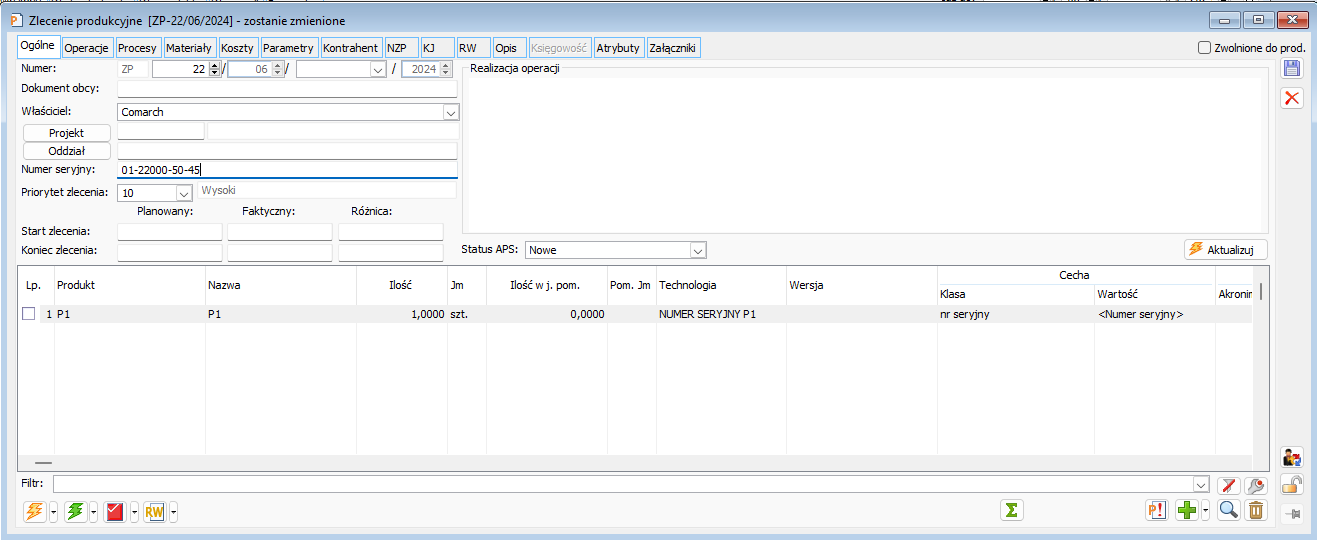
Po zaplanowaniu zlecenia i wykonaniu realizacji operacji, numer seryjny zostanie automatycznie przeniesiony z zakładki: Ogólne ZP na produkt, znajdujący się na realizacji operacji:
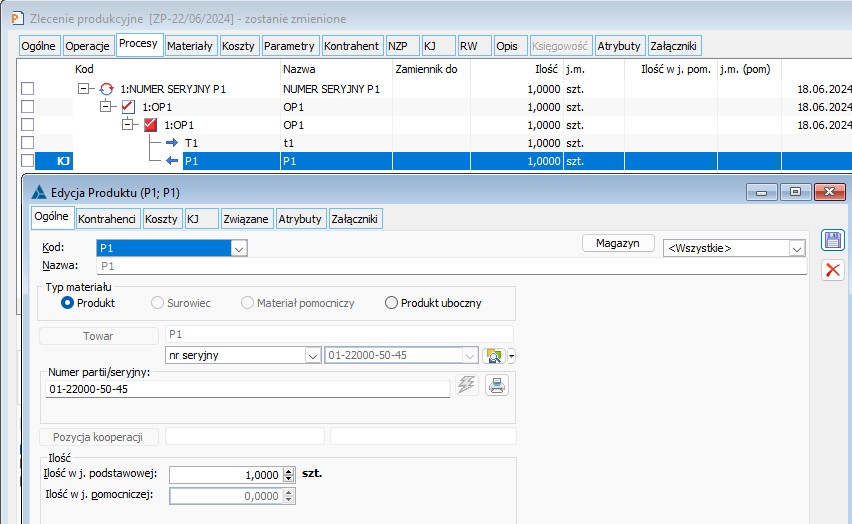
Następnie, po wygenerowaniu ze zlecenia dokumentu PW, numer seryjny zostanie zapisany również w wartości cechy na dostawie założonej w/w dokumentem PW:
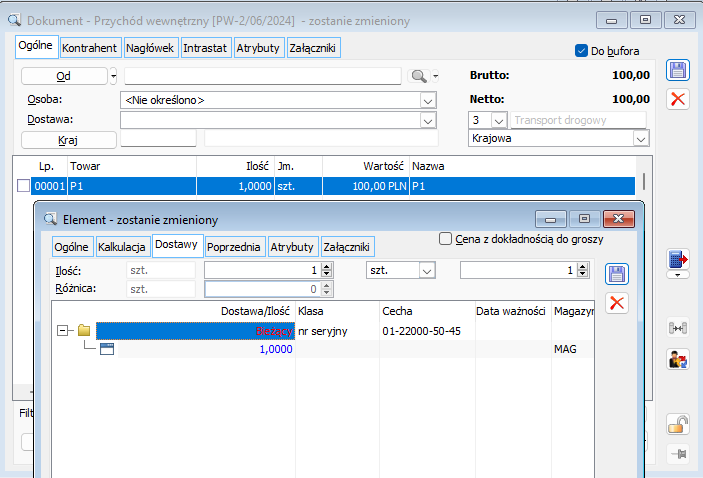
Czy wiesz czym w systemie Comarch ERP XL są magazyny produkcyjne?
Uwagi ogólne
Magazyny produkcyjne nie są rzeczywistymi magazynami, lecz magazynami tzw. wirtualnymi, przypisywanymi przez Użytkownika do magazynów rzeczywistych w danym centrum struktury firmy. Są one definiowane na potrzeby usprawnienia procesu produkcyjnego w systemie. Magazyny produkcyjne wskazują, który z magazynów w danym centrum jest magazynem surowców produkcyjnych, półproduktów, produktów gotowych itp.
Definiowanie magazynu produkcyjnego
W module Administrator w Słowniku kategorii należy zdefiniować wirtualne magazyny produkcyjne.
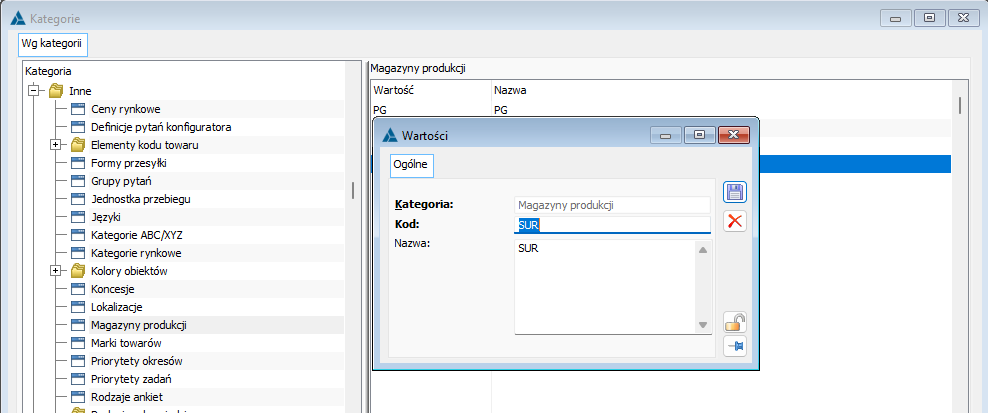
W oknie: Edycja struktury firmy na zakładce Magazyny na liście magazynów w kolumnie Magazyn produkcji poprzez dwuklik należy z listy zdefiniowanych wcześniej magazynów produkcyjnych wybrać odpowiedni. Poprzez tę operację następuje wiązanie magazynu wirtualnego z rzeczywistym.

Dodatkowo na definicji dokumentu Zlecenia kompletacji na zakładce Magazyny należy zaznaczyć parametr ‘Preferuj magazyny z karty towaru/receptury’.
Praktyczne wykorzystanie magazynu produkcyjnego
Na karcie towaru na zakładce Receptury możliwe jest zdefiniowanie receptury kompletacji. w oknie Receptura na zakładce Ogólne natomiast można wskazać zdefiniowany wcześniej magazyn produkcyjny. Na rozwijalnej liście magazyn produkcyjny wyróżniony został kolorem czerwonym. Podobnie sytuacja wygląda w oknie Składnik. Operator zatem definiując recepturę kompletacji nie musi pamiętać na którym magazynie rzeczywistym znajdują się surowce, ani na który rzeczywisty magazyn mają trafić produkty gotowe, wystarczy że wybierze odpowiedni magazyn produkcyjny.
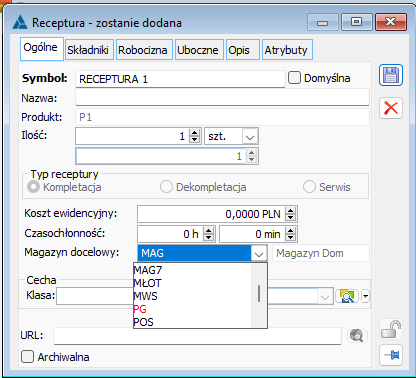
Na zleceniu kompletacji jeśli zostanie wybrana zdefiniowana wcześniej receptura wówczas w oknie Pozycja zlecenia domyślnie pojawią się rzeczywiste magazyny powiązane z wirtualnymi magazynami produkcyjnymi. Posiłkując się niniejszym przykładem rzeczywisty magazyn MAG25 został powiązany z magazynem produkcyjnym: SUR, natomiast magazyn MAG26 został powiązany z magazynem produkcyjnym PG. Wybierając na składnikach receptury magazyn produkcyjny SUR, na zleceniu kompletacji domyślnie na składnikach zlecenia kompletacji podpowie się magazyn MAG25. Wybierając na recepturze produktu magazyn produkcyjny PG, na zleceniu kompletacji domyślnie na pozycji podpowie się magazyn MAG26.
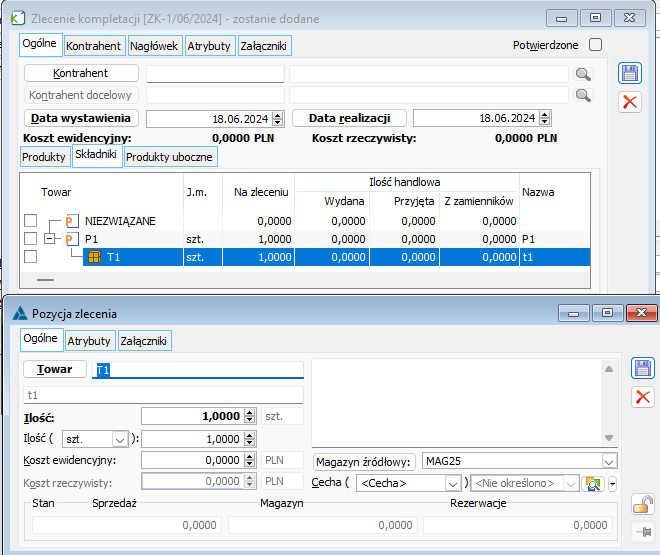
Czy wiesz, że istnieje możliwość szybkiego zdefiniowania technologii produkcyjnej?
Proces definiowania technologii produkcyjnej składającej się z kilku wykonywanych kolejno operacji można przeprowadzić w następujący sposób:
-
-
- Należy zdefiniować pierwszą operację i przypisać surowce.
- Dodać produkt o nazwie Operacja za pomocą przycisku na zakładce Materiały i Wyroby w Operacja w technologii, a następnie zapisać operacje.
-
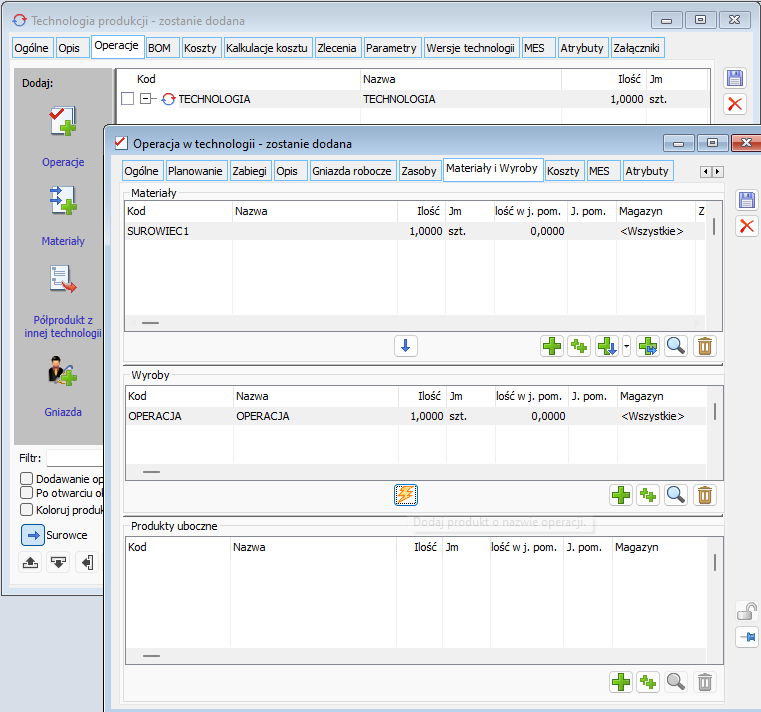
-
-
- Na zakładce Operacja technologii produkcyjnej zaznaczyć produkt pierwszej operacji, a następnie dodać nową operację – w efekcie produkt pierwszej operacji zostanie automatycznie przepisany jako surowiec operacji drugiej.
-
Czy wiesz, że w systemie ERP XL wprowadzono możliwość multiedycji zasobów produkcyjnych?
W systemie ERP XL wprowadzono możliwość multiedycji zasobów produkcyjnych. Po
zaznaczeniu kilku pozycji na liście i kliknięciu w kontrolkę multiedycji zasobów
pojawi się okno Edycja parametrów zasobów. Zmiany wprowadzone z poziomu tego okna zostaną przepisane na zaznaczone wcześniej karty zasobów produkcyjnych.
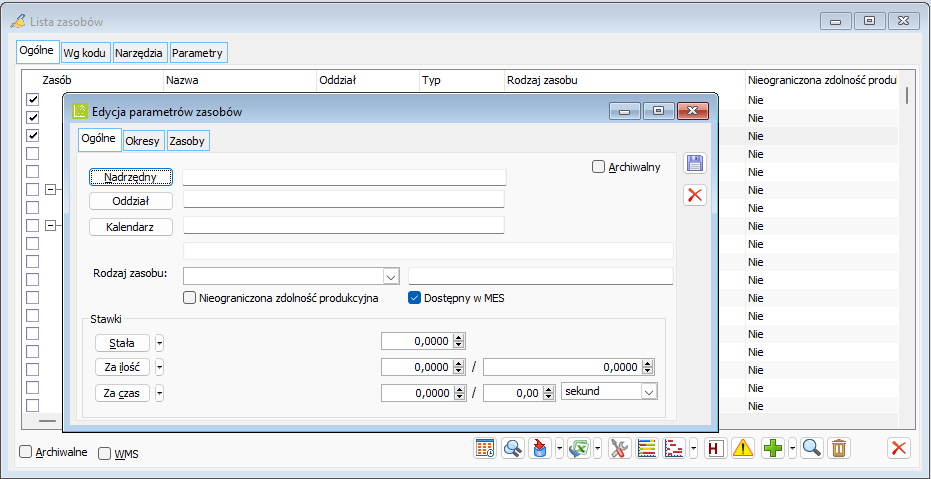
Czy wiesz, że do zlecenia produkcyjnego można przypisać dodatkowe koszty?
Podczas rozliczania produkcji do obiektów produkcyjnych przypisywane są automatycznie koszty w ramach predefiniowanych kategorii kosztów produkcji. Koszty te wynikają ze stawek określonych dla zasobów i stawek na technologii i operacjach oraz z wartości surowców. System ERP XL umożliwia przypisywanie innych kosztów, w ramach kategorii definiowanych przez Użytkownika. Źródłem takiego kosztu mogą być dokumenty handlowe (np. FZ za energię), zapisy księgowe, salda konta, składniki listy wynagrodzeń itd.
Dodatkowe koszty można przypisać do:
-
-
- Zlecenia produkcyjnego (lub wielu Zleceń produkcyjnych)
- Procesu produkcyjnego
- Operacji planowanej
- Realizacji operacji
- Zasobu produkcyjnego
- Surowca
- Produktu
-
Dodatkowe koszty przypisujemy do obiektów w ten sam sposób. Aby przypisać koszt należy zaznaczyć
dany obiekt produkcyjny, nacisnąć przycisk
[Przypisz koszt]. Zostanie wtedy otworzone okno: Koszt. W polu: Kategoria można wybrać jedną z kategorii kosztów produkcji zdefiniowaną przez Użytkownika. Kategorie definiowane są z poziomu modułu: Administrator w oknie: Słowniki kategorii.
Następnie Użytkownik może wskazać źródło kosztu, wybranego obiektu w ERP XL, np. dokument handlowy. W części: Kwota do przypisania, zostanie wyświetlona kwota wynikająca z dokumentu, jaką można przypisać do obiektu produkcyjnego. Możliwe jest zmniejszenie tej kwoty i przypisania tylko części wartości wynikającej z dokumentu. Podczas przypisywania wartości z dokumentu kontrolowana jest wartość już przypisana z tego samego dokumentu do produkcji (np. jeżeli z FZ na wartość 100 PLN został już przypisany koszt w wysokości 50 PLN, to możliwe będzie wykorzystanie tej samej FZ, jako źródła kosztu, ale tylko do wysokości 50 PLN, a więc pozostałej po ostatnim przypisaniu kosztu do produkcji z dokumentu).
W polu: Rozbij według wybiera się kryterium, według którego zostanie rozbity przypisany koszt. W zależności od poziomu przypisania kosztu, dostępne są różne kryteria jego rozbicia według zasady mówiącej, iż im wyższy poziom przypisania kosztu, tym więcej możliwości rozbicia kosztu, np. przypisując koszt z poziomu listy zleceń produkcyjnych, możliwe jest jego rozbicie na: zlecenia produkcyjne i elementy podrzędne do zleceń, czyli procesy w tych zleceniach, operacjach produkcyjnych, realizacje, surowce, produkty itd. podczas gdy przypisując koszt do produktu możliwe jest jego przypisanie tylko do poziomu produktów.
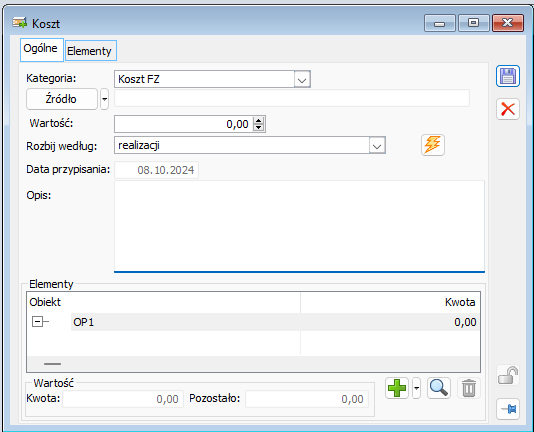
Po uruchomieniu przycisku
[Rozbij koszt wg wybranego klucza] na zakładce: Elementy, zostaną wyświetlone obiekty produkcyjne, na które został rozbity koszt. Dla każdego z elementów możliwa jest edycja ręczna przypisanego kosztu. Przed zapisaniem okna kosztu niezbędne jest rozdysponowanie pełnej wartości przypisanego kosztu. W przypadku edycji ręcznej może się zdarzyć, że część kosztu zostanie nie przypisana do żadnego elementu. Część ta zostanie wyświetlona w polu: Wartość – Pozostało.
Na zakładce: Elementy możliwe jest modyfikowanie przypisania kosztów do poszczególnych elementów. Dostępne są te same kryteria co w analogicznym polu na zakładce: Ogólne. Rozbicie następuje po wybraniu kryterium i naciśnięciu przycisku:
[Rozbij koszt wg wybranego klucza].
Dodatkowo za pomocą przycisku
[Dodaj element] można dołączyć nowy element, na który zostanie rozbity przypisany koszt. Po jego naciśnięciu zostanie wyświetlona lista zleceń produkcyjnych, umożliwiająca wybranie odpowiedniego elementu. Dodawanym elementem może być tylko element tego samego rodzaju, czyli jeżeli na zakładce wyświetlone są jako elementy produkty, możliwe jest dodanie jako elementu tylko produktu.
Czy wiesz, że istnieje możliwość automatycznego połączenia operacji produkcyjnych w technologii za pomocą półproduktów?
W wersji ERP XL mamy możliwość automatycznego połączenia operacji produkcyjnych w technologii. Operator zdefiniował technologię produkcyjną z kilkoma operacjami:
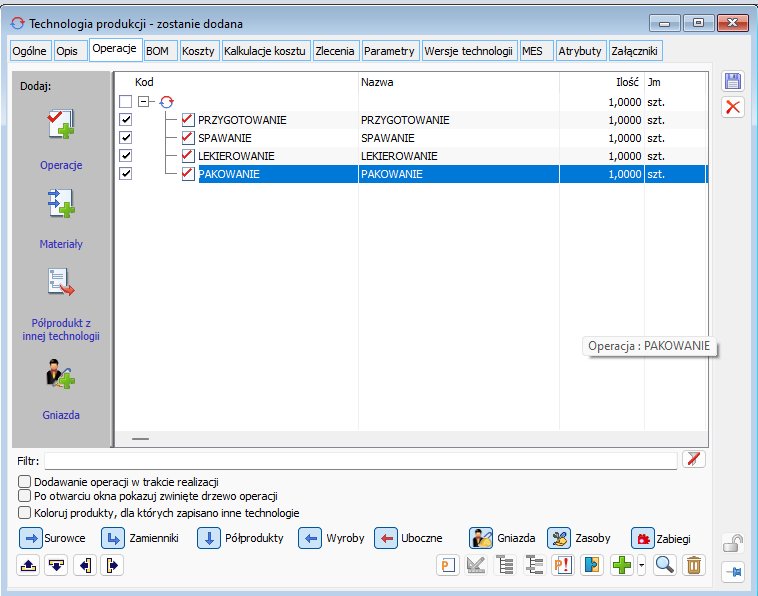
Aby uruchomić automatyczne łączenie operacji należy z poziomu zakładki Operacje zaznaczyć operacje, które mają zostać ze sobą połączone oraz kliknąć przycisk
. W efekcie zostaną wygenerowane półprodukty łączące zaznaczone pozycje.
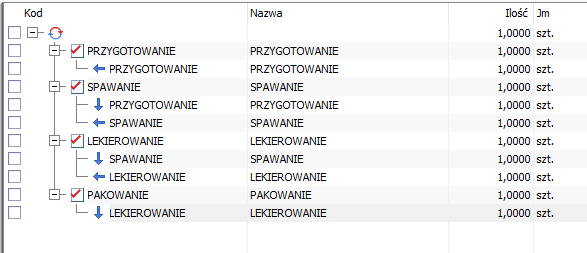
Czy wiesz, że istnieje możliwość wystawienia korekt do dokumentów handlowych związanych ze zleceniem produkcyjnym?
W programie zdefiniowano zlecenie produkcyjne na produkcję półki. Do realizacji operacji zostały wygenerowane dokumenty RW i PW. W wyniku realizacji zlecenia nie została jednak wykorzystana cała ilość pobranego surowca i zachodzi potrzeba jego zwrotu na magazyn.
W tym celu należy zmniejszyć ilość na surowcu, a następnie wybrać generowanie dokumentu korekty rozchodu wewnętrznego.
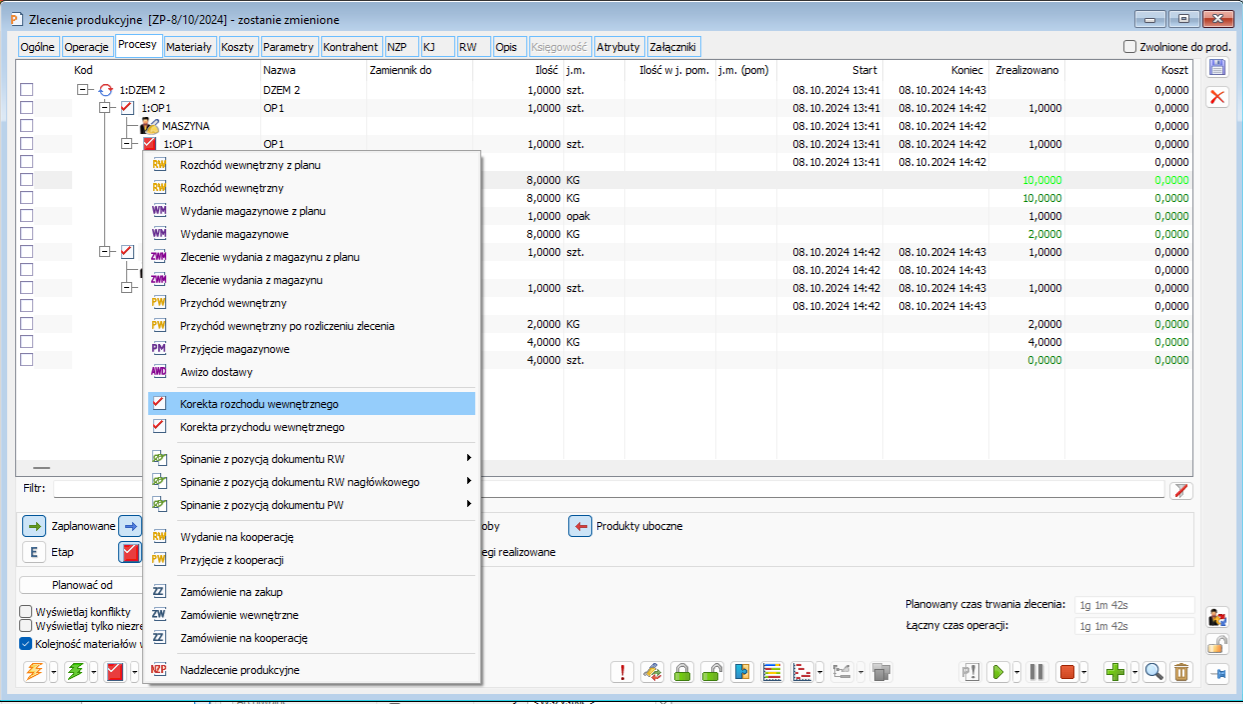
W efekcie zostanie wystawiony dokument korekty zgodnie z różnicą między ilością zadeklarowaną na zleceniu produkcyjnym, a ilością faktycznie wydaną na dokumentach związanych ze zleceniem.
W analogiczny sposób można zarejestrować korektę do dokumentu przychodu wewnętrznego.
Czy wiesz, że w systemie Comarch ERP XL można wygenerować zlecenie produkcyjne z jednego lub wielu istniejących dokumentów PW?
By poprawnie wygenerować zlecenie produkcyjne z PW, dokumenty PW muszą być zatwierdzone, a ich pozycje muszą mieć zdefiniowaną aktywną technologię produkcyjną.
Po realizacji zlecenia, wygenerowanego z dokumentu PW, produkty otrzymane na tym zleceniu zostaną automatycznie spięte z pozycjami PW, z którego wygenerowano ZP.
Generowanie ZP z PW rozpoczynamy od zaznaczenia dokumentów PW, z których ma być generowane ZP. Następnie wybieramy funkcję: Generuj ZP, dostępną spod prawego przycisku myszy.
Po wybraniu funkcji: Generuj ZP, zostanie otwarte okno: Wybierz sposób generowania zleceń, w którym można określić sposób generowania ZP z PW:
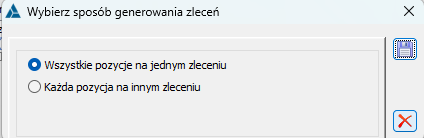
Po zaznaczeniu opcji: Wszystkie pozycje na jednym zleceniu i zapisaniu formatki dyskietką, zostanie wygenerowane jedno zlecenie produkcyjne dla wszystkich pozycji dokumentów PW, dla których uruchomiono funkcję: Generuj ZP.
Po zaznaczeniu opcji: Każda pozycja na innym zleceniu i zapisaniu formatki dyskietką, zostanie wygenerowane tyle zleceń, ile jest pozycji na dokumentach PW, dla których uruchomiono funkcję: Generuj ZP. (Pozycją każdego zlecenia będzie kolejna pozycja PW).
Czy wiesz, że w systemie Comarch ERPXL możliwe jest uruchomienie prostego interfejsu rejestracji produkcji?
Praktyczne zastosowanie
Prosty interfejs dla rejestracji produkcji został dedykowany do pracy na hali produkcyjnej i będzie umożliwiał wczytywanie danych dotyczących: czasu rozpoczęcia i zakończenia operacji, ilości zrealizowanych operacji, zużytych surowcach i uzyskanych produktach. Interfejs jest uruchamiany jako osobna aplikacja z możliwością pracy na ekranach dotykowych oraz współpracy z czytnikami kodów kreskowych.
Przed przystąpieniem do pracy z prostym interfejsem należy odpowiednio skonfigurować parametry.
Konfiguracja parametrów następuje w module Administrator w oknie: Struktura firmy na zakładce: Produkcja. Szczegółowe informacje znajdują się w dokumentacji do modułu Administrator.
Uruchomienie aplikacji
Aplikację Prostego interfejsu należy uruchomić plikiem: CDNPRD.EXE.
Logowanie do aplikacji będzie się odbywało poprzez logowanie operatora. Nie będzie to przeszkadzało w rejestrowaniu wykonania poszczególnych operacji – każde potwierdzenie wykonania operacji będzie się mogło odbyć po uprzedniej autoryzacji pracownika.
Lista operacji
Po zalogowaniu się operatora zostanie wyświetlone okno: Lista operacji. W oknie wyświetlana jest lista operacji w układzie kolumn. W oknie możliwe jest filtrowanie operacji według terminu (daty, godziny), zasobu, oddziału, operacji, zrealizowanych operacji.
Funkcja START służy do zarejestrowania uruchomienia operacji. Po zaznaczeniu na liście operacji i wciśnięciu przycisku Start lub F7 nastąpi uruchomienie. Zostanie otworzone okno: Realizacja operacji.
Funkcja KONIEC służy do rejestrowania wykonania operacji, jest obsługiwana po naciśnięciu przycisku Koniec lub klawisza F8.
Realizacja operacji
Okno: Realizacja operacji wywoływane jest po uruchomieniu funkcji: START.
Po uruchomieniu realizacji operacji w PI, nadawany jest jej nowy kod EAN, wyświetlany na belce operacji. Kod ten ułatwia identyfikację uruchomionej realizacji z poziomu zwykłego interfejsu (w oknie: Harmonogram operacji, zakładka: Wg EAN).
W obszarze Ogólne wyświetlane są podstawowe informacje na temat edytowanej operacji, możliwe jest wyszukiwanie, dodawanie, usuwanie oraz zamienianie surowców i produktów.
W obszarze Zasoby znajduje się lista zasobów przypisanych do edytowanej operacji produkcyjnej, możliwe jest wyszukiwanie, dodawania, usuwanie oraz zamienianie gniazda lub zasobu.
Czy wiesz, że w systemie Comarch ERP XL istnieje funkcja, która umożliwia automatyczne wygenerowanie dokumentu PW ze zlecenia produkcyjnego, po jego rozliczeniu?
Funkcja: Przychód wewnętrzny po rozliczeniu zlecenia jest dostępna z poziomu listy zleceń produkcyjnych, jak również z poziomu danego zlecenia produkcyjnego.
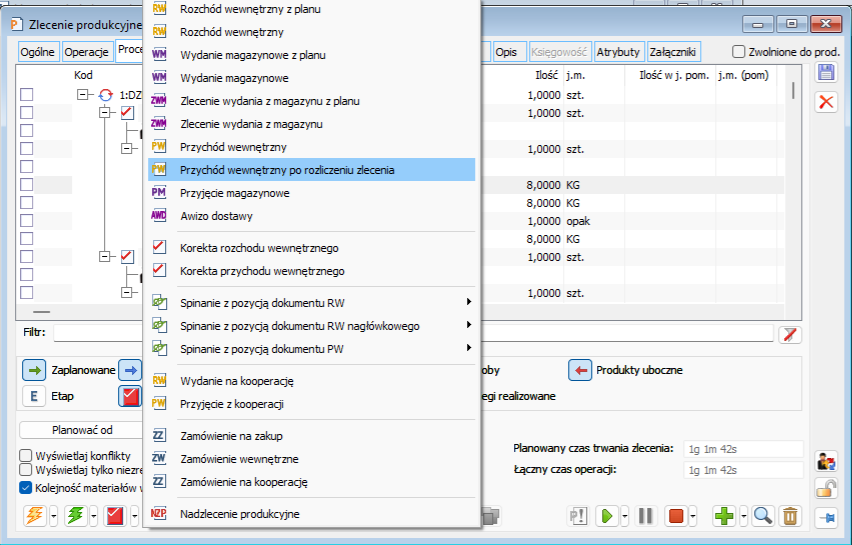
Jej działanie łączy ze sobą proces rozliczania zlecenia produkcyjnego i proces generowania dokumentu PW. Po uruchomieniu wymienionej funkcji, zostaje wywołane rozliczanie zlecenia, po czym generowany jest dokument PW, na którym, dla produktu podpowiada się odpowiednio wyliczony koszt.
Przykład1: Zaplanowano ZP dla 1szt. Produktu w oparciu o pewną technologię. Uruchomiono Realizację operacji. Następnie z ZP wygenerowano i zatwierdzono dokument RW na potrzebne do produkcji surowce. Następnie z poziomu zlecenia produkcyjnego uruchomiono funkcję: Przychód wewnętrzny po rozliczeniu zlecenia. W wyniku tych operacji został wygenerowany dokument PW, na którym widnieje odpowiednio wyliczona wartość produktu końcowego.
Czy wiesz, że lista zleceń produkcyjnych umożliwia zbiorcze raportowanie stanu produkcji dla wielu zleceń?
Umożliwiono prezentację szczegółów zlecenia w formie tabelarycznej. W oknie: Zlecenia produkcyjne, po naciśnięciu przycisku: Pokaż szczegóły zlecenia, wyświetlona zostaje nowa sekcja: Szczegóły zlecenia. Dla zlecenia wskazanego na liście, na zakładce: Materiały, wyświetlana jest lista materiałów danego zlecenia wraz z informacją o ilości, ilości zrealizowanej, zarezerwowanej oraz ilości dostępnej na magazynie źródłowym i wszystkich magazynach. Oprócz udostępnienia w sekcji: Szczegóły zlecenia nowej zakładki: Produkty, na obu zakładkach umożliwiono zestawienie danych z wielu zleceń zaznaczonych na liście.
Zakładka: Produkty w sekcji: Szczegóły zlecenia
Lista na zakładce: Produkty stanowi raport stopnia realizacji zleceń produkcyjnych. Listę tworzą pozycje wskazanego zlecenia produkcyjnego lub wielu zleceń zaznaczonych na liście. Najważniejszymi informacjami prezentowanymi na liście są: numer dokumentu źródłowego do którego wygenerowana została dana pozycja zlecenia, termin realizacji elementu zamówienia powiązanego z daną pozycją zlecenia (dotyczy ZS, ZW), ilość na pozycji zlecenia, termin produkcji określający najpóźniejszą datę realizacji rezerwacji zakupowej na produkt spośród wszystkich rezerwacji zakupowych na produkt powiązanych z daną pozycją zlecenia, ilość zrealizowana określająca ilość jaka znajduje się na zatwierdzonych dokumentach PW powiązanych z daną pozycją zlecenia, ilość w toku, ilość do realizacji, ilość zaplanowana oraz ilość do zaplanowania. W kolumnie: Związane, prezentowany jest numer dokumentu PW powiązanego z daną pozycją zlecenia. W przypadku, gdy z daną pozycją zlecenia powiązanych jest więcej dokumentów PW, w kolumnie wyświetlana jest fraza: Lista <…>.
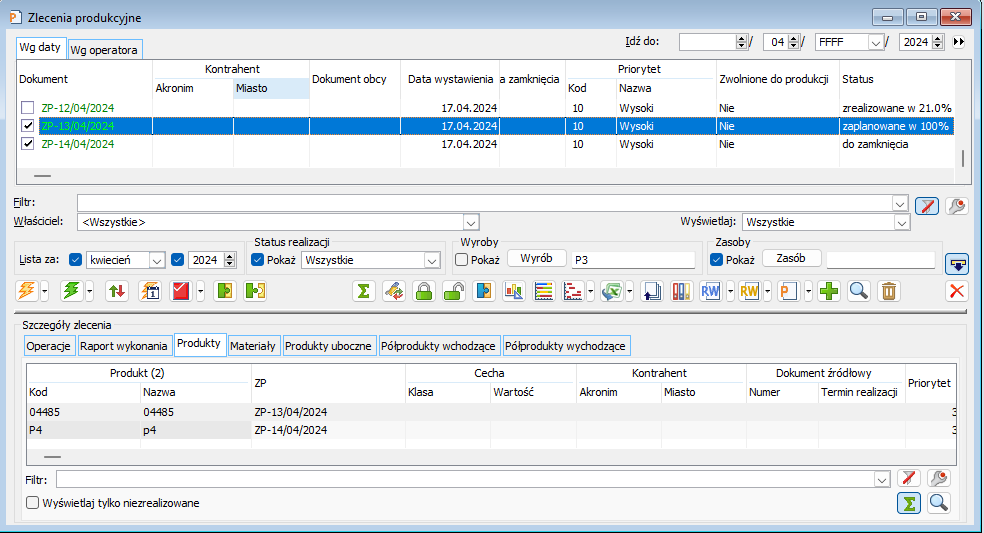
Szczególnie przydatną funkcjonalnością udostępnioną na liście jest sygnalizowanie opóźnienia planowanego terminu produkcji względem terminu realizacji na elemencie ZS/ZW powiązanym z daną pozycją zlecenia oraz sygnalizowanie upływu planowanego terminu produkcji. Funkcjonalność zrealizowana została poprzez kolorowanie, odpowiednio, terminu realizacji oraz terminu produkcji.
Przykład: W dniu 2023-04-18 zarejestrowane zostało zamówienie sprzedaży na 6 szt. towaru P1. Data realizacji na elemencie zamówienia to 2024-04-19. Do zamówienia wygenerowane zostało zlecenie produkcyjne. Planowany termin produkcji to 2024-04-20. Opóźnienie planowanego terminu realizacji pozycji zlecenia względem terminu realizacji na elemencie zamówienia zasygnalizowane zostaje poprzez wyświetlenie daty w kolumnie: Termin realizacji w kolorze czerwonym.
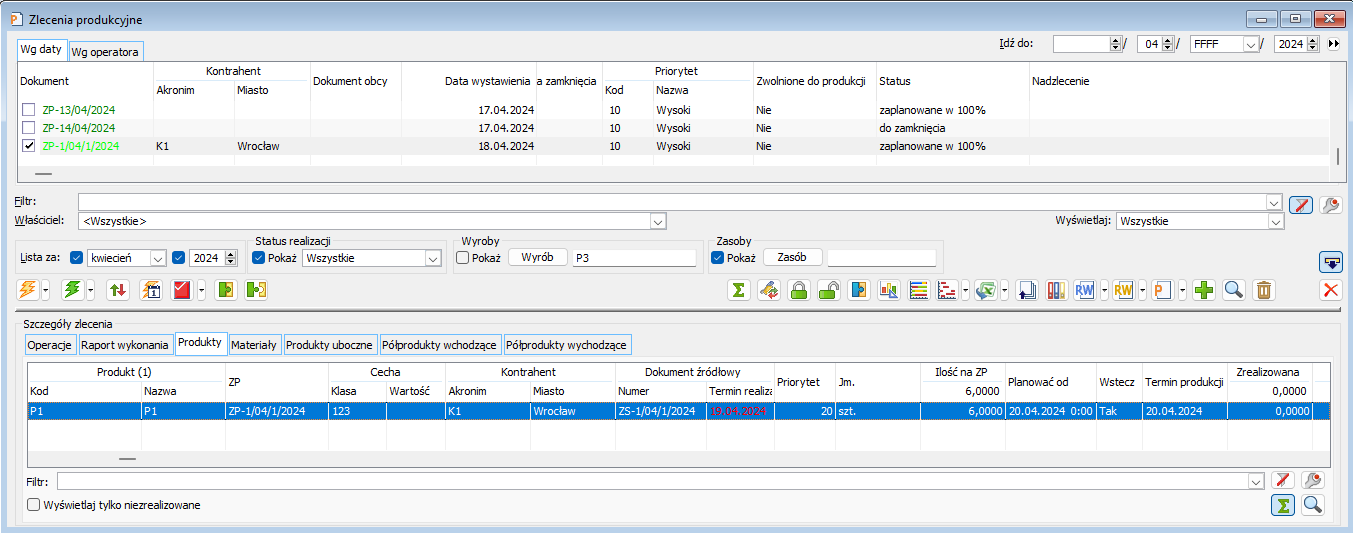
Listy na zakładkach: Produkty oraz Materiały wyposażone zostały dodatkowo w filtry: przykładowy parametr Wyświetlaj tylko niezrealizowane. Po jego zaznaczeniu na liście nie są wyświetlane elementy powiązane na pełną ilość z zatwierdzonymi dokumentami handlowymi. Dodatkowymi elementami wprowadzonymi na obu zakładkach są również: możliwość sumowania ilości w wybranych kolumnach oraz lokator ograniczający w kolumnie Kod.
Czy wiesz, że możliwa jest kalkulacja kosztów z uwzględnianiem kosztów dodatkowych i przenoszeniem ceny na element oferty lub zamówienia sprzedaży?
Na raporcie Kalkulacji kosztów została udostępniona funkcjonalność umożliwiająca szacowanie kosztów produktu w oparciu o wybrane metody z możliwością przenoszenia proponowanej ceny uzgodnionej na element oferty lub zamówienia sprzedaży. Oprócz kosztów bezpośrednio wynikających ze zdefiniowanej dla produktu technologii uwzględniane są również koszty dodatkowe, które można ręcznie wprowadzić do raportu.
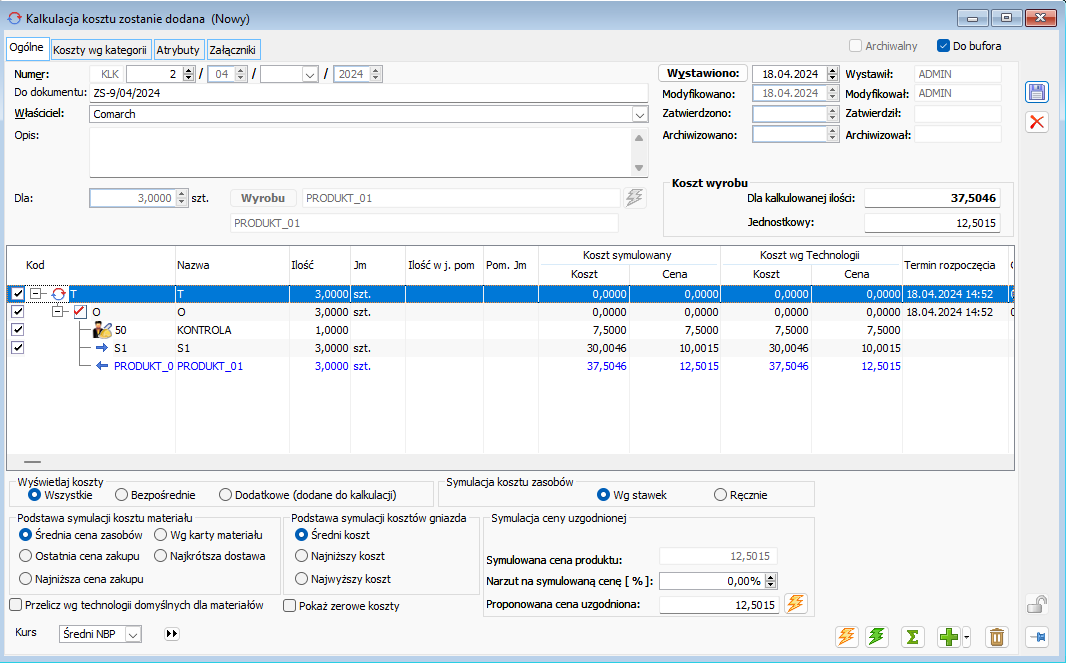
Proponowana cena uzgodniona jest wyliczana na podstawie symulowanego kosztu produktu.
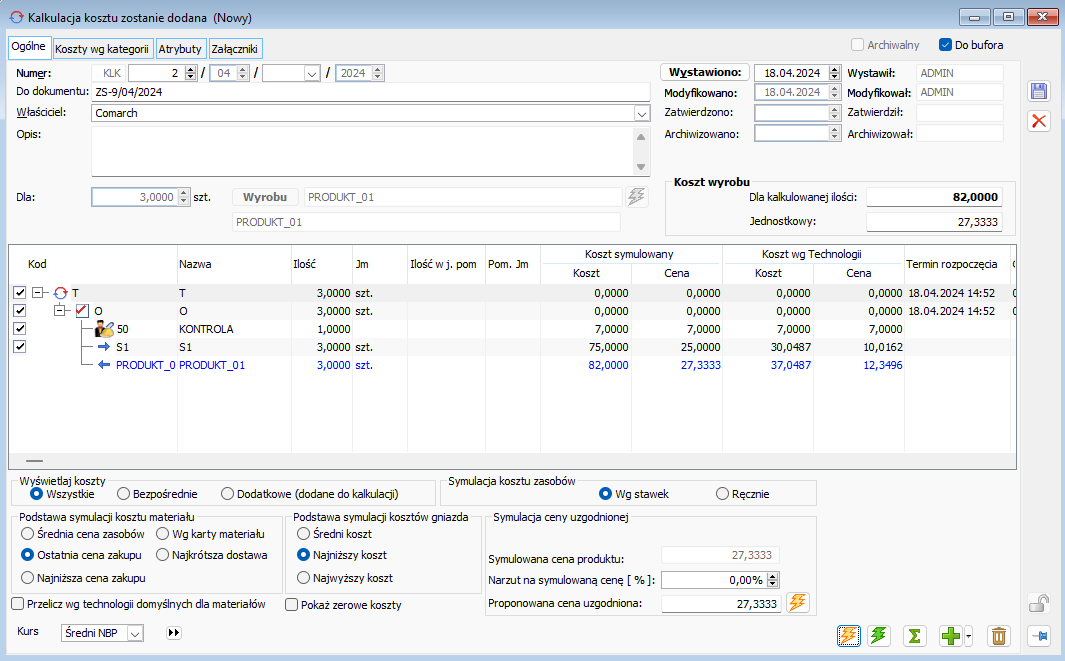
Po zmianie podstawy symulacji kosztu materiału lub gniazda roboczego należy przeliczyć raport
Czy wiesz, jak zdefiniować technologię z wykorzystaniem zamiennika jako półproduktu pochodzącego z innej technologii?
Konfiguracja operacji w technologii
Na operacji w technologii istnieje możliwość zdefiniowania zamienników. Jeśli zabraknie jednego surowca na magazynie system podczas planowania i pobierania zasobów sprawdzi czy jest jego zamiennik i odpowiednio go pobierze z magazynu. Wystarczy dodać na Operacji w technologii dwa materiały np. Towar1 i Towar2, a na formatce Materiał w technologii na zakładce Ogólne dla Towaru2 wskazać w polu: Zamiennik do – Towar1.
Jeśli dany surowiec jest półproduktem, można tak zdefiniować technologię, aby podczas planowania system sprawdzał czy znajduje się na magazynie, jeśli tak, to go zarezerwuje w odpowiedniej ilości. Jeśli natomiast zabraknie surowca, wówczas zaplanuje proces technologiczny do jego wyprodukowania.
W tym celu należy odpowiednio skonfigurować technologie:
- Należy zdefiniować technologię do produkcji półproduktu np. PP1 i na produkcie oznaczyć parametr Dalsze wykorzystanie ‘dowolne’.
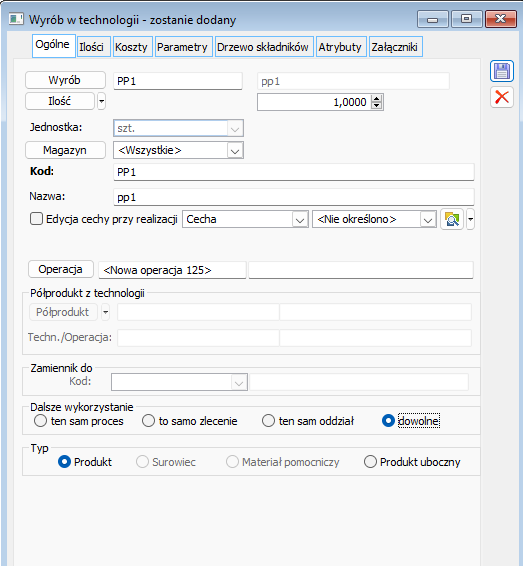
- Należy zdefiniować technologię do produkcji produktu finalnego i na operacji w technologii należy dodać dwa razy ten sam surowiec – półprodukt np. PP1.
- Pierwszy raz surowiec PP1 powinien być oznaczony tylko jako towar z magazynu
- Drugi raz surowiec PP1 powinien być oznaczony jako towar z magazynu, półprodukt pochodzący z innej technologii oraz zamiennik do (na liście rozwijalnej pojawią się surowce wcześniej dodane na operacji).
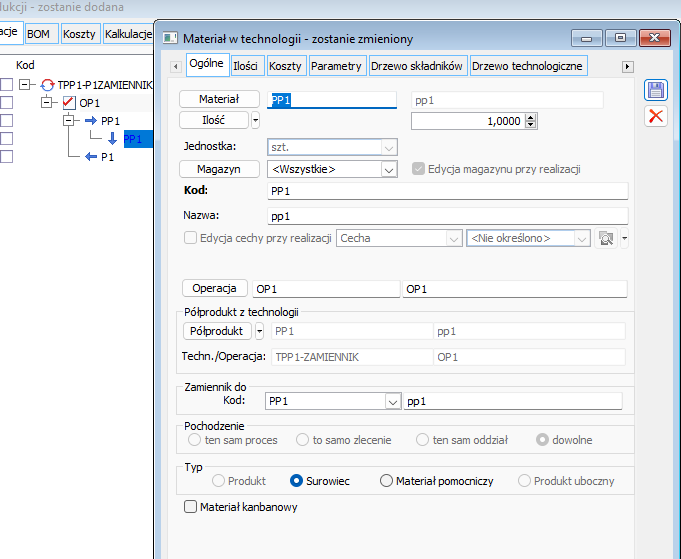
Zastosowanie skonfigurowanej technologii na zleceniu
Podczas planowania zlecenia na produkt finalny P1 system w pierwszej kolejności sprawdzi czy surowiec PP1 jest na magazynie, jeśli jest – wówczas go zarezerwuje, jeśli go nie ma – zaplanuje dwa procesy technologiczne.
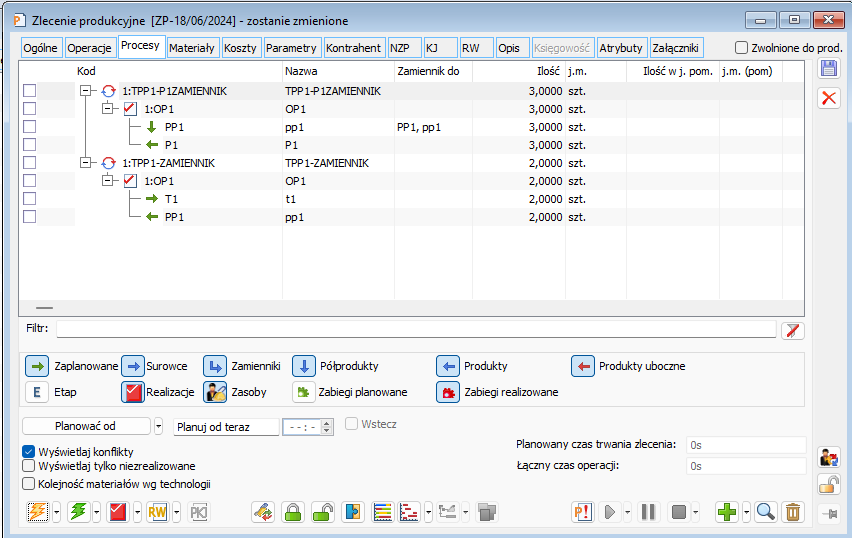
Czy wiesz, że w Systemie można utworzyć technologię wielowariantową?
Technologia wariantowa jest technologią, na której znajdują się produkty na wielu operacjach końcowych. Przykładem zastosowania tego typu technologii może być produkcja soku. Proces produkcyjny jest ten sam, aż do operacji rozlewu soku do opakowań o poszczególnych objętościach. Rozdzielenie ostatnich operacji rozlewu pozwala uniknąć niepotrzebnego powielania bliźniaczych technologii w bazie. Proces zostanie zaplanowany na zleceniu tylko dla opakowania, którego rozlew planowaliśmy.
Dodajemy nową technologię. Na zakładce: Ogólne.
- Wprowadzamy kod technologii: WIELOWARIANTOWA WG1/WG2,
- Zaznaczamy check: Zatwierdzona.
W technologii wybieramy zakładkę: Operacje i dodajemy nową operację. Na operacji wprowadzamy:
- Na zakładce: Ogólne kod operacji: 10,
- Na zakładce: Materiały i Wyroby wyrób: PP1.
Zapisujemy kartę materiału i operacji. W oknie technologii, na zakładce: Operacje, zaznaczamy produkt PP1 wychodzący z operacji 10 i naciskamy przycisk [Dodaj] . Zostanie dodana operacja, która od razu na zakładce: Materiały i Wyroby, będzie mieć dodany półprodukt PP1 z poprzedniej operacji. Następnie ustalamy:
- Na zakładce: Ogólne kod operacji: 20 WG1,
- Na zakładce: Materiały i Wyroby wyrób: WG1 w ilości 1 szt.
Zapisujemy kartę materiału i operacji. W oknie technologii, na zakładce: Operacje, ponownie zaznaczamy produkt PP1 wychodzący z operacji 10 i naciskamy przycisk [Dodaj] . Zostanie dodana operacja, która od razu na zakładce: Materiały i Wyroby, będzie mieć dodany półprodukt PP1 z poprzedniej operacji. Następnie ustalamy:
- Na zakładce: Ogólne kod operacji: 20 WG2,
- Na zakładce: Materiały i Wyroby wyrób: WG2 w ilości 2 szt.
Zapisujemy kartę materiału i operacji. Technologia powinna wyglądać następująco:
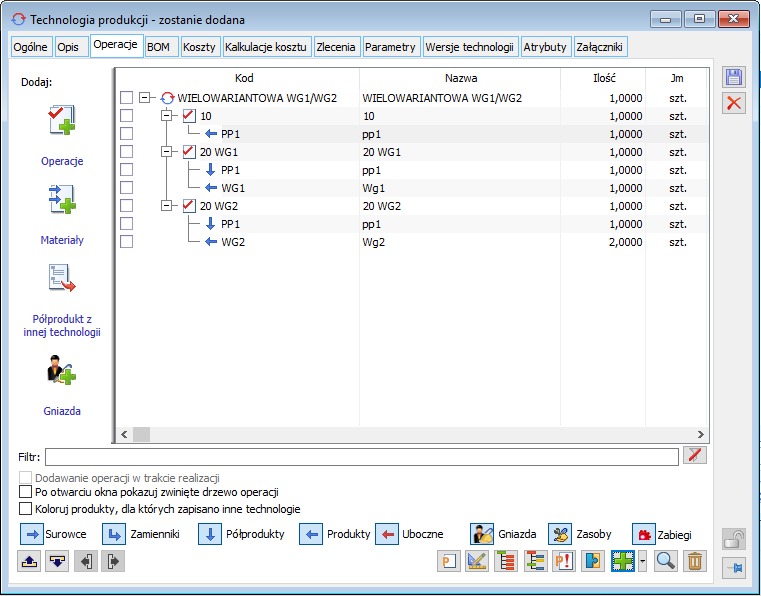
Czy wiesz, że w Systemie Comarch ERP XL udostępniono funkcjonalność łączenia pozycji na dokumentach RW generowanych z ZP?
System Comarch ERP XL pozwala zadecydować o tym, czy na dokumentach RW generowanych ze zlecenia produkcyjnego powinny być grupowane pozycje. Polecenie łączenia pozycji na dokumencie RW odbywa się poprzez zaznaczenie parametru „Łącz pozycje w produkcji” dodanego na definicji dokumentu RW.
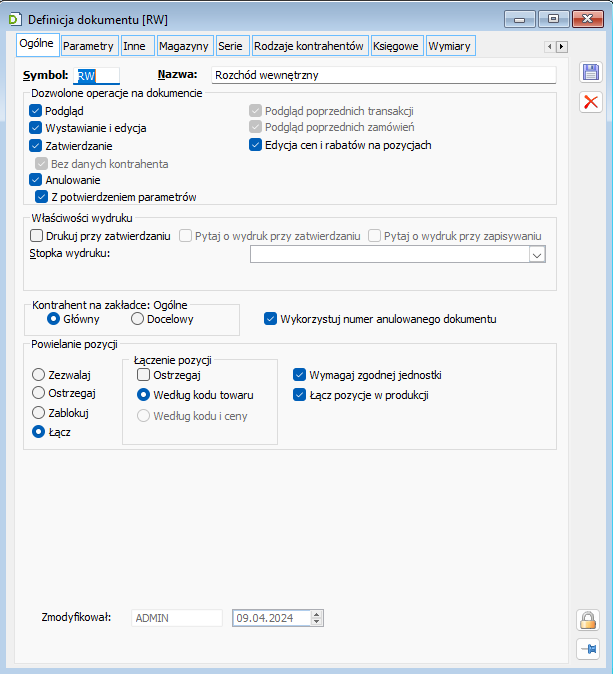
Domyślnie w Systemie ten parametr jest odznaczony, w takim przypadku na dokumencie pozycje nie są łączone.
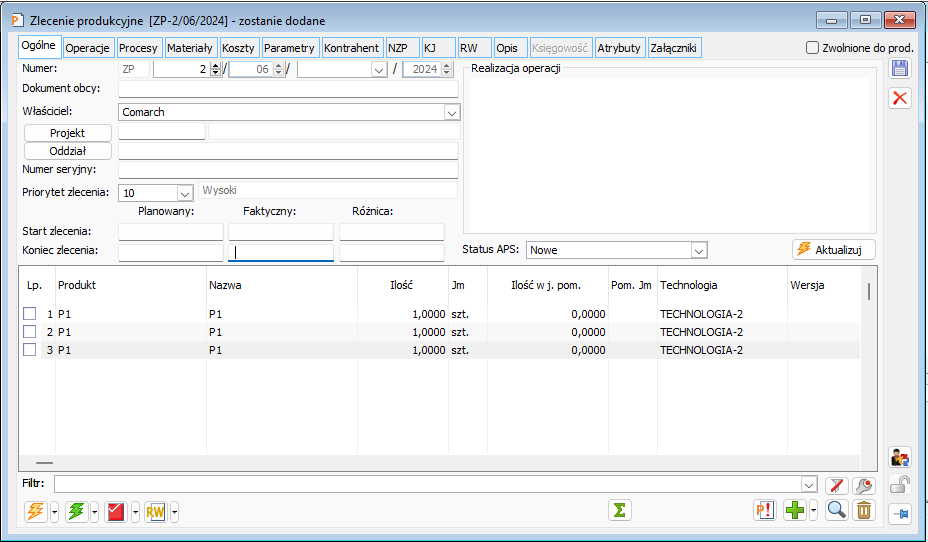
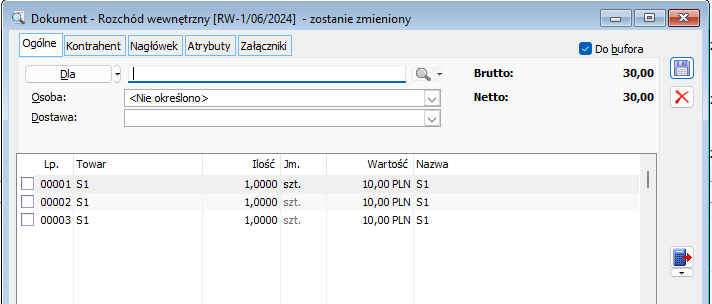
Zaznaczenie parametru będzie skutkowało tym, że na dokumencie RW będą połączone w jeden element te, które zostały powielone na ZP.
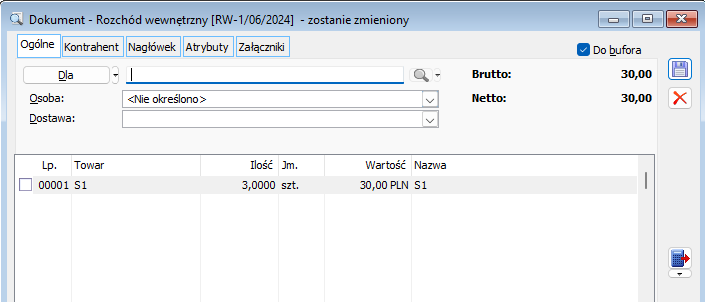
Czy wiesz, że w Comarch ERP XL istnieje możliwość wygenerowania potwierdzonych dokumentów RW, PW, RWK, PWK, podczas zamykania ZP/HPR?
W systemie Comarch ERP XL, na definicji dokumentów ZP i HPR, na zakładce: Inne dostępny jest parametr: Generuj zatwierdzone dokumenty przy zamykaniu zlecenia.
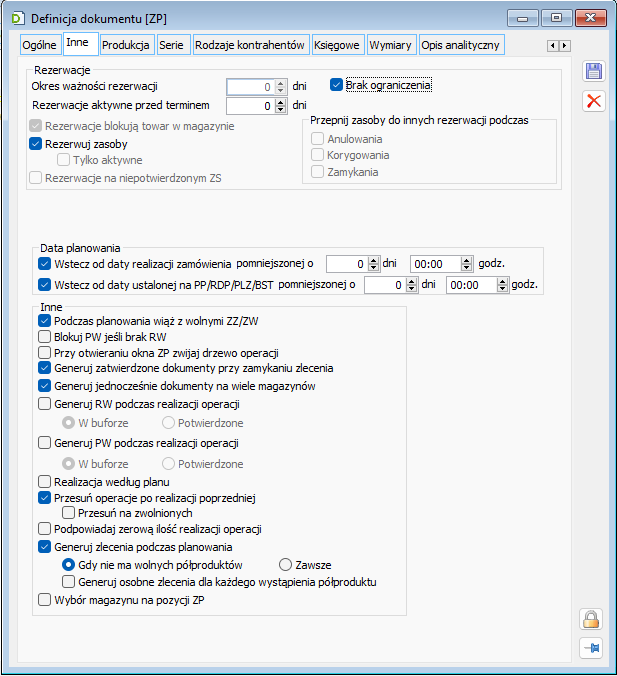
Parametr ten decyduje o ustawieniu domyślnym na dokumencie Zlecenia produkcyjnego oraz Harmonogramu projektu, na zakładce Parametry.
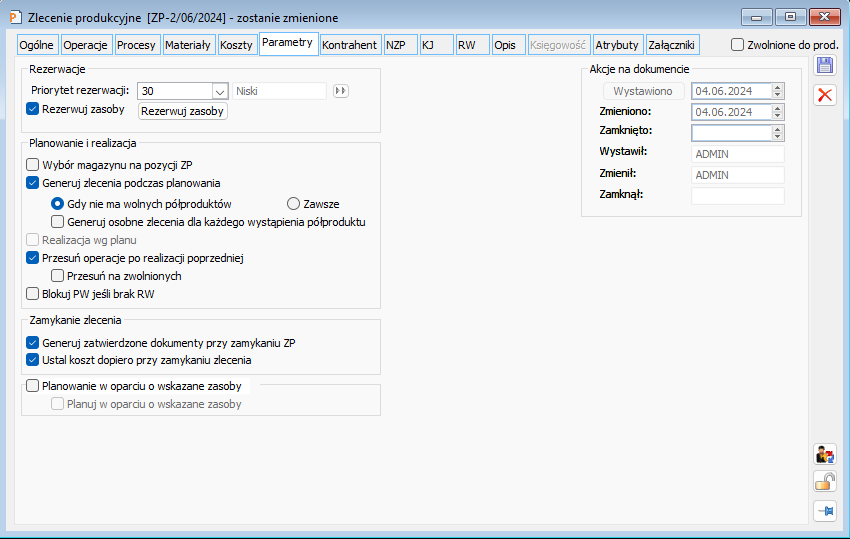
Przy zaznaczonym parametrze, podczas zamykania zlecenia lub harmonogramu projektu zostaną wygenerowane i zatwierdzone wszystkie dokumenty, których brakuje do zamknięcia zlecenia lub harmonogramu.
Czy wiesz, że na technologii istnieje możliwość ustalenia ilości domyślnej materiału, która będzie pojawiała się na ZP?
Zmiany na technologii
Parametr odpowiadający za tą funkcjonalność dotyczy wyłącznie materiałów, które są produktem. W oknie „Materiał w technologii” dla surowca, parametr ‘Ilość domyślna na ZP’ jest wyszarzony.
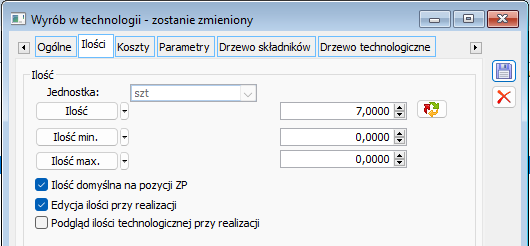

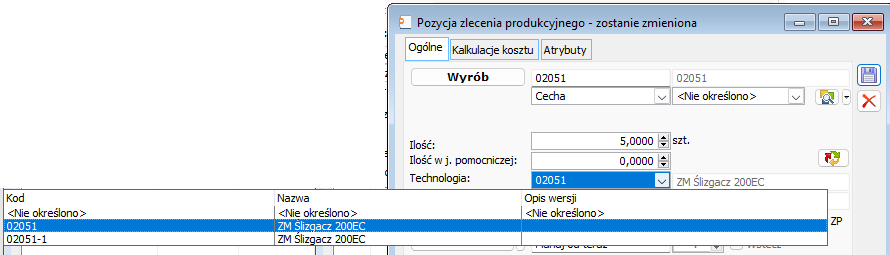
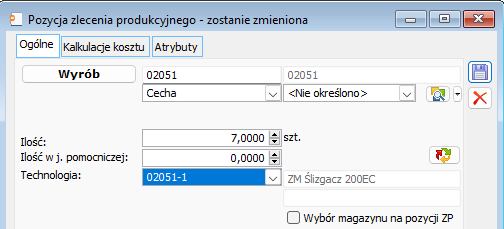
Zaznaczony parametr
W sytuacji gdy na technologii Operator zaznaczy parametr ‘Ilość domyślna na ZP’, po dodaniu produktu na ZP, na pozycji zlecenia w kolumnie ilość pokazana jest ilość pochodząca z technologii, również przy zmianie technologii na taką, która ma określoną ilość domyślną na ZP i zaznaczony parametr, na zleceniu zostanie ustalona ilość pochodząca z pola ‘Ilość’ z zakładki ‘Parametry’ w oknie „Materiał w technologii”.
Odznaczony parametr
W sytuacji gdy na technologii Operator nie zaznaczy parametru ‘Ilość domyślna na ZP’, po dodaniu produktu na ZP, na pozycji zlecenia w polu ‘Ilość’, niezależnie od tej wpisanej w pole ‘Ilość’ na zakładce ‘Parametry’ w oknie ‘Materiał w technologii’, jako domyślna zawsze będzie wpisywana 1.
W sytuacji, gdy zmiana technologii następuje na istniejącej już pozycji ZP, ilość pozostaje bez zmian w stosunku do ilości zdefiniowanej przy wyborze poprzedniej technologii.
Czy wiesz, że istnieje możliwość planowania ZP tak, aby kolejne operacje nie następowały bezpośrednio po sobie?
Zmiany na operacji w technologii
Aby umożliwić planowanie w określonych odstępach czasu, na formatce operacja w technologii dodano obszar ‘Odstępy między operacjami’, w nim parametry ‘po poprzedniej’ oraz ‘przed następną’ przyjmujące wartości całkowite oraz jednostki czasu: sekundy, minuty, godziny i dni.
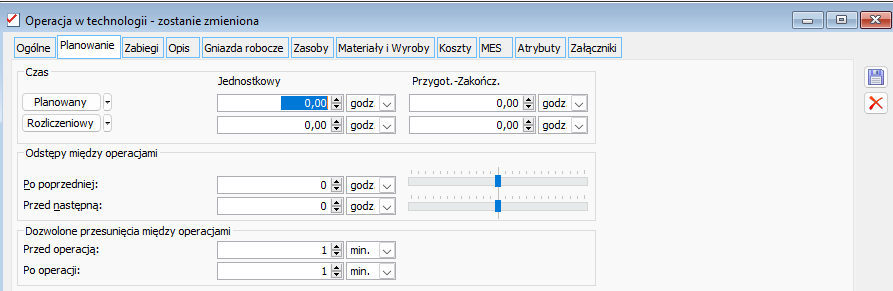
Planowanie zlecenia
W zależności od planowania, kontrolowany jest jeden z parametrów – w planowaniu w przód System weryfikuje ustawienie parametru ‘Po poprzedniej’, w planowaniu wstecz sprawdzane jest ustawienie parametru ‘Przed następną’.
Utworzona została technologia produkcyjna złożona z pięciu operacji. W ramach technologii produkowane są krzesła. W czwartej operacji krzesła wymagają pomalowania i po tej operacji konieczna jest 2 dniowa przerwa przed ostatnią operacją którą jest pakowanie. Operacja pierwsza trwa 2 godziny, operacja druga 6 godzin, trzecia 20 minut, czwarta 2 godziny, piąta również 2 godziny. Na operacji piątej ustawiono odstęp między operacjami Po poprzedniej = 2 dni.
W sytuacji, gdy na podstawie technologii, zlecenie zaplanowane zostanie w przód, System zaplanuje wykonanie operacji piątej nie wcześniej niż 2 dni po zakończeniu operacji 4. W sytuacji gdyby zasoby potrzebne do realizacji piątej operacji były niedostępne dokładnie dwa dni po zakończeniu operacji czwartej, System zaplanuje realizację operacji na pierwszy dostępny termin po upływie ustawionych 2 dni.
Utworzono technologie produkcyjną na podstawie której drewniane koraliki są dwukrotnie lakierowane i nanizane na żyłkę tworząc kolorowe drewniane korale. Technologia zbudowana jest z trzech operacji następujących po sobie – Kolorowanie, Lakierowanie 2, Nanizanie. W ramach pierwszej operacji kolorowane jest 100 koralików, kolorowanie jednego trwa 6 s. W ramach drugiej operacji koraliki pokrywane są warstwą lakieru bezbarwnego, lakierowanie 1 koralika trwa 10s. W ramach trzeciej operacji 100 koralików nawleka się na żyłkę o dł. 50 cm, operacja ta trwa w całości 15 minut. Operacja lakierowanie 2 musi rozpocząć się najwcześniej 3 godziny po zakończeniu operacji KOLOROWANIE i zakończyć 6 godzin przed rozpoczęciem operacji NANIZANIE – w związku z tym na operacji Lakierowanie 2 ustawiono parametr ‘Odstęp między operacjami, Przed następną = 6h’ na operacji KOLOROWANIE ten sam parametr uzupełniono wartością 3h. Zaplanowano, że na godzinę 15.00 30 listopada potrzebna jest 1 sztuka korali, w związku z tym wykonano planowanie wstecz: Każdy z zasobów ma zdefiniowany okres, w którym jest niedostępny: IŁ jest niedostępny od 00:00 do 23.59 30 XI, AN jest niedostępny 30 XI w godzinach 00:00 – 12:00, zasób KA jest niedostępny 30 XI w godzinach 08:00-15:00. Biorąc pod uwagę okresy niedostępności zasobów oraz bufory planowania, System zaplanował zlecenie tak, że operacja lakierowanie 2 zaplanowana została w pierwszym dostępnym terminie, jednak nie wcześniej niż 3 godziny po operacji kolorowanie. W związku z niedostępnością zasobu AN operacji została zaplanowana tak aby zakończyć się w ostatniej chwili dostępności zasobu AN tj. 29.11.2023 o godz. 23:59 zachowując jednak zdefiniowany 6 – godzinny odstęp pomiędzy operacjami lakierowanie 2 i nanizanie oraz okresy niedostępności poszczególnych zasobów. Operacja nanizanie zakończy się 30.11. o godzinie 07:59 w związku z niedostępnością zasobu KA.
Czy wiesz, że na zleceniach produkcyjnych (ZP) lub harmonogramie produkcji (HPR) można blokować wystawianie dokumentu PW, jeśli wcześniej nie wygenerowano RW?
Opis parametru
Funkcjonalność umożliwia opcjonalną blokadę generowania dokumentu PW ze zlecenia produkcyjnego (ZP) lub harmonogramu produkcji (HPR) w przypadku, gdy nie wygenerowano i zatwierdzono dokumentu RW.
Definicja dokumentu
W celu automatycznego ustawienia tego parametru na każdym ZP czy HPR, należy na definicji dokumentu zaznaczyć check: Blokuj PW jeśli brak RW.
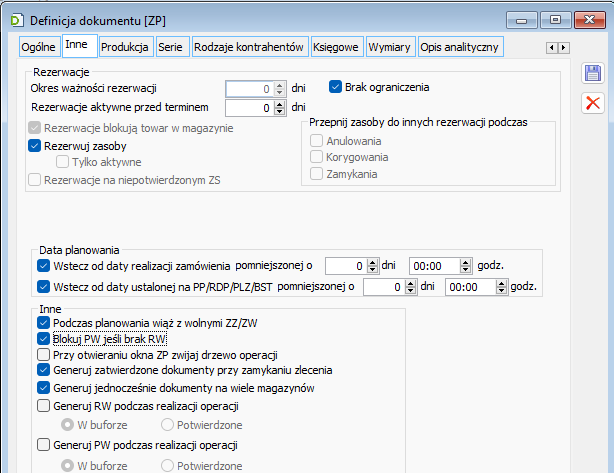
Zlecenie Produkcyjne
Jeżeli nie chcemy, aby na każdym ZP/HPR był zaznaczony parametr: Blokuj PW jeśli brak RW, możemy ten parametr zaznaczyć/odznaczyć ręcznie przy generowaniu ZP/HPR.
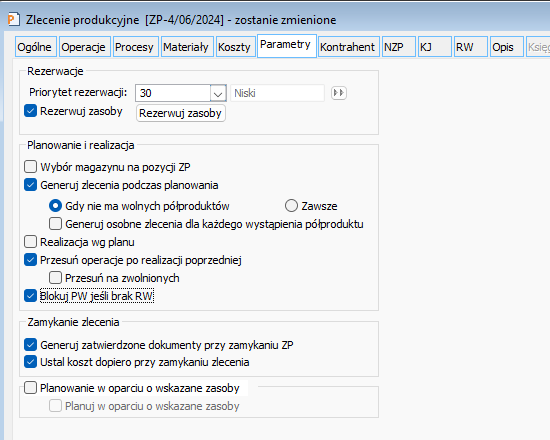
Generowanie PW, gdy brak RW
Przy zaznaczonym parametrze: Blokuj PW jeśli brak RW, jeśli w pierwszej kolejności nie wygenerujemy RW wyświetli się poniższy komunikat uniemożliwiający wystawienie PW.
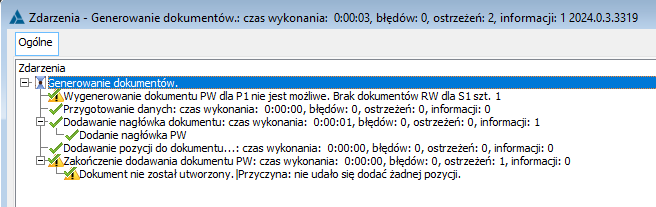